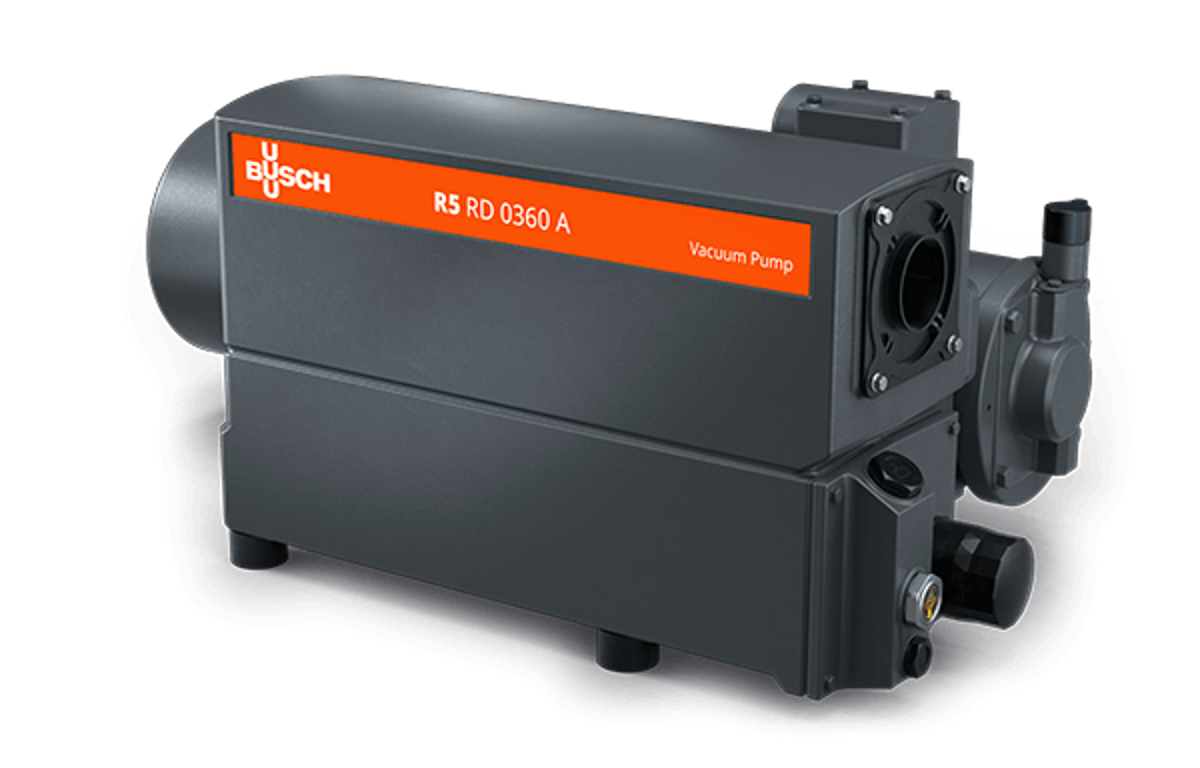
Abb. 1: Die Drehschieber-Vakuumpumpe R5 RD 0360 A ist eine Baugröße der neuesten Generation von Vakuumpumpen für das Verpacken. Quelle: Busch Vacuum Solutions.
Energieeffiziente Vakuumversorgung für fleischverarbeitende Betriebe
Hygienische Verpackung von Fleisch- und Wurstwaren
Ein integriertes Verpackungskonzept, das eine hygienische, sichere, schnelle und effiziente Verpackung der fertigen Produkte gewährleistet, ist ein wichtiger Bestandteil der modernen Fleisch- und Wurstwarenproduktion.
Deshalb arbeiten innovative fleischverarbeitende Betriebe kontinuierlich daran, ihre Produktionsprozesse zu optimieren und ihre Verpackungslinien bestmöglich in den Gesamtprozess zu integrieren. Die richtige Auswahl der Vakuumsysteme hat einen wesentlichen Einfluss auf die Betriebssicherheit und Wirtschaftlichkeit des Verpackungsprozesses. Je nach Größe der Anlage und den Produktionsmengen gibt es verschiedene Möglichkeiten der Vakuumversorgung. Diese Alternativen werden im Folgenden erläutert, und es werden Denkanstöße gegeben, um eine technologisch wie wirtschaftlich optimale Lösung zu finden.
Die richtige Auswahl der Vakuumsysteme hat einen wesentlichen Einfluss auf die Betriebssicherheit und Wirtschaftlichkeit des Verpackungsprozesses.
Die Vakuumverpackung von Fleisch- und Wurstwaren bietet einen grundlegenden Vorteil: Durch das Absaugen der Luft aus der Verpackung wird der Sauerstoffgehalt stark reduziert, die Aktivität der sauerstoffbedürftigen Bakterien verlangsamt und die Haltbarkeit dadurch erheblich verlängert.
Darüber hinaus ist die Vakuumverpackung hygienisch und ermöglicht eine ansprechende Präsentation der Produkte. Auf dem Markt ist eine breite Palette von Vakuumverpackungsmaschinen erhältlich, sodass für jeden Verpackungsbedarf eine geeignete Verpackungsmaschine zur Verfügung steht. Unabhängig von ihrem Design oder ihrer Baugröße haben diese Verpackungsmaschinen eines gemeinsam: Bei allen Maschinen muss Vakuum erzeugt werden, um die Anforderungen an die Vakuumverpackung zu erfüllen. Dies kann entweder durch eine integrierte oder eine separate Vakuumpumpe geschehen. Andere Alternativen sind zentrale Vakuumversorgungssysteme, an die mehrere Verpackungsmaschinen angeschlossen sind.
Auf dem Markt ist eine breite Palette von Vakuumverpackungsmaschinen erhältlich, sodass für jeden Verpackungsbedarf eine geeignete Verpackungsmaschine zur Verfügung steht.
Integrierte Vakuumpumpe
Üblicherweise wird die Vakuumpumpe bei jeder Vakuumverpackungsmaschine – sei es eine Vakuumkammerverpackungsmaschine, ein Traysealer oder eine Tiefziehverpackungsmaschine – integriert oder separat in unmittelbarer Nähe aufgestellt. Dabei werden fast ausschließlich ölgeschmierte Drehschieber-Vakuumpumpen (Abb. 1) eingesetzt.
Ständige Weiterentwicklungen sorgen dafür, dass die Vakuumpumpen der Dr.-Ing. K. Busch GmbH immer auf dem neuesten Stand der Technik sind und weltweit millionenfach eingesetzt werden.
Die Vakuumpumpe, entweder integriert oder separat bei der Verpackungsmaschine aufgestellt, ist die einfachste und gängigste Art zur Erzeugung von Vakuum für das Verpacken. Kurze Leitungen zwischen der Vakuumkammer, der Versiegelungsstation und der Vakuumpumpe sorgen dafür, dass die Luft schnell aus der Verpackung entfernt wird. Größere Tiefziehverpackungsmaschinen mit hohem Verpackungsvolumen können auch mit einem Vakuum-Booster ausgestattet werden.
Höhere Drehzahlen können durch die Kombination von Drehschieber-Vakuumpumpen mit Vakuum-Boostern erreicht werden, wodurch sich die Evakuierungszeit reduziert.
Teilzentralisierung
Bei der Teilzentralisierung (Abb. 2) werden die Drehschieber-Vakuumpumpen aus dem eigentlichen Verpackungsraum herausgenommen und in eine zentrale Vorvakuumanlage für alle Verpackungsmaschinen in einem separaten Raum integriert. Direkt in die Verpackungsmaschinen werden trockene, ölfreie Vakuum-Booster eingebaut und durch ein Rohrsystem mit der zentralen Vorvakuumerzeugung verbunden. Ein Teilzentralisierungssystem ist immer dann sinnvoll, wenn zwei bis maximal fünf Tiefziehverpackungsmaschinen in einem Bereich in geringem Abstand voneinander betrieben werden. Bei mehr Verpackungsmaschinen werden die Investitionskosten durch die Vakuum-Booster in den einzelnen Maschinen zu hoch, und es empfiehlt sich die komplette Zentralisierung der Vakuumversorgung.
-
Abb. 2: Teilzentralisierung der Vakuumversorgung. Quelle: Busch Vacuum Solutions.
Zentrale Vakuumversorgung
- Wirtschaftlichkeit
Für eine zentrale Vakuumversorgung werden üblicherweise weniger Vakuumpumpen benötigt.
-
Abb. 3: Vollzentralisierung der Vakuumversorgung. Quelle: Busch Vacuum Solutions.
-
Abb. 4: Zentralisierte Vakuumanlage für 30 Verpackungslinien mit Tiefziehverpackungsmaschinen. Quelle: Busch Vacuum Solutions.
- Hygiene
- Arbeitsweise
Dafür benötigt man einen Grobvakuumpumpstand für die Erstevakuierung und einen Feinvakuumpumpstand für die Evakuierung auf Verpackungsdruck. Die Umsteuerventile mit der dazugehörenden Umsteuerelektronik werden an den Verpackungsmaschinen angebracht. Sie steuern den Übergang von Grob- auf Feinvakuum.
Bei Tiefzieh-Verpackungsmaschinen wird die Formstation von einem separaten Tiefzieh-Vakuumpumpstand versorgt. Dieser sorgt dafür, dass die zuvor erwärmte Unterfolie in die Schalenform gesaugt wird und dort die gewünschte Form annimmt.
Diese Trennung in unterschiedliche Vakuumstationen ist zum Einen nötig, weil Form- und Siegelfunktion bei unterschiedlichen Vakua ablaufen, und zum Anderen, weil ein deutlich geringeres Saugvermögen bei der Zwei-Stufen-Evakuierung der Siegelkammer erforderlich ist. Das Rohrleitungssystem dient als Vakuumpuffer. Dieser Puffer ist nötig, um den Verpackungsdruck konstant zu halten und zwar auch dann, wenn alle Verpackungsmaschinen taktgleich fahren.
Das zentrale Vakuumsystem arbeitet vollautomatisch, das heißt, es schaltet bei hohem Vakuumbedarf einzelne Vakuummodule zu, bzw. bei Minderbedarf werden einzelne Vakuummodule ausgeschaltet. Sollte eine Vakuumpumpe im Grob-, Fein- oder Tiefziehpumpstand ausfallen, wird der Reservepumpstand automatisch in Betrieb gesetzt. Somit besteht für die Vakuumversorgung der Verpackungsmaschinen ein Höchstmaß an Betriebssicherheit.
- Wartung
- Integration ins Prozessleitsystem
Zusammenfassung
Bei Anlagen mit mindestens zwei Vakuumverpackungsmaschinen sollte der Betreiber oder der verantwortliche Betriebsleiter berücksichtigen, wie das Vakuum erzeugt wird. Man sollte nicht vergessen, dass auch die Produktion, z. B. mit Wurstfüllern oder Tumblern, Vakuum benötigt, das ebenfalls von einer zentralen Vakuumversorgung geliefert werden kann.
Die Dr.-Ing. K. Busch GmbH ist der weltweit größte Hersteller von Vakuumpumpen für das Verpacken.