Racerbiler skal være lette, hurtige og nemme at håndtere, men de skal være robuste nok til at lave snævre sving ved høj hastighed uden at komme uden for banen. Kulfiberforstærkede materialer bruges til at skabe et karrosseri, der er fem gange lettere end stål, men op til ti gange stærkere. Dette materiale med exceptionelle egenskaber er fremstillet ved hjælp af vakuumløsninger fra Busch.
Hvert år konkurrerer dygtige studerende fra tekniske universiteter over hele verden om at skabe en ny racerbilsprototype, der ikke er designet til Formel 1-racerbanen, men til amatør-racerkørere. Professionelt eller ej, det er ingen overraskelse, at det valgte materiale i højhastighedsverdenen i Formel 1 også er populært i denne konkurrence, hvor mange studerende vælger kulfiberforstærkede løsninger frem for metal. Kulfiber er hårdt – men ikke noget, du kan lave en bil af. Det er kraften i et kompositmateriale, der giver det dets unikke og vindende egenskaber.
Synergien i et kompositmateriale
Kombination af egenskaberne af harpiks og kulfiber skaber et langt stærkere materiale end hver af de to dele alene, hvilket giver en løsning, der kan klare udfordringerne med høje hastigheder og stærke kræfter. Slutmaterialet er så holdbart, at det kan bruges til stort set alle synlige dele af racerbilen. Hvad der ender som én del, begynder som mange. Stykker af harpikstilført kulfiberstof skæres ud efter et mønster, ligesom en skrædder ville skære stykker af stof ud til et jakkesæt. Disse lægges derefter sammen for at skabe den nødvendige tykkelse. Der bruges omkring syv lag til at skabe blot én millimeter, så antallet af lag pr. del kan hurtigt komme op i hundredvis. Vakuum bruges derefter til at komprimere disse lag, og Busch leverer vakuumpumperne til jobbet.
Fusion under vakuum
Delene lægges på en form og forsegles inde i plastikposer. En vakuumpumpe påsættes, og luften suges ud, så lagene presses mod hinanden og ikke kan bevæge sig. Derfra placeres den lagdelte form, der stadig er tæt komprimeret inde i vakuumposen, i en autoklave. Der holdes delene under vakuum, kombineret med varme og tryk. Varmen blødgør harpiksen, hvilket får lagene til at smelte sammen. Det kontinuerlige vakuum og tryk sikrer, at al luft fjernes, lagene bliver klemt tæt mod hinanden, og de konsoliderer sig. Det, der kommer ud af autoklaven, er ikke længere flere forskellige bøjelige lag, men et solidt og robust stykke, klar til racerbanen - uanset om man konkurrerer om en topplacering i Formel 1 eller om titlen som bedste universitetshold.
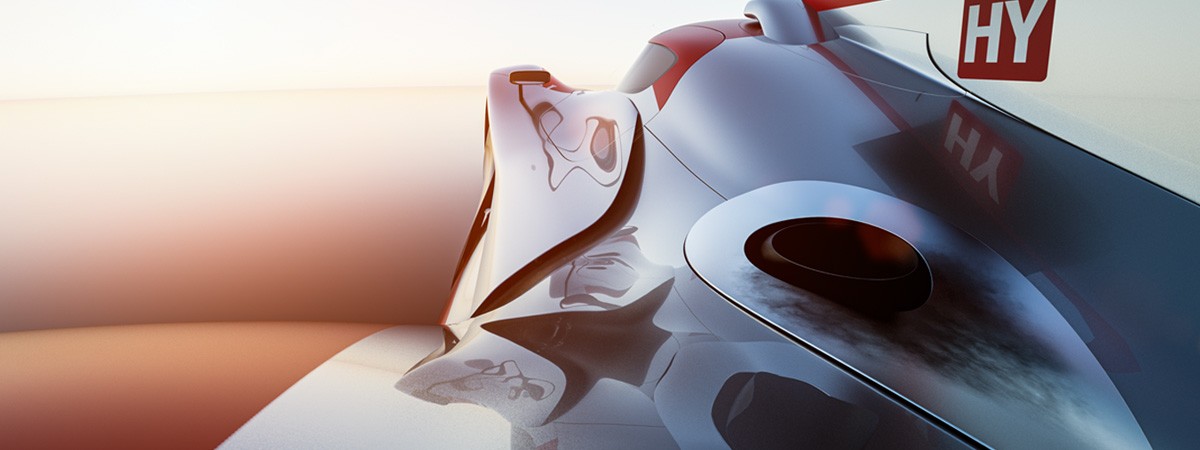
Med styrke og lethed rundt på racerbanen
Kulfiberforstærkede løsninger til letvægtshastighed
Fra foredragssal til racerbane
At designe, bygge og køre en racerbil til målstregen er ingen nem opgave, men hvert år tager universitetsstuderende fra hele verden udfordringen op og bringer deres prototyper til Formula Student-racerbanerne. I modsætning til Formel 1 er denne konkurrence langt mere end, hvem der kommer hurtigst rundt på banen. De biler, de studerende fremstiller, bedømmes på alt fra kurvehastighed og brændstofeffektivitet til fremstilling og omkostninger – og hvert hold skal præsentere en fuldstændig forretningsplan. Som følge heraf er det ikke kun studerende på ingeniørkurser, der udgør holdene, men også dem, der har hovedfag i business, økonomi og marketing. De studerende opfordres til selv at fremstille så meget af bilen som muligt. Det er hér, Busch er stolt af at yde support: I de sidste par år har Busch leveret vakuumpumper for at hjælpe de forskellige teams med at bygge deres drømmeracerbiler.
At designe, bygge og køre en racerbil til målstregen er ingen nem opgave, men hvert år tager universitetsstuderende fra hele verden udfordringen op og bringer deres prototyper til Formula Student-racerbanerne. I modsætning til Formel 1 er denne konkurrence langt mere end, hvem der kommer hurtigst rundt på banen. De biler, de studerende fremstiller, bedømmes på alt fra kurvehastighed og brændstofeffektivitet til fremstilling og omkostninger – og hvert hold skal præsentere en fuldstændig forretningsplan. Som følge heraf er det ikke kun studerende på ingeniørkurser, der udgør holdene, men også dem, der har hovedfag i business, økonomi og marketing. De studerende opfordres til selv at fremstille så meget af bilen som muligt. Det er hér, Busch er stolt af at yde support: I de sidste par år har Busch leveret vakuumpumper for at hjælpe de forskellige teams med at bygge deres drømmeracerbiler.