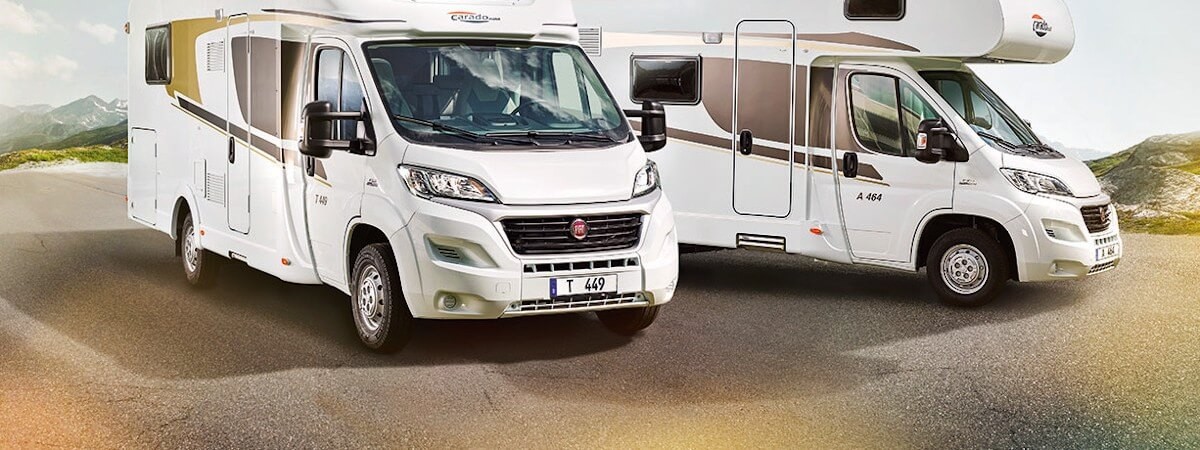
Carado motor homes and Sunlight motor homes and caravans are manufactured by Capron in Neustadt, Saxony. Source: Capron GmbH.
Huge Energy Savings with Centralized Vacuum Concept
Capron GmbH
A central vacuum system from Busch reduces energy costs in woodworking with CNC Machines.
This was the experience of Capron GmbH, a Germany-based manufacturer of Sunlight brand caravans. Interior fittings are manufactured in CNC machining centres using nesting tables and vacuum block units. On top of energy savings of 40%, Capron saved on maintenance costs and made its processes more efficient.
About Capron
Capron GmbH was founded in 2005 as part of the Erwin Hymer Group, and commenced production in 2006. The company now employs 390 staff, and manufactures more than 30 Carado and Sunlight motor homes and caravans daily. These are marketed internationally by distribution companies of the same name. In 2016 both brands are offering a range of 13 motor home models, and five different caravan layouts. The range extends from a compact two-person vehicle to a family model with sleeping accommodation for six. Vehicle assembly is carried out on two production lines 450m and 250m in length. The larger production line is the longest in the industry in Europe.Capron GmbH manufactures 6,500 Carado and Sunlight brand caravans annually at the company’s production site in Neustadt, Saxony. Capron’s manufacturing techniques focus on qualified staff, modern and lean production, and an efficient logistics system which requires no expensive warehousing. The company is also an extremely efficient energy consumer, one of the reasons for installing a centralized vacuum supply to clamp wooden components to the processing machines. Capron chose the latest claw vacuum technology by Busch.
Handling of workpieces on CNC machines
The interior fittings, including all wall and ceiling elements, are produced from wooden composite panels by CNC machining centres. The materials used are mainly poplar plywood, plywood composites, spruce strips and polystyrene, aluminium compounds, and glass-reinforced plastics. These materials are clamped by vacuum to the nesting tables and console vacuum block units. The original vacuum supply comprised up to three locally installed rotary vane or liquid ring vacuum pumps for each CNC machining centre. The continuous increase in production capacity from 1,200 vehicles in the first year 2006 to 6,500 in 2015 prompted the installation of additional machining centres, which were supplied with Busch MINK claw vacuum pumps as standard equipment. Toni Pietsch, the Capron project management director, immediately recognised the advantages of this technology in comparison to the previously used vacuum generators:- Lower energy consumption due to higher efficiency
- Significantly reduced maintenance effort due to contact-free and wear-free operating principle
- No operating fluids in the compression chamber, eliminating all fluid-related maintenance
- No carbon vanes requiring regular replacement
- No expenditure for replacement parts or disposal of operating fluids
-
View of the assembly line for motor homes. Source: Capron GmbH.
Vacuum system solution and its benefits for the customer
In 2015 Toni Pietsch decided to centralize the vacuum supply. The first stage was to connect five nesting machines to a central vacuum system. On the basis of positive experience with MINK claw vacuum technology, only these vacuum generators were considered. Busch project engineers designed a central vacuum system with a pumping speed equivalent to the nominal maximum demand of the five nesting machines, as defined by the machine manufacturer. In the knowledge that the actual demand was far less, tests were conducted to evaluate the demand in everyday use. After a year, the tests determined that a maximum of five or six of the twelve MINK claw vacuum pumps were required to meet the demand created by full production. This opened the way to the second stage of the project, in which seven additional machining centres with consoles will be connected to the central vacuum system without increasing the number of vacuum pumps. This stage will be implemented in the summer of 2016 with the extension of the vacuum ring main.
The control system automatically activates only the number of vacuum pumps required to meet the current demand.
The vacuum pumps are operated alternately, so they are all in service for approximately the same number of hours. The central vacuum system is connected to the machining centres by a ring main, which also serves as a vacuum reservoir. This has the advantage of immediate availability when vacuum is required by the clamping tables. The central system activates individual vacuum pumps as required to meet demand. According to Toni Pietsch, the centralization of the first four machining centres reduced energy consumption by about 40%.
The centralization of the first four machining centres reduced energy consumption by about 40%.
The cost-benefit analysis looks even more attractive when maintenance savings are included: costs for time, replacement parts, and materials disposal are all substantially lower. The central vacuum system is installed in a separate room. Waste heat generated by the system is recovered and used to heat the adjacent training workshop, further improving the overall energy balance.
Operational reliability is a high priority at Capron, so the four modules of three MINK claw vacuum pumps each have independent power supplies. If the power supply for one of these modules should fail, another module will activate automatically to take its place. The system will continue to operate in the event of controller failure: all vacuum pumps may be started and stopped individually by hand. Filters are installed directly at the machining centres to prevent dust or larger particles entering the vacuum system. The filter collection bins are transparent, so operators can see immediately if a bin requires emptying. Toni Pietsch found the absence of noise and heat emissions in the production area to be a further advantage, as this has led to better working conditions. In addition, valuable production space beside the machining centres can now be put to better use.
Operational reliability is a high priority at Capron, so the four modules of three MINK claw vacuum pumps each have independent power supplies. If the power supply for one of these modules should fail, another module will activate automatically to take its place. The system will continue to operate in the event of controller failure: all vacuum pumps may be started and stopped individually by hand. Filters are installed directly at the machining centres to prevent dust or larger particles entering the vacuum system. The filter collection bins are transparent, so operators can see immediately if a bin requires emptying. Toni Pietsch found the absence of noise and heat emissions in the production area to be a further advantage, as this has led to better working conditions. In addition, valuable production space beside the machining centres can now be put to better use.
-
Partial view of the Busch centralized vacuum system with a total of twelve MINK claw vacuum pumps. Source: Busch Vacuum Solutions.