The proper term is "vacuum-supported resin infusion process"; surfboard manufacturers give it a nickname: vacuum bagging. The process makes it possible to produce surfboards that are extremely light yet sturdy, the superior properties of which are particularly valued by professionals.
Boards for every occasion
Sliding down a mountain that emerges in the very moment you are riding it is perhaps one of the most profound interactions with the elements that one can experience. The first surfers used bundles of plant stalks, small tree trunks, planks or the tips of canoes. They started riding waves about 4,000 years ago and were true experts when it came to handling the ocean: these were the Polynesians, who conquered the Pacific in their canoes long before the European explorers. So the sport should actually be called he'e nalu – that is the Hawaiian word for surfing. Especially because you will find the hottest surf-spots in the world in Hawaii.
Surfboards have always been as individual as their owners. They exist in countless shapes and designs; the models are adjusted for diverse needs and demands. The construction influences the turning behaviour, buoyancy and speed. Whether small and manoeuvrable or long and tip-resistant – every surfer has his or her favourite board for every type of surf. Professionals travel to their competitions with a dozen or so boards. The best models are manufactured – often individually – in a vacuum-supported resin infusion process.
Assembly layer by layer
Rigid foam is usually used for the core of the surfboard. As of late, this also includes a helium-filled bubble made out of plastic foil in the middle to further reduce the base weight. This core is then coated with several layers of fibre made mainly from fibreglass or carbon fibre. The outermost layer is wrapped in a peel ply, a plastic material that is removed after curing. It leaves behind a uniformly rough surface that can be varnished later for the outer shell of the board. But for resin infusion, this structure is first covered with suction felt to ensure that the vacuum is distributed evenly. The package is now placed into the mould, which determines the final size and contour of the board. It consists of two halves and is initially pretreated with release wax so that it can be easily removed again. That is important, because very sticky synthetic resin will flow into the mould later.
Vacuum ensures strength
But the mould is first carefully packed in a vacuum bag. All open edges of the bag are closed using vacuum sealing tape to create an hermetically sealed pocket – the so-called "vacuum bag". It is only interrupted in two places by flexible pipe lines that lead to the inside of the mould. After the bag and sealing tape have been checked for leaks, a vacuum pump removes the air from the mould through one of the pipe lines. The second pipe line is then used to add the liquid resin.
The vacuum not only guarantees that the resin penetrates the layers of fibres without air pockets; thanks to an innovative vacuum process, significantly less resin is required to saturate the layers of fibre more thoroughly than was possible with conventional methods. The vacuum guarantees that the resin is uniformly distributed and completely fills the holes between the fibres. This creates twofold advantages for the final product: the finished composite material is particularly light and yet still demonstrates great stability.
The environment also profits twofold. Using less resin corresponds to lower consumption of raw materials and energy. In addition, the vacuum technology also pumps out the solvent vapours created when processing synthetic resin. They can be diverted out of the production area and treated.
Experts praise the outstanding fine tuning of the final product's flexibility, which can be achieved using the vacuum process. Professional surfers report that they do not need as many different boards thanks to the development of this type of surfboard.
R5 rotary vane vacuum pumps are among the vacuum pumps suitable for evacuating laminate moulds for resin infusion.
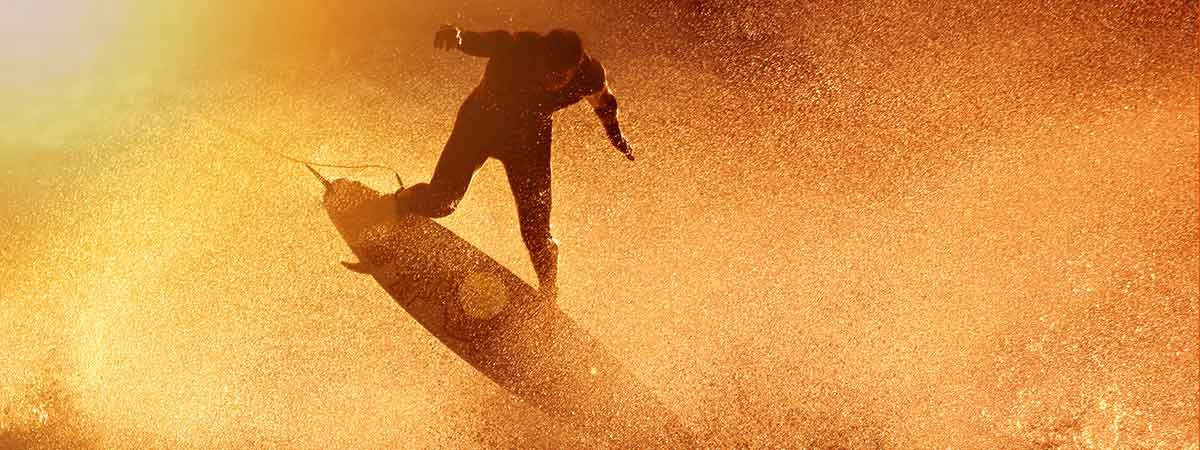
Making it easier to ride the waves
Perfect surfboards are created using vacuum
What else is created using vacuum technology for lightweight construction?
The vacuum-supported resin infusion process is not just used for surfboards. Many other products that very much depend on the combination of lighter weight and greater strength are also manufactured using this technology. They include rotor blades for wind and tidal energy plants, boat hulls for high-quality yachts, fuselages and wings for ultralight aeroplanes and gliders, but also a growing number of components for passenger planes, for example. In addition to the mechanical quality of the material, the military also values its radar-deflecting characteristics, for example in submarine structures. New application areas are being discovered all the time, for example, in medical technology, mechanical engineering and robotics, car manufacturing, transport and rail transport and also for high-tech sporting equipment like bobsleighs.
The vacuum-supported resin infusion process is not just used for surfboards. Many other products that very much depend on the combination of lighter weight and greater strength are also manufactured using this technology. They include rotor blades for wind and tidal energy plants, boat hulls for high-quality yachts, fuselages and wings for ultralight aeroplanes and gliders, but also a growing number of components for passenger planes, for example. In addition to the mechanical quality of the material, the military also values its radar-deflecting characteristics, for example in submarine structures. New application areas are being discovered all the time, for example, in medical technology, mechanical engineering and robotics, car manufacturing, transport and rail transport and also for high-tech sporting equipment like bobsleighs.