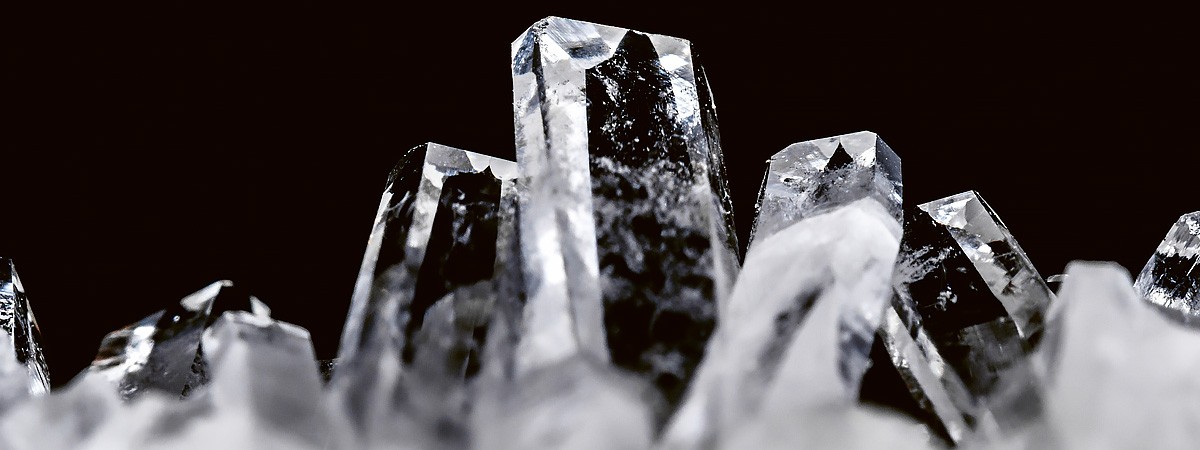
Creazione dei cervelli per la tecnologia odierna
Silicio ultrapuro per microchip
Siamo circondati dal silicio, il secondo elemento più abbondante nella crosta terrestre. Tuttavia, in natura si trova solo in combinazione con altri elementi, come la sabbia, il quarzo e altre rocce. Per un microchip è necessario un cristallo puro, che può essere ottenuto sotto vuoto utilizzando una pompa per vuoto Busch.
I microchip sono elementi fondamentali di cui la società moderna si affida. Sono il cervello dei dispositivi elettronici e sono utilizzati prevalentemente nei settori dell'intrattenimento e dell'automotive. Con il costante progresso che viviamo nell'era della tecnologia intelligente, vediamo apparire i microchip nei luoghi più inaspettati: giocattoli per bambini, lavatrici, persino i passaporti.
Un cristallo non solitario
La storia di ogni microchip inizia con il polisilicio, una forma di silicio costituita da più piccoli cristalli. Per l'industria elettronica, il silicio deve essere di altissima purezza. Ciò significa tipicamente tra il 99,999% e il 99,999999999%: vale a dire non più di un atomo non di silicio per un miliardo di atomi di silicio. Per creare un microchip, il polisilicio deve essere trasformato in un unico cristallo, chiamato silicio monocristallino. Questo è fondamentale per la produzione dei microchip: i bordi dei grani e le irregolarità nella struttura cristallina del polisilicio influirebbero sulla performance del microchip finito. Esistono diversi metodi per produrre silicio monocristallino, il più comune dei quali è il metodo Czochralski, che consiste nella coltivazione di un cristallo di silicio sotto vuoto.
Cristalli da semi
Il silicio monocristallino viene prodotto utilizzando il cosiddetto estrattore. Questo termine comprende una varietà di tecnologie diverse, con due parti chiave: un forno a vuoto e un meccanismo che solleva il cristallo conferendogli la sua forma. All'interno della camera del forno a vuoto, il polisilicio viene riscaldato a temperature estremamente elevate di circa 1410°C. Un piccolo pezzo di silicio monocristallino, chiamato seme, viene posizionato al centro e sollevato lentamente mentre ruota. Il seme solleva insieme a sé il silicio fuso, che si solidifica man mano che viene sollevato. In questo modo si ottiene una lunga barra cilindrica di silicio puro. Il silicio fuso è altamente reattivo, quindi per mantenere la sua elevata purezza, non deve entrare in contatto con l'aria ambiente. L'aria viene quindi evacuata dalla camera utilizzando una pompa per vuoto Busch Il risultato è un ambiente di crescita senza contaminanti e cristalli di altissima qualità, pronti a proseguire il loro lungo viaggio attraverso l'impianto di fabbricazione dei semiconduttori per diventare un microchip.
Un cristallo non solitario
La storia di ogni microchip inizia con il polisilicio, una forma di silicio costituita da più piccoli cristalli. Per l'industria elettronica, il silicio deve essere di altissima purezza. Ciò significa tipicamente tra il 99,999% e il 99,999999999%: vale a dire non più di un atomo non di silicio per un miliardo di atomi di silicio. Per creare un microchip, il polisilicio deve essere trasformato in un unico cristallo, chiamato silicio monocristallino. Questo è fondamentale per la produzione dei microchip: i bordi dei grani e le irregolarità nella struttura cristallina del polisilicio influirebbero sulla performance del microchip finito. Esistono diversi metodi per produrre silicio monocristallino, il più comune dei quali è il metodo Czochralski, che consiste nella coltivazione di un cristallo di silicio sotto vuoto.
Cristalli da semi
Il silicio monocristallino viene prodotto utilizzando il cosiddetto estrattore. Questo termine comprende una varietà di tecnologie diverse, con due parti chiave: un forno a vuoto e un meccanismo che solleva il cristallo conferendogli la sua forma. All'interno della camera del forno a vuoto, il polisilicio viene riscaldato a temperature estremamente elevate di circa 1410°C. Un piccolo pezzo di silicio monocristallino, chiamato seme, viene posizionato al centro e sollevato lentamente mentre ruota. Il seme solleva insieme a sé il silicio fuso, che si solidifica man mano che viene sollevato. In questo modo si ottiene una lunga barra cilindrica di silicio puro. Il silicio fuso è altamente reattivo, quindi per mantenere la sua elevata purezza, non deve entrare in contatto con l'aria ambiente. L'aria viene quindi evacuata dalla camera utilizzando una pompa per vuoto Busch Il risultato è un ambiente di crescita senza contaminanti e cristalli di altissima qualità, pronti a proseguire il loro lungo viaggio attraverso l'impianto di fabbricazione dei semiconduttori per diventare un microchip.
I luoghi più puliti della Terra
Nel mondo naturale non esiste aria veramente pulita. Ce ne rendiamo conto nelle giornate di sole, quando notiamo improvvisamente quel pulviscolo che rotea intorno a noi sotto un raggio di sole. Infatti, in ogni metro cubo d'aria sono contenute mediamente fino a 3.500.000.000 minuscole particelle, alcune invisibili a occhio nudo. Tuttavia, in alcuni processi di produzione, come l'industria aerospaziale, quella dei semiconduttori e quella farmaceutica, questo elemento vitale, altrimenti normale, può causare la contaminazione dei prodotti. Le camere bianche sono quindi essenziali. In quelle che impongono le condizioni più severe, in un metro cubo sono consentite soltanto 10 particelle minuscole di dimensioni ≥ 0,1, ovvero l'equivalente approssimativo di un singolo seme di sesamo in una piscina olimpionica.
Le industrie utilizzano una varietà di metodi per mantenere le camere bianche prive di contaminanti. Può trattarsi di tute protettive e maschere, oppure di docce d'aria, dove i lavoratori vengono sottoposti a getti d'aria per rimuovere le particelle persistenti. In una fabbrica di semiconduttori, persino profumi, trucco e prodotti per capelli non sono accettabili, poiché anche la più piccola particella può rovinare un lotto di wafer.
Quindi, se avete davvero bisogno di aria fresca, dimenticatevi le passeggiate in campagna. L'aria più pulita del nostro pianeta si trova all'interno di una camera bianca.
Nel mondo naturale non esiste aria veramente pulita. Ce ne rendiamo conto nelle giornate di sole, quando notiamo improvvisamente quel pulviscolo che rotea intorno a noi sotto un raggio di sole. Infatti, in ogni metro cubo d'aria sono contenute mediamente fino a 3.500.000.000 minuscole particelle, alcune invisibili a occhio nudo. Tuttavia, in alcuni processi di produzione, come l'industria aerospaziale, quella dei semiconduttori e quella farmaceutica, questo elemento vitale, altrimenti normale, può causare la contaminazione dei prodotti. Le camere bianche sono quindi essenziali. In quelle che impongono le condizioni più severe, in un metro cubo sono consentite soltanto 10 particelle minuscole di dimensioni ≥ 0,1, ovvero l'equivalente approssimativo di un singolo seme di sesamo in una piscina olimpionica.
Le industrie utilizzano una varietà di metodi per mantenere le camere bianche prive di contaminanti. Può trattarsi di tute protettive e maschere, oppure di docce d'aria, dove i lavoratori vengono sottoposti a getti d'aria per rimuovere le particelle persistenti. In una fabbrica di semiconduttori, persino profumi, trucco e prodotti per capelli non sono accettabili, poiché anche la più piccola particella può rovinare un lotto di wafer.
Quindi, se avete davvero bisogno di aria fresca, dimenticatevi le passeggiate in campagna. L'aria più pulita del nostro pianeta si trova all'interno di una camera bianca.