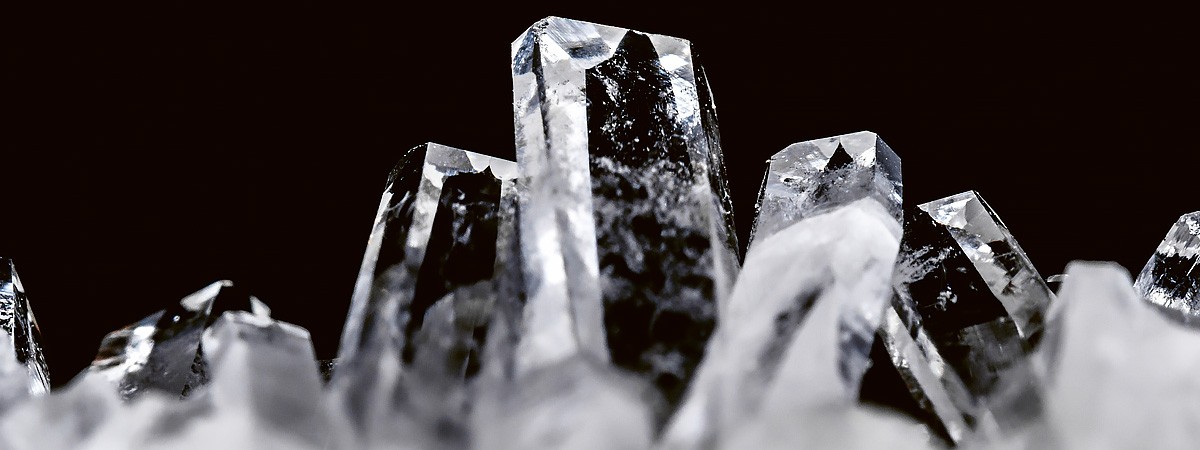
Créer les cerveaux de la technologie d’aujourd’hui
Silicium ultrapur pour les micro-puces
Deuxième élément le plus abondant de la croûte terrestre, le silicium est tout autour de nous. Mais dans la nature, il ne peut être trouvé qu’associé à d’autres éléments, comme le sable, le quartz et d’autres roches. Mais pour fabriquer une micro-puce, un cristal pur est requis. Ce dernier peut être obtenu sous vide en utilisant une pompe à vide Busch.
La société moderne dépend fortement des micro-puces. Elles sont les cerveaux de nos appareils électroniques, et sont le plus souvent utilisées dans les secteurs du divertissement et de l’automobile. Mais à mesure que nous progressons dans l’ère des technologies intelligentes, les micro-puces sont utilisées dans les objets les plus inattendus : les jouets pour enfants, les machines à laver et même dans votre passeport.
Un cristal fait de nombreux cristaux
L’histoire de chaque micro-puce commence par le polysilicium, une forme de silicium composé de nombreux petits cristaux. Pour l’industrie électronique, le silicium doit être d’une très grande pureté. De manière générale, elle doit être située entre 99,999 % et 99,999999999 %, soit pas plus d’un atome non-silicium par milliard d’atomes de silicium. Pour créer une micro-puce, le polysilicium doit être transformé en un seul cristal, appelé silicium monocristallin. Ce point est essentiel pour la fabrication de micro-puces, sinon les joints de grains et les irrégularités de la structure cristalline du polysilicium affecteraient les performances de la micro-puce finie. Il existe plusieurs méthodes de production du silicium monocristallin, la plus courante étant la méthode Czochralski, qui consiste à cultiver un cristal de silicium sous vide.
Cristaux issus de germes
Le silicium monocristallin est produit à l’aide d’une tête de tirage. Ce nom englobe une variété de technologies différentes, comportant deux éléments clés : un four sous vide et un mécanisme qui tire le cristal pour le former. À l’intérieur de la chambre du four sous vide, le polysilicium est chauffé à des températures extrêmement élevées d’environ 1 410 °C. Un petit morceau de silicium monocristallin, appelé germe, est placé au centre et est tiré lentement vers le haut, tout en tournant. Le germe tire avec lui le silicium fondu, qui se solidifie à mesure qu’il monte. On obtient ainsi une longue tige cylindrique de silicium pur. Le silicium fondu est particulièrement réactif. Pour conserver une pureté élevée, il ne doit donc pas entrer en contact avec l’air ambiant. Par conséquent, l’air est évacué de la chambre à l’aide d’une pompe à vide Busch. Il est ainsi possible d’obtenir un environnement de culture exempt de contaminants et des cristaux de la plus haute qualité, prêts à poursuivre leur long parcours à travers l'usine de semi-conducteurs, pour finalement devenir une micro-puce.
Un cristal fait de nombreux cristaux
L’histoire de chaque micro-puce commence par le polysilicium, une forme de silicium composé de nombreux petits cristaux. Pour l’industrie électronique, le silicium doit être d’une très grande pureté. De manière générale, elle doit être située entre 99,999 % et 99,999999999 %, soit pas plus d’un atome non-silicium par milliard d’atomes de silicium. Pour créer une micro-puce, le polysilicium doit être transformé en un seul cristal, appelé silicium monocristallin. Ce point est essentiel pour la fabrication de micro-puces, sinon les joints de grains et les irrégularités de la structure cristalline du polysilicium affecteraient les performances de la micro-puce finie. Il existe plusieurs méthodes de production du silicium monocristallin, la plus courante étant la méthode Czochralski, qui consiste à cultiver un cristal de silicium sous vide.
Cristaux issus de germes
Le silicium monocristallin est produit à l’aide d’une tête de tirage. Ce nom englobe une variété de technologies différentes, comportant deux éléments clés : un four sous vide et un mécanisme qui tire le cristal pour le former. À l’intérieur de la chambre du four sous vide, le polysilicium est chauffé à des températures extrêmement élevées d’environ 1 410 °C. Un petit morceau de silicium monocristallin, appelé germe, est placé au centre et est tiré lentement vers le haut, tout en tournant. Le germe tire avec lui le silicium fondu, qui se solidifie à mesure qu’il monte. On obtient ainsi une longue tige cylindrique de silicium pur. Le silicium fondu est particulièrement réactif. Pour conserver une pureté élevée, il ne doit donc pas entrer en contact avec l’air ambiant. Par conséquent, l’air est évacué de la chambre à l’aide d’une pompe à vide Busch. Il est ainsi possible d’obtenir un environnement de culture exempt de contaminants et des cristaux de la plus haute qualité, prêts à poursuivre leur long parcours à travers l'usine de semi-conducteurs, pour finalement devenir une micro-puce.
Les endroits les plus propres de la planète
Dans la nature, un air véritablement pur n’existe pas. Nous le remarquons les jours ensoleillés, lorsque nous voyons soudain la poussière danser autour de nous, dans un rayon de soleil. En fait, un bureau moyen contient jusqu’à 3 500 000 000 particules minuscules dans chaque mètre cube d’air, certaines invisibles à l’œil nu. Mais dans certains processus de fabrication, tels que ceux de l’aérospatiale, des semi-conducteurs et des industries pharmaceutiques, cet état de fait pourtant normal, peut entraîner la contamination des produits. C'est pourquoi les salles blanches sont essentielles. Les plus strictes ne permettent que 10 particules minuscules de ≥ 0,1 μm par mètre cube, soit l’équivalent approximatif d’une seule graine de sésame dans une piscine olympique.
Les installations utilisent diverses méthodes pour maintenir leurs salles blanches exemptes de contaminants. Cela va des combinaisons et masques de protection aux douches à air, où de l’air est projeté sur le personnel pour éliminer les particules persistantes. Dans une usine de semi-conducteurs, même les parfums, le maquillage et les produits capillaires sont interdits, car la plus infime des particules peut ruiner un lot de plaquettes.
Donc, si vous avez vraiment besoin d’air pur, oubliez la promenade à la campagne. L’air le plus pur sur notre planète est celui qui se trouve à l’intérieur d’une salle blanche.
Dans la nature, un air véritablement pur n’existe pas. Nous le remarquons les jours ensoleillés, lorsque nous voyons soudain la poussière danser autour de nous, dans un rayon de soleil. En fait, un bureau moyen contient jusqu’à 3 500 000 000 particules minuscules dans chaque mètre cube d’air, certaines invisibles à l’œil nu. Mais dans certains processus de fabrication, tels que ceux de l’aérospatiale, des semi-conducteurs et des industries pharmaceutiques, cet état de fait pourtant normal, peut entraîner la contamination des produits. C'est pourquoi les salles blanches sont essentielles. Les plus strictes ne permettent que 10 particules minuscules de ≥ 0,1 μm par mètre cube, soit l’équivalent approximatif d’une seule graine de sésame dans une piscine olympique.
Les installations utilisent diverses méthodes pour maintenir leurs salles blanches exemptes de contaminants. Cela va des combinaisons et masques de protection aux douches à air, où de l’air est projeté sur le personnel pour éliminer les particules persistantes. Dans une usine de semi-conducteurs, même les parfums, le maquillage et les produits capillaires sont interdits, car la plus infime des particules peut ruiner un lot de plaquettes.
Donc, si vous avez vraiment besoin d’air pur, oubliez la promenade à la campagne. L’air le plus pur sur notre planète est celui qui se trouve à l’intérieur d’une salle blanche.