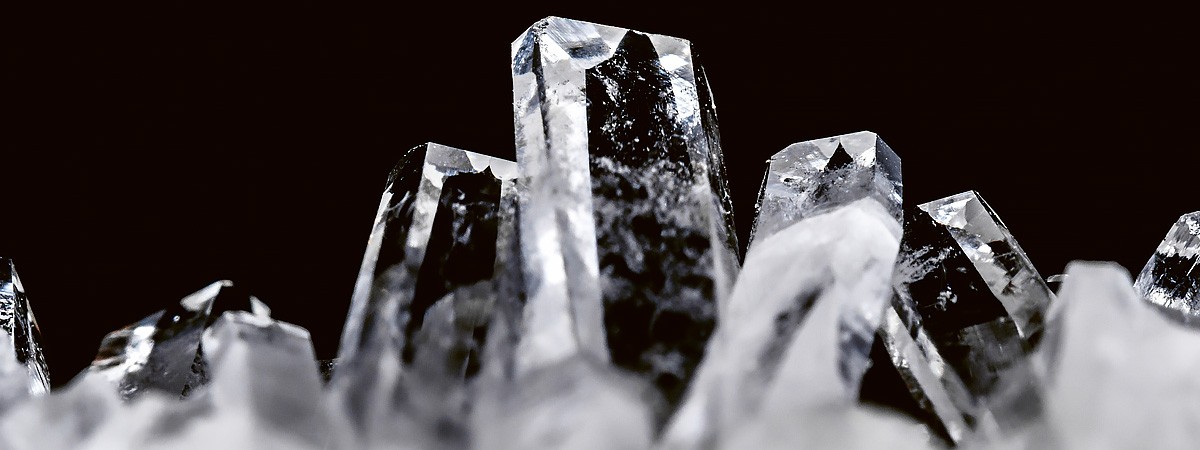
Creating the Brains of Today’s Technology
Ultra-pure silicon for microchips
As the second most abundant element in the Earth’s crust, silicon surrounds us. But in nature, it is only ever found combined with other elements – such as in sand, quartz, and other rocks. For a microchip, a pure crystal is needed. This can be formed under vacuum, using a vacuum pump from Busch.
Modern society relies heavily on microchips. They are the brains behind electronic devices and are most commonly used in the entertainment and automotive industries. But as we go ever further into the age of smart technology, microchips appear in the most unexpected places – kids’ toys, washing machines, even your passport.
One crystal made of many
The story of every microchip begins with polysilicon, a form of silicon made up of multiple small crystals. For the electronics industry, the silicon must be of ultra-high purity. This means typically between 99.999% and 99.999999999% – no more than one non-silicon atom per billion silicon atoms. To create a microchip, polysilicon must be transformed into one single crystal, called mono-crystalline silicon. This is critical for microchip production: The grain boundaries and irregularities in the crystal structure of polysilicon would otherwise affect the performance of the finished microchip. There are several methods of producing mono-crystalline silicon, the most common of which is the Czochralski method, growing a silicon crystal under vacuum.
Crystals from seed
Mono-crystalline silicon is produced using what is known as a puller. This name encompasses a variety of different technologies, with two key parts: a vacuum furnace and a mechanism that pulls the crystal into its form. Inside the chamber of the vacuum furnace, polysilicon is heated to extremely high temperatures of around 1410 °C. A small piece of mono-crystalline silicon, called a seed, is placed in the center and slowly drawn upwards while rotating. The seed pulls up the molten silicon with it, which solidifies as it rises. This creates a long, cylindrical rod of pure silicon. Molten silicon is highly reactive, so in order to maintain its high purity, it should not come into contact with ambient air. The air is therefore evacuated from the chamber using a vacuum pump from Busch. This results in a contaminant-free growing environment and the highest quality crystal, ready to continue its long journey through the semiconductor fab to becoming a microchip.
One crystal made of many
The story of every microchip begins with polysilicon, a form of silicon made up of multiple small crystals. For the electronics industry, the silicon must be of ultra-high purity. This means typically between 99.999% and 99.999999999% – no more than one non-silicon atom per billion silicon atoms. To create a microchip, polysilicon must be transformed into one single crystal, called mono-crystalline silicon. This is critical for microchip production: The grain boundaries and irregularities in the crystal structure of polysilicon would otherwise affect the performance of the finished microchip. There are several methods of producing mono-crystalline silicon, the most common of which is the Czochralski method, growing a silicon crystal under vacuum.
Crystals from seed
Mono-crystalline silicon is produced using what is known as a puller. This name encompasses a variety of different technologies, with two key parts: a vacuum furnace and a mechanism that pulls the crystal into its form. Inside the chamber of the vacuum furnace, polysilicon is heated to extremely high temperatures of around 1410 °C. A small piece of mono-crystalline silicon, called a seed, is placed in the center and slowly drawn upwards while rotating. The seed pulls up the molten silicon with it, which solidifies as it rises. This creates a long, cylindrical rod of pure silicon. Molten silicon is highly reactive, so in order to maintain its high purity, it should not come into contact with ambient air. The air is therefore evacuated from the chamber using a vacuum pump from Busch. This results in a contaminant-free growing environment and the highest quality crystal, ready to continue its long journey through the semiconductor fab to becoming a microchip.
The cleanest places on Earth
In the natural world, there’s no such thing as truly clean air. We’re reminded of this on sunny days, when we suddenly notice the dust dancing around us in a sunbeam. In fact, the average office has up to 3,500,000,000 tiny particles – some invisible to the naked eye – in every cubic meter of air. But in certain manufacturing processes, such as the aerospace, semiconductor, and pharmaceutical industries, this otherwise normal part of life can lead to products becoming contaminated. Clean rooms are therefore essential. The most stringent allow just 10 miniscule particles of ≥ 0.1μm per cubic meter: the rough equivalent of a single sesame seed in an Olympic swimming pool.
Facilities use a variety of methods to keep their clean rooms free of contaminants. These vary from protective suits and masks to air showers, where workers are blasted with air to remove lingering particles. In a semiconductor fab, even perfumes, makeup, and hair products are no-go, as even the tiniest particle can ruin a batch of wafers.
So, if you’re really in need of fresh air, forget a stroll in the countryside. The cleanest air on our planet can be found inside a clean room.
In the natural world, there’s no such thing as truly clean air. We’re reminded of this on sunny days, when we suddenly notice the dust dancing around us in a sunbeam. In fact, the average office has up to 3,500,000,000 tiny particles – some invisible to the naked eye – in every cubic meter of air. But in certain manufacturing processes, such as the aerospace, semiconductor, and pharmaceutical industries, this otherwise normal part of life can lead to products becoming contaminated. Clean rooms are therefore essential. The most stringent allow just 10 miniscule particles of ≥ 0.1μm per cubic meter: the rough equivalent of a single sesame seed in an Olympic swimming pool.
Facilities use a variety of methods to keep their clean rooms free of contaminants. These vary from protective suits and masks to air showers, where workers are blasted with air to remove lingering particles. In a semiconductor fab, even perfumes, makeup, and hair products are no-go, as even the tiniest particle can ruin a batch of wafers.
So, if you’re really in need of fresh air, forget a stroll in the countryside. The cleanest air on our planet can be found inside a clean room.