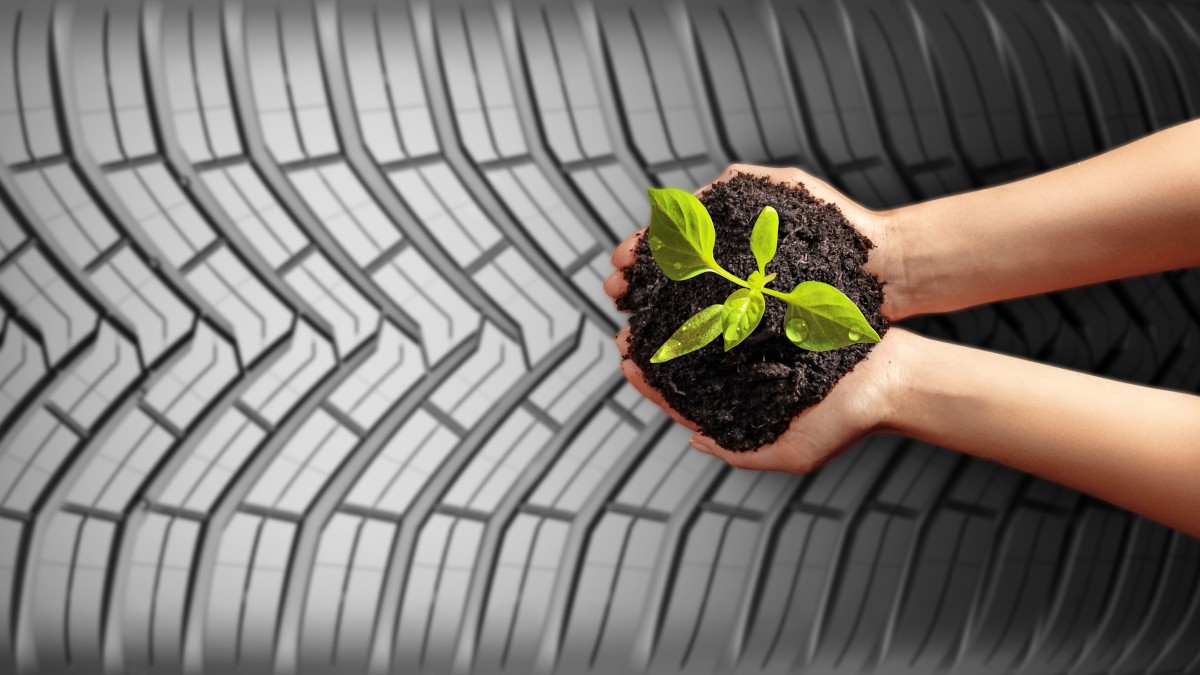
Fig. 1: Continental-dæk er fremstillet ved hjælp af den nyeste vakuumteknologi fra Busch. Foto: Continental Reifen GmbH.
Ny vakuumløsning sikrer sikre og bæredygtige dæk hos Continental
Continental Reifen Deutschland GmbH
Continental Reifen Deutschland GmbH fremstiller kvalitetsdæk til biler og varevogne på sin produktionsfabrik i Aachen i Tyskland. I fremstillingsprocessen for dæk anvender Continental en ekstremt effektiv metode til generering af vakuum, hvor en central vakuumforsyning fra Busch Vacuum Solutions leverer den nødvendige vakuum til at sikre en sikker håndtering på tre tekstilskæremaskiner. Ud over at reducere støjen i produktionslokalet betydeligt giver denne vakuumløsning også store besparelser på dækproducentens energi- og vedligeholdelsesomkostninger.
Næsten hver tredje bil i Europa kører på dæk fra Continental, som blander selve råmaterialet naturgummi, ekstruderer det og efter flere mellemtrin omdanner det til monteringsklare dæk. Et enkelt dæk består hovedsageligt af tre hovedkomponenter: tekstilsnor, ståltråd og en blanding af naturgummi. Disse tre grundmaterialer kombineres på en bestemt måde i de enkelte komponenter i dækket og samles derefter som karkassen og bæltet, der formes til et dæk og hærdes.
Tekstilsnoren består af et stort antal tekstiltråde og indsættes i en maskine ved hjælp af en stor afspolingsanordning. Det er her, tekstilsnoren belægges med naturgummi, og der skabes et gummibelagt net i form af en kontinuerlig lang strimmel, der er mindre end en millimeter tyk. Dette net afskæres til den ønskede bredde vinkelret i forhold til trådmønstret og rulles til en tekstilrulle igen med henblik på videre bearbejdning. Tekstilmaterialet fastgøres senere på det inderste gummilag. Den fungerer som et forstærkende element på indersiden af dækket. Gevindenes radiale orientering sikrer yderligere stabilitet. Dette lag påvirker primært dækkets bæreevne samt affjedringsegenskaber og køreegenskaber.
Næsten hver tredje bil i Europa kører på dæk fra Continental, som blander selve råmaterialet naturgummi, ekstruderer det og efter flere mellemtrin omdanner det til monteringsklare dæk. Et enkelt dæk består hovedsageligt af tre hovedkomponenter: tekstilsnor, ståltråd og en blanding af naturgummi. Disse tre grundmaterialer kombineres på en bestemt måde i de enkelte komponenter i dækket og samles derefter som karkassen og bæltet, der formes til et dæk og hærdes.
Tekstilsnoren består af et stort antal tekstiltråde og indsættes i en maskine ved hjælp af en stor afspolingsanordning. Det er her, tekstilsnoren belægges med naturgummi, og der skabes et gummibelagt net i form af en kontinuerlig lang strimmel, der er mindre end en millimeter tyk. Dette net afskæres til den ønskede bredde vinkelret i forhold til trådmønstret og rulles til en tekstilrulle igen med henblik på videre bearbejdning. Tekstilmaterialet fastgøres senere på det inderste gummilag. Den fungerer som et forstærkende element på indersiden af dækket. Gevindenes radiale orientering sikrer yderligere stabilitet. Dette lag påvirker primært dækkets bæreevne samt affjedringsegenskaber og køreegenskaber.
Brug af vakuum på tekstilskæremaskiner
Vakuumteknologi anvendes til håndtering af opgaver ved tekstilskæremaskinen. Den gummibelagte bane skæres til i den ønskede længde og sættes derefter direkte på en anden strimmel ved hjælp af pick-and-place. Her er præcis placering det vigtigste aspekt i forhold til kvaliteten af det færdige tekstilnet. De enkelte lag skal ligge lige oven på hinanden. Tidligere blev der monteret en sidekanalblæser i hver af de tre tekstilskæremaskiner. De leverede det nødvendige vakuum til håndtering af strimlerne af tekstil. Blæserne kørte konstant på fuld kraft og brugte derfor enorme mængder energi. Derudover skabte de betydelig støjforurening for produktionspersonalet.
Bæredygtig vakuumforsyning fra Busch til tekstilskæremaskiner
En medarbejder fra Continental Reifen foreslog via den interne ledelse for idégenerering, at man skulle se nærmere på vakuumforsyningen til tekstilskæremaskinerne. Deres primære bekymring var den akutte støjforurening på grund af de tidligere anvendte sidekanalblæsere. Eftersom Continental altid leder efter potentielle måder at forbedre sig på, besluttede de sig for at finde en mere ergonomisk og effektiv løsning. Vakuumeksperterne hos Busch Vacuum Solutions anbefalede at bruge en MINK-klovakuumpumpe til at generere vakuum og leverede i første omgang et testsystem. Det tog kun et par dage for Ingmar Heinze, afdelingsleder for forsyning og bæredygtig infrastruktur, at blive overbevist om, at han havde fundet den rigtige løsning til generering af vakuum. Efter testkørslen blev der installeret et vakuumsystem med to MINK MV Synchro-vakuumpumper på Continental. Dette system erstattede de tidligere tre sidekanalsblæsere og leverer nu centralt det nødvendige vakuum til flere tekstilskæremaskiner via rør i rustfrit stål. Synkrone MINK MV-vakuumpumper er som standard udstyret med en frekvensomformer og en efterspørgselsdrevet styreenhed. Vakuumpumperne registrerer den pumpehastighed, de skal bruge til en igangværende proces for at holde den gummibelagte tekstilsnor sikkert på plads og placere den præcist.
-
Fig. 2: Vakuumforsyning med to MINK MV-klovakuumpumper til håndtering af tekstilsnore. Kilde: Busch Vacuum Solutions.
Fordele ved Busch vakuumforsyning i tekstilskæring
Heldigvis gjorde brugen af dette nye vakuumsystem mere end blot at løse det primære problem med støjforurening. De hidtidige sidekanalblæsere opnåede et støjniveau på 94 dB. Det betød høj støjforurening for medarbejderne i produktionshallen. Med det nye vakuumsystem fra Busch kan vakuumanlæggets støjniveau ikke engang registreres, fordi det overdøves af den normale omgivende støj – hvilket betyder, at det er under 72 dB.Ud over den betydelige støjreduktion har det nye vakuumsystem også medført betydelige energibesparelser. Takket være den efterspørgselsdrevede styring anvendes der ikke altid fuld ydelse, hvilket betyder, at vakuumsystemet ofte kører med lavere rotationshastighed og strømforbrug. Systemet lukker også automatisk ned, når der ikke er nogen tekstiltråde, der skal holdes. Strømforbruget for de tidligere anvendte blæsere var generelt 15 kWh. Ved målinger med det nye vakuumsystem blev der målt et gennemsnitligt energiforbrug på kun 800 watt pr. time.
Det svarer til energibesparelser på over 90 %. Så investeringen betalte hurtigt sig selv og er på grund af energiaspektet berettiget til støtte fra det tyske forbundskontor for økonomi og eksportkontrol (BAFA).
Den nye løsning sparer også tæt på 90 procent af de årlige vedligeholdelsesomkostninger. Sidekanalsblæserne krævede omfattende reparationer og var derfor en kilde til høje omkostninger. MINK MV-klovakuumpumper giver fuldstændig tør kompression af indsugningsluften og fungerer dermed uden driftsvæsker såsom olie eller vand. Det gør vakuumpumperne stort set vedligeholdelsesfrie. Nedetider i forbindelse med servicering var også et problem. For det nye vakuumsystem med to MINK-klovakuumpumper kan de få, nødvendige serviceopgaver udføres på en af de to vakuumpumper, mens den anden fortsætter med at forsyne systemet med vakuum. Det betyder, at der ikke er flere afbrydelser, og at tekstilskæremaskinerne er mere tilgængelige.
Det nye vakuumsystem har nu kørt siden januar – til Ingmar Heinzes fulde tilfredshed.
Vi er meget tilfredse med vores nye vakuumforsyning til håndtering af tekstilstrimler under dækfremstilling. Vi var ikke alene i stand til at mindske støjforureningen for vores medarbejdere betydeligt, vi var også i stand til at reducere energiforbruget og vedligeholdelsesindsatsen betydeligt og øge systemets produktivitet. Det er et godt eksempel på bæredygtig forbedring!
-
Fig. 3: Rørledninger til vakuumforsyning til tekstilskæremaskiner hos Continental Reifen Deutschland GmbH. Kilde: Busch Vacuum Solutions.