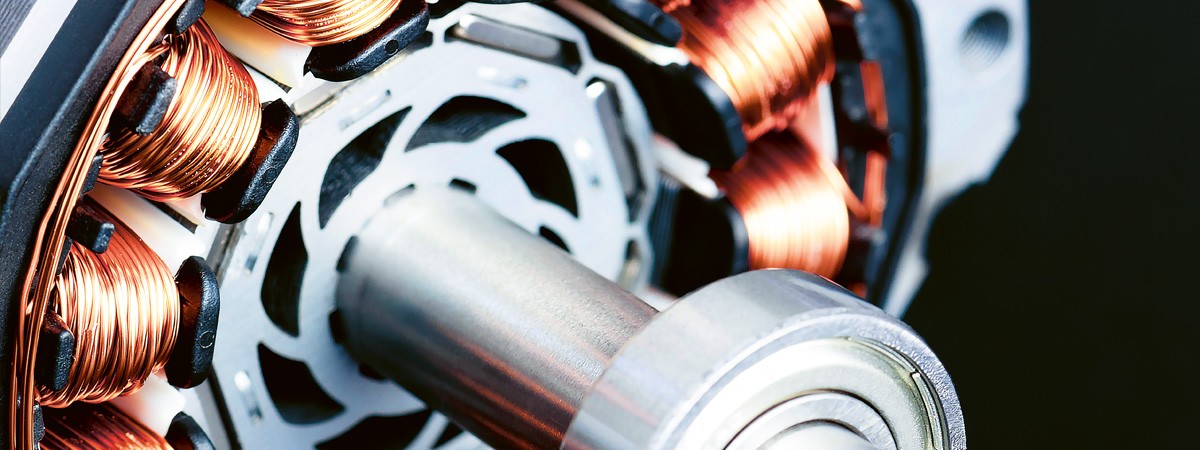
Magnets in Motion
Forming the heart of a motor with vacuum
Their invisible force can attract, repel, or set things in motion. Magnets are an integral part of the machinery we use every day. A vacuum pump from Busch ensures the high quality and resilience required of them.
Inside every motor is a permanent magnet: the driving force behind the motor’s rotation and the smooth operation of the machine it powers. This unassuming but vital piece of equipment began as an ordinary metal. To turn a metal into a magnet, it takes an electromagnetic charge and a series of mixing, grinding, heating, and pressing, assisted by a vacuum pump from Busch. However, only a few metals have the correct properties to make a permanent magnet. These are the ferromagnetic elements, which include iron, nickel and cobalt. By mixing these base metals with other materials, such as strontium carbonate, both their magnetic force and physical strength can be increased.
Aligning the charge
Ferromagnetic metals are made up of different regions called domains. Each domain has a magnetic charge – as though the piece of metal contains hundreds or thousands of tiny individual magnets. However, before the metal is processed, the domains are not aligned, and so they cancel each other out. In order to make an entire piece of metal magnetic, the domains must be aligned. To achieve this, the metal mixture is ground multiple times until each particle contains just one domain. First, the metal is ground in a dry process. Then it is ground again, with water added to the fine powder to create a slurry.
From mass to magnet
The wet process is what allows the new magnet to be formed into the shape required for a motor. The slurry is compacted into a form – in this case, small, curved rectangles that fit either side of the rotor. Once shaped, the excess water must be removed. First, the mass is pressed in the form and the resulting liquid removed. Then, a vacuum pump is used. It gently draws out the humidity so that it can be drained off. Putting the mass under vacuum also eliminates any small water or air pockets that might still be present, which could otherwise lead to unwanted porosity and weakness in the finished product. Once sufficient moisture has been removed, it’s time for the metal to become a magnet. The form is sintered in an oven at 1200 °C, then cooled. Finally, a strong electromagnetic charge is applied. This pulls all the previously jumbled domains into alignment and creates a coherent magnetic field. And so, a magnet is born, ready to turn a motor.
Aligning the charge
Ferromagnetic metals are made up of different regions called domains. Each domain has a magnetic charge – as though the piece of metal contains hundreds or thousands of tiny individual magnets. However, before the metal is processed, the domains are not aligned, and so they cancel each other out. In order to make an entire piece of metal magnetic, the domains must be aligned. To achieve this, the metal mixture is ground multiple times until each particle contains just one domain. First, the metal is ground in a dry process. Then it is ground again, with water added to the fine powder to create a slurry.
From mass to magnet
The wet process is what allows the new magnet to be formed into the shape required for a motor. The slurry is compacted into a form – in this case, small, curved rectangles that fit either side of the rotor. Once shaped, the excess water must be removed. First, the mass is pressed in the form and the resulting liquid removed. Then, a vacuum pump is used. It gently draws out the humidity so that it can be drained off. Putting the mass under vacuum also eliminates any small water or air pockets that might still be present, which could otherwise lead to unwanted porosity and weakness in the finished product. Once sufficient moisture has been removed, it’s time for the metal to become a magnet. The form is sintered in an oven at 1200 °C, then cooled. Finally, a strong electromagnetic charge is applied. This pulls all the previously jumbled domains into alignment and creates a coherent magnetic field. And so, a magnet is born, ready to turn a motor.
Magnets formed by lightning bolts
Not all magnets are made in a factory. Lodestone is a magnetic metal that can be found in nature. While man-made magnets are formed with high heat and controlled electricity, lodestone has a much more dramatic start to life. It begins as simple magnetite, which, despite its name, is not magnetic. For many years it was believed that it was magnetized by the Earth’s own magnetic field; however, the leading theory now is that it is magnetically charged by lightning strikes. When lightning touches down onto the Earth’s surface, it creates, for a very brief moment, an extremely strong electromagnetic field. This is enough to cause a change in the magnetite’s substructure and align its domains, ultimately “awakening” its magnetic capabilities.
Not all magnets are made in a factory. Lodestone is a magnetic metal that can be found in nature. While man-made magnets are formed with high heat and controlled electricity, lodestone has a much more dramatic start to life. It begins as simple magnetite, which, despite its name, is not magnetic. For many years it was believed that it was magnetized by the Earth’s own magnetic field; however, the leading theory now is that it is magnetically charged by lightning strikes. When lightning touches down onto the Earth’s surface, it creates, for a very brief moment, an extremely strong electromagnetic field. This is enough to cause a change in the magnetite’s substructure and align its domains, ultimately “awakening” its magnetic capabilities.