Racecars need to be light, fast, and easy to handle, but must be robust enough to make tight turns at high speed without coming off the track. Carbon-fiber-reinforced materials are used to create a car body that is five times lighter than steel, but up to ten times stronger. This material with exceptional properties is manufactured using vacuum solutions from Busch.
Every year, top students from technical universities across the world compete to create a new racecar prototype, designed not for the Formula 1 racetrack, but for amateur weekend racers. Professional or not, it is no surprise that the material of choice in the high-speed world of Formula 1 is also popular in this competition, with many students choosing carbon-fiber-reinforced solutions over metal. Carbon fiber is tough – but not something you can make a car from. It is the power of a composite that gives it its unique and winning characteristics.
The synergy of a composite
Combining the properties of resin and carbon fiber creates a far stronger material than either of the two parts on their own, providing a solution that can stand up to the challenges of high speeds and strong forces. The resulting material is so durable that it can be used for virtually all visible sections of the racecar. What finishes up as one part begins as many. Pieces of resin-infused carbon fiber cloth are cut out according to a pattern, just like a tailor would cut out pieces of fabric for a suit. These are then layered together to create the thickness needed. It takes around seven layers to create just one millimeter, so the number of layers per part can quickly climb into the hundreds. Vacuum is then used to compact these layers together, and Busch provides the vacuum pumps for the job.
Fusion under vacuum
The parts are laid on a mold and sealed inside plastic bagging. A vacuum pump is attached, and the air suctioned out so that the layers are compressed against each other and cannot move. From there, the layered-up mold, still tightly compacted inside the vacuum bag, is placed in an autoclave. There, the parts are maintained under vacuum, combined with heat and pressure. The heat softens the resin, causing the layers to fuse together, and the continuous vacuum and pressure ensure that all the air is removed, the layers stay squeezed tightly against one another, and that they consolidate. What comes out of the autoclave is no longer multiple different pliable layers but one solid and robust piece, ready for the racetrack – whether competing for a place on a Formula 1 podium or for the title of best university team.
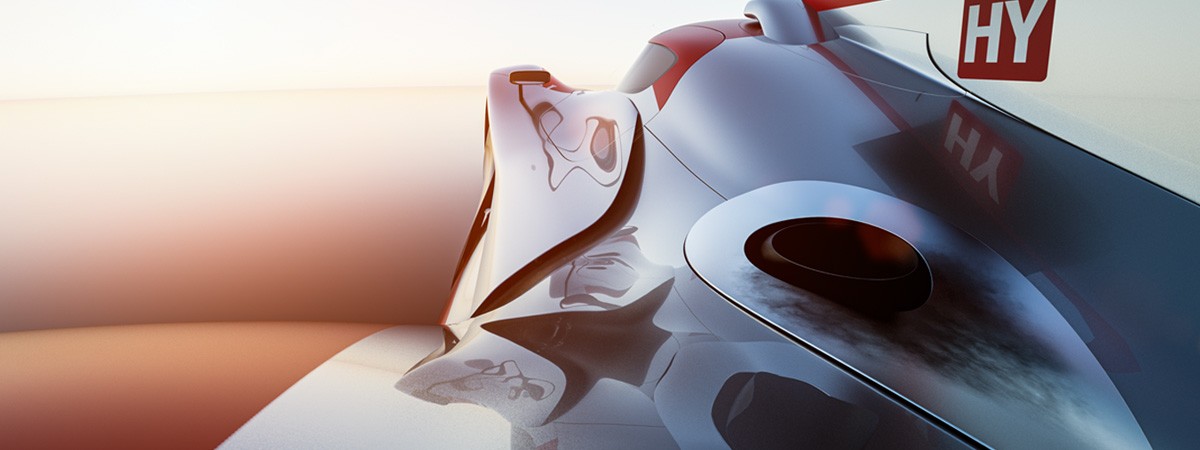
With strength and lightness around the racetrack
Carbon-fiber-reinforced solutions for lightweight speed
From lecture hall to racetrack
Designing, building, and driving a racecar to the finish line is no easy task, but every year, university students from around the world step up to the challenge and bring their prototypes to the Formula Student racetracks. Unlike Formula 1, this competition is far more than just who gets round the track fastest. The cars the students produce are graded on everything from cornering speed and fuel efficiency to manufacturing and costs – and each team must present a fully-fledged business plan. As a result, it is not only students on engineering courses that make up the teams, but also those majoring in business, finance, and marketing. The students are encouraged to manufacture as much of the car as possible themselves. This is where Busch is proud to provide support: For the past few years, Busch has been providing vacuum pumps to aid teams in building their dream racecars.
Designing, building, and driving a racecar to the finish line is no easy task, but every year, university students from around the world step up to the challenge and bring their prototypes to the Formula Student racetracks. Unlike Formula 1, this competition is far more than just who gets round the track fastest. The cars the students produce are graded on everything from cornering speed and fuel efficiency to manufacturing and costs – and each team must present a fully-fledged business plan. As a result, it is not only students on engineering courses that make up the teams, but also those majoring in business, finance, and marketing. The students are encouraged to manufacture as much of the car as possible themselves. This is where Busch is proud to provide support: For the past few years, Busch has been providing vacuum pumps to aid teams in building their dream racecars.