Vacuum pumps generally achieve more constant vacuum levels, making them the preferred choice for many industrial applications requiring a consistent vacuum supply like in vacuum drying.
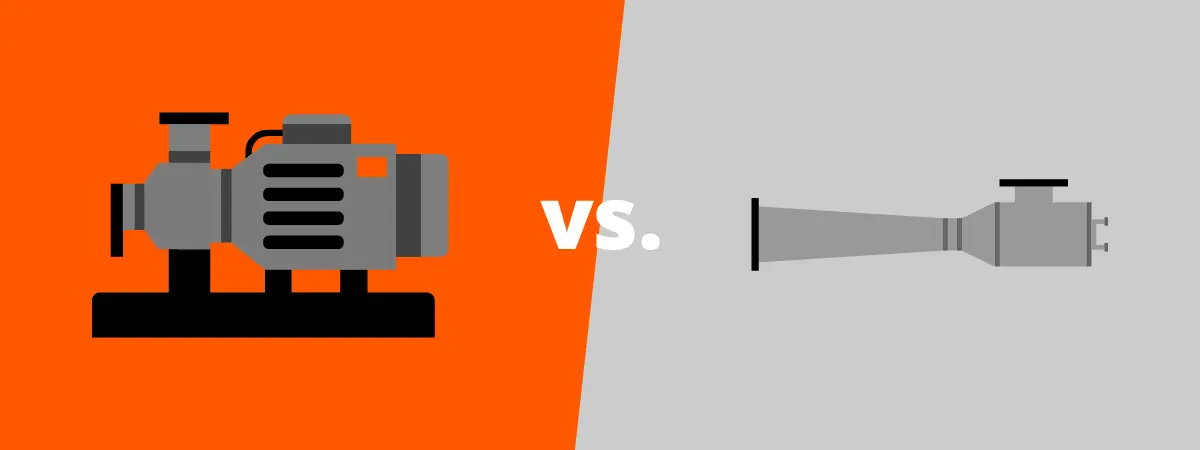
Vacuum Pumps vs. Vacuum Ejectors
Explore the differences between vacuum pumps and vacuum ejectors, and discover why vacuum pumps are the better choice for achieving optimal vacuum performance, efficiency, and long-term value in your operations.
Vacuum pumps generally achieve more constant vacuum levels, making them the preferred choice for many industrial applications requiring a consistent vacuum supply like in vacuum drying.
How vacuum ejectors work
Vacuum ejectors use compressed air or steam as a motive to generate vacuum. While they can be categorized by the type of motive used, their operation relies universally on Bernoulli’s principle. This principle states that when a fluid moves faster, its pressure decreases. Consequently, when the pressure is high, the fluid moves slowly.In a vacuum ejector, a high-pressure stream from an air compressor or steam generator is forced through a nozzle. As the nozzle narrows, the air speeds up to pass through the smaller space – just like water flows faster when you pinch the end of a garden hose. This happens because the same amount of air has to pass through, even though the space is smaller.
Following Bernoulli’s principle, this acceleration leads to a decrease in pressure, creating an area of low pressure around the throat section of the nozzle. Since gases naturally flow from areas of higher pressure to areas of lower pressure, the differential pressure around the nozzle draws in gas from the evacuation chamber through the inlet. This flow effectively evacuates the chamber, generating vacuum. The high-pressure stream then entrains and mixes with the gas from the chamber. During mixing, the energy of the high-pressure stream is transferred to the entrained gas, propelling the mixture forward. Finally, it is expelled through the discharge.
Multi-stage steam ejectors
Steam ejectors can range from single-stage units to multi-stage configurations, with the number of necessary ejector stages determined by the required vacuum level. This means that the higher the required vacuum has to be, the more ejector stages are needed.A multi-stage steam ejector is a system of multiple ejectors connected in series. It can achieve higher vacuum levels by progressively lowering the pressure at each stage. As pressure is reduced, the gas molecules spread out more and the density of the gas decreases. This means higher vacuum can be achieved. In this configuration, the motive steam and evacuated gas mixture exiting one stage is collected in a condenser, reducing the gas volume to be handled in the next stage.
Differences in application
Vacuum ejectors and vacuum pumps differ in both operating principle and applications. Vacuum ejectors are low-cost and easy to install. They are typically integrated into machines for tasks like pick and place. Since ejectors generate vacuum using compressed air, they are often chosen when the process already requires compressed air for other steps.Although the initial costs of vacuum ejectors are lower than those of a vacuum pump, ejectors consume a significant amount of compressed air or steam, resulting in higher operating costs over time. This makes vacuum pumps the more efficient choice, saving energy expenses. For this reason, the initial higher investment in a vacuum pump will be returned after a short period of time.
Moreover, the vacuum level that vacuum ejectors can achieve is limited. For medium and high vacuum applications, such as freeze-drying fruits and vegetables, vacuum pumps are required. Overall, vacuum pumps are more versatile since they can cover a wider range of vacuum levels, from rough to high vacuum. Due to the different vacuum pump types available, it is possible to easily find the right match for a specific application.
Advantages of vacuum pumps
Energy efficiency and operating costs
Steam ejectors use pressurized steam to generate vacuum. To create the steam, water is evaporated in a boiler. This process requires significant energy for heating and large quantities of water. Some of this heat is released into the environment around the ejector, ultimately leading to inefficient operation, heat loss, and higher operating costs. Vacuum pumps operate at lower temperatures and do not require additional heat or water supply. This saves costs and reduces the overall power consumption of the vacuum pump, making it the more energy-efficient choice.In a multi-stage steam ejector system, the last stage requires the most energy to generate the ultimate pressure. Significant savings can be realized by replacing this final ejector with a liquid ring vacuum pump, creating a hybrid system. The efficient operation of the liquid ring vacuum pump helps to reduce power consumption. However, replacing all steam ejectors in a vacuum system with vacuum pumps remains the best solution to reduce both power usage and operating costs.
Additionally, vacuum pumps from Busch can be equipped with ECOTORQUE, the variable speed drive (VSD) from Busch. With the VSD, the rotational speed of the vacuum pump can be precisely adjusted to the process demand so that only the necessary amount of energy is consumed. This makes vacuum pumps from Busch the ideal choice for all industries that want to save operating costs.
Environmental impact
Directly related to the topic of efficiency is environmental impact. Heat for steam generation requires energy. If that energy comes from non-renewable sources such as coal or natural gas, it adds to the carbon footprint.In addition, steam creates another problem. In multi-stage ejectors, the steam and process gas mixture is collected in a condenser to reduce the volume of gas to be handled in the next ejector stage. In the condenser, the steam cools down and condenses to water as it releases heat to the environment. This water, or condensate, is now discharged from the system. However, it often contains contaminants that it has absorbed from the process gas, resulting in large volumes of polluted water. The collection and treatment of this wastewater further increases operating costs and – when not treated correctly – results in environmental pollution.
To ensure a completely clean vacuum supply, vacuum can be generated with COBRA dry screw vacuum pumps from Busch. These vacuum pumps do not require oil in the compression chamber.
Customization
In contrast to vacuum ejectors, vacuum pumps are suitable for a wide range of applications and can be used in various industries, including those requiring high vacuum or operating with multiple gas types. Additionally, centralization of vacuum supply is possible, providing enhanced process control and efficiency. Busch offers turnkey vacuum systems that can be tailored to meet the unique needs of different industries. These are built in local systems building centers and can be installed in a separate room at the costumer’s site. Local experts from Busch connect it to the production process by integrating the necessary piping and ductwork. Supplying vacuum from a separate equipment room entails a range of advantages like reduced noise levels, space optimization, or improved air quality in the production areas.Moreover, Busch vacuum pumps are available in different design options, including special corrosion-resistant coatings (Aqua) and ATEX versions for use in potentially explosive areas. This extensive portfolio ensures that vacuum pumps can be selected for a wide range of applications and environments.
Noise levels
The constant stream of pressurized steam or air in vacuum ejectors generates high sound pressure levels due to its velocity. This means that during the evacuation process, ejectors can be 16 times louder than vacuum pumps. This can be problematic in environments where it is vital to control sound pressure levels and avoid high vibration. Reducing this sound pressure level of vacuum ejectors requires extensive measures like incorporating silencers.Vacuum pumps from Busch operate more quietly, contributing to a better working environment by reducing noise.
FAQ
Why are vacuum pumps more efficient than vacuum ejectors?
Vacuum pumps are generally more efficient than vacuum ejectors due to their operating principle and energy usage. Unlike ejectors, which rely on a continuous supply of pressurized steam or compressed air, vacuum pumps use moving parts like claws or screws to evacuate air and gases from a sealed environment. This mechanical process allows precise control over the vacuum level, reducing energy losses, saving operating costs, and optimizing efficiency. Vacuum pumps also consume less energy since they do not require heat or water for steam creation. Moreover, they can generate higher vacuum levels for applications like freeze-drying.
How does a vacuum ejector work?
Vacuum ejectors use compressed air or steam as a motive fluid to generate vacuum using Bernoulli's principle. While we often think of fluids as liquids, air is also considered a fluid because it flows similarly. According to Bernoulli, when a fluid moves faster, its pressure decreases. Conversely, high pressure corresponds to slower flow.
In a vacuum ejector, a high-pressure stream is forced through a narrowing nozzle, causing the air to accelerate, much like water speeds up when you pinch a hose. This acceleration reduces pressure at the throat of the nozzle, the narrowest point, creating a low-pressure area. Gases flow from the evacuation chamber with higher pressure into the inlet, effectively generating vacuum inside the chamber. The high-pressure stream mixes with the entrained gas, transferring energy and propelling the mixture forward, which is then expelled through the outlet.
What is the difference between a vacuum pump and a vacuum ejector?
Vacuum pumps remove air or other gases from a sealed environment to generate vacuum. They use moving parts such as vanes, claws, or screws to trap, compress and expel gas. Vacuum pumps are versatile, offering precise control over vacuum levels, and are commonly used in various industries, such as chemical and pharmaceutical, research and development, and electronics. Vacuum ejectors, on the other hand, do not have moving parts and instead use high-pressure streams to generate vacuum. For applications requiring higher vacuum levels, multiple ejectors can be staged to progressively lower the pressure. Steam ejectors are often used for pick-and-place applications inside processes that already use compressed air.
What is the difference between a steam ejector and a steam jet ejector?
The terms steam ejector and steam jet ejector are often used interchangeably and refer essentially to the same device. The term “jet” highlights the rapid movement of steam, which is crucial for efficiently entraining other gases.
What is the difference between a steam ejector and a vacuum ejector?
A vacuum ejector uses a high-pressure stream to generate vacuum. This high-pressure stream, or motive, can be either steam or compressed air. A steam ejector, therefore, is a specific type of vacuum ejector that relies on steam to operate. A venturi, also known as air-powered ejector, on the other hand, uses compressed air.
How do I select the right vacuum solution for my process?
Several factors must be considered when selecting the right vacuum solution. These factors vary depending on the application and the specific needs of your process.
Use our product finder to find your ideal vacuum pump. Or contact us to find out which vacuum solution fits your needs best. Our Busch experts are happy to help!