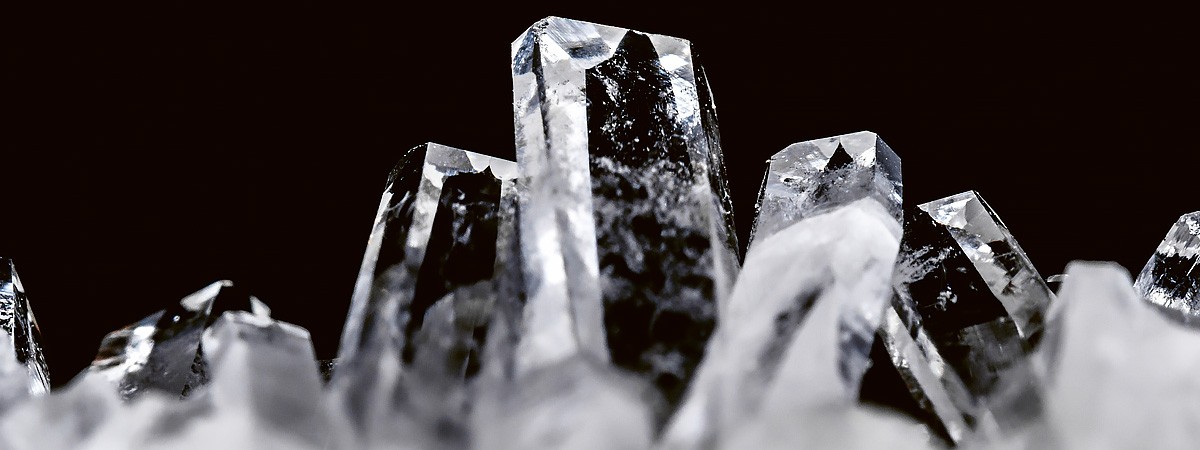
Criação dos cérebros da tecnologia atual
Silício ultrapuro para microchips
O silício nos rodeia como o segundo elemento mais abundante na crosta terrestre. Mas na natureza, ele só é encontrado combinado com outros elementos, como areia, quartzo e outras rochas. Para um microchip, é necessário um cristal puro. Ele pode ser formado sob vácuo usando uma bomba de vácuo da Busch.
A sociedade moderna depende muito dos microchips. Eles são os cérebros por trás dos dispositivos eletrônicos e são mais comumente usados nos setores de entretenimento e automotivo. Mas à medida que entramos cada vez mais na era da tecnologia inteligente, os microchips aparecem nos lugares mais inesperados - em brinquedos para crianças, máquinas de lavar roupa e até mesmo no seu passaporte.
Um cristal feito de vários
A história de cada microchip começa com o polissilício, uma forma de silício composta por vários pequenos cristais. Para a indústria eletrônica, o silício deve ser de altíssima pureza. Isso significa normalmente entre 99,999% e 99,999999999% - não mais do que um átomo não silício por bilhão de átomos de silício. Para criar um microchip, o polissilício deve ser transformado em um único cristal, chamado de silício monocristalino. Isso é crítico para a produção de microchips: caso contrário, os limites de granulação e as irregularidades na estrutura cristalina do polissilício afetariam o desempenho do microchip acabado. Existem vários métodos de produção de silício monocristalino, sendo o mais comum o método de Czochralski, que cultiva um cristal de silício sob vácuo.
Cristais de semente
O silício monocristalino é produzido usando o que é conhecido como extrator. Este nome abrange uma variedade de tecnologias diferentes, com duas partes principais: um forno a vácuo e um mecanismo que puxa o cristal para criar sua forma. Dentro da câmara do forno a vácuo, o polissilício é aquecido a temperaturas extremamente altas de cerca de 1.410 °C. Um pequeno pedaço de silício monocristalino, chamado de semente, é colocado no centro e lentamente puxado para cima enquanto é girado. A semente puxa com ela o silício fundido para cima, que se solidifica à medida que sobe. Isso cria uma haste longa e cilíndrica de silício puro. O silício fundido é altamente reativo, portanto, para manter sua elevada pureza, ele não deve entrar em contato com o ar ambiente. Portanto, o ar é evacuado da câmara usando uma bomba de vácuo da Busch. Isso cria um ambiente de crescimento livre de contaminantes e o cristal da mais alta qualidade, pronto para continuar sua longa jornada através da fabricação de semicondutores para se tornar um microchip.
Um cristal feito de vários
A história de cada microchip começa com o polissilício, uma forma de silício composta por vários pequenos cristais. Para a indústria eletrônica, o silício deve ser de altíssima pureza. Isso significa normalmente entre 99,999% e 99,999999999% - não mais do que um átomo não silício por bilhão de átomos de silício. Para criar um microchip, o polissilício deve ser transformado em um único cristal, chamado de silício monocristalino. Isso é crítico para a produção de microchips: caso contrário, os limites de granulação e as irregularidades na estrutura cristalina do polissilício afetariam o desempenho do microchip acabado. Existem vários métodos de produção de silício monocristalino, sendo o mais comum o método de Czochralski, que cultiva um cristal de silício sob vácuo.
Cristais de semente
O silício monocristalino é produzido usando o que é conhecido como extrator. Este nome abrange uma variedade de tecnologias diferentes, com duas partes principais: um forno a vácuo e um mecanismo que puxa o cristal para criar sua forma. Dentro da câmara do forno a vácuo, o polissilício é aquecido a temperaturas extremamente altas de cerca de 1.410 °C. Um pequeno pedaço de silício monocristalino, chamado de semente, é colocado no centro e lentamente puxado para cima enquanto é girado. A semente puxa com ela o silício fundido para cima, que se solidifica à medida que sobe. Isso cria uma haste longa e cilíndrica de silício puro. O silício fundido é altamente reativo, portanto, para manter sua elevada pureza, ele não deve entrar em contato com o ar ambiente. Portanto, o ar é evacuado da câmara usando uma bomba de vácuo da Busch. Isso cria um ambiente de crescimento livre de contaminantes e o cristal da mais alta qualidade, pronto para continuar sua longa jornada através da fabricação de semicondutores para se tornar um microchip.
Os lugares mais limpos da Terra
No mundo natural, não existe ar verdadeiramente limpo. Lembramos disso em dias ensolarados, quando de repente percebemos a poeira dançando ao nosso redor em um raio de sol. De fato, um escritório médio tem até 3.500.000.000 de partículas minúsculas - algumas invisíveis a olho nu - em cada metro cúbico de ar. Mas em certos processos de fabricação, como nas indústrias aeroespacial, de semicondutores e farmacêutica, essa parte normal da vida pode levar à contaminação dos produtos. Salas limpas são, portanto, essenciais. As mais rigorosas permitem apenas 10 partículas minúsculas de ≥ 0,1 μm por metro cúbico: o equivalente aproximado de uma única semente de gergelim em uma piscina olímpica.
As instalações usam uma variedade de métodos para manter suas salas limpas e livres de contaminantes. Eles variam desde roupas de proteção e máscaras a chuveiros de ar, onde os trabalhadores recebem jatos de ar para remover partículas remanescentes. Em uma fábrica de semicondutores, até mesmo perfumes, maquiagem e produtos para cabelo são proibidos, pois mesmo a menor partícula pode arruinar um lote de wafers.
Portanto, se você realmente precisa de ar fresco, esqueça um passeio pelo campo. O ar mais limpo do nosso planeta pode ser encontrado dentro de uma sala limpa.
No mundo natural, não existe ar verdadeiramente limpo. Lembramos disso em dias ensolarados, quando de repente percebemos a poeira dançando ao nosso redor em um raio de sol. De fato, um escritório médio tem até 3.500.000.000 de partículas minúsculas - algumas invisíveis a olho nu - em cada metro cúbico de ar. Mas em certos processos de fabricação, como nas indústrias aeroespacial, de semicondutores e farmacêutica, essa parte normal da vida pode levar à contaminação dos produtos. Salas limpas são, portanto, essenciais. As mais rigorosas permitem apenas 10 partículas minúsculas de ≥ 0,1 μm por metro cúbico: o equivalente aproximado de uma única semente de gergelim em uma piscina olímpica.
As instalações usam uma variedade de métodos para manter suas salas limpas e livres de contaminantes. Eles variam desde roupas de proteção e máscaras a chuveiros de ar, onde os trabalhadores recebem jatos de ar para remover partículas remanescentes. Em uma fábrica de semicondutores, até mesmo perfumes, maquiagem e produtos para cabelo são proibidos, pois mesmo a menor partícula pode arruinar um lote de wafers.
Portanto, se você realmente precisa de ar fresco, esqueça um passeio pelo campo. O ar mais limpo do nosso planeta pode ser encontrado dentro de uma sala limpa.