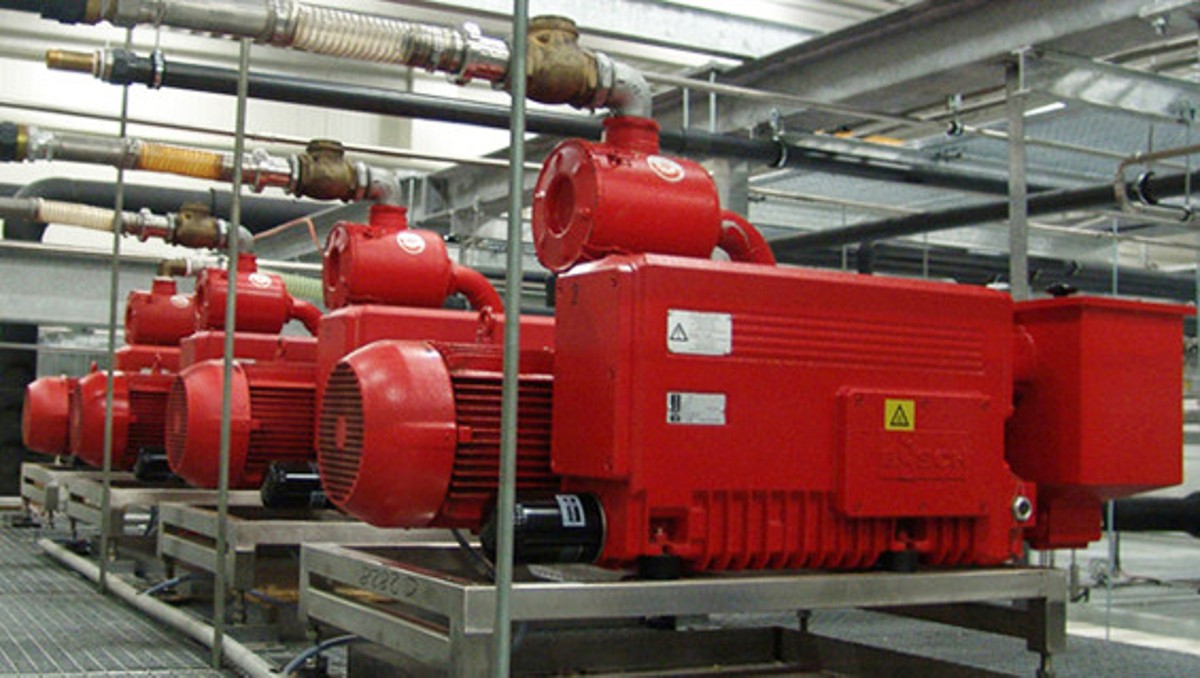
R5 vacuum pumps from Busch for MAP packaging.
Economical and Safe Packaging of Sausages and Convenience Products in an Oxygen Atmosphere
Packaging in an oxygen atmosphere
Packaging using protective gas is a common method for increasing the shelf life of sausages and convenience products. The film packaging used as part of this process must first be evacuated and the gas then drawn in. Carbon dioxide (CO2), nitrogen (N2), oxygen (O2) or a mixture of these gases are normally used for this method, known as “modified atmosphere packaging” (MAP). Treatment with oxygen involves a certain safety risk in the packaging process due to the risk of explosion in the case of concentrations of oxygen in excess of 21 percent.
Packaging in an oxygen atmosphere
Manufacturers of packaging machines and vacuum pumps have devised different safety concepts to ensure absolute safety in the implementation of this process.
These vacuum pumps are setting standards not only in terms of safety, but also in terms of reliability and economy.
Packaging of sausage and meat products
For more than ten years now, one of the largest producers of sausage products in Germany, with a daily production capacity of over 100 tonnes, has used Busch rotary vane vacuum pumps for packaging its products. In 1996, the vacuum supply was centralised. The central unit now in place supplies the vacuum for the thermoforming machines in 17 packaging lines on which sausage and meat products are packaged. On five additional tray sealing machines, convenience products are packaged using different protective gases, including oxygen. The vacuum packaging of these products is carried out by four identical rotary vane vacuum pumps from the oxygen version of the Busch R5 series. These vacuum pumps are installed on a mezzanine directly above the packaging room.The operators of these vacuum pumps have identified a clear advantage of the Busch models over standard vacuum pumps:
- If a power failure occurs and oxygen floods into the vacuum pump, the oxygen must not be allowed to come into contact with mineral oil. For this reason, these vacuum pumps are operated using a fully synthetic lubricant, known as a perfluoropolyether (PFPE).
- These four Busch R5 vacuum pumps in the oxygen version have been in three-shift operation for over ten years and achieve an average operating time of 6000 hours per year.
- The operator opts to rely on Busch to supply the maintenance of these vacuum pumps. The rotary vane vacuum pumps undergo maintenance twice a year, a process that involves a number of different checks. When the actual maintenance process is performed, filter elements are replaced as a preventive measure. It is not necessary to replace the fully synthetic lubricant as perfluoropolyether is outstandingly inert and therefore does not form compounds with other materials such as oxygen. R5 rotary vane vacuum pumps for oxygen applications are therefore lubricated for their full service lives.
- This represents an extremely significant advantage for the operators working for the sausage and meat producer, as there are no longer any costs for replacing the lubricant. The operators only need to factor in the shortfalls that may occur due to the replacement of the filter elements.
- This represents an extremely significant advantage for the operators working for the sausage and meat producer, as there are no longer any costs for replacing the lubricant. The operators only need to factor in the shortfalls that may occur due to the replacement of the filter elements.
This meat processing business follows a rigorous freshness policy in order to ensure that the time between producing the goods and the goods going on display at the retailer's premises does not exceed 24 hours. Production must therefore also be performed on Saturdays, to ensure that fresh goods can be sold in the markets on Mondays. For the technical team, this means being able to fully rely on the vacuum pumps. If a pump were to break down, this would lead to a packaging line standing idle and consequently to a production shortfall with the potential for goods to spoil. However, the technicians responsible for the production of the sausage products have peace of mind thanks to their extremely positive experiences: none of the Busch rotary vane vacuum pumps have ever broken down.
This is clearly an excellent indication of the quality of the vacuum pumps, and it is also evidence that the preventive maintenance provided by the Busch customer service team is working well. The use of the Busch R5 vacuum pumps in the oxygen version also proves that even after an operating time of ten years and after well over 60,000 operating hours, the performance, reliability and operational safety of the pumps remain completely unimpaired.