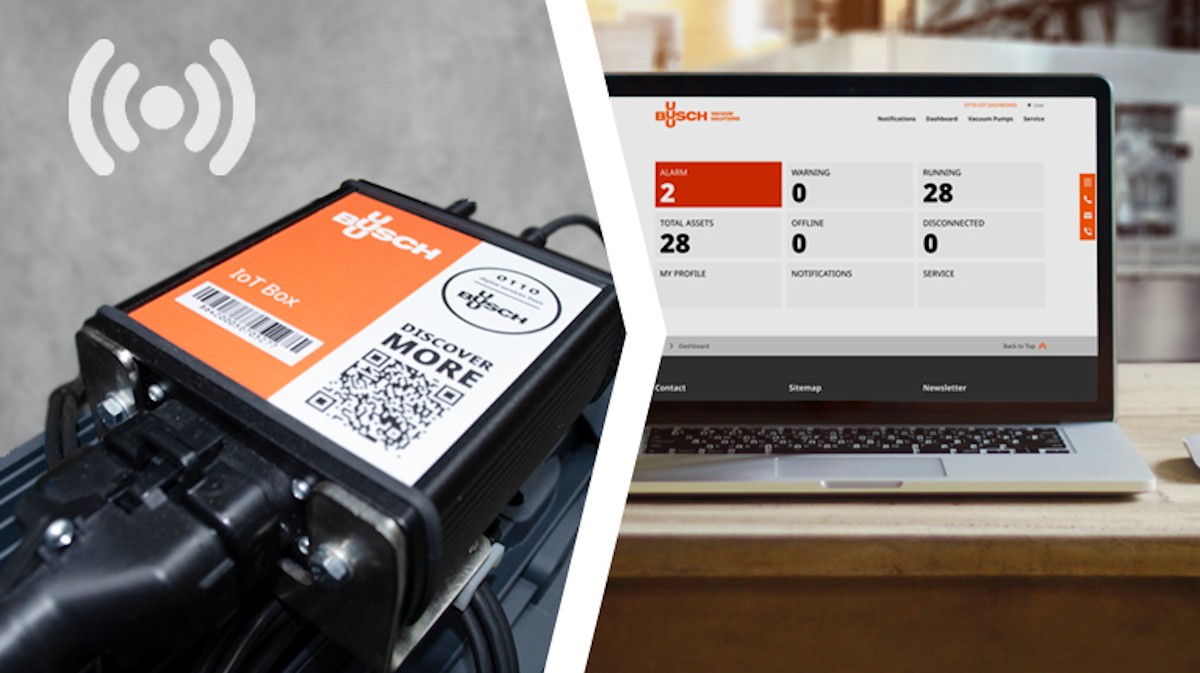
Source : Busch Solutions de Vide.
7 conseils pour réduire les temps d'arrêt de production
Les arrêts de production constituent l'un des plus grands risques dans l'industrie manufacturière. Qu'il s'agisse de pannes d'équipements ou de pénuries de matières premières, tout arrêt de production peut entraîner des pertes importantes de revenus et de parts de marché.
Les temps d'arrêt planifiés sont des arrêts programmés de l'équipement ou du processus de fabrication permettant d'effectuer les opérations de maintenance, les contrôles, les réparations, les mises à niveau ou les réglages de fabrication. Il est essentiel de planifier les temps d'arrêt pour la maintenance afin de maintenir votre équipement dans son état optimal et d'éviter les temps d'arrêt imprévus. Bien que les temps d’arrêt planifiés interrompent votre processus de fabrication, ils vous permettent de garder le contrôle de votre production.
Les temps d’arrêt imprévus concernent les pannes inattendues ainsi que les défaillances de votre équipement ou de votre processus de fabrication. Ils entraînent la détérioration des denrées alimentaires si elles ne sont pas emballées, ainsi que des retards coûteux dans les calendriers de production et de livraison. De plus, lorsque les opérations sont instables, il est plus difficile de respecter les réglementations environnementales et de se conformer aux mesures de durabilité. Ce qui pourrait entraîner une augmentation des incidents environnementaux.
La prévention des arrêts de production est donc essentielle pour garantir la productivité.
Adoptez nos sept conseils pour réduire les temps d'arrêt des équipements sur votre ligne de production.
1. Développez un système d’identification et de résolution rapides des problèmes de production
-
Source : Busch Solutions de Vide.
2. Utilisez l'analyse prédictive pour identifier les problèmes potentiels avant qu'ils ne se produisent
-
Source : Busch Solutions de Vide.
3. Mettez en place un programme de maintenance préventive
Vous pouvez recueillir en continu des informations précieuses sur votre équipement pour adopter une approche systématique de la maintenance. Grâce à une maintenance bien anticipée, vous pouvez réagir aux pannes d'équipements ou aux accidents potentiels avant qu'ils ne se produisent. En réduisant les risques de temps d'arrêt imprévu, vos collaborateurs peuvent se concentrer sur des tâches plus importantes.
-
Source : Piman Khrutmuang – stock.adobe.com.
4. Créez un système pour gérer les problèmes dès qu’ils surviennent
-
Source : Busch Solutions de Vide.
5. Automatisez autant de processus que possible pour réduire les erreurs humaines
Vos collaborateurs pourront ainsi se consacrer à des tâches plus importantes et développer leurs compétences, ce qui permettra d'améliorer les bénéfices de votre entreprise et de démontrer à vos salariés qu'ils sont votre meilleure ressource.
-
Source : Gorodenkoff - stock.adobe.com.
6. Formez les opérateurs au bon fonctionnement de l’équipement
-
Source : Busch Solutions de Vide.
7. Utilisez une solution IoT intelligente
Les solutions IoT intelligentes permettent de réduire les temps d’arrêt en vous fournissant un système qui identifie et résout rapidement les problèmes de production (conseil 1). Il suit et surveille votre équipement et vos processus grâce aux sciences analytiques prédictives, ce qui vous permet de créer un calendrier de maintenance et de commander à l’avance les pièces détachées nécessaires (conseil 2). Les capteurs et l'analyse des données permettent à l’IoT de suivre et de surveiller en permanence les performances et les données d’optimisation des processus de votre équipement. Ainsi, vous pouvez adopter une approche préventive de la maintenance (conseil 3) et prévenir les problèmes potentiels (conseil 4), réduisant alors efficacement la fréquence des temps d’arrêt planifiés ou non. L’IoT permet également d’automatiser les tâches, de réduire le temps nécessaire à leur réalisation et, finalement, d'améliorer la productivité tout en réduisant les erreurs humaines (conseil 5). Avec des outils faciles à utiliser et intuitifs, il est facile d’apprendre à se servir de l’IoT. Vos collaborateurs seront capables de l'utiliser correctement en un rien de temps (conseil 6). Vous souhaitez optimiser vos processus en installant un système IoT ? Découvrez comment le Busch IoT Dashboard et la Busch Vacuum App peuvent vous aider dans la surveillance de votre procédé de vide ! Busch vous propose également un service de maintenance préventive en envoyant automatiquement un technicien spécialisé en fonction des données collectées.
FAQ
Qu’est-ce que le temps d'arrêt de production ?
- Le temps d’arrêt est le temps pendant lequel un processus de fabrication est interrompu. Il existe deux types de temps d'arrêt : les temps planifiés et les imprévus.
- Les temps d’arrêt planifiés concernent les arrêts programmés de l’équipement pour effectuer la maintenance, les contrôles, les réparations ou les mises à niveau.
- Les temps d’arrêt imprévus concernent les pannes inattendues ou les défaillances de votre équipement ou processus de fabrication.
Comment calculer les temps d’arrêt de production ?
Utilisez la formule suivante pour calculer les coûts d’arrêt de la fabrication :
Temps d’arrêt % = (quantité de temps d’arrêt/durée de fonctionnement prévue) * 100
Quel est le temps d’arrêt moyen de production ?
Les fabricants perdent en moyenne 800 heures par an de temps de production, ou plus de 15 heures par semaine, en raison des temps d’arrêt de l’équipement.
Voyons un scénario courant pour une usine de parmesan :
un bloc de parmesan pèse en moyenne 42 kg. Le prix estimatif est de 9 € par kilo, soit un bloc de parmesan d’une valeur totale de 378 €. Trois blocs de fromage peuvent être produits par minute, soit 68 040 € par heure.
Si l’usine de parmesan connaissait 15 heures d’arrêt non planifié dû à une défaillance de l’équipement, elle perdrait 1 020 600 €.