When it comes to windshields, care and precision is key. Such fragile products need to be held gently but securely as they move down the production line. Busch provides vacuum systems designed to ensure that the right hold is maintained wherever it is needed.
On their journey from raw glass to a ready-to-install window, windshields for cars, vans, and trucks are put through their paces. They are moved from station to station, maneuvered into position, and held in place at every stop on the way. Wherever it is in the process, the windshield needs to be held securely – with no damage to either windscreen or worker. And a windshield is no lightweight at typically 10 to 15 kg. An assembly line needs a solution that does not transfer this weight and strain to its personnel. A vacuum set-up is the ideal solution. Suction cups powered by vacuum give a secure but gentle grip, making this system perfect to guide the glass safely through the production line and onto the finished vehicle.
Keeping the rain out
One such station, and a good example of where a windshield needs to be held in place, is weatherproofing. No driver wants to see – or feel – water trickling into the vehicle, and this process makes sure this will not happen. A rubber sealant is installed around the edges of the windshield and a gutter profile at its base: Two small but important additions that help keep the car’s occupants and sensitive electrical equipment dry in a rainstorm – or in the car wash. Accuracy here is vital; sealant applied sloppily now will mean a leaky car later. Vacuum provides this precise hold, ensuring that the windshield does not move during application and that each part is applied exactly where and how it should be.
A firm hold and a quick change
Each car model needs its own specific shape and size of suction cup, and so these must be changed correspondingly when a new design rolls into production. In other assembly line setups, this can be a time-consuming process and mean that the whole process comes to a standstill for long periods, but the quick-release mechanism between the vacuum system and the holding device ensures quick and easy changeovers. A central vacuum solution from Busch can deliver the vacuum needed to maintain this firm grip on the production line.
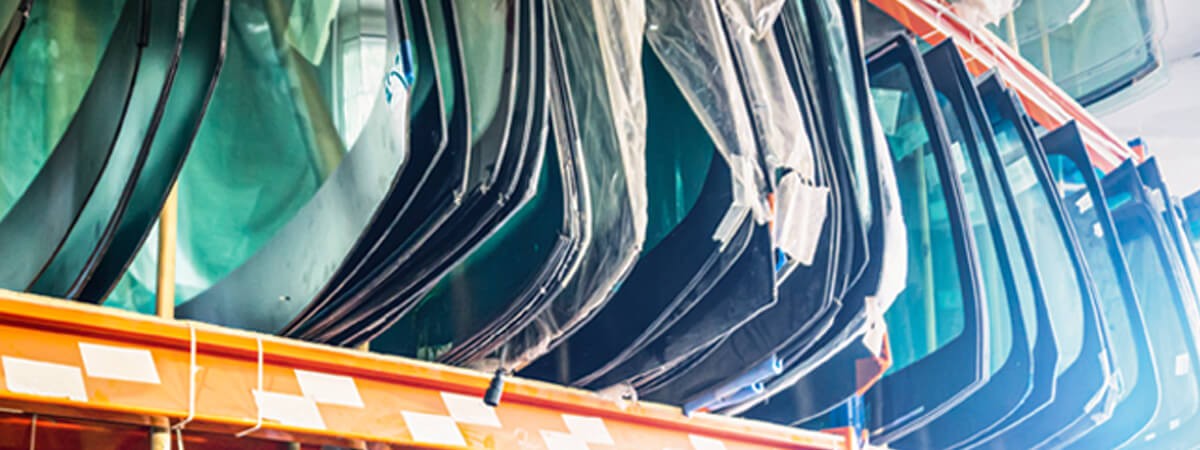
Safe Handling on the Assembly Line
Windshield production using vacuum
Glass that protects the driver
Break a typical house window and it will splinter, creating sharp, jagged edges. But break the glass in any car window and you will see something different: The glass will break in such a way as to not cause injury to anyone inside the car. There are two types of specially treated glass used in the car manufacturing process: Tempered glass and laminated glass. Tempered glass is used for the side windows and is created by heating a panel of “normal” glass to very high temperatures. It is then cooled rapidly, creating glass many times stronger than traditional glass of a similar thickness. This means that it is already harder to break – but if it does, it has an additional safety measure. Rather than creating dangerous shards, it crumbles into pebble-like pieces with no sharp edges. The windshield, however, helps the car maintain its structural integrity, making tempered glass unsuitable. Instead, laminated glass is used. This glass panel contains multiple layers bonded together under heat and pressure: Two made of glass with one made of plastic polyvinyl butyral resin sandwiched between. This resin provides an extra layer of protection and means the glass can bend and take significant impact before breaking, even acting as a cushion if the car’s occupant is flung against it in a crash.
Break a typical house window and it will splinter, creating sharp, jagged edges. But break the glass in any car window and you will see something different: The glass will break in such a way as to not cause injury to anyone inside the car. There are two types of specially treated glass used in the car manufacturing process: Tempered glass and laminated glass. Tempered glass is used for the side windows and is created by heating a panel of “normal” glass to very high temperatures. It is then cooled rapidly, creating glass many times stronger than traditional glass of a similar thickness. This means that it is already harder to break – but if it does, it has an additional safety measure. Rather than creating dangerous shards, it crumbles into pebble-like pieces with no sharp edges. The windshield, however, helps the car maintain its structural integrity, making tempered glass unsuitable. Instead, laminated glass is used. This glass panel contains multiple layers bonded together under heat and pressure: Two made of glass with one made of plastic polyvinyl butyral resin sandwiched between. This resin provides an extra layer of protection and means the glass can bend and take significant impact before breaking, even acting as a cushion if the car’s occupant is flung against it in a crash.