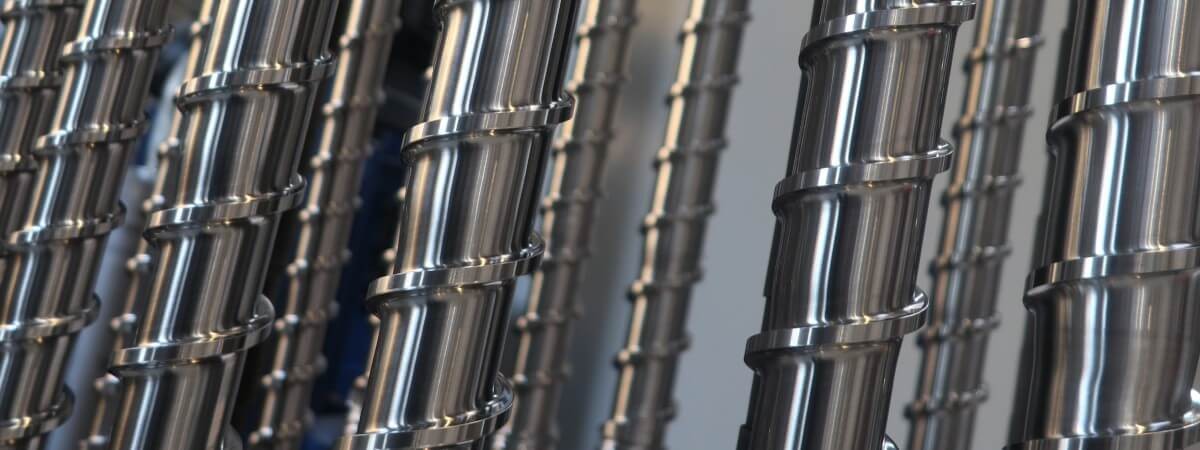
Il. 1: Azotowana plazmowo śruba wytłaczarki przygotowan do procesu powlekania łukowego PVD. Źródło: Busch Vacuum Solutions
Śrubowa pompa próżniowa do powlekania łukowego PVD
Głównym obszarem działalności firmy Dreistegen GmbH jest wykańczanie powierzchni dużych metalowych narzędzi i elementów. Stosuje ona różne metody obróbki warstwy dyfuzyjnej takie jak azotowanie, nawęglanie azotowe lub utlenianie, a także techniki powlekania, takie jak fizyczne osadzanie z fazy gazowej (PVD) i chemiczne osadzanie z fazy gazowej (CVD) przy użyciu zimnej plazmy.
W zakresie nakładania utwardzonych cienkich warstw metodą odparowania łukowego (łukowe PVD) pod próżnią Dreistegen stosuje śrubową pompę próżniową
COBRA NC firmy Busch Vacuum Solutions. Jako pompa wspomagająca współpracuje ona z dwiema równoległymi turbomolekularnymi pompami próżniowymi, wytwarzając próżnię w komorze powlekania.
W roku 2008 doktor Oliver Kayser zainaugurował własną działalność gospodarczą w budynkach starej fabryki tekstyliów w mieście Monschau w niemieckim regionie Eifel. Liczący co najmniej 200 lat temu stary budynek przemysłowy został przywrócony do życia przez firmę Kayser, której działalność początkowo koncentrowała się na azotowaniu plazmowym i powlekaniu PVD narzędzi i komponentów. To, co zaczęło się od małej firmy w częściowo zrujnowanych budynkach, przekształciło się w nowoczesne, średniej wielkości przedsiębiorstwo zatrudniające 40 pracowników nanoszących specjalne cienkie warstwy na obrabiane elementy, aby chronić je przed zużyciem i korozją. Co więcej, powłoki te mogą pomóc powstrzymać tworzenie się osadów na powierzchni. W ten sposób unika się pasożytniczych reakcji z innymi materiałami. Wielu klientów firmy Dreistegen działa w branży przetwórstwa tworzyw sztucznych i zleca powlekanie narzędzi wtryskowych, wytłaczanych lub rozdmuchiwanych. Doktor Oliver Kayser opracował specjalną formę powłoki, która zapobiega degradacji stopionego tworzywa sztucznego przez stymulację katalityczną powierzchni narzędzia. Dzięki temu tworzywo sztuczne nie przykleja się do formy. Dla operatora oznacza to, że podczas stosowania wytłaczania lub formowania wtryskowego można szybko zmienić materiał i kolor. Ponadto można zmniejszyć ilość środka ułatwiającego wyjmowanie z formy lub całkowicie wyeliminować użycie środka.
Firma Dreistegen pokrywa również narzędzia formujące i formy odlewnicze, głównie dla przemysłu samochodowego i jego dostawców. Dreistegen oferuje szeroką gamę powłok i wykończeń poprzez azotowanie, PVD i CVD.
Doktor Oliver Kayser intensywnie działa w zakresie nowoczesnych technik powlekania i nieustannie eksperymentuje ze sposobami optymalizacji cienkich warstw, aby nadać im specyficzne właściwości przynoszące korzyści jego klientom w określonych zastosowaniach. Obejmuje to również optymalizację technologii jego zakładu.
Zakupiony przez niego system do powlekania łukowego PVD, o użytecznej średnicy toczenia 1200 milimetrów i użytecznej wysokości 1500 milimetrów został pierwotnie instalowany z systemem próżniowym składającym się ze smarowanej olejem obrotowej łopatkowej pompy próżniowej jako pompy wspomagającej i z dwóch systemów wspomagania próżniowego. System ten generował podciśnienie wymagane dla dwóch turbomolekularnych pomp próżniowych, które pracowały równolegle. Kayser wymienił cały ten wspomagający zespół próżniowy na model COBRA NC 400 B firmy Busch. Śrubowa pompa próżniowa osiąga ciśnienie końcowe wynoszące 0,05 mbara (hPa) w jednym etapie. Dzięki temu jest w stanie zastąpić starą trzystopniową jednostkę próżniową innego producenta pod względem maksymalnego ciśnienia i wydajności pompowania, jednocześnie osiągając znacznie lepszą energooszczędność.
Firma Kayser docenia stabilne i niezawodne działanie pompy COBRA NC oraz jej cichą pracę. Ponadto zajmuje ona dużo mniej miejsca niż poprzedni system próżniowy.
-
Il. 2: System do powlekania łukowego PVD wykorzystujący śrubową pompę próżniową COBRA NC jako pompę wspomagającą dwóch turbomolekularnych pomp próżniowych. Źródło: Busch Vacuum Solutions
Kayser dokładnie zbadał również śrubowe pompy próżniowe innego producenta. Miały jednostronny system łożysk i były napędzane specjalnym silnikiem, który trudno się wymieniało.
Kayser był pod wrażeniem modułowej, funkcjonalnej konstrukcji pompy COBRA z dwustronnym systemem łożysk na dwóch wirnikach śrubowych i standardowym silnikiem z mocowaniem kołnierzowym, który można wymienić w dowolnym momencie.
Faktyczny proces PVD w łuku trwa 14–18 godzin od załadunku komory powlekania do usunięcia obrabianych elementów. Pompa próżniowa COBRA NC pracuje w krótkich przerwach między dwoma procesami montażu i demontażu obrabianych elementów. Oznacza to, że pompa COBRA NC pracuje przez cały rok. Dla Kaysera idealne rozwiązanie stanowi obecna konfiguracja wytwarzania próżni procesowej w jego systemie powlekania, składająca się z połączenia śrubowej pompy próżniowej COBRA NC i dwóch równoległych turbomolekularnych pomp próżniowych.
Materiał bazowy obrabianego elementu przed pokryciem łukiem PVD musi osiągnąć określony poziom twardości powierzchni. Z tego powodu firma Dreistegen zazwyczaj przygotowuje powlekane obrabiane elementy w procesie azotowania plazmowego.
Elementy azotowane plazmowo są następnie piaskowane kulkami szklanymi lub w razie potrzeby lekko polerowane. Po oczyszczeniu obrabianych elementów mocuje się je na uchwytach i ładuje do komory lakierniczej. Zamkniętą komorę następnie opróżnia się do poziomu próżni wynoszącego 5–10 mbar (hPa). Obrabiane elementy w komorze są następnie podgrzewane do maksymalnie 450°C.
Po osiągnięciu temperatury procesu naturalne tlenki ulegają erozji w plazmie z wyładowaniem jarzeniowym argonu. Następnie wyparki łukowe są zapalane i dzięki temu mogą się poruszać. Jednak dzięki magnesom trwałym, przymocowanym z tyłu, pozostają one związane z materiałami donorowymi, takimi jak tytan, chrom lub ich stopy. Można również stosować stopy aluminium lub inne metale.
W łuku materiał donorowy jest odparowywany w procesie podobnym do wybuchu, a poszczególne cząsteczki pary zostają niemal całkowicie zjonizowane. Elektryczne gruntowanie (BIAS) służy do wystrzeliwania jonów na obrabiane elementy. Dodawane są również gazy reaktywne takie jak azot, acetylen, metan, tlen i wodór. Wprowadzenie tych gazów powoduje wzrost ciśnienia w komorze powlekania do 2–10 mbar (hPa). Uwolnione z plazmy reaktywne gazy wiążą się z jonami metali na powierzchni obrabianego przedmiotu, tworząc warstwy twardej powłoki. Do typowych związków należą azotek tytanu (TiN), węgloazotek tytanu (TiCN), azotek chromu (CrN), azotek glinowo-tytanowy (AlTiN) i tlenek chromu (Cr2O3). Dzięki dużej energii cząstek i sile wyrzutu utworzona powłoka jest wyjątkowo przyczepna i jednorodna, nawet na elementach obrabianych o skomplikowanych kształtach. Cienkie warstwy utworzone przez firmę Dreistegen z zastosowaniem odparowywania łukowego osiągają poziomy twardości powyżej 2000 HV (twardość Vickersa).
W porównaniu z oryginalną jednostką próżniową nakład prac konserwacyjnych wymaganych w systemie próżniowym jest znacznie mniejszy dzięki zastosowaniu śrubowej pompy próżniowej COBRA NC.
Jedyną pracą wymaganą przy śrubowej pompie próżniowej jest coroczna wymiana oleju przekładniowego.
Doktor Oliver Kayser podkreśla, że absolutne bezpieczeństwo pracy śrubowej pompy próżniowej jest dla niego bardzo ważne. Utrata pompy próżniowej podczas procesu przyczyniłaby się do ogromnych uszkodzeń, ponieważ spowodowałoby to, że kosztowne obrabiane elementy stałyby bezużyteczne.
Po dwóch latach nieprzerwanej pracy maszyny COBRA NC doktor Oliver Kayser mówi:
W firmie Dreistegen jesteśmy zadowolonymi klientami firmy Busch i pozostajemy pod wrażeniem jakości urządzeń.