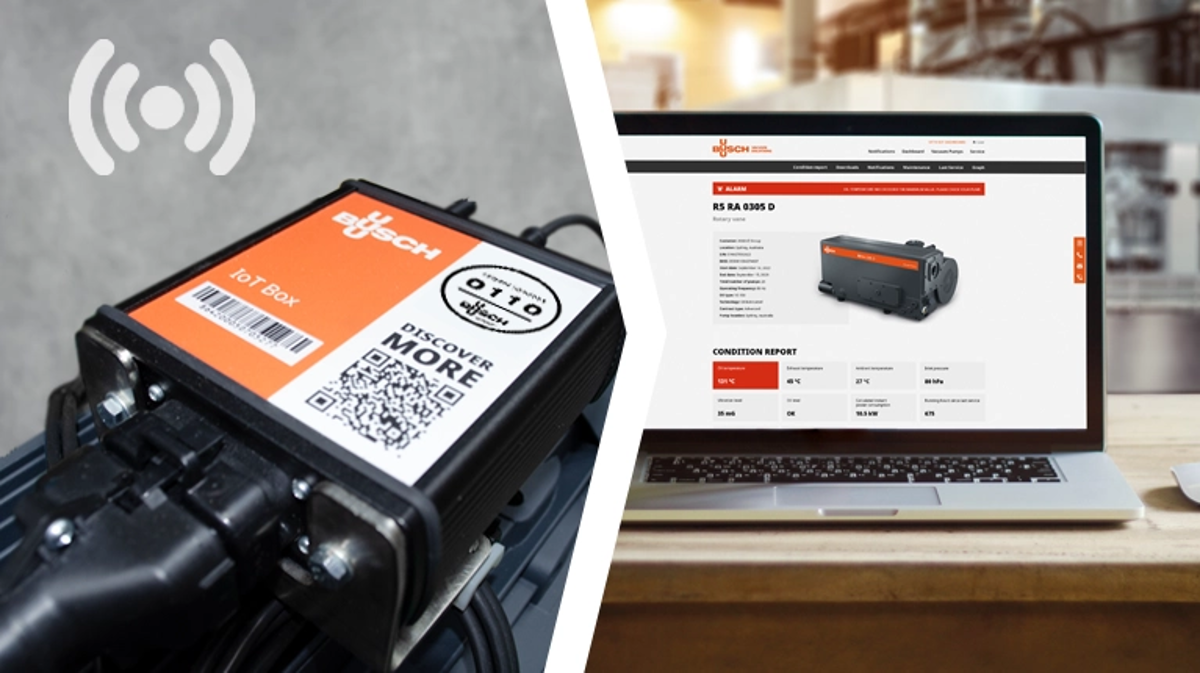
出典:Busch Vacuum Solutions
生産ダウンタイムを低減する7つの方法
生産ダウンタイムは、製造業における最大のリスクの1つです。装置の故障や原材料の不足など、どのような生産ダウンタイムであっても、収益や市場シェアに影響が及ぶ恐れがあります。
ダウンタイムには、計画されたものと予定外のものの2種類があります。
計画されたダウンタイムとは、メンテナンス、検査、リペア、アップグレード、または各種設定作業のために製造装置または工程を計画的に停止することを指します。装置を最適な状態に保ち、予定外のダウンタイムを回避するためには、メンテナンスのためのダウンタイムを計画することが重要です。計画されたダウンタイムでは、製造プロセスは中断されますが、生産性の制御は可能です。
製造装置やプロセスで予期せぬ停止や故障が起こると、予定外のダウンタイムが発生します。結果として包装できない食品が腐敗したり、生産や納期が遅れて損害につながることさえあります。さらに、稼働が不安定な場合、環境規制を遵守し、持続可能な施策を行うことがより困難になります。それが原因で環境事故が増加する可能性もあります。
したがって、生産ダウンタイムを防ぐことが生産性の確保にとってのカギとなります。
ここでは、製造ラインにある機械のダウンタイムを低減するための7つのヒントをご紹介します。
計画されたダウンタイムとは、メンテナンス、検査、リペア、アップグレード、または各種設定作業のために製造装置または工程を計画的に停止することを指します。装置を最適な状態に保ち、予定外のダウンタイムを回避するためには、メンテナンスのためのダウンタイムを計画することが重要です。計画されたダウンタイムでは、製造プロセスは中断されますが、生産性の制御は可能です。
製造装置やプロセスで予期せぬ停止や故障が起こると、予定外のダウンタイムが発生します。結果として包装できない食品が腐敗したり、生産や納期が遅れて損害につながることさえあります。さらに、稼働が不安定な場合、環境規制を遵守し、持続可能な施策を行うことがより困難になります。それが原因で環境事故が増加する可能性もあります。
したがって、生産ダウンタイムを防ぐことが生産性の確保にとってのカギとなります。
ここでは、製造ラインにある機械のダウンタイムを低減するための7つのヒントをご紹介します。
1. 製造の問題を迅速に特定し解決するためのシステムを開発する
このシステムでは、データを集めて分析し、装置のメンテナンス要件を総合的に把握できるようにする必要があります。データを解釈することで、予防保全の実施による生産上の問題解決に役立てることができます。このようなシステムを導入し機器の故障の可能性を警告することで、工場では生産トラブルによる時間のロスを削減し、コストのかかる計画外ダウンタイムを防ぐことができます。
-
出典:Busch Vacuum Solutions
2. 予測分析を用いて、潜在的な問題を事前に特定する
予測分析は、リアルタイムでマシンデータから問題の発生につながるパターンを検出します。分析に従い、機械のどの部分に故障の可能性があるかを数週間前に知らせることができます。これにより、メンテナンススケジュールの立案やスペアパーツの事前発注、ダウンタイムの短縮やトラブルの再発防止が可能になります。
-
出典:Busch Vacuum Solutions
3. 予防保全ログラムの実施
予防保全プログラムは、予定外の機械のダウンタイムを最小限に抑える最も効果的な方法の1つです。
機器に関する貴重な情報を日常的に収集することで、体系的なメンテナンスが可能になります。的確なメンテナンスにより、予測される機器の故障や事故が発生する前に対応することができます。予期せぬダウンタイムの発生を抑えることで、従業員はより収益性の高いタスクに集中できます。
機器に関する貴重な情報を日常的に収集することで、体系的なメンテナンスが可能になります。的確なメンテナンスにより、予測される機器の故障や事故が発生する前に対応することができます。予期せぬダウンタイムの発生を抑えることで、従業員はより収益性の高いタスクに集中できます。
-
出典:Piman Khrutmuang - stock.adobe.com
4. 不具合や問題が発生したときに対処するためのシステムを作る
不具合が発生したときに追跡・監視するシステムがあれば、生産ラインにおける問題の根本原因を特定することができます。そうすることで、故障がどのように発生するか、またその再発を防止するにはどうすればよいかを理解することができます。これが予定外のダウンタイムを低減し、生産効率が高まります。
-
出典:Busch Vacuum Solutions
5. できるだけ多くのプロセスを自動化し、人為的エラーを減らす
人為的エラーが発生しやすい反復的な単純作業を自動化することにより、ダウンタイムを削減し、製造プロセスをさらに効率化できます。
そうすることより、従業員は収益性の高いタスクに集中し、スキルアップを図ることができます。それが企業の利益向上につながり、また、従業員が会社にとって最も貴重なリソースであることを示すこともできます。
そうすることより、従業員は収益性の高いタスクに集中し、スキルアップを図ることができます。それが企業の利益向上につながり、また、従業員が会社にとって最も貴重なリソースであることを示すこともできます。
-
出典:Gorodenkoff - stock.adobe.com。
6. オペレーター向けに装置の正しい操作方法のトレーニングを実施する
オペレーターに装置を適切に使用するためのトレーニングを行うことで、製造プロセスのダウンタイムを大幅に低減できます。オペレーターが装置の正しい使用方法を知っていれば、プロセスを停止する可能性が低くなるほか、緊急事態にも迅速に対応できるようになります。適切なトレーニングを行うことで、人為的ミスによる予定外のダウンタイムが防止され、職場での事故のリスクも低減されます。
-
出典:Busch Vacuum Solutions
7. インテリジェントなIoTソリューションを使用する
ここまで6つのヒントをご紹介しましたが、多すぎると感じた方もいるのではないでしょうか。そこで、ヒント7では、オールインワンのソリューションをご紹介します。
インテリジェントなIoTソリューションは、生産上の問題を迅速に特定して解決するシステムを提供することで、ダウンタイムの低減に役立ちます(ヒント1)。予測分析により装置やプロセスを追跡、監視し、メンテナンススケジュールの作成や必要なスペアパーツの事前発注を可能にします(ヒント2)。センサーとデータ分析により、IoTでは装置のパフォーマンスとプロセスの最適化データを継続的に追跡し監視することができます。これにより、予防保全(ヒント3)と潜在的な問題の発生を予測する(ヒント4)機会が得られ、計画的または非計画的なダウンタイムの頻度を効果的に低減することができるのです。また、IoTでは、タスクの自動化とタスク完了までの所要時間の短縮を実現し、生産性の向上と人為的エラーの削減を達成できます(ヒント5)。ツールが使いやすいため、IoTの操作方法は簡単です。すぐに正しい使い方ができるようになります(ヒント6)。IoTシステム導入によるプロセス最適化を是非ご検討ください。Busch IoT DashboardとBusch Vacuum Appが、お客様の真空プロセスのモニタリングにどのように役立つかをご紹介します。またBuschは、収集したデータの分析に基づき必要な時にサービススタッフを自動で派遣することで、予防保全も提供可能です。
インテリジェントなIoTソリューションは、生産上の問題を迅速に特定して解決するシステムを提供することで、ダウンタイムの低減に役立ちます(ヒント1)。予測分析により装置やプロセスを追跡、監視し、メンテナンススケジュールの作成や必要なスペアパーツの事前発注を可能にします(ヒント2)。センサーとデータ分析により、IoTでは装置のパフォーマンスとプロセスの最適化データを継続的に追跡し監視することができます。これにより、予防保全(ヒント3)と潜在的な問題の発生を予測する(ヒント4)機会が得られ、計画的または非計画的なダウンタイムの頻度を効果的に低減することができるのです。また、IoTでは、タスクの自動化とタスク完了までの所要時間の短縮を実現し、生産性の向上と人為的エラーの削減を達成できます(ヒント5)。ツールが使いやすいため、IoTの操作方法は簡単です。すぐに正しい使い方ができるようになります(ヒント6)。IoTシステム導入によるプロセス最適化を是非ご検討ください。Busch IoT DashboardとBusch Vacuum Appが、お客様の真空プロセスのモニタリングにどのように役立つかをご紹介します。またBuschは、収集したデータの分析に基づき必要な時にサービススタッフを自動で派遣することで、予防保全も提供可能です。
FAQ
生産ダウンタイムとは何ですか?
- ダウンタイムとは、製造プロセスが停止している間の時間を指します。ダウンタイムには、計画されたものと予定外のものの2種類があります。
- 計画されたダウンタイムとは、メンテナンス、検査、リペア、アップグレードを実施するために製造装置を計画的に停止することを指します。
- 予定外のダウンタイムとは、製造装置やプロセスの予期せぬ停止や故障を指します。
生産ダウンタイムはどのように計算するのですか?
生産ダウンタイムのコストは、次の計算式を使用して計算されます:
ダウンタイム率 =(ダウンタイムの時間/予定稼働時間)* 100
平均的なダウンタイムはどれくらいですか?
製造業では、機器のダウンタイムにより、年間平均800時間、週当たり15時間以上の生産時間が失われています。
一般的なパルメザンチーズ工場に当てはめて考えてみましょう:
パルメザンチーズの塊1個の重さは平均42kgです。価格を1kgあたり9ユーロとすると、1個のパルメザンチーズの価値は378ユーロとなります。1分あたり3個のパルメザンチーズを生産できるため、1時間あたりの金額は68,040ユーロとなります。
このパルメザンチーズ工場で、装置の故障による予定外のダウンタイムが1週間で15時間あるとすると、1,020,600ユーロの損失が発生することになります。