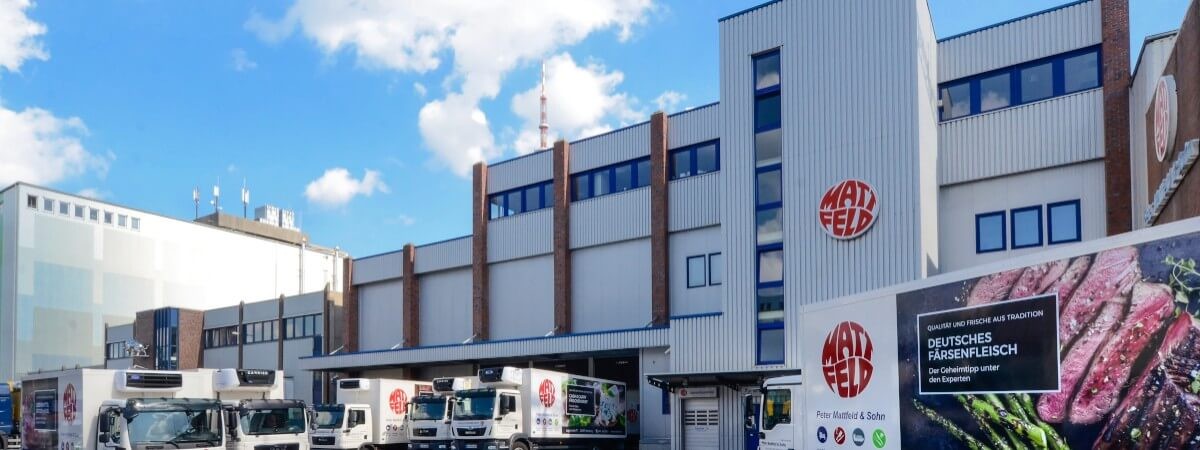
Fig. 1: The company Peter Mattfeld & Sohn GmbH is located on the premises of the meat wholesale market in Hamburg. Source: Peter Mattfeld & Sohn GmbH.
Reduction of CO2 Emissions and Operating Costs by Means of a Centralized Vacuum Supply
Peter Mattfeld & Sohn GmbH
The company Peter Mattfeld & Sohn GmbH butchers and processes up to 1,200 pig halves and 100 beef quarters per day. The meat products are cut to customer requirements or packaged as standard products and sold to customers throughout Germany. As the first EC-certified butchering facility in Hamburg, Peter Mattfeld & Sohn is also committed to resource-saving and sustainable production. An energy management audit in 2010 led to the decision to replace the vacuum supply on the individual packaging machines with a much more energy-efficient central vacuum system from Busch. This change has reduced CO2 emissions by 20 tons per year, which is an enormous benefit for the environment. At the same time, operating costs were reduced by 8,100 Euros annually.
About Peter Mattfeld & Sohn GmbH
Already in its third generation, the company Peter Mattfeld & Sohn GmbH (Fig. 1) is located on the premises of the meat wholesale market in Hamburg. The former agency for pig and beef halves has developed into a company with 150 employees today. The butchering of pork halves and beef quarters remains an important business area of Peter Mattfeld & Sohn, and one of the specialities is the North German heifer meat. The cash & carry fresh foods market for bulk purchasers, wholesale meat imports as well as the artisan convenience food production form three further pillars of the business. The broad business segment and product range also explain the complexity of the customer base. In addition to the general food industry, wholesalers and communal caterers from the clinics and catering sectors throughout Germany are among their customers.Peter Mattfeld & Sohn was already a participant in the "Unternehmen für Ressourcenschutz" (companies for resource protection) project of the Hanseatic City of Hamburg in 2009 and is also Hamburg's environmental partner.
The issue that led to the decision to change the vacuum system was the fact that the existing vacuum pumps in the three thermoforming packaging machines and one chamber packaging machine, with their heat radiation and exhaust air, unnecessarily heated the room air that was cooled to 9° C. Additional energy was then needed to cool the air in production areas.
Vacuum system solution and its benefits for the customer
For Managing Director Kai Mattfeld, it was clear that he would bring Busch Vacuum Solutions on board as a recognized specialist for vacuum generation during packaging. Busch offered a central vacuum system that was installed in a room separated from the cooled production areas. The individual packaging chambers are evacuated in two stages to be able to run maximum cycle frequencies on the packaging lines. The critical pressure gradient is exploited in each case. This enables the fastest possible evacuation time and thus achieves the highest possible cycle time on every packaging machine. One ring line for the rough vacuum for the first evacuation and one ring line for the medium vacuum for the evacuation to packaging pressure connect the packaging machines with the vacuum system. The reversing valves with the corresponding control unit are mounted on the packaging machines or in the control cabinet next to them. They control the transition from rough to medium vacuum.For thermoforming packaging machines, the molding stations are supplied using a separate thermoforming vacuum pump unit. This ensures that the previously heated base foils are sucked into the tray mold and take the desired shape. On the one hand, this separation into different vacuum stations is necessary as molding and packaging require different vacuum levels and, on the other, as a substantially lower pumping speed is required for the two-stage evacuation of the packaging chamber.
The central vacuum system is fully automatic: it activates individual vacuum modules if a higher vacuum level is required and/or switches off individual vacuum modules if the demand in vacuum is lower.
The advantages of the vacuum system were obvious soon after it was installed. The energy used to cool the production rooms could be reduced because there were no vacuum pumps installed any longer, avoiding unwanted heat emissions in the cooled rooms. The newly installed vacuum system had fewer vacuum pumps than previously required for the decentralized solution. This in itself brought further energy savings. In addition, individual vacuum pumps are automatically switched off by the vacuum system's control unit if the vacuum level in the vacuum vessels can be maintained with reduced pumping speed. The vacuum pumps in the packaging machines, on the other hand, ran non-stop from switching on the packaging machine to switching it off. Kai Mattfeld says that some vacuum pumps used to be in permanent operation from early in the morning until late in the evening, regardless of whether the machines were packaging or not.
Operational reliability was an important criterion when Kai Mattfeld purchased the central vacuum system. Due to the modular design of the vacuum system and the subdivision into rough, medium and forming vacuum, the performance of a vacuum pump can be automatically adopted by a stand-by vacuum pump in the event of a failure.
The performance of a vacuum pump can be automatically adopted by a stand-by vacuum pump. This ensures maximum operational reliability for the vacuum supply to the packaging machines.
Peter Mattfeld & Sohn has signed a service agreement with Busch. This ensures that all regular maintenance work is carried out on time and professionally for a fixed rate. Several years after going into operation, Kai Mattfeld knows that his decision to centralize the vacuum supply was the right one – from an economic point of view and for the sake of the environment!
-
Fig. 2: Partial view of the central vacuum supply at Peter Mattfeld & Sohn. Source: Busch Vacuum Solutions.