Continental Reifen Deutschland GmbH社は、ドイツ アーヘンの工場で自動車用の高品質タイヤを製造しています。Continental社のタイヤ製造プロセスは、極めて有効で効率的な真空生成方式を採用しており、Busch Vacuum Solutionsの集中真空システムが3台の繊維裁断機に真空を供給することで機械を正確に稼働させています。この真空ソリューションは、製造現場の騒音を大幅に低減するだけでなく、エネルギーコストやメンテナンスコストも削減します。
ヨーロッパでは、ほぼ3台に1台の車がContinental社のタイヤを装着しています。同社は、天然ゴムの原材料を独自に配合して押出成形し、いくつかの中間工程を経て、完成品に仕上げます。基本的に1本のタイヤは、繊維ロープ、スチールワイヤー、天然ゴム配合物という主に3つの要素で構成されます。この3つの基本材料を所定の方法で組み合わせて個々のコンポーネントを作り、カーカスやベルトとして組み立てた後、タイヤとして成形し、硬化させます。
繊維ロープは多数の繊維から成り、大型の巻取装置によってカレンダー機に挿入されます。カレンダー機は繊維ロープを天然ゴムでコーティングし、厚さ1mm以下の長い帯状シートに成形します。このシートを繊維の向きに対して垂直に、必要な幅に裁断した後、再び巻いて次の工程に運びます。その後、繊維素材はゴムの最も内側の層に直接貼り付けられます。これが、タイヤの内側の補強材の役割を果たします。繊維を放射状に配置することで、安定性はさらに高まります。この層は、主にタイヤの運搬能力、サスペンションの挙動、ハンドリング特性に影響します。
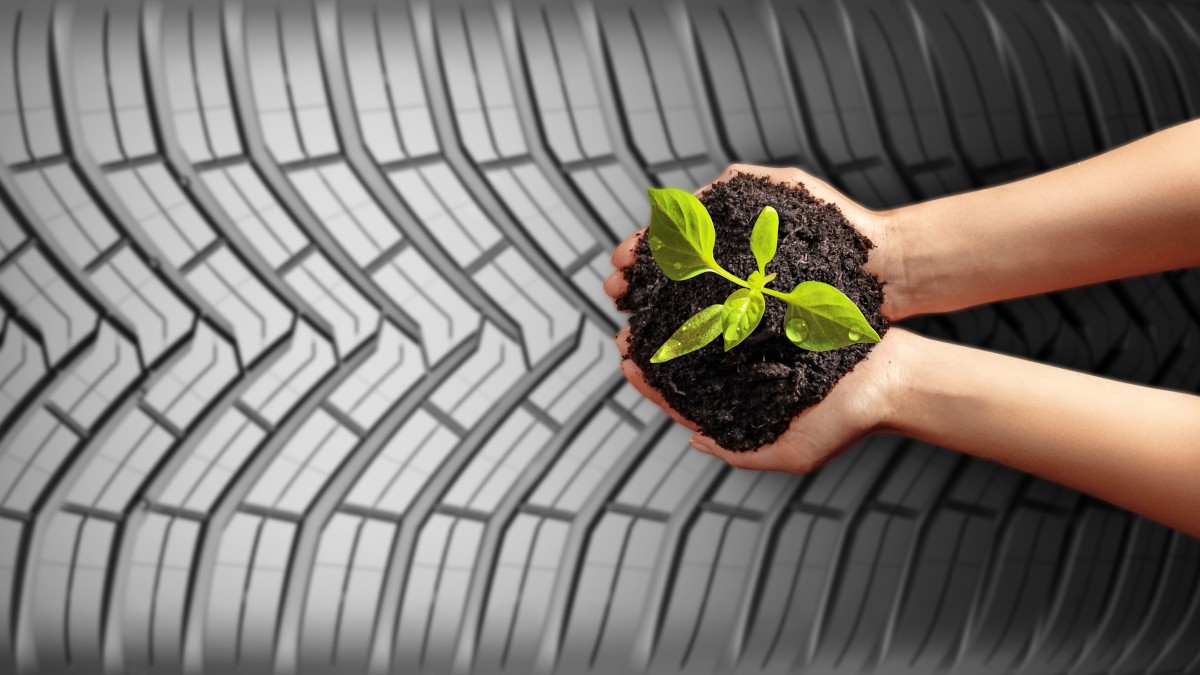
図1:Continental社のタイヤは、Buschの最先端の真空テクノロジーを使用して製造されています。写真:Continental Reifen GmbH。
新しい真空ソリューションがContinental社の安全で持続可能なタイヤ貢献
Continental Reifen Deutschland GmbH
繊維裁断機での真空の利用
繊維裁断機でのハンドリングには真空テクノロジーが利用されています。ゴム引きシートは目的の長さに裁断され、ピックアンドプレースを利用して別シートに直接重ねられます。最終的な繊維シートの品質にとって、ここでの精密な配置は極めて重要で、 個々の層を正確に重ねていく必要があります。以前は、3台の裁断機のそれぞれにサイドチャネルブロワーが1台ずつ設置されていました。 これらのブロワーが繊維シートのハンドリングに必要な真空を供給していましたが、 常に最大出力で運転され、大量のエネルギーを消費していました。その上、ひどい騒音を発し、製造スタッフの健康に影響を与えていました。
繊維裁断機向けの持続可能なBuschの真空供給
Continental Reifen社の1人の従業員が、社内のアイデアマネジメントを通じ、真空を利用した裁断機の検討を提案しました。従業員にとっての最大の問題は、以前から使われていたサイドチャネルブロワーによる深刻な騒音でした。Continental社は常に改善の可能性を探っていたため、より人間工学に即した効率的なソリューションを探すことにしました。Busch Vacuum Solutionsの真空スペシャリストは、真空生成にMINKクロー真空ポンプを使用することを推奨し、まずテスト用のシステムを提供しました。ユーティリティーおよび持続可能なインフラ担当の責任者であるIngmar Heinze氏は、数日もかからず、真空生成の適切なソリューションを見つけたと確信しました。試運転後、MINK MV Synchro真空ポンプ2台を搭載した真空システムがContinental社に設置されました。このシステムが従来の3台のサイドチャネルブロワーに代わって、複数の繊維裁断機に必要な真空をステンレスパイプ経由で集中供給するようになりました。MINK MV Synchro真空ポンプには周波数コンバーターとデマンド式の制御ユニットが標準装備されています。真空ポンプは必要な排気速度を検出し、繊維ロープを埋め込んだゴムシートを正確に保持し、配置する連続的なプロセスに供給します。
-
図2:2台のMINK MVクロー真空ポンプを利用した、繊維ロープのハンドリングに使用される真空供給。出典:Busch Vacuum Solutions.
繊維裁断におけるBuschの真空供給のメリット
この新しい真空システムのメリットは、騒音という主要な問題の解消だけではありませんでした。以前使用していたサイドチャネルブロワーの騒音値は94 dBにも達しており、 製造現場のスタッフに騒音の被害が及ぶレベルでした。Buschの新しい真空システムでは、真空ユニットの騒音が通常の周辺雑音にかき消され、騒音値を測定できないほど(72 dB未満)です。このように大幅な騒音の低減だけでなく、新しい真空システムは大幅な省エネももたらしました。デマンド式の制御により常にフル性能で真空システムを稼働する必要がなく、回転数と消費電力を抑えられる場合も少なくありません。また、繊維ロープのホールドが必要ないときには、システムが自動的にシャットダウンされます。以前に使用していたブロワーの消費電力は、通常15 kWhでしたが、 新しい真空システムで測定したところ、1時間あたりの平均消費電力はわずか800ワットでした。
これは、90%以上のエネルギーコストの削減に相当します。そのため、投資を速やかに回収できるほか、エネルギーの面でも、ドイツ連邦経済 輸出管理庁(BAFA)の助成を受けることができます。
さらに、新しいソリューションは年間メンテナンスコストも90%近く削減します。サイドチャネルブロワーには集中的なリペアが必要であり、それが高いコストの要因となっていました。MINKクロー真空ポンプは完全にドライな圧縮原理を採用しており、潤滑油や作動液を使いません。そのため、この真空ポンプはほぼメンテナンスフリーとなっています。以前は整備のためのダウンタイムも問題の1つでした。2台のMINKクロー真空ポンプを搭載した新しい真空システムでは、1台でちょっとした整備作業を行っている間も、もう1台がシステムに真空を供給し続けます。つまり、繊維裁断機の運転を中断することなく、高い可用性が得られるということになります。
新しい真空システムは1月から稼働しており、Ingmar Heinze氏は満足しています。
タイヤ製造中の繊維シートのハンドリングに使用する新しい真空供給システムは順調に稼働しています。従業員に対する騒音の影響を大きく低減し、エネルギー消費量やメンテナンスの手間を抑える一方、生産性は向上しました。これこそ持続可能な改善の好例です。
-
図3:Continental Reifen Deutschland GmbHにある繊維裁断機の真空供給用パイプライン。出典:Busch Vacuum Solutions.