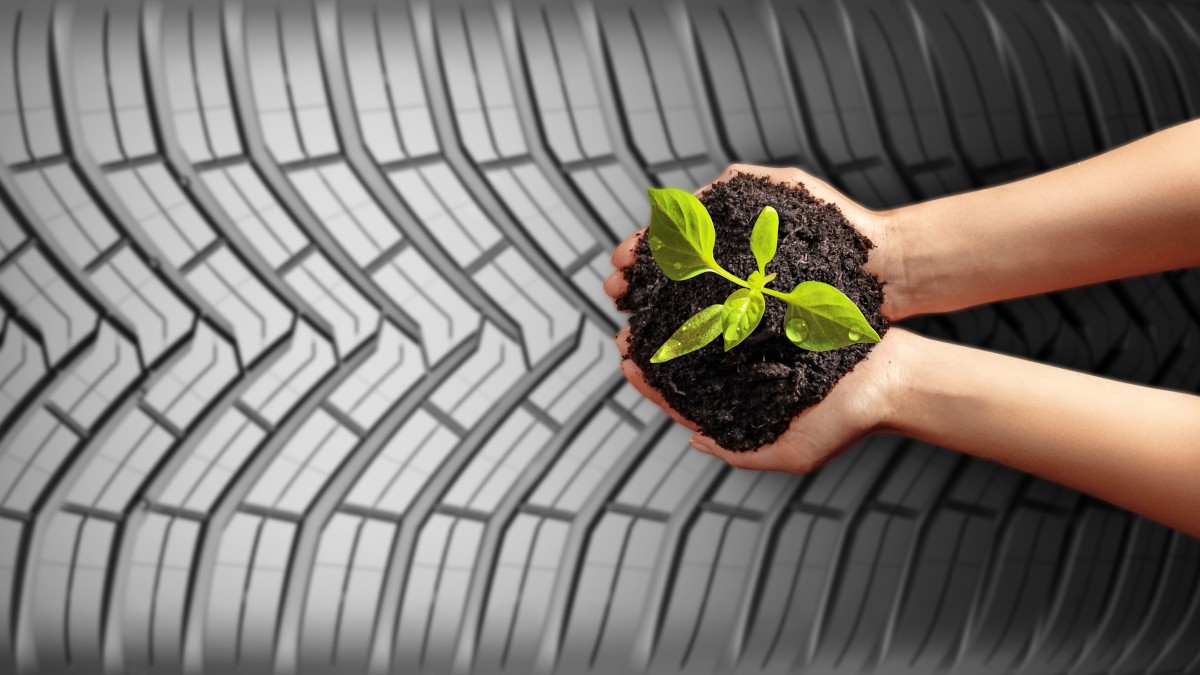
Fig. 1: Continental-däck tillverkas med hjälp toppmodern vakuumteknik från Busch. Foto: Continental Reifen GmbH.
Ny vakuumlösning garanterar säkra och hållbara däck hos Continental
Continental Reifen Deutschland GmbH
Continental Reifen Deutschland GmbH tillverkar däck av hög kvalitet för bilar och vans på produktionsanläggningen i Aachen i Tyskland. I däcktillverkningen använder Continental en extremt effektiv metod för vakuumgenerering, där en central vakuumförsörjning från Busch Vacuum Solutions levererar nödvändigt vakuum för att säkerställa säker hantering på tre textilskärmaskiner. Utöver att minska bullret i produktionsutrymmet leder den här vakuumlösningen även till stora besparingar när det gäller däcktillverkarens energi- och underhållskostnader.
Nästan vart tredje fordon i Europa kör på däck tillverkade av Continental, som själv blandar råmaterialet av naturgummi, därefter extruderar det och efter flera mellansteg, tillverkar monteringsklara däck av det. Ett enda däck består huvudsakligen av tre huvudkomponenter: textilkord, ståltråd och naturgummiblandning. Dessa tre grundmaterial kombineras på ett specifikt sätt i däckets individuella komponenter och monteras sedan som stomme och bälte, formas till ett däck och härdas.
Textilkorden består av ett stort antal textiltrådar och förs in i en mangel med en stor upprullningsenhet. Det är där textilkorden beläggs med naturgummi och en gummerad väv skapas i form av en kontinuerlig lång remsa som är mindre än en millimeter tjock. Den här väven kapas i önskad bredd, vinkelrätt mot trådmönstret och rullas samman till en textilrulle för fortsatt bearbetning. Textilmaterialet fäst senare direkt på det innersta gummilagret. Det fungerar som armeringselement på däckets insida. Trådarnas radiella orientering säkerställer ytterligare stabilitet. Det här lagret påverkar primärt däckets bärförmåga samt fjädringens beteende och hanteringskarakteristiken.
Nästan vart tredje fordon i Europa kör på däck tillverkade av Continental, som själv blandar råmaterialet av naturgummi, därefter extruderar det och efter flera mellansteg, tillverkar monteringsklara däck av det. Ett enda däck består huvudsakligen av tre huvudkomponenter: textilkord, ståltråd och naturgummiblandning. Dessa tre grundmaterial kombineras på ett specifikt sätt i däckets individuella komponenter och monteras sedan som stomme och bälte, formas till ett däck och härdas.
Textilkorden består av ett stort antal textiltrådar och förs in i en mangel med en stor upprullningsenhet. Det är där textilkorden beläggs med naturgummi och en gummerad väv skapas i form av en kontinuerlig lång remsa som är mindre än en millimeter tjock. Den här väven kapas i önskad bredd, vinkelrätt mot trådmönstret och rullas samman till en textilrulle för fortsatt bearbetning. Textilmaterialet fäst senare direkt på det innersta gummilagret. Det fungerar som armeringselement på däckets insida. Trådarnas radiella orientering säkerställer ytterligare stabilitet. Det här lagret påverkar primärt däckets bärförmåga samt fjädringens beteende och hanteringskarakteristiken.
Användning av vakuum till textilskärmaskiner
Vakuumteknik används för hanteringsuppgifter vid textilskärmaskinen. Gummiväven skärs till önskad längd och appliceras sedan direkt på en annan remsa genom att ta och placera. Här är exakt positionering den mest kritiska aspekten när det gäller kvaliteten på den färdiga textilväven. De individuella lagren måste ligga exakt ovanpå varandra. En sidokanalfläkt installerades tidigare i var och en av de tre textilskärmaskinerna. De tillhandahöll nödvändigt vakuum för hantering av textilremsorna. Fläktarna körde konstant på full effekt och förbrukade därmed enorma mängder energi. Dessutom utsatte de produktionspersonalen för kraftigt buller.
Hållbar Busch vakuumförsörjning för textilskärmaskiner
En anställd hos Continental Reifen föreslog via den interna Idea management att någon borde ta en närmare titt på vakuumförsörjningen till textilskärmaskinerna. Det huvudsakliga problemet var den höga bullernivån på grund av sidokanalsfläktarna som användes tidigare. Eftersom Continental alltid försöker hitta potentiella sätt att bli bättre beslutade de sig för att söka efter en mer ergonomisk och effektiv lösning. Vakuumexperter på Busch Vacuum Solutions rekommenderade att använda en MINK klovakuumpump för att generera vakuum och tillhandahöll inledningsvis ett testsystem. Det tog ett par dagar för Ingmar Heinze, chef över Utilities and Sustainable Infrastructure, att bli övertygad om att han hade hittat rätt lösning för att generera vakuum. Efter testkörningen installerades ett vakuumsystem med två MINK MV Synchro vakuumpumpar hos Continental. Det här systemet ersatte de tidigare tre sidokanalsfläktarna och levererar nu nödvändigt vakuum för flera textilskärmaskiner via rostfria stålrör. MINK MV Synchro vakuumpumpar har en frekvensomvandlare och behovsstyrd styrenhet som standard. Vakuumpumparna detekterar vilken pumphastighet som de behöver tillhandahålla under en pågående process för att säkert hålla den gummerade textilkorden och placera den exakt.
-
Fig. 2: Vakuumförsörjning med två MINK MV klovakuumpumpar för hantering av textilkordar. Källa: Busch Vacuum Solutions.
Fördelar med Busch vakuumförsörjning inom textilskärning
Lyckligtvis gjorde användningen av detta nya vakuumsystem mer än att bara lösa huvudproblemet med buller. De tidigare sidokanalsfläktarna uppnådde bullernivåer på 94 dB. Det innebar höga bullernivåer för personalen i tillverkningshallen. Med det nya vakuumsystemet från Busch går det inte ens att detektera någon bullernivå från vakuumenheten eftersom den drunknar i det normala omgivningsbullret – vilket innebär att det är lägre än 72 dB.Utöver den avsevärda bullerminskningen ledde det nya vakuumsystemet även till avsevärda energibesparingar. Tack vare den behovsdrivna styrningen är det inte alltid full prestanda används, vilket innebär att vakuumsystemet ofta arbetar vid lägre varvtal och strömförbrukning. Systemet stängs även av automatiskt om det inte finns några textilremsor att hålla. Strömförbrukningen för fläktarna som användes tidigare var vanligtvis 15 kWh. När man gjorde mätningar med det nya vakuumsystemet fastställdes en genomsnittlig energiförbrukning på bara 800 watt per timme.
Det innebär energikostnadsbesparingar på mer än 90 procent. Så investeringen betalade sig själv direkt och, sett utifrån energiaspekten, är den berättigad för finansiering från BAFA (Bundesamt für Wirtschaft und Ausführungskontrolle).
Den nya lösningen sparar även närmare 90 procent av de årliga underhållskostnaderna. Sidokanalsfläktarna krävde intensiva reparationer och var därför en källa till höga kostnader. MINK MV klovakuumpumar tillhandahåller helt torr komprimering av insugsluften och arbetar därmed utan driftsvätskor som olja eller vatten. Det gör att vakuumpumparna kräver minimalt underhåll. Stilleståndstider för service brukade också utgöra ett problem. För det nya vakuumsystemet med två MINK klovakuumpumpar kan de få nödvändiga serviceuppgifterna utföras på en av de två vakuumpumparna medan den andra fortsätter att leverera vakuum till systemet. Det innebär att det inte längre krävs några avbrott och högre tillgänglighet för textilskärmaskinerna.
Det nya vakuumsystemet har varit i drift sedan januari – till Ingmar Henzes fullständiga belåtenhet.
”Vi är mycket nöjda med vår nya vakuumförsörjning för hantering av textilremsor under däcktillverkningen. Vi kunde inte bara minska bullernivån för våra anställda utan kunde även avsevärt minska energiförbrukningen och underhållsarbetet och öka systemets produktivitet. Detta är ett förstklassigt exempel på hållbar förbättring!”
-
Fig. 3: Rörledningar för vakuumförsörjnigen till textilskärmaskinerna hos Continental Reifen Deutschland GmbH. Källa: Busch Vacuum Solutions.