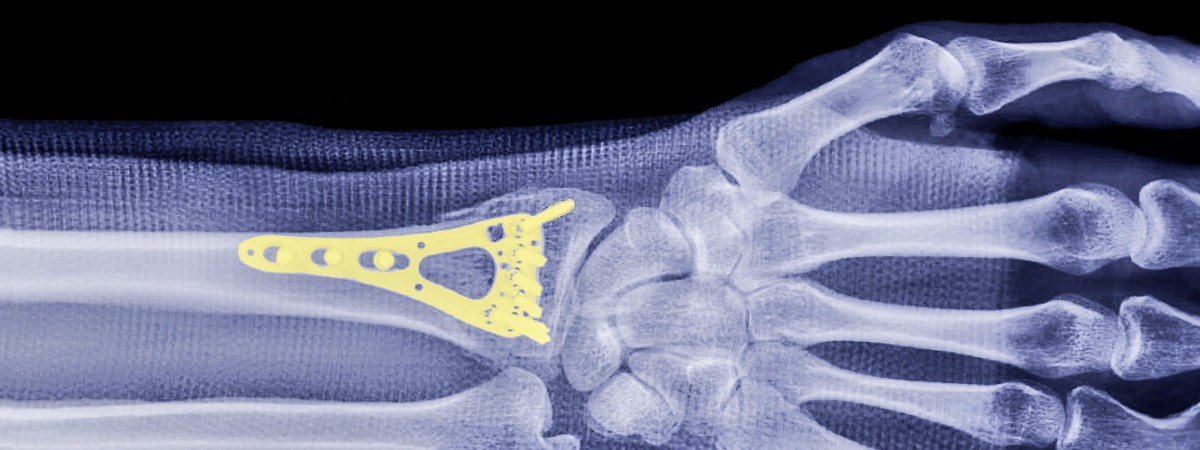
New Joints Fresh from the Press
Tailor-made under vacuum
It’s not just small plastic pieces that can be 3D printed. Advancements in additive manufacturing mean different shapes can be created from a variety of raw materials. Now, 3D printing produces custom-fit orthopedic implants for patients with the help of a vacuum pump from the Busch Group.
In the past, a patient waiting for a medical implant had two options: a generic piece from a catalogue, or an extremely long wait for a custom fit. 3D printing allows the best of both: an anatomically accurate implant and a short time to surgery. The improved fit also means less discomfort during recovery and a lower chance of needing follow-up operations.
A printed implant
Every human body is different. So creating an implant using traditional metalworking techniques could take weeks of laborious shaping, milling and grinding to get the complex anatomical form just right – and may require multiple parts. With 3D printing the process is less labor intensive. The implant is mapped out in a design program, which divides it into hundreds, or even thousands, of small slices. The 3D printer then “prints” each individual slice, one on top of the other – a process that creates just one piece and can be completed in a matter of days.Focused under vacuum
Metal implants are created by electron beam melting (EBM) under vacuum. First, a vacuum pump from Busch removes all the air from the build chamber. Then, a tungsten wire is heated to 2,500°C, which causes it to emit electrons. These are focused into a beam and projected onto a bed of powdered metal, usually titanium or cobalt-chrome. The electron beam heats up and fuses the particles of powder that it comes into contact with, tracing the shape provided by the design program. This creates a thin layer of metal on the bed of the powder container – the bottom layer of the 3D object. The container is then lowered, along with what has been printed so far, more powder is added, and the next layer is fused on top of the first. This process repeats until the final layer – and the implant – is complete. EBM is carried out under vacuum for three different reasons. Firstly, for precision. If other gas molecules are present, the electron beam can collide with them and deflect, resulting in the wrong metal particles fusing. This can have a big impact on the accuracy of the final product. Vacuum also ensures a homogenous material: As there is no air in the chamber, bubbles cannot form in the melted metal. Finally, the lack of oxygen means that the metal does not oxidize when it is heated. This means that any leftover powder can be reused for the next printing process.
A transplant with no donor
Printing with living cells sounds like something from a science fiction movie, but bioprinting human tissue is the next step in medical advancements. Using “bio-ink,” a combination of human cells and various biocompatible materials, tissue-like 3D structures can be printed. This could be comparatively simpler tissues like skin, or more complex structures like internal organs. This development would allow for organ transplants to be made from the recipient’s own tissue – with no donor necessary, and no chance of rejection. It would also have applications in drug testing and disease modelling. This is a complex process with some ethical considerations, but it has the potential to revolutionize healthcare in the future.
Printing with living cells sounds like something from a science fiction movie, but bioprinting human tissue is the next step in medical advancements. Using “bio-ink,” a combination of human cells and various biocompatible materials, tissue-like 3D structures can be printed. This could be comparatively simpler tissues like skin, or more complex structures like internal organs. This development would allow for organ transplants to be made from the recipient’s own tissue – with no donor necessary, and no chance of rejection. It would also have applications in drug testing and disease modelling. This is a complex process with some ethical considerations, but it has the potential to revolutionize healthcare in the future.