Mixing, shaping, and firing are the three main stages of brickmaking. But there is one more crucial step in the process: Degassing. Mixing adds tiny pockets of air to the clay that need to be removed to ensure a solid, stable brick. Vacuum pumps from Busch deliver the necessary vacuum for the degassing process.
It is just like baking. When you stir in each new ingredient, you also add small air bubbles. Bubbles create a beautifully light and airy dough, but need to be kept in check during brickmaking. The goal is a strong product that will last – and in a brick, air bubbles can have the opposite effect. During shaping and pressing, air pockets meet and combine, creating a void that weakens the brick’s structure. Even smaller bubbles can be a problem: A porous brick can warp and lose its shape at high temperatures. To avoid this, the clay needs to be solid and non-porous when it enters the kiln to be fired, making a strong, durable brick with no hidden voids.
Pressing out the air
To get the clay ready to be shaped and fired, these air bubbles need to be removed in a process called degassing. After mixing, it is sent through a vacuum chamber. This change in pressure causes the bubbles to rise to the top of the clay mixture. They break through the surface and are extracted. If there is any excess water in the mixture, it is also squeezed out and removed in the same way. This leaves just the clay compound, now free of air and at the right moisture level for the next stage of the process. Busch has suitable vacuum solutions to be used during this degassing process.
Porosity for insulation
Certain types of brick, however, benefit from a bit of extra air inside. Small pockets of air act as insulation, helping the bricks retain heat and keep buildings warm. However, instead of relying on unpredictable air bubbles, brickmakers have a way of creating porosity on their own terms. Additional materials such as sawdust, paper pulp, or polystyrene are added to the clay mixture. As tiny solids mixed into the clay, they pass through the degassing process unscathed. But they cannot withstand the intense heat of firing and burn away in the kiln, leaving behind tiny, evenly distributed air pockets in the finished brick.
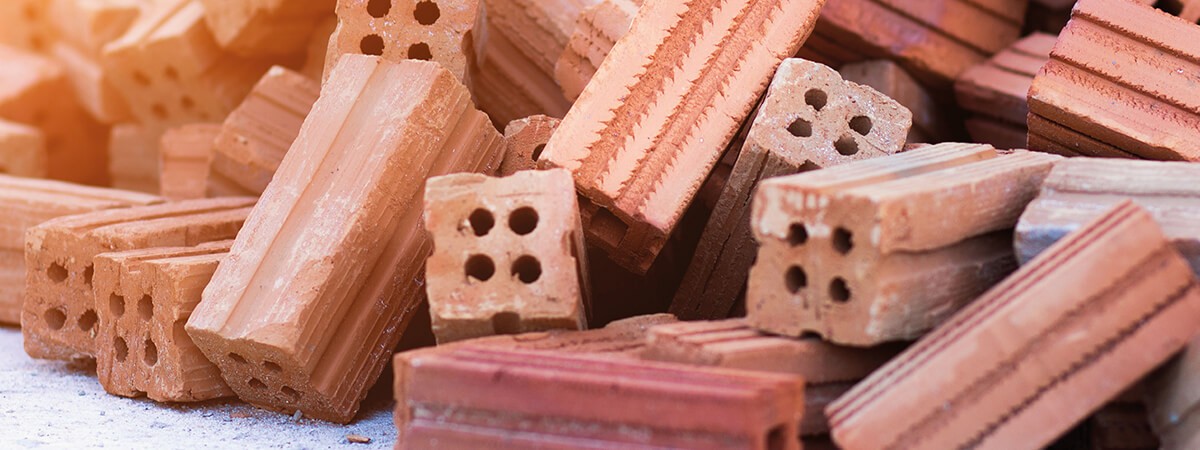
Bricks Without Bubbles
Clay compounds degassed under vacuum
From raw clay to hard brick
Bricks need to withstand any conditions the elements can throw at them: Fluctuating temperatures, different humidity levels, and any other weather typical of the area. Raw clay is very malleable, making shaping easy, but when it dries, it becomes brittle and weak. Another stage in the process is needed to make a brick suitable for building: Firing. In a kiln, the bricks are exposed to increasing temperatures. At the lower temperatures, the clay brick loses any residual water content, and any additional materials – such as those added to create porosity – will burn off. As the mercury climbs, the chemical process begins and the clay’s internal structure changes. The brick changes color and it gets harder and more durable. When the kiln reaches its top temperature – over 1,000 °C – vitrification begins. The extreme temperature causes the clay to partially melt into a glass-like material, which binds the different elements of the brick and creates a strong and hard-wearing product.
Bricks need to withstand any conditions the elements can throw at them: Fluctuating temperatures, different humidity levels, and any other weather typical of the area. Raw clay is very malleable, making shaping easy, but when it dries, it becomes brittle and weak. Another stage in the process is needed to make a brick suitable for building: Firing. In a kiln, the bricks are exposed to increasing temperatures. At the lower temperatures, the clay brick loses any residual water content, and any additional materials – such as those added to create porosity – will burn off. As the mercury climbs, the chemical process begins and the clay’s internal structure changes. The brick changes color and it gets harder and more durable. When the kiln reaches its top temperature – over 1,000 °C – vitrification begins. The extreme temperature causes the clay to partially melt into a glass-like material, which binds the different elements of the brick and creates a strong and hard-wearing product.