Lithium-ion batteries are at the heart of e-mobility. Key processes during their manufacture are performed under vacuum. BUSCH has the proper vacuum pumps for various requirements.
Lithium (Li) is the lightest of the solid elements and its electrically charged ions move extremely easily. Li-ion batteries – the ones in cars being rechargeable – can store more charge per unit of mass than other battery types. This not only makes them the ideal energy source for smartphones and tablets, but also for electric cars. They are currently the only batteries that make reasonable ranges possible.
Paste free of air pockets
The interior of the batteries is made up of foils of electrodes that are coated with a lithium paste (slurry). The raw materials for the slurry are blended in a mixer. The output should be a homogeneous mass without air pockets. To remove possible air pockets, vacuum is applied in the mixer.
After casting the slurry, the coated electrodes need to dry. Moisture in the battery cells would lead to loss of performance and premature aging. Drying under vacuum ensures that any remaining moisture is very efficiently reduced to a minimum.
Electrolyte filling and formation
The ions move between the electrodes using a conductive material: the electrolytes. Liquid electrolytes are applied using an injection lance. During this process, a defined pressure profile is used to switch between evacuation and flushing with an inert protective gas to evenly distribute the mass throughout the cell. The wetting of the electrodes to improve current flow is also improved using this method.
During the formation process, the battery cells are electrically charged for the first time. This releases gases that can be both toxic and explosive. They are therefore suctioned out using vacuum pumps.
In the end, the quality control process is used to check the finished battery cells for leakage. If there is a leak, electrolyte solution that evaporates under vacuum escapes and can be easily detected. BUSCH identifies the ideal solution for the various vacuum technology requirements that each individual application needs to meet.
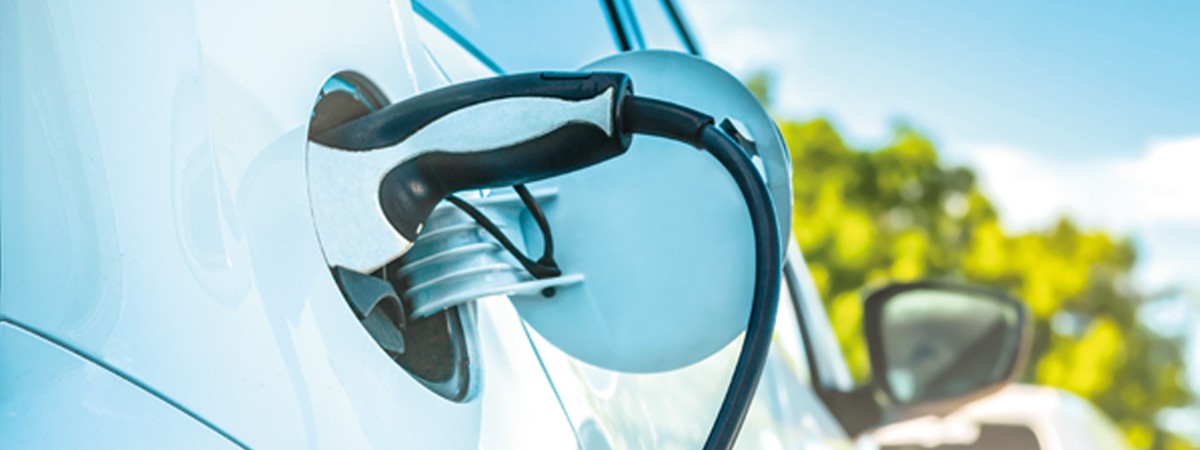
Vacuum essential for e-mobility
Many applications in battery production
Thinner than a hair
The electrodes of a Li-ion storage battery consist of extremely thin foils. In batteries, Lithium is used as an anode; rechargeable batteries use lithium metallic oxide as a cathode. The oxide is mixed with a binding agent and other additional materials into a homogeneous paste (slurry). It is evenly applied to aluminum foil in the coating machine. This process is similar to printing with an inkjet printer. Aluminum is the substrate and serves as a conductor that absorbs the charging current and then emits the stored electricity again. After the coating process, a roller system conveys the foil while simultaneously pressing it flat until the individual sheets become thinner than a hair. The thicker the coating and the thinner the electrode foil, the more capacity the battery has.
The electrodes of a Li-ion storage battery consist of extremely thin foils. In batteries, Lithium is used as an anode; rechargeable batteries use lithium metallic oxide as a cathode. The oxide is mixed with a binding agent and other additional materials into a homogeneous paste (slurry). It is evenly applied to aluminum foil in the coating machine. This process is similar to printing with an inkjet printer. Aluminum is the substrate and serves as a conductor that absorbs the charging current and then emits the stored electricity again. After the coating process, a roller system conveys the foil while simultaneously pressing it flat until the individual sheets become thinner than a hair. The thicker the coating and the thinner the electrode foil, the more capacity the battery has.