The measures used to extinguish fires often cause more damage than the flames themselves. Ensuring that a fire cannot break out in the first place is always better than fighting it. The Wagner Group developed OxyReduct technology for this purpose. Vacuum pumps and compressors from Busch play a central role in this technology.
Can you name the safest metropolitan city in the world? It is the Bolivian capital of La Paz – at least when it comes to the risk of fires. Fires inside and outside of buildings are practically non-existent. The oxygen content of the air at sea level is about 21 percent. Due to the lower air pressure at an average elevation of 3600 meters, the oxygen content in La Paz is comparable to an oxygen content of 14 percent at sea level. At such a low level of oxygen, materials like wood or plastics can no longer burn. Even paper only ignites in the form of individual sheets.
Risk for archives and server centers
However, most of the world's population lives outside of Bolivia at elevations lower than the high plateaus of the Andes. This means that countless facilities are maintained at a normal oxygen concentration, which puts them at a clear risk of fire damage. These include facilities in which a fire and the associated fire-fighting measures would have existential repercussions, such as hazardous materials warehouses, archives and museum storerooms, or server centers. IT systems that serve facilities like airports simply cannot be allowed to fail!
The basic idea behind OxyReduct is to create an atmosphere similar to that found at high altitudes and thus preclude any risk of fire. Controlled introduction of nitrogen reduces the oxygen content in the air, making it impossible for a fire to start. Nitrogen is an inert gas. It suffocates fire, makes up a large part of the Earth's atmosphere and is available everywhere. It is possible to have gas producers deliver it in tanks, but that generates exorbitant costs over the long term.
Protective gas directly from the air
The OxyReduct system extracts nitrogen from the ambient air at the location where it is needed, using the vacuum pressure swing adsorption (VPSA) process to do this. The air is thereby pressed through molecular sieves made from activated carbon, which bonds oxygen molecules to its surface. Constant fluctuation between pressure and vacuum regenerates the sieves, oxygen re-enters the ambient air and the nitrogen is fed to the location where it is to be used.
MINK claw vacuum pumps and claw compressors from Busch provide vacuum and overpressure for the rapid changes in pressure. Compared to conventional oxygen reduction systems, the operating and energy costs can thus be reduced by up to 80 percent with the support of MINK technology. Busch awarded the Wagner manufacturing company with the "Innovation in Vacuum Busch Award" in 2017 for developing the OxyReduct system.
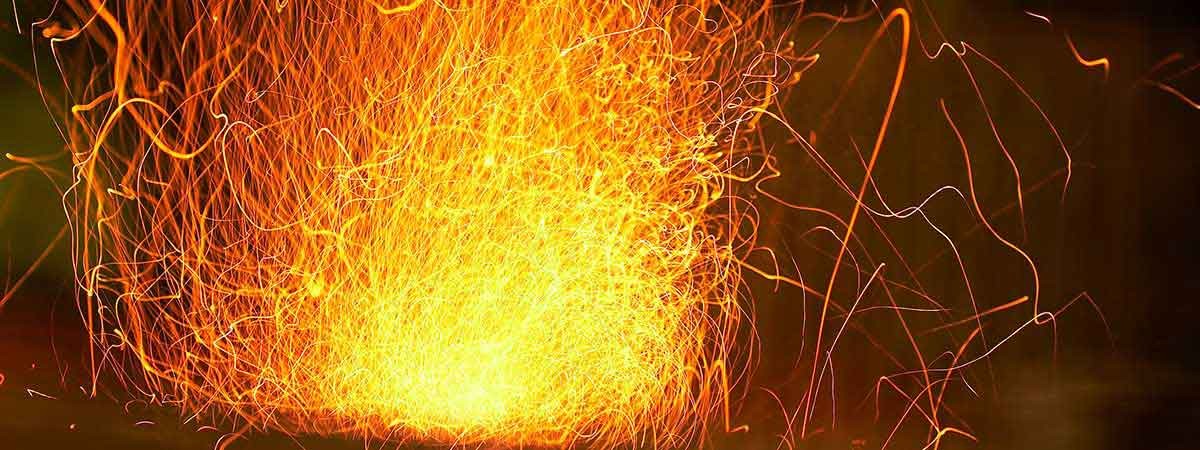
Preventive fire protection with nitrogen
Vacuum and compression produce protective atmosphere
How does VPSA work?
Technical gases are everywhere. They are used for tasks such as steel making and food processing, in water treatment or in hospitals. Most of these gases – nitrogen, oxygen, argon and other noble gases – are elements naturally found in the Earth's atmosphere. The traditional method used to extract them is air separation. Atmospheric gases have different boiling points. They can be separated from each other during the transition from the gaseous to the liquid phase. But the air has to be cooled to a temperature close to negative 200 degrees, which expends large amounts of energy.
Systems that work according to the principle of vacuum pressure swing adsorption (VPSA) work at ambient temperature and thus require significantly less energy. They use the physical process of adsorption. This requires a material with a porous structure such as activated carbon, silicate gel or a certain type of ceramic compound (zeolite). These materials adsorb certain gas molecules, which they can "hold" and concentrate on their surface. This works particularly well at increased pressures. If air is forced through this type of material, one gas is adsorbed while the others flow through. Specific gases in the mixture in the ambient air can be separated from each other this way.
However, after only a few seconds, the adsorption capacity of the porous material is exhausted. Vacuum is hence applied to separate the adsorbed gas from the material again. Then the gas is again introduced at high pressure. The VPSA system thus "oscillates", rapidly switching back and forth from vacuum to compression. The system is usually designed in duplicate: one half adsorbs while the other half regenerates. This facilitates a continuous supply of the desired gas.
Technical gases are everywhere. They are used for tasks such as steel making and food processing, in water treatment or in hospitals. Most of these gases – nitrogen, oxygen, argon and other noble gases – are elements naturally found in the Earth's atmosphere. The traditional method used to extract them is air separation. Atmospheric gases have different boiling points. They can be separated from each other during the transition from the gaseous to the liquid phase. But the air has to be cooled to a temperature close to negative 200 degrees, which expends large amounts of energy.
Systems that work according to the principle of vacuum pressure swing adsorption (VPSA) work at ambient temperature and thus require significantly less energy. They use the physical process of adsorption. This requires a material with a porous structure such as activated carbon, silicate gel or a certain type of ceramic compound (zeolite). These materials adsorb certain gas molecules, which they can "hold" and concentrate on their surface. This works particularly well at increased pressures. If air is forced through this type of material, one gas is adsorbed while the others flow through. Specific gases in the mixture in the ambient air can be separated from each other this way.
However, after only a few seconds, the adsorption capacity of the porous material is exhausted. Vacuum is hence applied to separate the adsorbed gas from the material again. Then the gas is again introduced at high pressure. The VPSA system thus "oscillates", rapidly switching back and forth from vacuum to compression. The system is usually designed in duplicate: one half adsorbs while the other half regenerates. This facilitates a continuous supply of the desired gas.