For a process that needs air flow, you have two options available: an air blower or a compressor. Compressors and blowers vary by the pressure of the air that they produce. Compressors compact air into a small space, making it denser. Blowers, on the other hand, only move it by increasing the pressure slightly. If you need a solution with lower pressure, you will find all relevant information about blowers.
Operating principle of air compressors
A compressor is a mechanical device that reduces the volume of air or gas to increase the pressure. The operating principle of vacuum pumps and compressors is the same, just in reverse.There are two basic types of air compressors: positive displacement and dynamic.
A positive displacement compressor draws in air at atmospheric pressure and compresses it. It does this via a mechanical reduction process. Depending on the type of compressor, claws, vanes, or impeller blades push the same volume of air into an increasingly smaller space before forcing it out through the outlet.
All compressors offered by Busch are positive displacement compressors.
Types of positive displacement compressors

Rotary vane compressors
A rotary vane compressor uses an elliptical slotted rotor situated within a cylinder. The rotor has slots along its length, each slot contains a vane. The vanes are forced outwards by centrifugal force when the compressor is rotating, and the vanes move in and out of the slot because the rotor is eccentric to the casing. The vanes sweep the cylinder, sucking air in on one side and ejecting it on the other. In general, vane compressors are used for smaller applications where floor space is an issue; however, they are not as efficient as rotary screw compressors.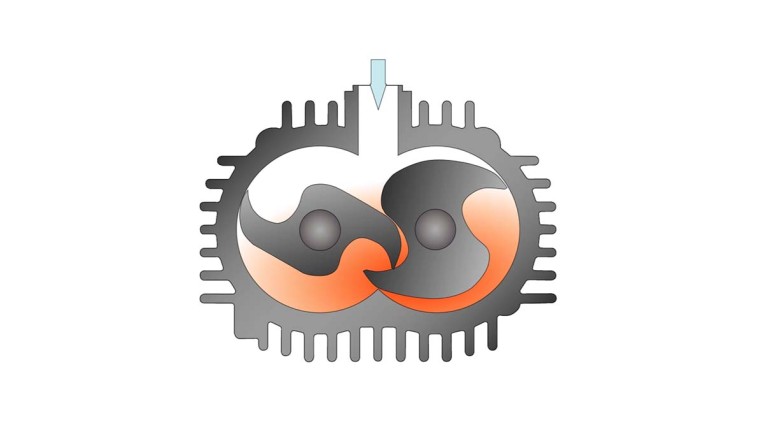
Claw compressors
Claw compressors feature two claw-shaped rotors. The rotors are mounted in a cylinder and move in opposite directions. The shape of these claw rotors extracts, compresses, and expels the air or gas.The claw rotors do not come into contact with each other or the housing. The minimal clearance between the rotors and the chamber housing optimizes the internal seal. This means that no lubricants or operating fluids are required in the compression chamber.
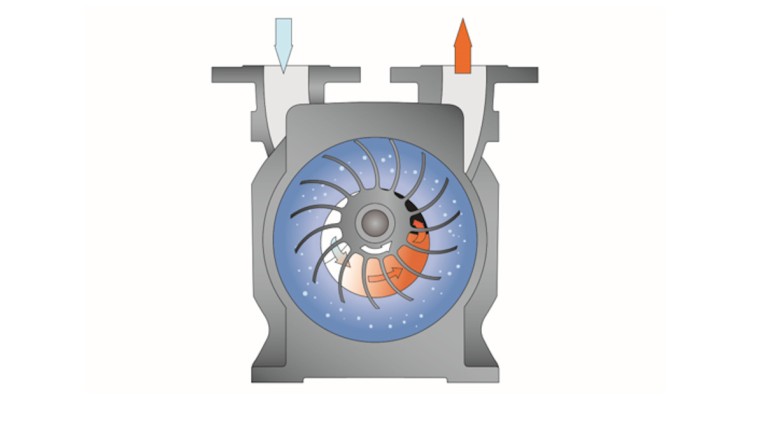
Liquid ring compressors
An eccentrically mounted impeller rotates in a housing partially filled with operating fluid. The impeller blades dip into the fluid, and the centrifugal force exerted by their rotation forms what is known as a liquid ring within the housing. The operating fluid is usually water, but other liquids may be used if required by the process conditions.The air or gas is transported in the spaces between the blades and the liquid ring. The eccentric rotation of the impeller alters the volume of these spaces. The air or gas is drawn in, compressed, and expelled.
In single-stage versions, compression is carried out once. In two-stage versions, the air or gas is compressed again to allow higher compression to be achieved.
Liquid ring compressors can be operated as a simple continuous flow system, or as a partial or total recirculation system.
TECHNICAL CONSIDERATIONS FOR SELECTING AIR COMPRESSORS
Only a thorough analysis of your process can help you decide which compressor is appropriate. Key factors that you should consider are: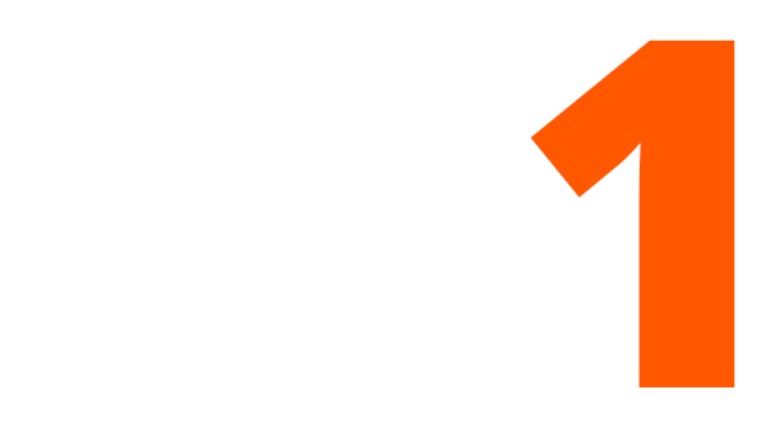
Pressure and Flow
The pressure you need is determined by how much force is needed to perform a certain task at a particular moment. Choose a compressor that does not generate enough pressure, and it will not be able to complete the task, but choose a compressor that generates more pressure than is needed, and energy will be wasted.Flow refers to how well the compressor can carry out the task over a certain period. A lower flow is needed if a task is carried out intermittently than if it is continuous. For a continuously running process, the compressor must have adequate flow to avoid interruptions.
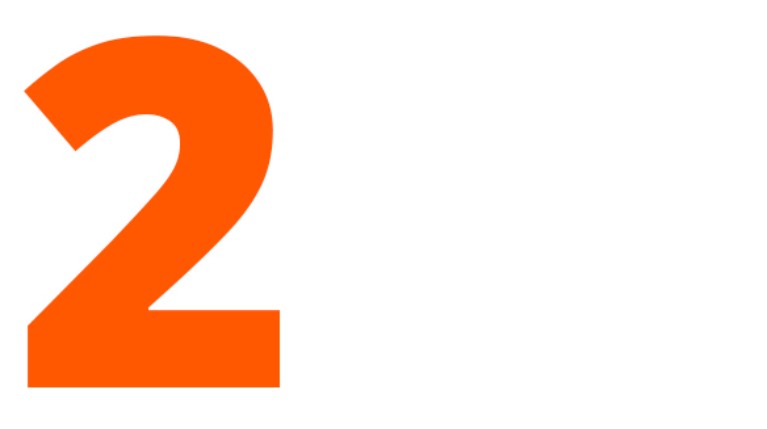
Operating conditions
Where will the compressor be installed? The operation of a compressor can be affected by ambient temperatures and elevation, so a compressor that is a good choice in one location may not be suitable in another. You should also consider the humidity levels. Noise is another factor – if your compressor is to be located near workstations, a quieter solution would be best.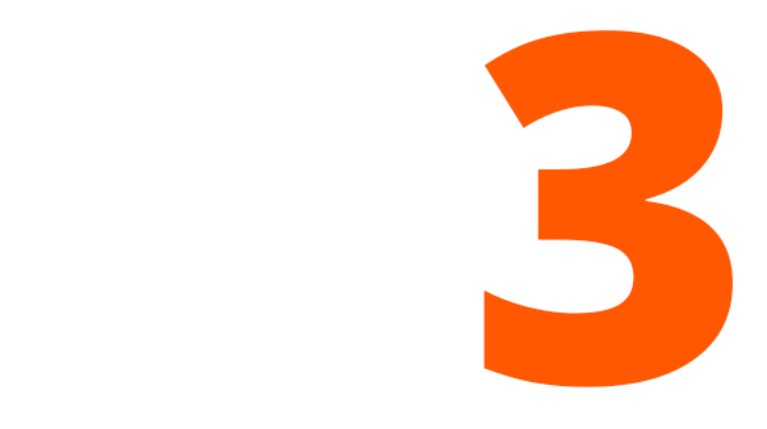
Cooling system
Do you need an air-cooled or water-cooled compressor? Determining how the gas to be compressed behaves during the compression process will give you the answer. Liquid ring compressors run much cooler than other compressor technologies and are therefore best for applications that require compression of explosive gases. You should also consider your own set-up, such as ambient temperature, ventilation, and room layout, as this may affect your decision.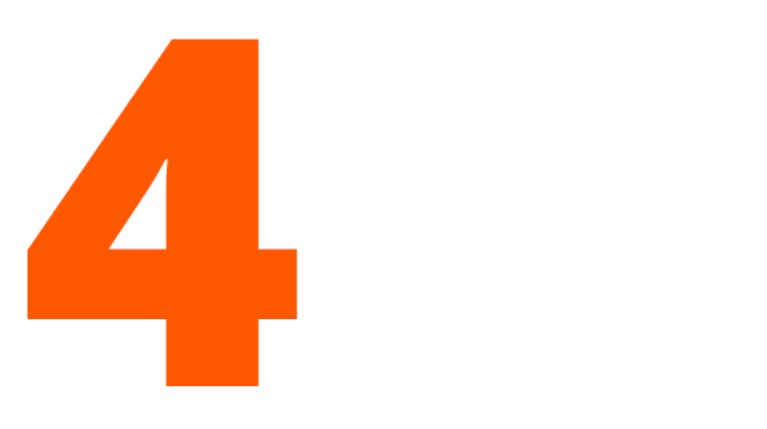
Lubrication system
Compressors can be dry, dry-running, liquid-sealed, or lubricated. Dry and dry-running systems are the ideal solution for processes that require the output gas to be completely free of oil and moisture, such as in the food and beverage industry. Liquid-sealed compressors provide a second oil-free option, as liquid ring technology requires no additional lubrication in the compression chamber. Busch offers compressor solutions that are dry, dry-running, or liquid sealed.Main uses for air compressors
Compressors find application in different industries and are also prevalent in settings that are familiar to everyday consumers. For example, the portable 12V DC electric air compressor that is often carried in the glove compartment or trunk of a car is a common example of a simple version of air compressor that finds use among consumers to inflate tires to the correct pressure.Some of the common applications and industries that utilize compressors include the following:
-
Healthcare industry
Compressed air is used in many different applications throughout hospitals and other medical facilities. Compressors generate breathing air for those with respiratory conditions, under anesthesia, or who need to inhale certain medications. Compressed air is also used to power surgical tools and equipment in the operating room. In dental procedures, compressors provide compressed air to power pneumatically operated dental instruments, such as drills or toothbrushes.
-
Biogas production
To create biogas, organic waste is broken down by microorganisms in an oxygen-free environment. Compressors are used in the recirculation process to increase the activity of these anaerobic bacteria and avoid sediment accumulating on the bottom of the tank. They also compress the biogas before it is injected into the natural gas network pipeline.
-
Pneumatic conveying
Pneumatic conveying is used in many manufacturing processes to transport dry bulk materials or powders through a pipeline. Find out more.
-
Printing industry
The printing industry uses compressed air for various processes, such as separating individual paper sheets and feeding them into the printing machine. Compressed air is also needed for such tools as pressers, rollers, and paper drills.
-
Controlled atmosphere ultra-low-oxygen storage
After harvest, fruits and vegetables can either be transported immediately, or stored for later. A controlled atmosphere in ultra-low-oxygen storage (CA/ULO) increases the storage time while maintaining the product’s original taste. Compressors are an integral part of the pressure swing adsorption (PSA) process, which generates the nitrogen necessary to create the optimal storage atmosphere.
FAQ
How do air compressors work?
Air compressors compress air or gas, creating a high-pressure air flow. The exact operating principle varies depending on the technology, but a positive displacement air compressor pushes air through a chamber of gradually decreasing volume.
What is the difference between a blower and a compressor?
While both a compressor and a blower create overpressure, they use different methods and give different results. A blower uses a slight increase in pressure to push the air or gas in a certain direction. A compressor raises the pressure of the air or gas by compressing it into a small space, making it denser.
What is the difference between a vacuum pump and a air compressor?
The operating principle is the main difference between a vacuum pump and a compressor. A vacuum pump draws air from a closed environment or container, creating vacuum. An air compressor draws air from the ambient environment and compresses it into a container with a high pressure. Put simply, a compressor fills a space with air, and a vacuum pump empties it.
What size of air compressor do I need?
The pressure you need is determined by how much force is needed to perform a certain task at a particular moment. Choose a compressor that does not generate enough pressure, and it will not be able to complete the task, but choose a compressor that generates more pressure than is needed, and energy will be wasted.
Flow refers to how well the compressor can carry out the task over a certain period. A lower flow is needed if a task is carried out intermittently than if it is continuous. For a continuously running process, the compressor must have adequate flow to avoid interruptions.
If you are uncertain what size of compressor is best for your application, get in touch with us . We will be happy to help.