Ein kontinuierliches Verfahren für die Herstellung von Leichtbauplatten schafft neue Möglichkeiten – nicht nur fürs Urban Paddling. Beim Formen der Elemente spielt Vakuum eine wichtige Rolle.
Die Straßen verstopft, U- und S-Bahn rappelvoll – in Städten wie Amsterdam, Austin oder Macao schweift der Blick in den Stoßzeiten schon mal über die kaum genutzten Wasserwege: Hätte man doch nur ein Boot zur Hand! Seit kurzem kann man diese Phantasie relativ leicht und preisgünstig in die Tat umsetzen. Die belgische Firma Onak hat ein Kanu entwickelt, das im Wesentlichen aus einem einzigen Stück Kunststoffplatte besteht. Diese lässt sich zu einem Trolley von der Größe eines mittleren Koffers zusammenfalten und ebenso transportieren. Auseinandergefaltet verwandelt es sich in wenigen Minuten in ein funktionierendes Wasserfahrzeug.
Waben geben Halt
Das Geheimnis des neuartigen Bootes ist sein Material, eine Sandwichplatte mit Wabenkernen aus Polypropylen (PP). Wie der Name sagt, erinnert ihr Inneres an Bienenwaben. Die Wände der Sechsecke geben den Halt, die vielen Hohlräume zwischen ihnen und den Deckschichten machen die Platte extrem leicht.
Wegen eben dieser Eigenschaften werden ähnliche Platten schon seit längerem im Rennsport sowie in der Luft- und Raumfahrt verwendet. Allerdings ist ihre herkömmliche Herstellung ziemlich aufwendig, weil Deckschicht und Innenleben getrennt produziert und Platte für Platte zusammengefügt werden.
An der Universität Löwen in Belgien hat Dr.-Ing. Jochen Pflug vor einiger Zeit ein Verfahren entwickelt, um Wabenkernplatten per Endlosverfahren in einem Durchgang zu fertigen. Danach gründete er die Unternehmen EconCore und ThermHex, die das Verfahren lizenzieren beziehungsweise selbst für die Herstellung der Endlosplatten verwenden.
Formen und Falten
Bei dieser thermoplastischen Wabenkernproduktion gelangt der formbare Kunststoff direkt aus der Extrusion durch eine Breitschlitzdüse auf eine Rotationsvakuumtiefziehwalze. Ihr Name beschreibt die Funktion: Die Walzenoberfläche ist so gestaltet, dass sie die Wände für halbe Waben vorformt. Vom Vakuum in ihrem Inneren und durch viele Löcher auf der Oberfläche wird das heiße Material in die entsprechende Form gezogen. Die Rotation sorgt für kontinuierlichen Ausstoß.
In einem ausgeklügelten Prozess werden die Wabenhälften anschließend gefaltet und zu ganzen Waben zusammengefügt. Im selben Durchgang können nun unterschiedliche Deckschichten auflaminiert werden. Sie können aus Kunststoff, Metallblech oder faserverstärkten Organo-Sheets bestehen. Letztere kann man später verformen und durch Spritzguss zu Funktionseinheiten wie Ösen, Griffen oder Halterungen gestalten. Die Wabenkernplatten kommen überall dort zum Einsatz, wo stabile flächige Leichtbauelemente benötigt werden. Neben dem Kanu fürs Urban Paddling – ein neuer Trend? – können das zum Beispiel auch Rümpfe für große Yachten, LKW-Aufbauten, Karosserieteile, Elemente für den Hausbau oder Gondeln für Windkraftgeneratoren sein.
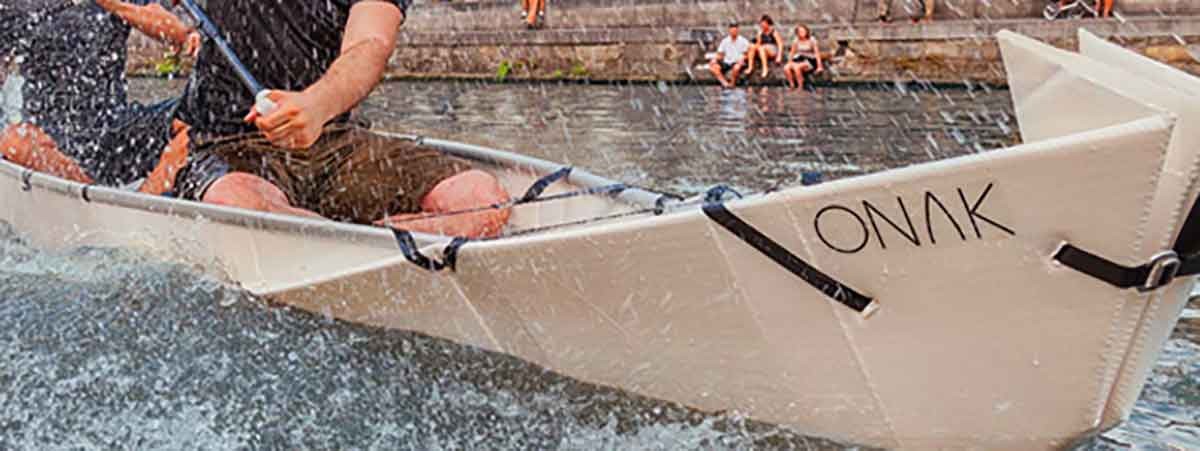
Endlos leichte Platten
Vakuum hilft bei kontinuierlichem Produktionsprozess
Warum Wabe?
Die Natur neigt zu Sparsamkeit. Deshalb tendiert sie dazu, Flächen als Kreise und Körper als Kugeln zu formen – möglichst viel Inhalt bei minimiertem Außen. Ordnet sie viele Kreise nebeneinander an, eliminiert sie die unweigerlichen Lücken: Aus dem Kreis wird ein Sechseck, aus der Kugel die Wabe. Woher die Bienen wissen, dass dies die mathematisch sparsamste Struktur ist und wie sie beim Wabenbau zuverlässig exakte 120-Grad-Winkel bilden, ist unbekannt. Sicher ist, dass die Insekten damit bei geringstem Wachsverbrauch das stabilste dreidimensionale Gebilde schaffen, das mit ihrer „Technologie“ möglich ist. In der Strukturbionik hat der Mensch dieses Muster übernommen und verwendet es für zahlreiche statische Elemente.
Die Natur neigt zu Sparsamkeit. Deshalb tendiert sie dazu, Flächen als Kreise und Körper als Kugeln zu formen – möglichst viel Inhalt bei minimiertem Außen. Ordnet sie viele Kreise nebeneinander an, eliminiert sie die unweigerlichen Lücken: Aus dem Kreis wird ein Sechseck, aus der Kugel die Wabe. Woher die Bienen wissen, dass dies die mathematisch sparsamste Struktur ist und wie sie beim Wabenbau zuverlässig exakte 120-Grad-Winkel bilden, ist unbekannt. Sicher ist, dass die Insekten damit bei geringstem Wachsverbrauch das stabilste dreidimensionale Gebilde schaffen, das mit ihrer „Technologie“ möglich ist. In der Strukturbionik hat der Mensch dieses Muster übernommen und verwendet es für zahlreiche statische Elemente.