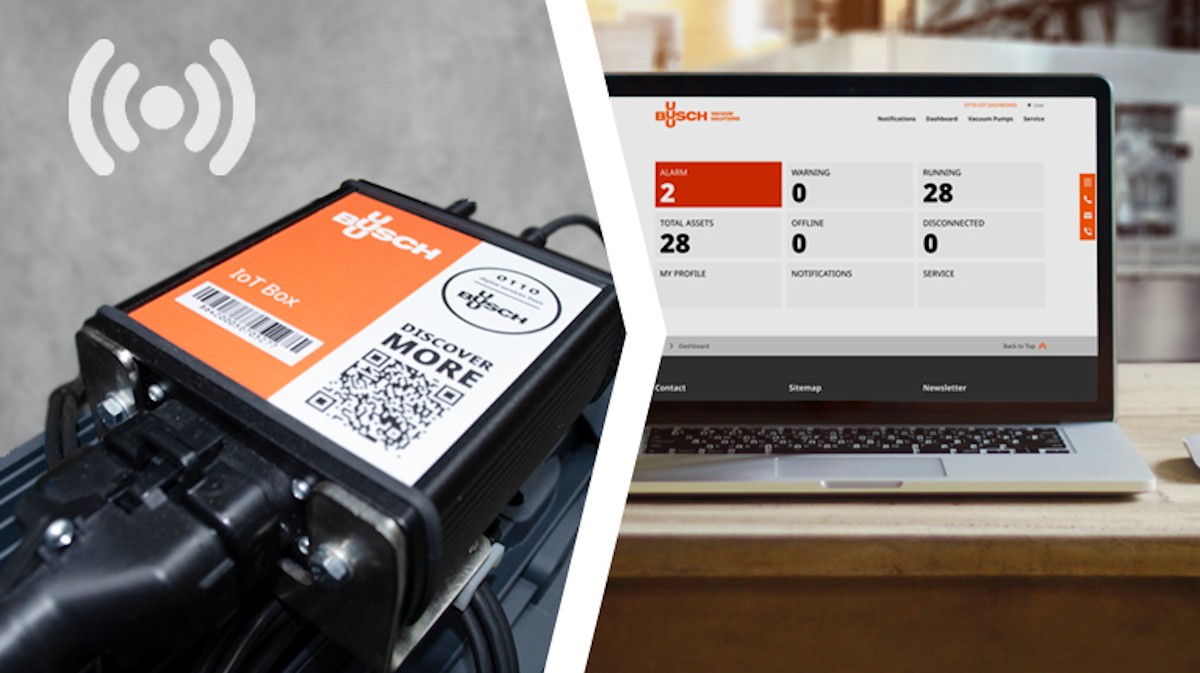
Quelle: Busch Vacuum Solutions.
7 Tipps zur Verringerung von Stillstandszeiten
Stillstandszeiten in der Produktion stellen eines der größten Risiken in der Fertigungsindustrie dar. Vom Ausfall der Anlagen bis hin zu Rohstoffknappheit: Stillstandszeiten können zu erheblichen Einbußen bei Umsatz und Marktanteil führen.
Geplante Stillstandszeiten meinen das planmäßige Abschalten von Produktionsanlagen zur Durchführung von Wartungs-, Inspektions-, Instandsetzungs-, Auf- und Umrüstungsarbeiten. Stillstandszeiten für Wartungsarbeiten müssen unbedingt geplant werden, damit Ihre Anlagen in einem einwandfreien Zustand bleiben und ungeplante Stillstandszeiten vermieden werden. Obwohl geplante Stillstandszeiten Ihren Produktionsprozess unterbrechen, behalten Sie dennoch die Kontrolle über die Produktivitätsprozesse.
Ungeplante Stillstandszeiten treten auf, wenn Ihre Produktionsanlagen oder Ihr Produktionsprozess unerwartet ausfallen. Lebensmittel verderben, wenn sie nicht verpackt werden, es treten kostspielige Verzögerungen in der Produktion auf, und Lieferpläne können nicht eingehalten werden. Darüber hinaus ist es bei instabilen Betriebsabläufen oft anspruchsvoller, Umweltvorschriften und Nachhaltigkeitsmaßnahmen einzuhalten. Dies kann letztlich zu einer Zunahme von Zwischenfällen mit Auswirkungen auf die Umwelt führen.
Daher ist die Vermeidung von Produktionsstillstandszeiten der Schlüssel zur Gewährleistung von Produktivität.
Befolgen Sie daher unsere sieben Tipps zur Reduzierung von Stillstandszeiten in Ihrer Produktionslinie.
1. Entwickeln Sie ein System zur schnellen Identifizierung und Behebung von Produktionsproblemen
-
Quelle: Busch Vacuum Solutions.
2. Nutzen Sie prädiktive Analytik, um potenzielle Probleme noch vor deren Auftreten zu erkennen
-
Quelle: Busch Vacuum Solutions.
3. Implementieren Sie ein Programm für vorbeugende Wartung
Sie sollten regelmäßig wichtige Leistungsdaten Ihrer Anlagen erfassen, um systematisch Wartung durchführen zu können. Mit einer solchen zielgerichteten Wartung können Sie auf vorhersehbare Zwischenfälle oder Ausfälle Ihrer Anlagen reagieren, noch bevor diese auftreten. Durch die Verringerung unerwarteter Stillstandszeiten kann sich Ihr Personal dann profitableren Aufgaben zuwenden.
4. Implementieren Sie ein System für den Umgang mit Störungen und Problemen
-
Quelle: Busch Vacuum Solutions.
5. Automatisieren Sie möglichst viele Prozesse, um menschliche Fehler zu reduzieren
So haben Ihre Mitarbeiter mehr Zeit, sich auf wertstiftendere Aufgaben zu konzentrieren und ihre Fähigkeiten weiterzuentwickeln. Dies führt zu höheren Gewinnen für Ihr Unternehmen und zeigt Ihren Mitarbeitern, dass sie Ihr wertvollstes Gut sind.
-
Quelle: Gorodenkoff - stock.adobe.com.
6. Schulen Sie Ihre Mitarbeiter in der ordnungsgemäßen Bedienung der Anlagen
-
Quelle: Busch Vacuum Solutions.
7. Setzen Sie intelligente IoT-Lösungen ein
Intelligente IoT-Lösungen tragen zur Reduzierung von Stillstandszeiten bei, indem sie ein System zur schnellen Identifizierung und Behebung von Produktionsproblemen bereitstellen (Tipp 1). Ein solches System überwacht Ihre Geräte und Prozesse mit prädiktiven Analysen, sodass Sie einen Wartungsplan erstellen und die erforderlichen Ersatzteile im Voraus bestellen können (Tipp 2). Sensoren und Datenanalysen ermöglichen es IoT-Lösungen, Leistungs- und Prozessoptimierungsdaten Ihrer Anlagen kontinuierlich nachzuverfolgen. Dies gibt Ihnen die Möglichkeit, vorbeugende Wartung durchzuführen (Tipp 3) und potenzielle Probleme vorherzusagen (Tipp 4). Dadurch wird die Häufigkeit geplanter oder ungeplanter Stillstandszeiten effektiv verringert. IoT-Lösungen ermöglichen ferner die Automatisierung von Aufgaben, was die dafür erforderlichen Zeiten verkürzt und schließlich auch zu einer Produktivitätssteigerung bei gleichzeitiger Verringerung menschlicher Fehler führt (Tipp 5). Dank der benutzerfreundlichen Tools kann die Bedienung von IoT-Lösungen einfach erlernt werden. Ihre Mitarbeiter werden innerhalb kürzester Zeit in der Lage sein, das System korrekt zu nutzen (Tipp 6).
Möchten Sie Ihren Prozess durch die Installation eines IoT-Systems optimieren?
Erfahren Sie, wie das Busch IoT Dashboard und die Busch Vacuum App Sie bei der Überwachung Ihres Vakuumprozesses unterstützen können! Busch bietet auch vorbeugende Wartung an: Dabei besucht Sie nach der Analyse der erfassten Daten bei Bedarf automatisch einer unserer Servicespezialisten.
FAQ
Was sind Produktionsstillstandszeiten?
- Stillstandszeiten sind die Zeiten, in denen ein Produktionsprozess angehalten wird. Es werden zwei Arten von Stillstandszeiten unterschieden, geplante und ungeplante.
- Geplante Stillstandszeiten meinen das planmäßige Abschalten von Produktionsanlagen zur Durchführung von Wartungs-, Inspektions-, Instandsetzungs-, Auf- und Umrüstungsarbeiten.
- Ungeplante Stillstandszeiten treten auf, wenn Ihre Produktionsanlagen oder Ihr Produktionsprozess unerwartet ausfallen.
Wie werden Produktionsausfälle berechnet?
Verwenden Sie die folgende Formel zur Berechnung der Kosten von Produktionsstillstandszeiten:
Stillstandszeit in % = (Dauer der Stillstandszeit/geplante Betriebszeit) * 100
Wie lange dauern Produktionsstillstandszeiten durchschnittlich an?
Hersteller verlieren im Durchschnitt 800 Stunden pro Jahr oder mehr als 15 Stunden pro Woche an Produktionszeit durch den Ausfall von Anlagen.
Nehmen wir ein typisches Szenario eines Parmesankäseherstellers:
Ein Parmesanblock wiegt durchschnittlich 42 kg. Der Preis beträgt etwa 9 Euro pro Kilo, was einem Gesamtwert von 378 Euro pro Parmesankäselaib entspricht. Pro Minute können drei Käselaibe produziert werden, was 68.040 Euro pro Stunde entspricht.
Falls in der Parmesankäsefabrik in einer Woche 15 Stunden ungeplante Stillstandszeiten aufgrund des Ausfalls der Produktionsanlagen auftreten, verlöre die Fabrik dadurch 1.020.600 Euro.