Antipasti und Feinkostprodukte sind seit über hundert Jahren die Spezialität von Feinkost Dittmann. Am Produktionsstandort Taunusstein werden verschiedenen Produkte hergestellt und als Konserven in Gläser oder als Frischeprodukte in Kunststoffschalen verpackt. Die Vakuumversorgung der Verpackungsmaschinen erfolgt seit über einem Jahr mit einer Vakuumzentralanlage von Busch, die erheblich wirtschaftlicher arbeitet als die zuvor eingesetzte Vakuumtechnik. Alleine der Energieverbrauch konnte um mehr als 70 Prozent reduziert werden.
In der sogenannten „Frische-Abteilung" im Produktionsbetrieb in Taunusstein werden die Produkte in Kunststoffschalen (Trays) verpackt. Dabei wird die Luft aus den Verpackungsschalen gesaugt, bevor ein CO2N2-Gasgemisch als Schutzgas in die Verpackungen eingebracht wird. Anschließend wird die Verpackung mit einer Kunststofffolie gasdicht versiegelt und zusätzlich mit einem Kunststoffdeckel verschlossen. Diese Verpackungsart stellt sicher, dass der Sauerstoffgehalt durch das Absaugen der Luft und das Einbringen des Schutzgases in die Verpackung garantiert unter einem Prozent liegt. Die Haltbarkeit der Produkte wird dadurch massiv erhöht. Außerdem ist die Produktpräsentation in der Klarsichtverpackung optimal, weil keine Folie direkt auf den Produkten anliegt oder diese vielleicht sogar durch den in der Verpackung herrschenden Unterduck zerdrücken würde.
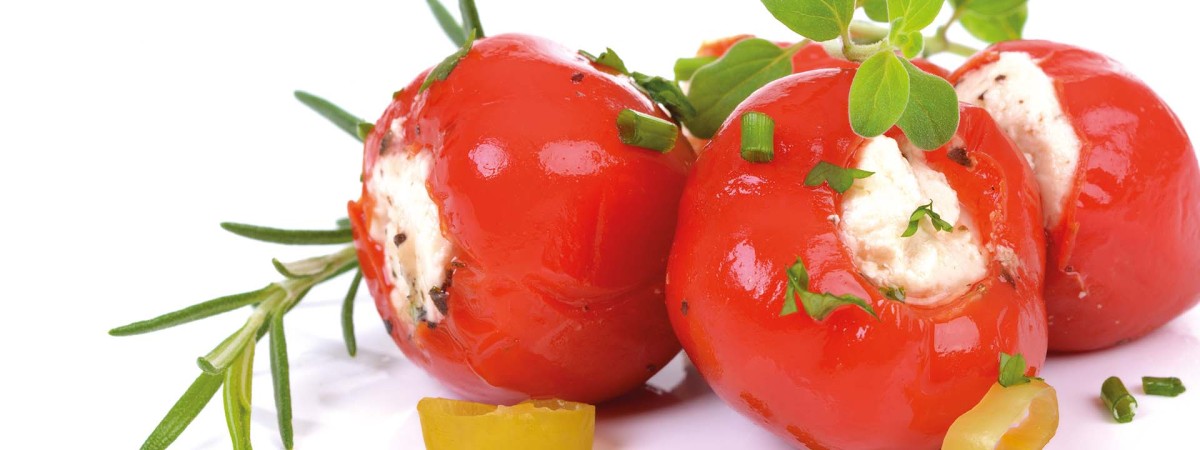
Quelle: © www.istockphoto.com - kabVisio.
70 % weniger Energieverbrauch - Effiziente Anwendung von Vakuumtechnik bei der Lebensmittelverpackung
Feinkost Dittmann
-
Quelle: Busch Vacuum Solutions.
Insgesamt wird an vier Verpackungsmaschinen (Tray Sealer) im Zwei-Schicht-Betrieb verpackt. Das dazu notwendige Vakuum wurde von sechs ölgeschmierten Drehschieber-Vakuumpumpen mit je 5,5 Kilowatt Antriebsleitung erzeugt. Ursprünglich waren diese direkt an den Verpackungsmaschinen installiert. Aus hygienischen Gründen und um die Wärmebelastung in den Produktionsräumen zu senken, wurden diese Vakuumpumpen später in einen separaten Raum über der Produktion untergebracht und mit einem Rohrleitungsnetz an die Verpackungsmaschinen angeschlossen. Mit dieser Lösung war Andreas Lutz als technischer Projektleiter im Produktionswerk nicht wirklich glücklich, denn die Vakuumpumpen erforderten weiterhin einen hohen Wartungsaufwand. Außerdem wurden Schwankungen oder Störungen im Vakuumnetz erst dann bemerkt, wenn eine der Verpackungsmaschinen eine Fehlermeldung gab und automatisch abschaltete, wenn das Vakuumniveau nicht schnell genug oder gar nicht erreicht wurde. Dies führte immer wieder zu Produktionsstillständen an einzelnen Verpackungslinien.
2013 kontaktierte Andreas Lutz die Vakuumspezialisten von Busch, deren Aufgabe es war, eine betriebssichere und wirtschaftlichere Lösung anzubieten. Dabei sollte das vorhandene Rohrleitungsnetz weiter benutzt werden. Außerdem sollte die Vakuumversorgung so ausgelegt werden, dass bei einer Vergrößerung der Produktionskapazität weitere Verpackungsmaschinen angeschlossen werden können. Busch analysierte detailliert die örtlichen Begebenheiten und alle technischen Parameter und arbeitete eng mit dem Projektleiter von Dittmann und dem hauseigenen Labor zusammen. Das Ergebnis dieser Analyse und einer ausführlichen Beratung war eine Vakuumzentralanlage mit vier Mink Klauen-Vakuumpumpen.
-
Vakuumzentralanlage mit Mink Klauen-Vakuumpumpen von Busch
Diese haben den grundsätzlichen Vorteil, dass sie keine Betriebsmittel wie Öl im Verdichtungsraum benötigen. Damit entfallen alle Wartungsarbeiten im Zusammenhang mit Öl wie Ölkontrolle, Ölwechsel, Ölfilterwechsel sowie die Kosten zur Beschaffung und Entsorgung von Ölen und Filtern. Außerdem arbeiten Mink Klauen-Vakuumpumpen völlig berührungsfrei. Das heißt, es gibt im Verdichtungsraum keine Teile, die sich mechanisch berühren und somit verschleißen. Damit entfällt auch der Austausch von Verschleißteilen und die damit verbundenen Arbeitszeiten und -kosten. Die berührungsfreie Arbeitsweise der Klauen-Vakuumtechnologie ermöglicht außerdem einen hohen Wirkungsgrad und damit verbunden, eine kleinere Antriebsleitung als herkömmliche Vakuumpumpen.
Diese Vakuumzentrale wurde Ende 2013 installiert. Den Mink Klauen-Vakuumpumpen sind drei Vakuumbehälter mit je 3.000 Liter Volumen vorgeschaltet. Somit ist sichergestellt, dass sofort ein ausreichendes Vakuumniveau direkt an der Maschine ansteht, wenn dieses benötigt wird.
Während zuvor alle sechs Drehschieber-Vakuumpumpen durchschnittlich 15 Stunden pro Tag in Betrieb waren, sind die Mink Vakuumpumpen in der neuen Zentralanlage so gesteuert, dass nur so viele laufen, wie für den momentan tatsächlichen Vakuumbedarf notwendig sind.
Zwei der Vakuumpumpen mit Standardmotoren tragen die sogenannte Grundlast. Die anderen zwei Vakuumpumpen sind frequenzgeregelt und sorgen durch die Anpassung ihrer Drehzahl für die Feinregelung des Vakuumbedarfs. Mit dieser intelligenten Lösung passt sich die Saugleistung der Vakuumzentralanlage exakt an den aktuellen Bedarf an.
Durch diese Regelung werden die tatsächlichen Betriebszeiten der einzelnen Vakuumpumpen drastisch reduziert, weil bei normalem Betrieb nie alle vier Vakuumpumpen unter Volllast arbeiten. Die Vakuumzentralanlage von Feinkost Dittmann hat also noch genügend Leistungsreserven, um weitere Verpackungsmaschinen anzuschließen. Es ist geplant, einen Vakuumfüller für Glaskonserven zusätzlich anzuschließen, was die jetzt dort dezentral installierte Flüssigkeitsring-Vakuumpumpe mit 7,5-Kilowatt-Antriebsmotor überflüssig macht und somit eine weitere Energieeinsparung mit sich bringt.
Nach über zwei Jahren Betriebszeit kann Projektleiter Andreas Lutz eine überaus positive Bilanz ziehen:
Die Wartung der neuen Vakuumzentralanlage erfolgt durch die Servicetechniker von Busch. Diese beschränkt sich allerdings auf eine jährliche Messung von Enddruck und Stromaufnahme an jeder einzelnen Vakuumpumpe sowie den Wechsel der vorgeschalteten Partikelfilter und einem Getriebeölwechsel.
Diese Vakuumzentrale wurde Ende 2013 installiert. Den Mink Klauen-Vakuumpumpen sind drei Vakuumbehälter mit je 3.000 Liter Volumen vorgeschaltet. Somit ist sichergestellt, dass sofort ein ausreichendes Vakuumniveau direkt an der Maschine ansteht, wenn dieses benötigt wird.
Während zuvor alle sechs Drehschieber-Vakuumpumpen durchschnittlich 15 Stunden pro Tag in Betrieb waren, sind die Mink Vakuumpumpen in der neuen Zentralanlage so gesteuert, dass nur so viele laufen, wie für den momentan tatsächlichen Vakuumbedarf notwendig sind.
Zwei der Vakuumpumpen mit Standardmotoren tragen die sogenannte Grundlast. Die anderen zwei Vakuumpumpen sind frequenzgeregelt und sorgen durch die Anpassung ihrer Drehzahl für die Feinregelung des Vakuumbedarfs. Mit dieser intelligenten Lösung passt sich die Saugleistung der Vakuumzentralanlage exakt an den aktuellen Bedarf an.
Durch diese Regelung werden die tatsächlichen Betriebszeiten der einzelnen Vakuumpumpen drastisch reduziert, weil bei normalem Betrieb nie alle vier Vakuumpumpen unter Volllast arbeiten. Die Vakuumzentralanlage von Feinkost Dittmann hat also noch genügend Leistungsreserven, um weitere Verpackungsmaschinen anzuschließen. Es ist geplant, einen Vakuumfüller für Glaskonserven zusätzlich anzuschließen, was die jetzt dort dezentral installierte Flüssigkeitsring-Vakuumpumpe mit 7,5-Kilowatt-Antriebsmotor überflüssig macht und somit eine weitere Energieeinsparung mit sich bringt.
Nach über zwei Jahren Betriebszeit kann Projektleiter Andreas Lutz eine überaus positive Bilanz ziehen:
- Senkung des Energiebedarfs um mehr als 70 Prozent
- Drastische Reduzierung der Wartungsarbeiten
- Erhöhung der Betriebssicherheit
- Keinerlei Störungen oder Ausfälle
Die Wartung der neuen Vakuumzentralanlage erfolgt durch die Servicetechniker von Busch. Diese beschränkt sich allerdings auf eine jährliche Messung von Enddruck und Stromaufnahme an jeder einzelnen Vakuumpumpe sowie den Wechsel der vorgeschalteten Partikelfilter und einem Getriebeölwechsel.
Über Feinkost Dittmann
Die Anfänge von Feinkost Dittmann (Reichold Feinkost GmbH) gehen zurück bis in das Jahr 1901 als Carl Dittmann in Wiesbaden ein Feinkostgeschäft eröffnete. Heute ist Feinkost Dittmann deutscher Marktführer bei Oliven, Antipasti, Kapern, Knoblauch- sowie Sardellenspezialitäten und die beliebteste Feinkost-Marke des deutschen Handels. Das familiengeführte Unternehmen hat seinen Hauptsitz in Diez bei Limburg an der Lahn. In Taunusstein bei Wiesbaden steht das deutsche Produktionswerk, in dem insgesamt 320 Mitarbeiter verschiedene Antipasti-Spezialitäten beispielsweise aus Oliven, Feta, Knoblauch, Paprika oder getrockneten Tomaten sowie viele weitere Feinkostartikel produzieren. Diese gehen dann, unter verschiedenen eigenen Markennamen an nationale und internationale Einzelhandelsketten und Discounter. Aktuell exportiert das Familienunternehmen seine vielfältigen Spezialitäten in weltweit über 30 Länder. In Spanien, Griechenland und der Türkei produziert Feinkost Dittmann ebenfalls in eigenen Betrieben Feinkostprodukte.-
Produktionsbetrieb von Feinkost Dittmann in Taunusstein