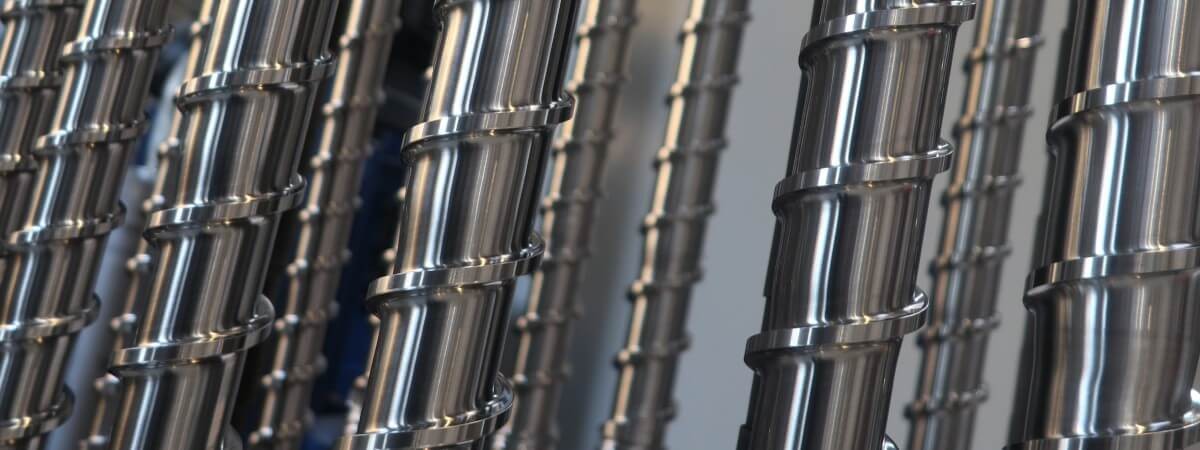
Fig. 1: parafuso de extrusora, sujeito a nitruração a plasma, preparado para o processo de revestimento PVD por arco. Fonte: Busch Vacuum Solutions.
Bomba de vácuo de parafuso para o revestimento PVD por arco
O acabamento de superfícies de grandes moldes e componentes em metal é a atividade principal da Dreistegen GmbH. Para o efeito, a empresa aplica vários tratamentos por camadas de difusão, tais como a nitruração, a carbonitretação ou a oxidação, e técnicas de revestimento, tais como a deposição física de vapor (PVD) e a deposição química em fase de vapor (CVD), aplicando plasma frio.
Para a aplicação de camadas finas endurecidas através da evaporação por arco (PVD por arco) sob vácuo, a Dreistegen recorre a uma bomba de vácuo de parafuso COBRA NC da Busch Vacuum Solutions. Tratando-se de uma bomba primária, ela funciona com duas bombas de vácuo turbomoleculares em paralelo para a geração de vácuo na câmara de revestimento.
Em 2008, Dr. Oliver Kayser lançou o seu próprio negócio nos edifícios de uma antiga fábrica de têxteis em Monschau, na região da Eifel, na Alemanha. O edifício industrial de mais de 200 anos foi revitalizado por Kayser, cujo negócio inicialmente se focava na nitruração a plasma e no revestimento por PVD para moldes e componentes. Desde os seus humildes primórdios em edifícios parcialmente deteriorados, o empreendimento tornou-se numa média empresa com 40 empregados, que aplicam camadas finas especiais em peças de trabalho para a proteção contra o desgaste e a corrosão. Além disso, estes revestimentos podem ajudar a impedir a acumulação de resíduos nas suas superfícies. Deste modo, as reações parasitárias com outros materiais são prevenidas. Muitos dos clientes da Dreistegen são da área do processamento de plásticos e contratam a empresa para revestir moldes para injeção, extrusão ou sopro. O Dr. Oliver Kayser desenvolveu uma forma especial de revestimento, que previne que a estimulação catalítica da superfície do molde provoque a degradação do plástico fundido. Consequentemente, o plástico não adere ao molde. Para a empresa fabricante, isto significa que é possível mudar o material e a cor rapidamente durante a moldagem por extrusão ou injeção. Além disso, a quantidade de desmoldante pode ser reduzida ou pode mesmo dispensar-se o seu uso.
A Dreistegen também reveste ferramentas de conformação e moldes de fundição, principalmente, para a indústria automóvel e os seus fornecedores. A Dreistegen oferece uma gama de tratamentos de nitruração, revestimentos PVD e CVD e acabamentos.
O Dr. Oliver Kayser está profundamente empenhado nas técnicas de revestimento modernas e está sempre a experimentar novas maneiras de otimizar as camadas finas, para lhes conferir propriedades específicas que gerem mais-valias para os seus clientes em determinadas aplicações. Isto também inclui a otimização da tecnologia da sua fábrica.
Originalmente, o sistema de revestimento PVD que adquiriu, com um diâmetro de viragem útil de 1200 milímetros e uma altura útil de 1500 milímetros, foi instalado originalmente com um sistema de vácuo constituído por uma bomba de vácuo de palhetas rotativas lubrificada a óleo, como bomba primária, e dois boosters de vácuo. Este sistema gerava o vácuo necessário para as duas bombas de vácuo turbomoleculares, que funcionavam em paralelo. Kayser substituiu esta unidade de vácuo primária por completo por uma COBRA NC 400 B da Busch. A bomba de vácuo de parafuso atinge uma pressão final de 0,05 mbar (hPa) num único estágio. Como tal, é adequada para substituir a antiga unidade de vácuo de três estágios de outro fabricante em termos de pressão final e caudal, alcançando uma eficiência energética muito superior.
Kayser valoriza o desempenho estável e fiável da COBRA NC e o seu funcionamento silencioso. Além disso, ocupa muito menos espaço do que o sistema de vácuo anterior.
-
Fig. 2: sistema para o revestimento PVD por arco que utiliza uma bomba de vácuo de parafuso COBRA NC como bomba primária para duas bombas de vácuo turbomoleculares. Fonte: Busch Vacuum Solutions.
Kayser também examinou cuidadosamente as bombas de vácuo de parafuso de outro fabricante. Estas dispunham de um sistema de rolamentos unilateral e eram acionadas por um motor especial difícil de substituir.
Kayser ficou impressionado com o design funcional modular da COBRA, com um sistema de rolamentos bilateral nos dois rotores de parafuso, e com o seu motor padrão flangeado, que pode ser substituído em qualquer altura.
Do carregamento da câmara de revestimento à remoção das peças de trabalho, o próprio processo PVD por arco demora entre 14 e 18 horas. A bomba de vácuo COBRA NC continua a funcionar durante as breves interrupções entre os dois processos de montagem e remoção das peças de trabalho. Isto significa que a COBRA NC funciona o ano inteiro. Para Kayser, a configuração atual para a geração do vácuo do processo no seu sistema de revestimento – constituído pela combinação de uma bomba de vácuo de parafuso COBRA NC e duas bombas de vácuo turbomoleculares em paralelo a jusante – é a solução ideal.
O material de base da peça de trabalho deve alcançar um determinado nível de dureza superficial antes de poder receber um revestimento PVD por arco. Por este motivo, por norma, a Dreistegen prepara as peças de trabalho a revestir através de um processo de nitruração a plasma.
Em seguida, as peças de trabalho tratadas por nitruração a plasma são decapadas com microesferas de vidro ou polidas ligeiramente, se necessário. Assim que as peças de trabalho tiverem sido limpas, são fixadas em suportes e carregadas para a câmara de revestimento. A seguir, a câmara fechada é evacuada até alcançar um nível de vácuo de 10-5 mbar (hPa). Em seguida, as peças de trabalho na câmara são aquecidas até uma temperatura máxima de 450 °C.
Assim que a temperatura do processo tiver sido alcançada, os óxidos naturais são erodidos em plasma de descarga luminescente de árgon. Depois, os evaporadores por arco são inflamados, podendo ser deslocados. No entanto, continuam ligados aos materiais doadores de titânio, cromo ou as suas ligas, devido aos ímanes permanentes fixados na traseira. As ligas de alumínio ou outros metais também podem ser utilizados.
No arco, o material doador é vaporizado através de um processo semelhante a uma explosão, sendo as partículas individuais do vapor quase completamente ionizadas. O escorvamento elétrico (BIAS) é utilizado para disparar os iões sobre as peças de trabalho. Os gases reativos, como o nitrogénio, acetileno, metano, oxigénio e hidrogénio, também são acrescentados. A adição destes gases causa uma subida da pressão na câmara de revestimento até 10-2 mbar (hPa). Os gases reativos libertados do plasma ligam-se aos iões do metal na superfície da peça de trabalho, para formarem camadas de revestimento duro. Alguns dos compostos típicos são o nitreto de titânio (TiN), carbonitreto de titânio (TiCN), nitreto de crómio (CrN), nitreto de alumínio-titânio (AlTiN) e óxido de crómio (Cr2O3). Devido à elevada energia das partículas e potência de projeção, o revestimento criado é excecionalmente aderente e uniforme, mesmo em peças de trabalho com formas complexas. As camadas finas criadas pela Dreistegen, através da evaporação por arco, alcançam níveis de dureza de mais de 2000 HV (dureza Vickers).
Em comparação com a unidade de vácuo original, os trabalhos de manutenção do sistema de vácuo necessários são consideravelmente menores, graças à utilização da bomba de vácuo de parafuso COBRA NC.
O único trabalho que tem de ser efetuado na bomba de vácuo de parafuso é a mudança anual do óleo de engrenagens.
O Dr. Oliver Kayser realça que a absoluta segurança de funcionamento da bomba de vácuo de parafuso é de primordial importância para ele. A perda da bomba de vácuo durante o processo iria causar grandes danos, uma vez que deixaria as peças de trabalho inutilizáveis.
Depois de dois anos de operação ininterrupta da COBRA NC, o Dr. Oliver Kayser diz:
Nós, na Dreistegen, somos clientes satisfeitos da Busch e estamos impressionados com a qualidade das máquinas.