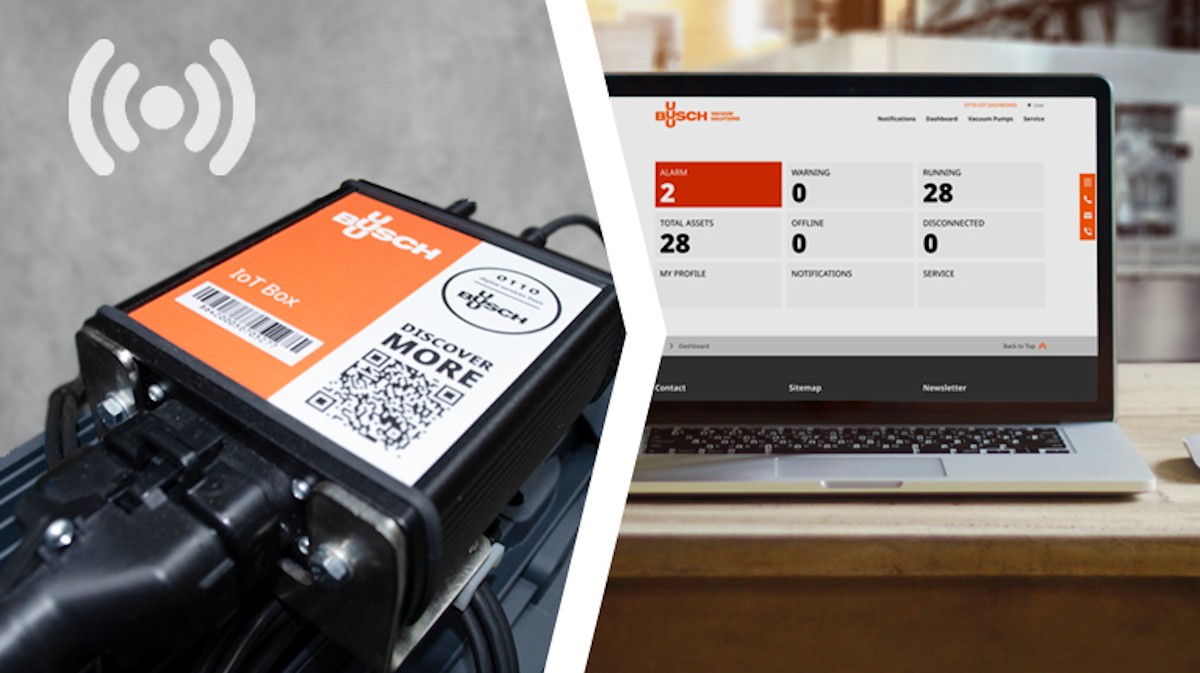
Źródło: Busch Vacuum Solutions.
7 sposobów na skrócenie czasu przestoju w produkcji
Czas przestoju w produkcji to jedno z największych zagrożeń w branży produkcyjnej. Od awarii sprzętu po braki surowców: każdy czas przestoju w produkcji może skutkować znacznymi stratami w przychodach i udziale w rynku.
Planowany czas przestoju to zaplanowane wyłączenie sprzętu lub zatrzymanie procesów produkcyjnych w celu przeprowadzenia konserwacji, inspekcji, napraw, modernizacji albo przezbrojeń. Bardzo ważne jest zaplanowanie czasu przestoju na konserwację, aby utrzymać sprzęt w jak najlepszym stanie i uniknąć nieplanowanych przestojów. Chociaż planowany czas przestoju przerywa proces produkcji, nadal ma się kontrolę nad procesami produkcyjnymi.
Nieplanowany czas przestoju ma miejsce w przypadku nieoczekiwanego wyłączenia lub awarii sprzętu produkcyjnego bądź zatrzymania procesu produkcyjnego. Wpływa na psucie się artykułów spożywczych, jeśli nie są one zapakowane, a także kosztowne opóźnienia w produkcji i dostawach. Poza tym gdy produkcja jest niestabilna, trudniej przestrzegać przepisów dotyczących ochrony środowiska i stosować środki w celu zapewnienia zrównoważonego rozwoju. Może to prowadzić do wzrostu ilości zdarzeń środowiskowych.
Dlatego zapobieganie przestojom w produkcji ma kluczowe znaczenie dla zapewnienia produktywności.
Zachęcamy do postępowania zgodnie z naszymi siedmioma wskazówkami, aby skrócić czas przestoju maszyn na linii produkcyjnej.
1. Opracowanie systemu szybkiego identyfikowania i rozwiązywania problemów produkcyjnych
-
Źródło: Busch Vacuum Solutions.
2. Wykorzystanie analityki predykcyjnej do identyfikacji potencjalnych problemów jeszcze przed ich wystąpieniem
-
Źródło: Busch Vacuum Solutions.
3. Wdrożenie programu konserwacji zapobiegawczej
Można rutynowo zbierać cenne informacje na temat swojego sprzętu, aby zapewnić systematyczne podejście do konserwacji. Odpowiednio ukierunkowana konserwacja umożliwia reagowanie na przewidywane awarie sprzętu lub wypadki, zanim do nich dojdzie. Dzięki ograniczeniu ryzyka nieoczekiwanych czasów przestoju pracownik może skupić się na bardziej dochodowych zadaniach.
-
Źródło: Piman Khrutmuang – stock.adobe.com.
4. Stworzenie systemu radzenia sobie z usterkami i problemami w miarę ich pojawiania się
-
Źródło: Busch Vacuum Solutions.
5. Automatyzacja jak największej liczby procesów w celu zmniejszenia liczby błędów ludzkich
Dzięki temu pracownicy będą mieli więcej czasu, aby skupić się na dochodowych zadaniach i rozwijać swoje umiejętności, co przełoży się na większe zyski firmy i pokaże pracownikom, że są najcenniejsi.
-
Źródło: Gorodenkoff – stock.adobe.com.
6. Szkolenie dla użytkowników w zakresie prawidłowej obsługi sprzętu
-
Źródło: Busch Vacuum Solutions.
7. Korzystanie z inteligentnych rozwiązań IoT
Inteligentne rozwiązania IoT pomagają skrócić czas przestoju dzięki systemowi, który umożliwia szybką identyfikację i rozwiązywanie problemów produkcyjnych (wskazówka 1). Monitoruje i śledzi sprzęt i proces za pomocą analityki predykcyjnej, pozwalając tworzyć harmonogram konserwacji i zamawiać niezbędne części zamienne z wyprzedzeniem (wskazówka 2). Czujniki i analityka danych umożliwiają IoT ciągłe śledzenie i monitorowanie danych dotyczących wydajności i optymalizacji. Pozwala to wdrażać konserwację zapobiegawczą (wskazówka 3) i przewidywać potencjalne problemy w miarę ich pojawiania się (wskazówka 4), co skutecznie zmniejsza częstotliwość planowanych lub nieplanowanych czasów przestoju. IoT umożliwia również automatyzację zadań, skracając czas ich realizacji, a w rezultacie zwiększając produktywność i zmniejszając liczbę błędów ludzkich (wskazówka 5). Dzięki przyjaznym dla użytkownika narzędziom łatwo nauczyć się obsługi IoT. Pracownicy w krótkim czasie będą w stanie prawidłowo z niego korzystać (wskazówka 6). Może warto zoptymalizować swój proces, instalując system IoT? Dowiedz się, w jaki sposób pulpit Busch IoT i aplikacja Busch Vacuum App mogą pomóc w monitorowaniu procesu próżniowego! Firma Busch zapewnia również konserwację zapobiegawczą, automatycznie wysyłając w razie potrzeby specjalistę ds. serwisu na podstawie analizy zebranych danych.
FAQ
Czym jest czas przestoju w produkcji?
- Czas przestoju to czas, w którym proces produkcyjny zostaje zatrzymany. Istnieją dwa rodzaje czasu przestoju: planowany i nieplanowany.
- Planowany czas przestoju to zaplanowane wyłączenie sprzętu produkcyjnego w celu przeprowadzenia konserwacji, inspekcji, napraw i modernizacji.
- Nieplanowany czas przestoju to nieoczekiwane wyłączenie lub awaria sprzętu produkcyjnego lub zatrzymanie procesu produkcyjnego.
Jak obliczyć czas przestoju w produkcji?
W celu obliczenia kosztów przestojów produkcji należy skorzystać z następującego wzoru:
Czas przestoju % = (ilość przestojów / planowany czas eksploatacji) * 100
Jaki jest średni czas przestoju w produkcji?
W wyniku przestoju sprzętu producenci tracą średnio 800 godzin rocznie, czyli ponad 15 godzin tygodniowo.
Rozważmy typowy scenariusz dotyczący fabryki parmezanu:
blok parmezanu waży średnio 42 kg. Szacunkowa cena to 9 euro za kilogram, co odpowiada jednemu blokowi parmezanu o łącznej wartości 378 euro. W ciągu minuty można wyprodukować trzy bloki sera, co daje 68 040 euro na godzinę.
Gdyby fabryka parmezanu miała w ciągu jednego tygodnia 15 godzin nieplanowanego czasu przestoju spowodowanego awarią sprzętu, straciłaby 1 020 600 euro.