PolyComp GmbHは、コンパウンドのスペシャリストとして、特殊なエンジニアリングプラスチックの受託製造とライセンスによる製造を行っています。その製品は、耐熱プラスチックや高強度の熱可塑性樹脂から、柔らかく柔軟性のある熱可塑性エラストマーまで多岐にわたり、要望に応じてさまざまな添加剤の組み合わせにも対応しています。取り扱う製品が幅広いため、何種類もの押出し機や特殊なスクリューを使い分けられる、フレキシブルな生産設備が必須です。
ただし、どの押出成形機にも共通していることがあります。同社では、スクリュー部で溶融材料からベーパーやガスを抽出するために、Busch Vacuum SolutionsのPLASTEX脱気システムのみを利用しています。MINKクロー真空ポンプを搭載したこのシステムは、信頼性が高く、メンテナンスも容易です。
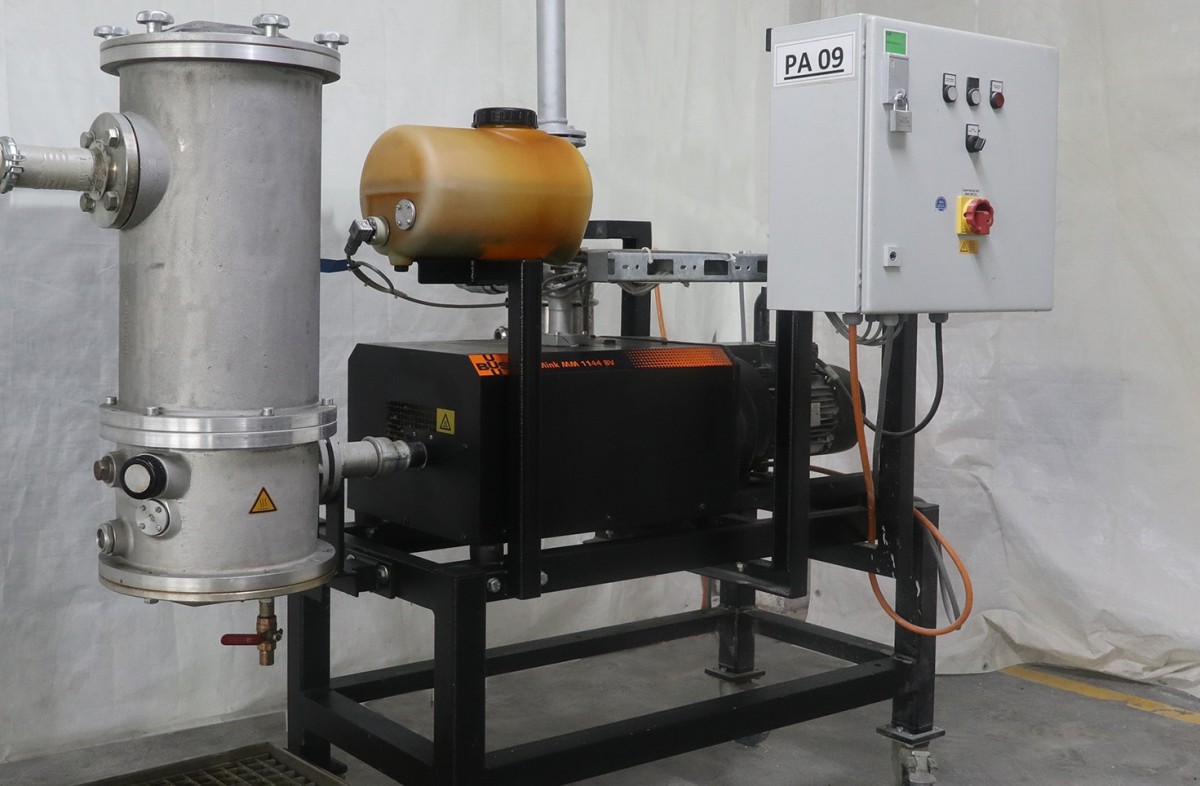
押出成形時の溶解脱気用の最新の真空テクノロジー
-
図1:PolyComp社の7基のPLASTEX脱気システムのうちの1基。これらは押出成形機とは別のフロアに設置されています。
PolyComp社について
PolyComp社は、2000年に経営陣による企業買収で設立され、本社はドイツ、ハンブルク郊外のノルダーシュテットにあります。2013年、PolyComp社は、ハンブルクを拠点とし、化学およびテクノロジー製品のグローバルな取引に重点を置くFeddersenグループに買収されました。PolyComp社は、ポリオレフィン(PP/PE)、EVA、PA、PBT、PC、ABS、EVOH、POM、PMMAなどのコンパウンドの製造を主力事業としています。これらのコンパウンドには、炭素繊維や天然繊維、単純な充填剤からガラスビーズ、着色剤やワックスなど、さまざまな添加剤が混合されます。
フィルム用コンパウンド
同社が得意とするのがフィルム用コンパウンドですが、ここでは必要なゲル量が非常に少なくなっています。製造には特殊なスクリューを使った押出し工程や、高いフィルタリング精度のスクリーンチェンジャーを使った工程もあります。同社は、合計で8台のシングルまたはツインスクリューによる押出成形機を使用しています。6台の押出成形機で溶融材料の脱気が行われています。2009年までは、このプロセスに水封式真空ポンプが利用されていましたが、ガスやベーパーが水に混ざって凝結するため、使用済みの水の処理の問題が生じるようになりました。水の処理や廃棄のためのコストはかさむ一方でした。
Production Managerのアシスタントを務めるHenning von Brühl氏は次のようにコメントしています:「どのような物質が水に混入するかを正確に予測することはできませんでした。真空ポンプの封液には、ベースとなる物質のガスや蒸気、ポリマーだけでなく、添加剤の一部も混入することがありました。」 この原因は、製品が幅広く、扱うコンパウンドの種類が多いことにありました。ベースとなる物質が同じであっても、さまざまな添加剤の使用により水に含まれる物質の組成が変化することがあります。PolyComp社は週5日、3交代制で操業しているため、処理しなければならない水が大量に発生していました。
当社のソリューション
2009年、環境に配慮したソリューションを求めていた同社は、封液不要のPASTEX脱気システム(図1)を提供しているBuschに連絡することにしました。MINKクロー真空ポンプ(図2)と上流のスタンディングフィルターおよび精密ろ過フィルターがこのシステムの中心です。フィルターは凝結水と固形物を分離するために使用されます。MINKドライクロー真空ポンプには、水やオイルなどの作動流体が不要です。つまり、ポンプを通過したベーパーやガスが作動流体と接触することがなく、混合や反応も起こりません。しかし、精度の高いセパレーター技術でも、残留モノマーがポンプ内部に入り込み、ポンプの劣化や副生成物の原因となることを防ぐことはできません。そのため、このMINKクロー真空ポンプにはフラッシング装置を付属させています。この装置のおかげで、決められた間隔で正確にフラッシング液を真空ポンプに供給することができるため、副生成物解消に役立っています。Maintenance ManagerのStefan Stolpは、押出成形機にかける材料ごとにフラッシング液の量とフラッシングの間隔を定義しました。フラッシングプロセスは、ダウンタイム中だけでなく製造中にも実行できます。-
図2:PLASTEX脱気システムの中核となるMINKクロー真空ポンプ。非接触式の動作原理により、潤滑油や作動流体が不要です。
最初のPLASTEX脱気システムの購入後、PolyComp社は順次すべての水封式真空ポンプと交換していきました。Stefan Stolp氏はこのソリューションに大変満足しています。まず、廃水の問題が解消されました。さらに、PLASTEX脱気システムは非常に信頼性が高く、メンテナンス作業がほぼ不要となっています。フィルターは定期的に清掃し、必要に応じてフラッシング剤を補充する必要があります。補充の間隔は、製品の原料によって異なります。この作業は、製造チームのメンバーが直接行います。メンテナンスチームは、平均で10か月経過後にすべての真空ポンプを分解して清掃するようにしています。Henning von Brühl氏は、「全体的に見て、以前の水封式真空ポンプと比較し非常に管理しやすい作業量です」と述べています。
エンジニアのSimone Patermann氏は、PLASTEX脱気システムを利用することのもう1つのメリットを見つけました。エネルギーマネジメントシステムの国際規格であるISO 50001の認証を取得しているという理由だけではありませんが、PolyCompの生産部門の責任者である同氏は、エネルギー消費量に常に注目しています。
これには2つの主な要因があります。まず、作動流体がまったく不要であるため、作動液を運ぶための動力も不要となります。次に、Minkクロー真空ポンプは完全な非接触式です。その結果、部品同士が擦れ合わないため、摩擦抵抗による余計な動力の需要も生じません。
2018年、PolyComp社は新しい押出成形ラインを立ち上げました。その心臓部となったのが、最大出力1,500 kg/hの2軸押出成形機です。2台のサイドフィーダー(図3)により、異なる種類の粉体ベースの充填素材を同時に添加し、高い出力で混合することができます。1台のサイドフィーダーをPLASTEX脱気システムに接続できます。これにより、脱気なしのサイドフィーダーと比較して充填素材の体積を減らし、かさ密度を3倍にすることが可能となりました。それが生産量のアップにつながります。
エンジニアのSimone Patermann氏は、PLASTEX脱気システムを利用することのもう1つのメリットを見つけました。エネルギーマネジメントシステムの国際規格であるISO 50001の認証を取得しているという理由だけではありませんが、PolyCompの生産部門の責任者である同氏は、エネルギー消費量に常に注目しています。
MINKクロー真空ポンプは、他の原理と比較し最も効率の高い真空原理を採用しています。そのため、性能クラスが同等の真空ポンプと比較し省エネです。
2018年、PolyComp社は新しい押出成形ラインを立ち上げました。その心臓部となったのが、最大出力1,500 kg/hの2軸押出成形機です。2台のサイドフィーダー(図3)により、異なる種類の粉体ベースの充填素材を同時に添加し、高い出力で混合することができます。1台のサイドフィーダーをPLASTEX脱気システムに接続できます。これにより、脱気なしのサイドフィーダーと比較して充填素材の体積を減らし、かさ密度を3倍にすることが可能となりました。それが生産量のアップにつながります。
-
図3:ツインスクリュー押出成形機に設置された2台のサイドフィーダー。PLASTEX脱気システムが、充填材料供給時の体積の削減に貢献します。出典:PolyComp
PolyComp社の経営陣は、信頼性、メンテナンスの手間、経済的効率性の面でBuschのPLASTEX脱気システムを選んだのは正しい選択だったと述べています。信頼性の高さは、製造にも好影響を与えます。以前使用していた水封式真空ポンプで生じていた故障や修理、清掃などによるダウンタイムは過去のものとなりました。