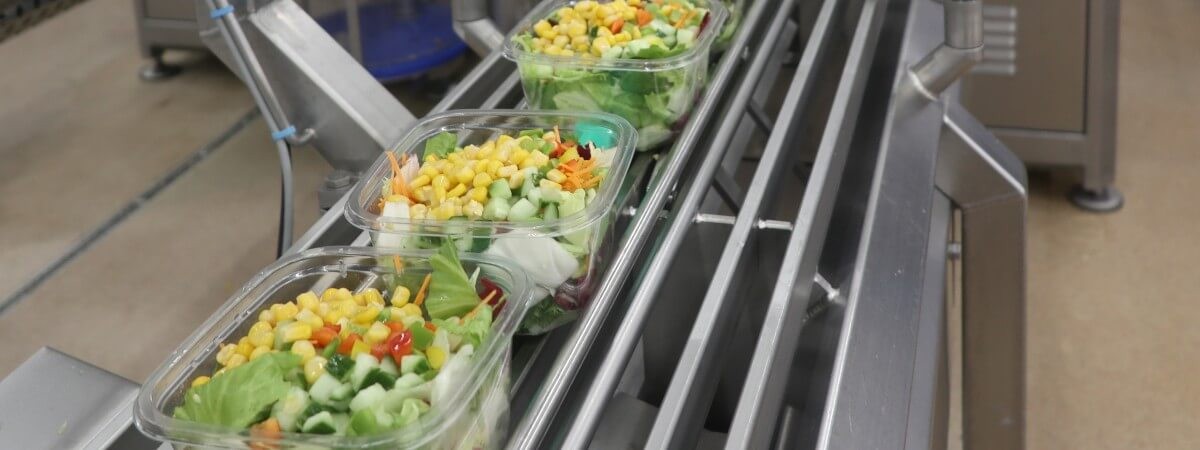
Fig: 1: One of twelve lines used to package convenience products on tray sealers. Source: Busch Vacuum Solutions.
Enormous Energy Savings for Packaging Process
Gartenfrisch Jung
Fresh and ready-to-eat salads, vegetable dishes, herbs, and freshly cut fruit form part of Gartenfrisch Jung GmbH's product portfolio. The long-established company has evolved into the German market leader for fresh convenience products thanks to its quality and experience. Since early 2019, the vacuum supply to its tray sealer packaging machines has been exceptionally energy-efficient following the installation of a central vacuum system by Busch Vacuum Solutions.
About Gartenfrisch Jung
Gartenfrisch Jung produces its convenience foods in a modern facility in Jagsthausen, a town in the German state of Baden-Württemberg. To allow it to supply fresh raw produce all year round, the company has its own growers in Germany and Portugal. Cultivation in two different climate zones ensures that the entire product range can be supplied year-round, sold to end users across Germany via supermarket chains and discount stores.
Gartenfrisch Jung processes 120 tonnes of raw food every day.
Process of evacuation
The ready-to-eat salad dishes (Fig. 1) are packaged on twelve packaging lines with tray sealer packaging machines. In the past, these packaging machines were equipped with one rotary vane vacuum pump each, though one machine had two vacuum pumps. These 13 vacuum pumps were used to evacuate the trays to the required vacuum level prior to sealing. A two-shift operation is in place on all twelve packaging lines. The vacuum pumps ran constantly throughout these shifts, apart from during breaks. During a third shift, the production facilities are cleaned while all machinery is stationary.
Jochen Neff, who is in charge of technology at Gartenfrisch Jung, was looking for an alternative vacuum supply, because the heat radiated by the 13 vacuum pumps was putting a strain on the air conditioning system in the production facilities, which are cooled to between 5 and 6 degrees Celsius. Furthermore, the vacuum pumps had an installed motor output of over 50 kilowatts. The vacuum experts from Busch Vacuum Solutions analyzed the situation and recommended a centralized vacuum supply, which could be set up in a non-air-conditioned room outside the production facilities.
Vacuum system solution and its benefits for the customer
Because Jung's convenience products have the ideal vacuum for packaging at a vacuum level of 400 millibars, Busch recommended using MINK claw vacuum pumps.
No oil-based lubrication is required.
-
Fig. 2: Vacuum system with three MINK claw vacuum pumps during assembly with the two vacuum vessels in the background. Source: Busch Vacuum Solutions.
Centralizing the vacuum supply enabled the total installed motor rating to be reduced from 50.2 to 16 kilowatts (Fig. 3) if we assume that two of the vacuum pumps run at 60 Hertz, i.e. maximum power.
This would correspond to a 68 percent reduction in energy consumption. However, in practice Jochen Neff has discovered that only one of the two MINK claw vacuum pumps is normally in use and that this tends to run at a reduced rotational speed. After several months of use, Jochen Neff has measured average power consumption of four kilowatt hours for the entire vacuum supply. This is mainly linked to the fact that the twelve packaging lines do not all always run at maximum speed and not all of the machines are in use all the time. The demand-based control system then decreases the rotational speed to reduce the output, meaning that the system only provides the performance that is actually required. In practice, this equates to energy savings of over 90 percent for vacuum generation.
The demand-based control system only provides the performance that is actually required. This equates to energy savings of over 90 percent for vacuum generation.
-
Fig. 3: Comparison of energy consumption for a decentralized and centralized vacuum supply. Source: Busch Vacuum Solutions.
The new centralized vacuum system was installed in April 2019 and has been in use every since. It is connected to the packaging machines via a network of pipelines. Two upstream vacuum vessels with a volume of 1,500 liters each make sure that the required vacuum level is available in the packaging chambers as soon as it is needed in the packaging cycle. Removing the 13 original vacuum pumps from the production areas relieved strain from the air conditioning system. This meant that the air conditioning system could be turned down to keep the room temperature between 5 and 6 degrees Celsius. The savings in energy costs as a result of reducing the air conditioning output have not been measured. However, it can generally be assumed that the change resulted in a significant reduction in the energy consumed by the air conditioning system.
Thanks to the vacuum system's redundant design, maintenance can be carried out on the individual MINK claw vacuum pumps during production and packaging. MINK claw vacuum pumps are nearly maintenance-free. Maintenance is limited mainly to the annual preventive change in gear oil. This is performed by a Busch service technician. With the centralized vacuum system, Jochen Neff has created a highly energy-efficient, reliable and economical vacuum supply for packaging his convenience products.
Thanks to the vacuum system's redundant design, maintenance can be carried out on the individual MINK claw vacuum pumps during production and packaging. MINK claw vacuum pumps are nearly maintenance-free. Maintenance is limited mainly to the annual preventive change in gear oil. This is performed by a Busch service technician. With the centralized vacuum system, Jochen Neff has created a highly energy-efficient, reliable and economical vacuum supply for packaging his convenience products.