Przystawki i wyroby delikatesowe są specjalnością firmy Feinkost Dittmann od ponad stu lat. W zakładzie produkcyjnym w Taunusstein w Niemczech produkowane są rozmaite przetwory w opakowaniach szklanych oraz wyroby świeże w plastikowych tackach. Wytwarzanie próżni do maszyn pakujących realizowane jest przez centralny system próżniowy firmy Busch od ponad roku. Rozwiązanie to jest dużo bardziej ekonomiczne niż technologia próżniowa używana wcześniej. Zużycie energii obniżono o ponad 70%.
Produkty w tak zwanym „dziale świeżym” są pakowane do plastikowych tacek w zakładzie produkcyjnym w Taunusstein. Podczas tego procesu powietrze jest zasysane z tacek opakowaniowych przed wprowadzeniem do opakowania mieszaniny gazów ochronnych złożonej z CO 2 N 2 . Następnie opakowanie zabezpiecza się folią z tworzywa sztucznego, aby stało się gazoszczelne, a na koniec dodatkowo zamyka się plastikową pokrywką. Dzięki odprowadzeniu powietrza i użyciu gazów ochronnych ten rodzaj opakowania gwarantuje, że zawartość tlenu jest niższa niż 1%. W rezultacie przydatność produktów do spożycia znacząco się wydłuża. Ponadto prezentacja produktu w tym przezroczystym opakowaniu jest doskonała, ponieważ folia nie leży bezpośrednio na produkcie, nie rozgniata z powodu podciśnienia w opakowaniu.
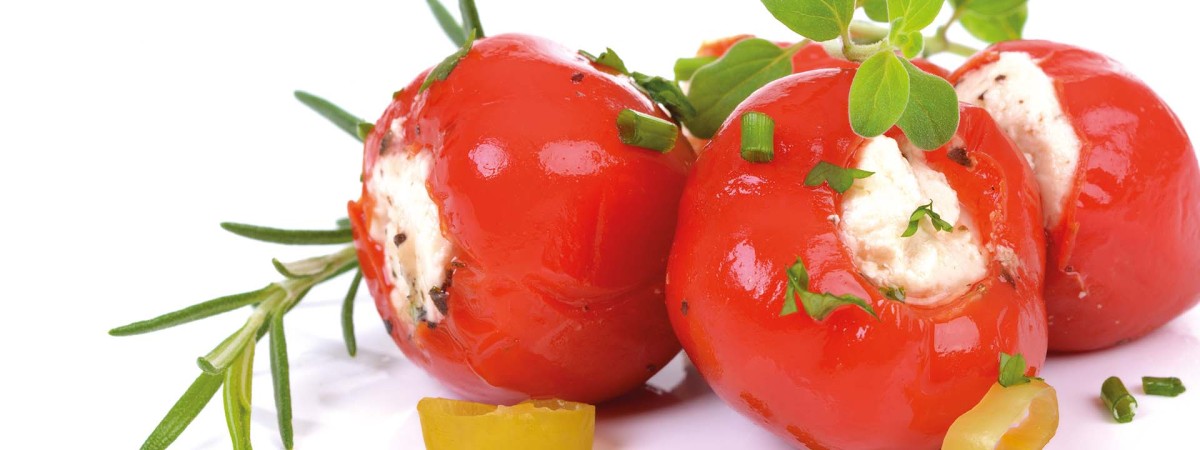
Zdjęcie: © www.istockphoto.com - kabVisio.
Wytwarzanie próżni dla pakowania żywności – zużycie energii mniejsze o 70%
-
Źródło: Busch Vacuum Solutions
W sumie do pakowania używane są cztery maszyny pakujące (pakowarki do tacek) pracujące na dwie zmiany. Próżnię niezbędną do tego procesu wytwarzają rotacyjne łopatkowe pompy próżniowe, z których każda wyposażona jest w silnik o mocy 5,5 kilowata. Pierwotnie były one zainstalowane bezpośrednio na maszynach pakujących. Ze względów higienicznych i w celu obniżenia obciążenia cieplnego w pomieszczeniach produkcyjnych pompy te zostały później zainstalowane w osobnym pomieszczeniu nad jednym z pomieszczeń produkcyjnych i połączone siecią rur z maszynami pakującymi. Andreas Lutz, kierownik projektów technicznych w zakładzie produkcyjnym, nie był z tego rozwiązania zadowolony, ponieważ pompy próżniowe nadal wymagały sporo konserwacji. Ponadto wahania i usterki w sieci próżniowej zauważano dopiero wtedy, gdy jedna z maszyn pakujących zgłaszała błąd i wyłączała się automatycznie, kiedy zadany poziom próżni był osiągany zbyt wolno lub nie był osiągany w ogóle. Wskutek tego wielokrotnie dochodziło do przestojów w produkcji na poszczególnych liniach pakujących.
W 2013 roku Andreas Lutz skontaktował się ze specjalistami od instalacji próżniowych z firmy Busch. Jako zadanie mieli zaoferować bardziej niezawodne i efektywne rozwiązanie. Jednocześnie należało uwzględnić dalsze wykorzystanie istniejącej sieci rurociągów. Dodatkowo instalacja wytwarzania próżni miała zostać tak zaprojektowana, aby możliwe było podłączenie kolejnych maszyn pakujących, gdyby wzrosła skala produkcji. Firma Busch szczegółowo przeanalizowała warunki na miejscu oraz wszystkie parametry techniczne, ściśle współpracując z kierownikiem projektów z firmy Feinkost Dittmann i własnym laboratorium. Efektem tej analizy i wszechstronnych konsultacji był centralny system próżniowy z czterema kłowymi pompami próżniowymi MINK.
-
Centralny system próżniowy z kłowymi pompami próżniowymi MINK firmy Busch
Ich podstawową zaletą jest to, że nie wymagają stosowania płynu eksploatacyjnego takiego jak olej w komorze sprężenia. Dzięki temu zbędne stają się wszelkie prace konserwacyjne związane z olejem, na przykład jego kontrole, wymiany i wymiany filtra oleju, i nie trzeba ponosić kosztów zakupu oraz pozbywania się oleju i filtrów. Kłowe pompy próżniowe Mink również działają na zasadzie bezstykowej. Oznacza to, że w komorze sprężania nie mają części, które wchodziłyby ze sobą w kontakt mechaniczny, a tym samym ulegały zużyciu. W rezultacie nie trzeba wymieniać części zużywalnych i ponosić związanych z tym nakładów czasowych i finansowych. Bezstykowa praca charakterystyczna dla kłowej pompy próżniowej pozwala na osiągnięcie wysokiego stopnia sprawności dzięki temu, że wymaga ona silnika mniejszej mocy niż konwencjonalne pompy próżniowe.
Taki centralny system próżniowy zainstalowano pod koniec 2013 roku. Przed kłowymi pompami próżniowymi MINK znajdują się trzy zbiorniki próżniowe o objętości 3000 litrów każdy. Taki układ zapewnia, że w razie potrzeby dostateczny poziom próżni jest natychmiast dostępny dla maszyn.
Wcześniej wszystkie sześć rotacyjnych łopatkowych pomp próżniowych pracowały średnio po 15 godzin na dobę. Pompy próżniowe MINK w nowym, centralnym systemie są sterowane tak, aby w danym czasie pracowały tylko te, które są potrzebne do osiągnięcia faktycznie wymaganej próżni.
Dwie z tych pomp próżniowych z silnikami standardowymi są odpowiedzialne za tak zwane obciążenie podstawowe. Pozostałe dwie pompy próżniowe mają siniki sterowane częstotliwościowo i zapewniają precyzyjne dostosowanie próżni do zapotrzebowania poprzez regulację ich prędkości obrotowej. To inteligentne rozwiązanie sprawia, że centralny system próżniowy precyzyjnie i samoczynnie dostosowuje swoją szybkość pompowania do bieżących wymagań.
Takie sterowanie znacząco skraca rzeczywisty czas pracy poszczególnych pomp próżniowych, ponieważ podczas normalnej pracy żadna z czterech pomp próżniowych nigdy nie musi działać pod pełnym obciążeniem. W rezultacie centralny system próżniowy firmy Feinkost Dittmann dysponuje dostatecznymi rezerwami mocy, aby w przyszłości można było podłączyć kolejne maszyny pakujące. W planach jest jeszcze podłączenie napełniarki próżniowej do przetworów w opakowaniach szklanych, co pozwoliłoby wyeliminować bieżącą zdecentralizowaną instalację pomp próżniowych z pierścieniem cieczowym i napędem o mocy 7,5 kilowata, a tym samym uzyskać dalsze oszczędności energii.
Po ponad dwóch latach eksploatacji kierownik projektów Andreas Lutz, podsumowując sytuację, jest niezwykle zadowolony:
Konserwacją nowego centralnego systemu próżniowego zajmują się serwisanci firmy Busch. Niemniej jednak ogranicza się ona do wykonywanych raz w roku pomiarów maksymalnego ciśnienia i poboru prądu poszczególnych pomp próżniowych oraz do wymiany zainstalowanych przed pompą filtrów cząstek stałych i wymiany oleju w skrzyni przekładniowej.
Taki centralny system próżniowy zainstalowano pod koniec 2013 roku. Przed kłowymi pompami próżniowymi MINK znajdują się trzy zbiorniki próżniowe o objętości 3000 litrów każdy. Taki układ zapewnia, że w razie potrzeby dostateczny poziom próżni jest natychmiast dostępny dla maszyn.
Wcześniej wszystkie sześć rotacyjnych łopatkowych pomp próżniowych pracowały średnio po 15 godzin na dobę. Pompy próżniowe MINK w nowym, centralnym systemie są sterowane tak, aby w danym czasie pracowały tylko te, które są potrzebne do osiągnięcia faktycznie wymaganej próżni.
Dwie z tych pomp próżniowych z silnikami standardowymi są odpowiedzialne za tak zwane obciążenie podstawowe. Pozostałe dwie pompy próżniowe mają siniki sterowane częstotliwościowo i zapewniają precyzyjne dostosowanie próżni do zapotrzebowania poprzez regulację ich prędkości obrotowej. To inteligentne rozwiązanie sprawia, że centralny system próżniowy precyzyjnie i samoczynnie dostosowuje swoją szybkość pompowania do bieżących wymagań.
Takie sterowanie znacząco skraca rzeczywisty czas pracy poszczególnych pomp próżniowych, ponieważ podczas normalnej pracy żadna z czterech pomp próżniowych nigdy nie musi działać pod pełnym obciążeniem. W rezultacie centralny system próżniowy firmy Feinkost Dittmann dysponuje dostatecznymi rezerwami mocy, aby w przyszłości można było podłączyć kolejne maszyny pakujące. W planach jest jeszcze podłączenie napełniarki próżniowej do przetworów w opakowaniach szklanych, co pozwoliłoby wyeliminować bieżącą zdecentralizowaną instalację pomp próżniowych z pierścieniem cieczowym i napędem o mocy 7,5 kilowata, a tym samym uzyskać dalsze oszczędności energii.
Po ponad dwóch latach eksploatacji kierownik projektów Andreas Lutz, podsumowując sytuację, jest niezwykle zadowolony:
- obniżenie zapotrzebowania na energię o ponad 70%
- zdecydowane obniżenie nakładów na konserwację,
- większa niezawodność,
- brak usterek i awarii.
Konserwacją nowego centralnego systemu próżniowego zajmują się serwisanci firmy Busch. Niemniej jednak ogranicza się ona do wykonywanych raz w roku pomiarów maksymalnego ciśnienia i poboru prądu poszczególnych pomp próżniowych oraz do wymiany zainstalowanych przed pompą filtrów cząstek stałych i wymiany oleju w skrzyni przekładniowej.