Undersea cables carry data streams and electricity over long distances. They are coated with plastic by extruders under vacuum to ensure that they remain stable and their insulation remains intact.
It is a miracle, however, that they even exist. A whole series of attempts to lay undersea cables in the 1850s and 1860s failed miserably. They broke, corroded quickly, got entangled in fishing nets, or could not be stopped when unrolling into deep water. Moreover, the performance of the first functioning cables was extremely modest, and they were only suitable for telegraphy. But the world insisted on being connected, and so all hurdles were eventually overcome.
Nowadays, undersea cables transmit gigantic streams of data between all continents. They are also needed for supplying power, for example to islands and offshore plants. Conversely, they supply green electricity from sea-based wind farms to the mainland.
Strict requirements
Undersea cables must meet very strict requirements to be able to reliably provide this infrastructure service. In addition to high mechanical strength, they also require high chemical stability. The insulation and conductor material must withstand both the strain during installation and the permanent attack from the aggressive salt water for as many decades as possible.
Among other things, the cable cores for conducting current and data – such as copper strands or glass fiber strands – must be protected by insulating layers. They are given a coating consisting of several layers of highly stable plastics. For example, current-conducting strands typically have three different layers: a thin layer of molten polyethylene (PE) is applied directly to the metal and serves to smooth its surface. This is followed by the second, actual insulation layer made of a different PE plastic. The third coating of a further PE layer provides mechanical protection.
Multi-layer production
The plastic is melted in an extruder and then fed into a mould. The copper strand is fed into the mold and the plastic is placed around it. Vacuum is permanently maintained in the mold between the strand and the coating. It ensures that the three layers cling directly to the metal or to each other without air inclusions. From the individual cables produced, additional steps are taken to create multi-core undersea cables, which for example connect the power grids on both sides of a waterway. Due to the often extreme length of such cables, an extrusion process can take a whole week, during which the process must be uninterrupted. MINK claw vacuum pumps have proven to be particularly efficient and reliable in this context.
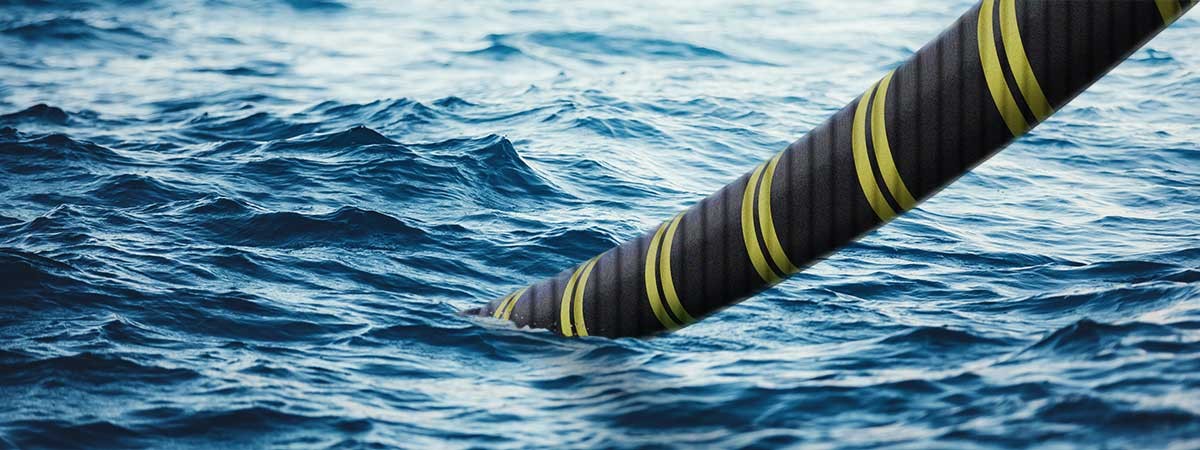
A Connected World
Vacuum lends undersea cables stability and durability
How long is the longest undersea cable?
This is certainly not an easy question to answer. On the one hand, new cables are constantly being laid, and every record will probably be broken in the foreseeable future. On the other hand, it would be fair to divide this "competition" into two categories:
Power cables
Currently, the 580-kilometre NorNed cable is probably the longest undersea cable carrying electricity. It connects the networks of Norway and the Netherlands. Several, significantly longer cables are being planned or already under construction.
Data cables
The longest undersea cable network for data transmission connects Europe, Africa, Asia and Australia. It runs through the three oceans, the Mediterranean Sea and the Red Sea. Its 39 landing points include the German North Sea coast, Djibouti, Perth in Australia and Okinawa in Japan. Including all its branches, it has a total length of around 39,000 kilometers.
This is certainly not an easy question to answer. On the one hand, new cables are constantly being laid, and every record will probably be broken in the foreseeable future. On the other hand, it would be fair to divide this "competition" into two categories:
Power cables
Currently, the 580-kilometre NorNed cable is probably the longest undersea cable carrying electricity. It connects the networks of Norway and the Netherlands. Several, significantly longer cables are being planned or already under construction.
Data cables
The longest undersea cable network for data transmission connects Europe, Africa, Asia and Australia. It runs through the three oceans, the Mediterranean Sea and the Red Sea. Its 39 landing points include the German North Sea coast, Djibouti, Perth in Australia and Okinawa in Japan. Including all its branches, it has a total length of around 39,000 kilometers.
An interactive overview of all undersea cables can be found here:
www.submarinecablemap.com
www.submarinecablemap.com