Jedi Kunststofftechnik GmbHは、軟質PVCロール、シート、ウェブ素材のトップメーカーとして、特に軟質PVCの加工を中心に製造を行ってきました。材料は、納入された大袋から吸引式空気搬送システムを介して押出成形機に供給されます。
このたび、搬送システムの真空生成を再設計して導入することにしました。Jedi Kunststofftechnikでは、2018年の初めから、速度制御付きのMINKクロー真空ポンプを利用していますが、これはそれ以前に使用していたサイドチャネルブロワーよりもはるかにエネルギー効率が高くなっています。これにより、真空生成のためのエネルギー消費量を最大で70%削減することができました。
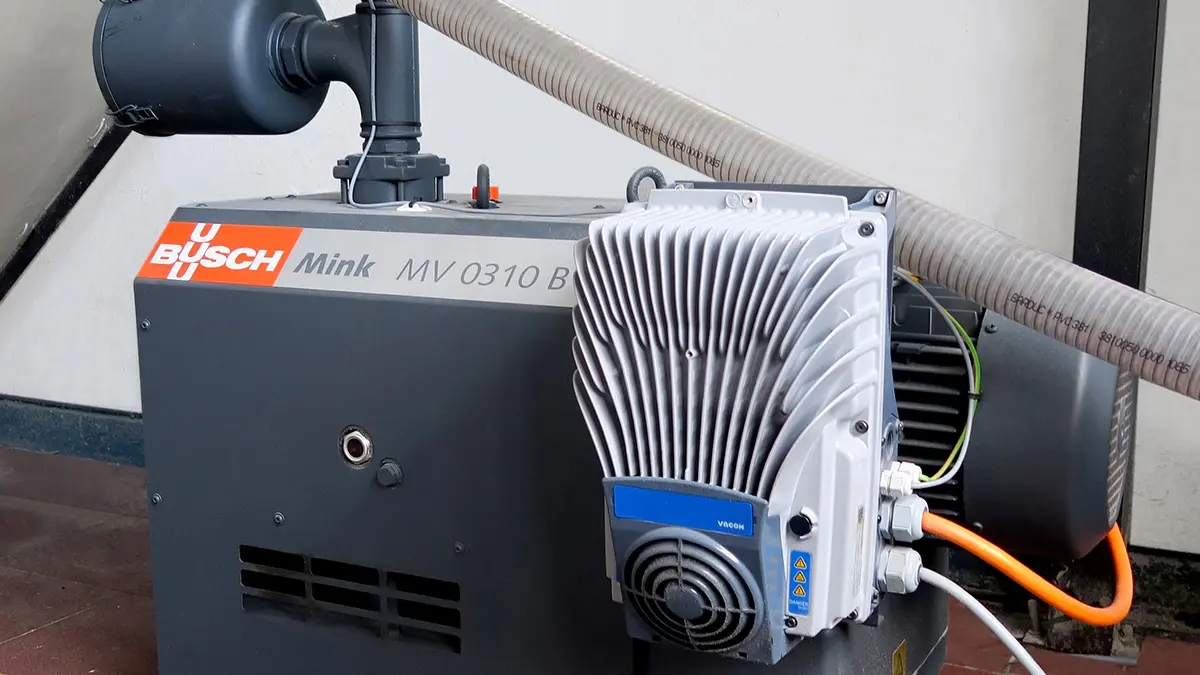
図1:Jedi Kunststofftechnikの輸送システムの真空供給に利用されているBuschの3基のMINK MV 0310 Bクロー真空ポンプのうちの1基 出典:Busch Vacuum Solutions.
材料供給に最新の真空テクノロジーを採用したことにより最大で70%の省エネを実現
Jedi Kunststofftechnik GmbH
Marco Di Martino氏は、1990年代半ばにノルトライン ヴェストファーレン州のエイトドルフに主に透明な軟質PVC半製品を扱うJedi Kunststofftechnik社を設立しました。現在、同社は40人の従業員を抱え、軟質PVCロール、シート、繊維の世界的なトップメーカーとなっています。これらの材料は、同社の顧客によって、ストリップカーテンや床の保護マット、ローラーシャッターやテントの柔軟性のある視認窓などに加工されています。3交代制で製造されている製品は、厚さ1~12 mm、最大ロール幅2,200 mmであり、ヨーロッパ各地の顧客に供給されています。吸引式空気輸送システム
製造は単軸の押出成形機を使った5つの押出ラインで行われています。材料は、大袋から定量供給システムや乾燥機を経て、吸引式空気輸送システムを経由で押出成形機に供給されます。以前は、4本の押出成形ラインに4基のサイドチャネルブロワーを設置して、輸送システムに必要な真空を供給していました。ベアリングやエンジンの損傷、ホイールのさびなどによる不具合の割合が高く、サイドチャネルブロワーは信頼性の低い真空発生器となっていました。4基のサイドチャネルブロワーの消費電力は、ブロワサイズに応じ異なりますが、12.5~15 kWでした。運転も制御されておらず、3交代制の間ブロワーが連続運転されていました。消費電力や信頼性の面で、オーナーのMarco Di Martino氏にとっては満足できないソリューションでした。また、製造場所のブロワーから出る高い騒音値も大きな問題となっていました。
プロセスの最適化
Busch Vacuum Solutionsと連絡をとり、Buschの真空スペシャリストによる輸送システムの測定が行われました。測定の結果、サイドチャネルブロワーが、常時絶対圧力700 hPa(mbar)という性能限界で稼働していることが分かりました。この圧力では、サイドチャネルブロワーは設計排気速度の約30%にしか到達できません。このデメリットを解消するために、設計排気速度の高い大型のブロワーが使用されていましたが、結果としてエネルギー消費量が増えました。高い差圧とそれに伴う低い排気速度が、ブロワーの過熱とそれによる故障の原因となっていました。このように真空供給の実際の状況を分析した結果、Buschは新しいクロー真空ポンプ、MINK MV 0310 Bの導入を提案しました。絶対運転圧力が700 hPa(mbar)であっても、このポンプでは排気速度が低下しません。このポンプは周波数コンバーターを標準装備しています。デマンドに応じ自動的に回転速度を変え、排気速度を調整します。MINK MVクロー真空ポンプの到達真空はサイドチャネルブロワーよりもはるかに優れ、最大で150 hPa(mbar)(絶対値)に達します。Marco Di Martinoは、2018年よりそれまでに設置されていた4基のサイドチャネルブロワーに替えて2基のMINK MV 0310 Bクロー真空ポンプ(図1)を使用しています。4基のサイドチャネルブロワーの消費電力が合計で55 kWだったのに対し、MINKクロー真空ポンプは50 Hz運転でそれぞれ8 kWしか必要としません。Jedi Kunststofftechnikでは、5つ目の押出成形ラインの立ち上げ時にもMINK MV 0310 Bをさらに1基設置しました。3基すべての真空ポンプが、カスケード型の制御システムを介して運転されています。上流にある2個のタンクにより、合計で1,000リットルのバッファ容量が確保されています。3基のMINK MVクロー真空ポンプのうち1基は、タンク内の絶対圧力が500 hPa(mbar)を超えると自動的に起動する仕組みになっています。他の2基の真空ポンプは、700 hPa(mbar)の絶対圧力に達するとオンになり、1基目の真空ポンプをサポートします。圧力や排気速度の微調整は、可変速ドライブで補われています。
実際には、1~2基のMINK真空ポンプで十分な流量を確保できます。3基目の真空ポンプは、ピーク需要時にのみ使用されます。運用開始後6か月が経過し、オーナーのMarco Di Martino氏は非常に満足しています。まず、押出成形ラインが4本から5本に増えたにもかかわらず、真空供給(図2)の消費電力を55 kWから24 kWに減らすことができました。また、新しいMINK MV 0310 Bの速度制御のおかげで、連続運転される真空ポンプは1基もなく、実際に需要のあるときにだけ運転されるようになりました。2018年の電気代には、エネルギーコストの削減効果がはっきり現れています。前年比で消費電力は160,000 kW時削減されました。これは、年初にはサイドチャネルブロワーがまだ使用されており、後から5番目の押出成形ラインが追加されたという状況で達成された成果です。
-
図2:MINK MVクロー真空ポンプの断面図。出典:Busch Vacuum Solutions.
以前はブロワーの故障や修理が頻繁に発生していましたが、Busch社の新型クロー式真空ポンプではまったく問題が発生していません。ダウンタイムや修理にかかるコストに加えて、個々の押出成形ラインのスループットにも好影響が及んでいます。また、新しい真空ポンプの騒音値は、以前のサイドチャネルブロワーよりもかなり低くなっています。Marco Di Martino氏は、押出成形ラインのすぐ隣にある製造室では、騒音をまったく感じないと述べています。MINK MVクロー真空ポンプは、必要なメンテナンスも最小限です。メーカーであるBuschは、ギアオイルの交換は、最大で20,000時間の使用後にのみ行うことを推奨しています。