A continuous process for the production of lightweight panels is opening up new opportunities – and not just for urban paddling. Vacuum plays an important role in shaping the elements.
The streets are clogged, the subway and commuter trains are jam-packed – at rush hour in cities like Amsterdam, Austin and Macao, people are looking to the rarely used waterways: if only I had a boat right now! And recently, they have been able to achieve this dream relatively easily and at an affordable price. The Belgian company Onak has developed a canoe that is made primarily from a single plastic panel. This can be folded together to create a trolley the size of a medium-sized suitcase that can then be transported. Once unfolded, it transforms into a fully fledged boat in just a few minutes.
Honeycomb structures provide more support
The secret to this innovative boat is its material, a sandwich panel with a honeycomb core made from polypropylene (PP). As the name suggests, its interior is reminiscent of a beehive. The walls of the hexagons provide structure, while the large number of cavities between the cells and the outer layers make the panel exceptionally light.
And it is precisely these properties that have led to similar panels being used in the racing and aerospace industries for years. However, the conventional production process is rather complicated because the outer layers and interior are produced separately and then joined together panel by panel.
A little while ago, Dr. Jochen Pflug from Leuven University developed a technique for producing these honeycomb panels in a single step in one continuous process. He then founded the companies EconCore and ThermHex to license the technology and use it to produce endless panels respectively.
Forms and folds
During the thermoplastic production of the honeycomb core, a flat sheet die directs the malleable plastic straight from the extruder onto a rotary vacuum deep drawing drum. The name reflects the operating principle: the surface of the drum is designed to create the walls for one half of the honeycomb cells. The vacuum inside the drum draws the hot material through a large number of holes on the surface and into the corresponding mold. The rotary mechanism allows for continuous output.
As part of a sophisticated process, the two halves of the honeycomb are then folded and joined together to create a full honeycomb cell. During the same run, different outer layers can now be laminated on top. These layers can be made from plastic, sheet metal or fiber-reinforced organo sheets. The latter can be deformed at a later stage and made into functional units such as eyes, handles or brackets using injection molding technology. The honeycomb core panels are used for anything that calls for flat, stable lightweight elements. As well as canoes for urban paddling – which could be the next big trend – they could also be used for the hulks of large yachts, trailers for trucks, vehicle body components, residential construction, or nacelles for wind turbines.
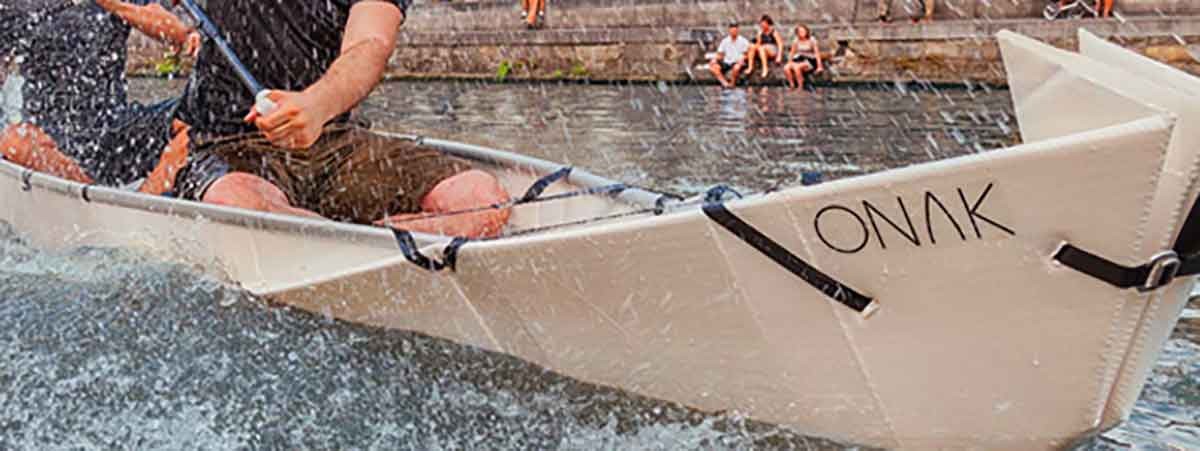
An Endless Run of Lightweight Panels
Vacuum supports continuous production processes
Why honeycomb?
Nature has a tendency to be economical. That is why surfaces are often circles and bodies are often spheres – as much content as possible with a minimum on the outside. When lots of circles are arranged next to one another, the inevitable gaps are eliminated: the circle then becomes a hexagon and the sphere becomes a honeycomb. We cannot be certain how bees know that this structure is the most economical in mathematical terms and how they reliably form exact 120-degree angles when building their hives. One thing that is certain is that these insects create the most stable three-dimensional structure feasible with their "technology" while using as little wax as possible. Humans have adopted this pattern in structural bionics and use it for countless static elements.
Nature has a tendency to be economical. That is why surfaces are often circles and bodies are often spheres – as much content as possible with a minimum on the outside. When lots of circles are arranged next to one another, the inevitable gaps are eliminated: the circle then becomes a hexagon and the sphere becomes a honeycomb. We cannot be certain how bees know that this structure is the most economical in mathematical terms and how they reliably form exact 120-degree angles when building their hives. One thing that is certain is that these insects create the most stable three-dimensional structure feasible with their "technology" while using as little wax as possible. Humans have adopted this pattern in structural bionics and use it for countless static elements.