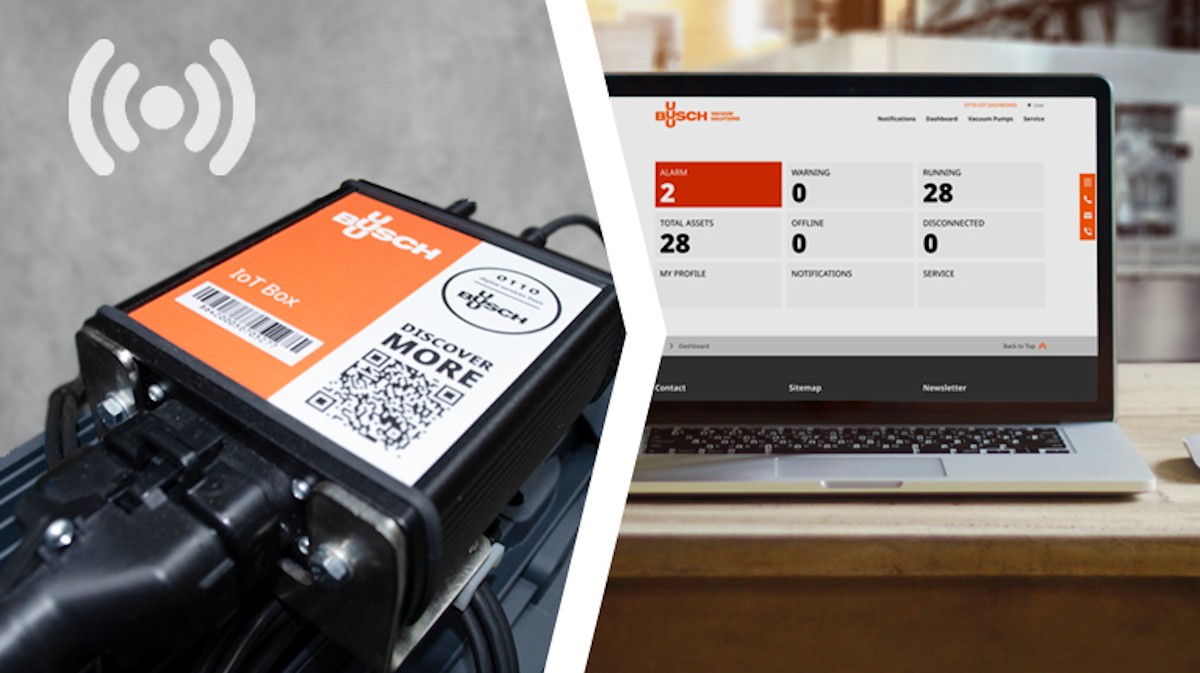
Fonte: Busch Vacuum Solutions.
7 formas de reduzir os tempos de inatividade da produção
Os tempos de inatividade da produção são um dos maiores riscos na indústria da transformação. Desde falhas no equipamento a faltas de matérias-primas, qualquer tempo de inatividade na produção pode resultar em grandes perdas nas receitas e na quota de mercado.
O tempo de inatividade planeado é uma paragem programada do equipamento ou dos processos com a finalidade de realizar tarefas de manutenção, inspeção, reparações, upgrades ou configurações de produção. É fundamental planear o tempo de inatividade para fins de manutenção, de forma a manter o seu equipamento em boas condições e evitar tempo de inatividade não planeado. Apesar de o tempo de inatividade planeado interromper o seu processo de produção, continua a ter o controlo dos processos de produtividade.
O tempo de inatividade não planeado ocorre quando se verifica uma paragem ou falha inesperadas do seu equipamento ou processo de produção. O resultado pode ser bens alimentares estragados se não forem embalados, bem como dispendiosos atrasos na produção e nos prazos de entrega. Além disso, quando as operações são instáveis, é mais difícil respeitar os regulamentos ambientais e cumprir medidas de sustentabilidade. O resultado pode ser um aumento dos incidentes ambientais.
Por isso, prevenir tempo de inatividade da produção é fundamental para garantir a produtividade.
Siga as nossas sete dicas para reduzir o tempo de inatividade das máquinas na sua linha de produção.
1. Desenvolver um sistema para a rápida identificação e resolução de problemas na produção
-
Fonte: Busch Vacuum Solutions.
2. Usar a análise preditiva para identificar potenciais problemas antes de estes ocorrerem
-
Fonte: Busch Vacuum Solutions.
3. Implementar um programa de manutenção preventiva
Pode, de forma rotineira, recolher valiosas informações sobre o seu equipamento para uma abordagem sistemática à manutenção. Com a manutenção direcionada adequada pode reagir às falhas de equipamento ou acidentes previstos antes mesmo de ocorrerem. Reduzindo a possibilidade de tempos de inatividade inesperados, o seu pessoal pode dedicar-se a tarefas mais rentáveis.
-
Fonte: Piman Khrutmuang - stock.adobe.com.
4. Criar um sistema para lidar com erros e problemas à medida que estes ocorrem
-
Fonte: Busch Vacuum Solutions.
5. Automatizar o maior número possível de processos para reduzir o erro humano
Assim, o seu pessoal terá mais tempo disponível para se dedicar a tarefas rentáveis e para desenvolver as suas competências, o que irá traduzir-se em maiores lucros para a sua empresa e mostrar aos seus colaboradores que eles são o seu recurso mais valioso.
-
Fonte: Gorodenkoff - stock.adobe.com.
6. Formar os operadores sobre como operar corretamente o equipamento
-
Fonte: Busch Vacuum Solutions.
7. Usar soluções IoT inteligentes
As soluções IoT inteligentes ajudam a reduzir o tempo de inatividade, oferecendo-lhe um sistema que rapidamente identifica e resolve problemas na produção (dica 1). Estas soluções acompanham e monitorizam o seu equipamento e o processo através da análise preditiva, permitindo-lhe criar um plano de manutenções e encomendar as peças sobressalentes necessárias com antecedência (dica 2). Os sistemas de sensores e a análise de dados permitem que a IoT acompanhe e monitorize continuamente o desempenho e os dados de otimização de processos do seu equipamento. Isto dá-lhe a oportunidade de implementar a manutenção preventiva (dica 3) e prever potenciais problemas à medida que estes ocorrem (dica 4), reduzindo eficazmente a frequência de tempos de inatividade planeados ou não planeados. A IoT também permite automatizar as tarefas, reduzindo o tempo que demora a concluí-las e, em última análise, aumentar a produtividade e reduzir o erro humano (dica 5). Graças às suas ferramentas intuitivas, é fácil aprender a usar a IoT. A sua força de trabalho conseguirá usá-la corretamente num instante (dica 6). Gostaria de otimizar o seu processo através da instalação de um sistema IoT? Saiba como o painel IoT da Busch e a Busch Vacuum App o podem ajudar na monitorização do seu processo a vácuo! A Busch também lhe oferece manutenção preventiva através do envio automático de um especialista de serviço quando necessário, com base na análise dos dados recolhidos.
FAQ
O que é o tempo de inatividade da produção?
- O tempo de inatividade é o tempo durante o qual um processo de produção está parado. Há dois tipos de tempo de inatividade: os planeados e os não planeados.
- O tempo de inatividade planeado é uma paragem programada do equipamento de produção com a finalidade de realizar tarefas de manutenção, inspeção, reparações e upgrades.
- O tempo de inatividade não planeado é uma paragem ou falha inesperada do seu equipamento ou processo de produção.
Como calcular o tempo de inatividade da produção?
Utilize a seguinte equação para calcular os custos de tempo de inatividade da produção:
% de tempo de inatividade = (quantidade de tempos de inatividade/tempo de funcionamento planeado) * 100
Qual é a média de tempo de inatividade produção?
Os fabricantes perdem, em média, 800 horas por ano, ou mais de 15 horas por semana, de tempo de produção devido a tempo de inatividade do equipamento.
Consideramos um cenário comum para uma fábrica de queijo parmesão:
um bloco de queijo parmesão pesa, em média, 42 kg. O preço estimado é de 9 euros por quilo, o que significa que um bloco de queijo parmesão tem um valor total de 378 euros. Por minuto é possível produzir três blocos de queijo, o que resulta em 68 040 euros por hora.
Se, numa semana, a fábrica de parmesão sofresse 15 horas de tempo de inatividade não planeado devido a uma falha no equipamento, poderia perder 1 020 600 euros.