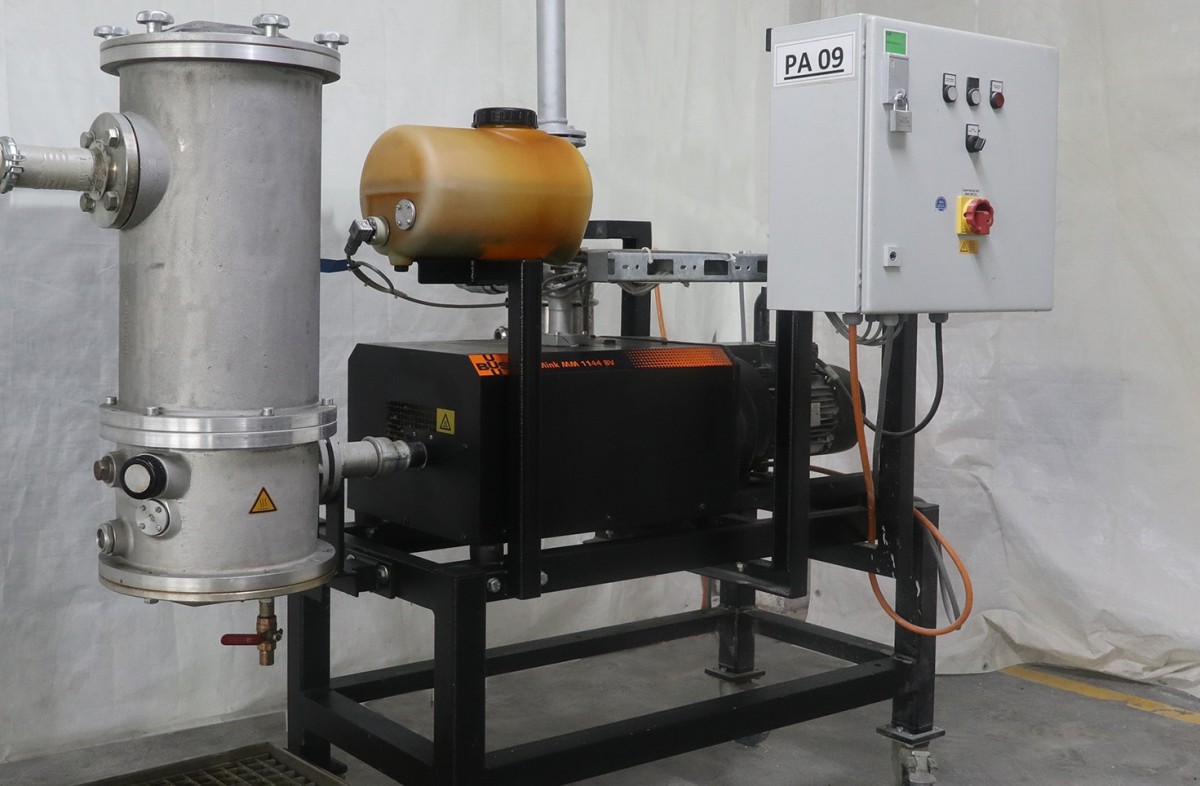
Tecnologia de vácuo moderna para a desgaseificação da fundição durante a extrusão
No entanto, há um aspeto comum a todas as extrusoras: para a extração de vapores e gases de material fundido nas secções de parafuso: a PolyComp confia exclusivamente em sistemas de desgaseificação PLASTEX da Busch Vacuum Solutions. Estes sistemas equipados com bombas de vácuo de rotores de garra MINK são excecionalmente fiáveis e fáceis de manter.
-
Fig. 1: um de um total de sete sistemas de desgaseificação PLASTEX na PolyComp. Estes sistemas estão instalados num andar por cima das extrusoras.
Sobre a PolyComp
A PolyComp foi fundada através de uma operação de compra, em 2000, e a sua sede está localizada em Norderstedt, nos arredores de Hamburgo, Alemanha. Em 2013, o controlo da PolyComp foi assumido pelo grupo Feddersen de Hamburgo, que se foca na comercialização mundial de produtos químicos e técnicos.A atividade principal da PolyComp inclui a composição de misturas de poliolefinas (PP/PE), assim como de EVA, PA, PBT, PC, ABS, EVOH, POM e PMMA. Estes compostos são misturados com vários aditivos que vão desde carbono ou fibras naturais, cargas simples a microesferas de vidro, aditivos de cor ou ceras.
Compostos para filme plástico
Uma das especialidades da PolyComp são os compostos para filme plástico, que requerem quantidades extremamente reduzidas de gel. O processo de produção inclui um estágio de extrusão com configurações de parafuso específicas e a aplicação de um dispositivo de troca de crivo com elevada precisão de filtragem. A empresa utiliza um total de oito extrusoras com fuso único ou duplo. O material fundido é desgaseificado em seis destas extrusoras. Até 2009, a empresa utilizava bombas de vácuo de anel líquido para este processo.A eliminação da água usada estava a tornar-se cada vez mais problemática, uma vez que os gases e vapores se misturavam com a água e condensavam. O custo do tratamento ou da eliminação da água estava constantemente a aumentar.
A nossa solução
Estando à procura de uma solução ecológica em 2009, a empresa entrou em contacto com a Busch, que propôs a instalação de um sistema de desgaseificação PASTEX (fig. 1), que não requer quaisquer fluidos operacionais. O sistema é constituído no essencial por uma bomba de vácuo de rotores de garra MINK (fig. 2) e um separador de líquidos e poeiras e um filtro fino a montante. Os filtros são utilizados para separar os condensados e sólidos. As bombas de vácuo de rotores de garra MINK não requerem quaisquer fluidos operacionais, tais como água ou óleo. Isto significa que os vapores e gases bombeados não entram em contacto com quaisquer fluidos operacionais, com os quais se poderiam misturar ou aos quais poderiam reagir. No entanto, nem a tecnologia de separação mais cuidadosa consegue prevenir sempre a infiltração de monómeros residuais no interior das bombas e o fenómeno de fissuração. Por este motivo, a bomba de vácuo de rotores de garra MINK está equipada com um dispositivo de limpeza. Este permite a alimentação da bomba de vácuo com uma quantidade de líquido de lavagem doseada com precisão em intervalos definidos, ajudando a evitar a formação de fissuras. O gestor de manutenção Stefan Stolp definiu a quantidade de líquido de lavagem e os intervalos de lavagem para cada um dos materiais extrudidos. O processo de lavagem pode ser executado durante os períodos de inatividade ou mesmo com a produção em curso.-
Fig. 2: as bombas de vácuo de rotores de garra MINK constituem o componente principal dos sistemas de desgaseificação PLASTEX. Graças ao seu princípio de funcionamento sem contacto, não requerem quaisquer fluidos operacionais, tais como água ou óleo.
A engenheira Simone Patermann identificou mais uma vantagem da utilização dos sistemas de desgaseificação PLASTEX. Enquanto chefe de produção, ela está sempre de olho no consumo energético, sobretudo, porque a PolyComp possui uma certificação segundo a norma ISO 50001 relativamente a sistemas de gestão energética.
Em 2018, a PolyComp lançou uma nova linha de extrusão, cujo elemento central é uma extrusora com duplo fuso, com um rendimento de até 1500 kg por hora. As duas unidades de dosagem laterais (fig. 3) permitem adicionar diferentes tipos de cargas à base de pó ao mesmo tempo, e compor uma mistura com um elevado rendimento. Uma unidade de dosagem lateral pode ser ligada a um sistema de desgaseificação PLASTEX. Isto reduz o volume de cargas e permite triplicar a densidade aparente em comparação com uma unidade de dosagem lateral sem desgaseificação. Daqui resulta um aumento considerável da taxa de rendimento total.
-
Fig. 3: as duas unidades de dosagem lateral na extrusora com duplo fuso. Um sistema de desgaseificação PLASTEX ajuda a reduzir o volume ao adicionar material de cargas. Fonte: PolyComp