MINK
Dry claw vacuum pumps and compressors
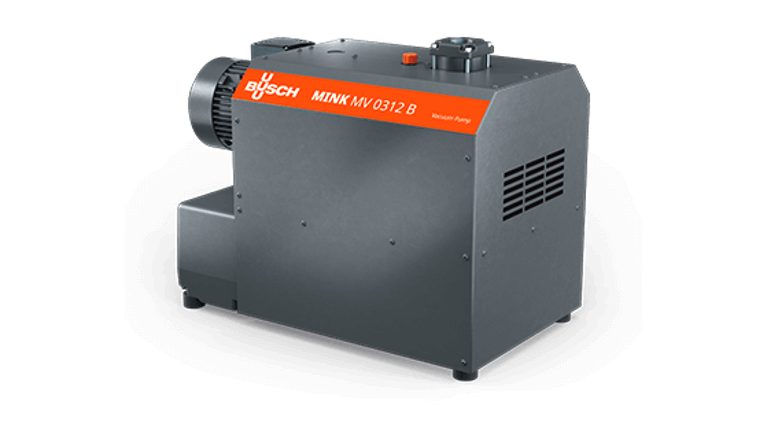
MINK claw vacuum pumps and compressors are the result of continuous development in claw technology. Decades of experience in countless applications have led to substantial improvements.
MINK claw technology combines performance, reliability and efficiency through an innovative design. It can be used for both, vacuum and compressed air generation.
The dry and contact-free operating principle provides the benefit of nearly maintenance-free operation.
MINK vacuum pumps and compressors are perfectly suited for industrial applications, in which constant vacuum or overpressure and oil-free operation are essential.
Operating principle
MINK claw vacuum pumps and compressors feature two claw-shaped rotors. The rotors are mounted in a housing and move in opposite directions. The shape of these claw rotors extracts, compresses and expels the pumped medium.The minimal clearance between the rotors and the chamber housing optimizes the internal seal. So, no lubricants or operating fluids are required in the compression chamber.
MINK vacuum pumps and compressors are driven by a directly flange-mounted motor. A synchronizing gearbox maintains precise rotor timing.
MINK MA
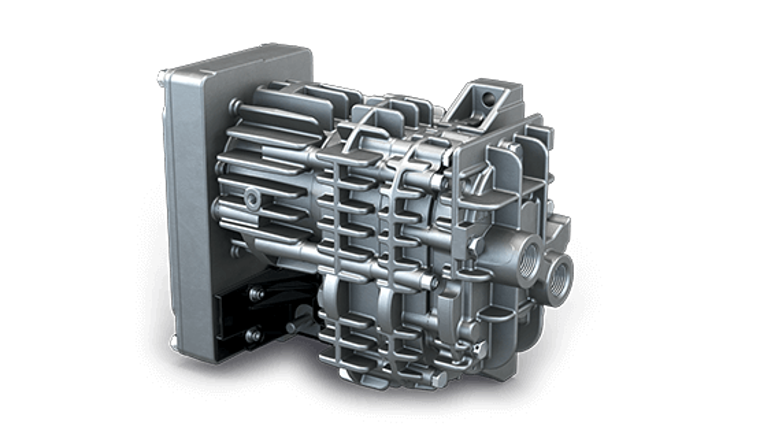
- Specially designed for mobile applications
- Compact design
- Vibration-resistant
- Operation under extreme conditions
- Dry and contact-free compression
- Maintenance-free
- Integrated speed control
Benefits of the MINK MA series
MINK MA are dry claw compressors, specially developed to compress or transport air in mobile applications mainly for the automotive and transport sector.
These compressors are resistant to severe vibration. They may be operated in temperature ranges between -40 °C and +100 °C and at elevations between -1,000 m and 4,000 m.
The "all-in-one" design leads to a very small footprint making MINK MA the optimum solution for mobile applications.
Their operating principle is dry. Thus, the pumped medium is not contaminated and may be used later without filtration or cleaning.
None of the internal moving parts come in contact with each other. Components are not subject to wear and servicing tasks are eliminated completely.
An integrated speed control allows the volume flow to be altered dynamically. Thus, MINK MA compressors always operate within the most efficient output range.
The CAN communication system permits parameters such as rotational speed, power consumption and temperature to be permanently recorded and controlled.
All MINK MA products
MINK MB
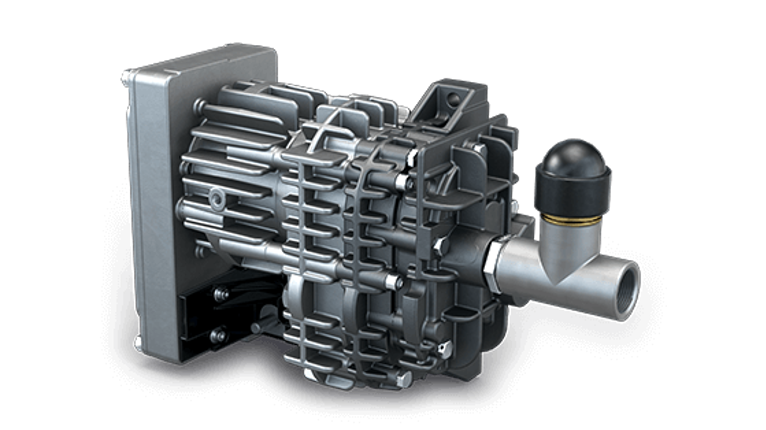
- Specially designed for mobile applications
- Compact design
- Vibration-resistant
- Operation under extreme conditions
- Dry and contact-free compression
- Maintenance-free
- Integrated speed control
Benefits of the MINK MB series
MINK MB are dry claw vacuum pumps mainly for the automotive and transport sector.
They are resistant to severe vibration and may be operated in temperature ranges between -40 °C and +40 °C.
The "all-in-one" design leads to a very small footprint making MINK MB the optimum solution for mobile applications.
Their operating principle is dry. Thus, the pumped medium is not contaminated and may be used later without filtration or cleaning.
None of the internal moving parts come in contact with each other. Components are not subject to wear and servicing tasks are eliminated completely.
An integrated speed control allows the pumping speed to be altered dynamically. Thus, MINK MB vacuum pumps always operate within the most efficient output range.
The CAN communication system permits parameters such as rotational speed, power consumption and temperature to be permanently recorded and controlled.
All MINK MB products
MINK MH
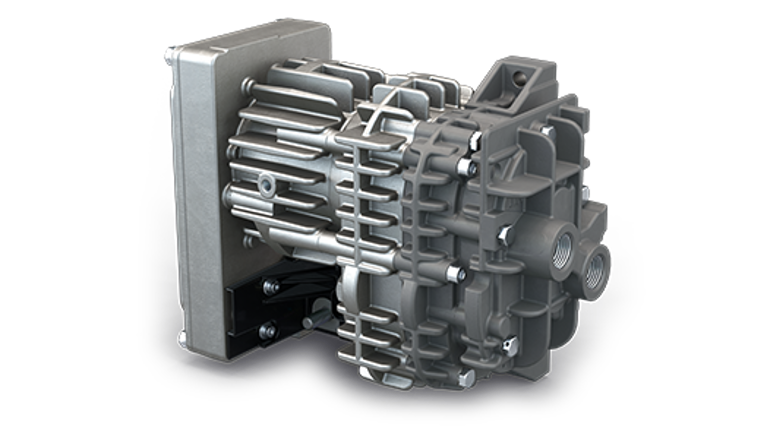
- Specially designed for fuel cells
- Hydrogen-approved by SGS-TÜV
- Compact design
- Vibration-resistant
- Operation under extreme temperature conditions
- Dry and contact-free operating principle
- Maintenance-free
- Integrated speed control
Benefits of the MINK MH series
MINK MH are hydrogen-approved claw compressors specially developed for the recirculation of hydrogen (H2) in fuel cells.
They are resistant to severe vibration levels and may be operated under extreme temperature conditions, between -30°C and +85°C.
The "all-in-one" design leads to a very small footprint making MINK MH the optimum solution for every fuel cell.
Their compression is dry. This means that no operating fluids are present in the compression chamber.
None of the internal moving parts of the compressor come in contact with each other. Components are not subject to wear and servicing tasks are eliminated completely.
An integrated speed control allows the volume flow to be altered dynamically. Thus, MINK MH always operate within the most efficient output range. Their volume flow remains constant throughout the entire life cycle.
The CAN communication system permits parameters such as rotational speed and power consumption to be permanently recorded and controlled.
Fields of application
Mink MH are the ideal solution for the following sectors in which hydrogen recirculation plays an important role:
- Transportation: automotive, rail, maritime, aviation
- Stationary: electricity generation
Operating principle fuell cell
In a fuel cell, a combination of hydrogen (coming from the tank) and oxygen (from the air) produces electricity, heat and water as a by-product.
A fuel cell consists of two electrodes, an anode and a cathode. A membrane separates them from each other and is responsible for the ion transport.
Hydrogen is supplied on the anode side, oxygen on the cathode side. The hydrogen molecules are split into protons and electrons.
The hydrogen protons diffuse through the membrane to the cathode, where they react with the oxygen to form water, thereby releasing energy.
It is important that oxygen does not diffuse into the hydrogen loop to prevent explosive conditions. Therefore, hydrogen is injected in a higher quantity. This excess hydrogen shall not be released to the atmosphere because of legal regulations and efficiency reasons.
The solution is to recirculate it back to the system inlet. For that purpose, our MINK MH claw compressor comes into operation. It has been specially developed for the recirculation of excess hydrogen in fuel cells and is hydrogen-approved by TÜV Saar.
All MINK MH products
MINK MI/MM Vacuum Pumps
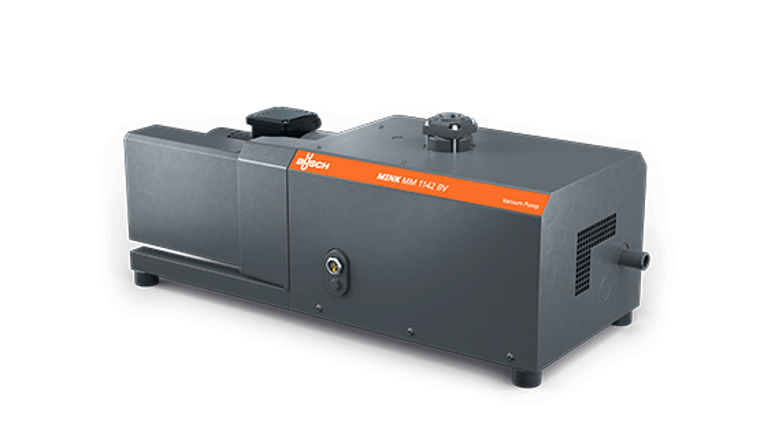
- Reliable rough vacuum generation
- High efficiency levels
- Nearly maintenance-free
- Dry and contact-free compression
Benefits of the MINK MI/MM vacuum pump series
MINK MI/MM claw vacuum pumps have been specially designed for dependable industrial vacuum generation, for example for pneumatic conveying, thermoforming, plastics processing, woodworking and many more.
These vacuum pumps operate at very high efficiency levels. They deliver constantly high pumping speeds during their entire life cycle. With substantial lower energy consumption than conventional vacuum generators of the same output.
The contact-free operating principle provides the benefit of nearly maintenance-free operation. None of the internal moving parts come in contact with each other. Components are not subject to wear and servicing tasks are reduced to a minimum.
The proven, dry claw vacuum technology allows MINK MI/MM to run without operating fluids in the compression chamber. In practice, this means no contamination of the pumped medium and no environmental emissions.
MINK MI/MM Compressors
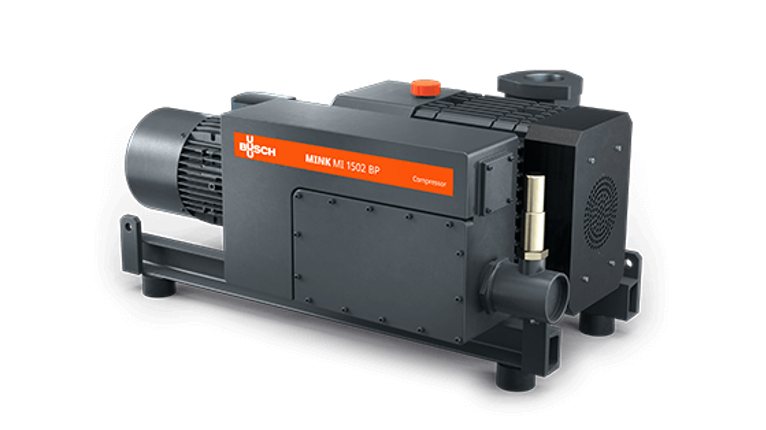
- Reliable compressed air generation
- High efficiency levels
- Nearly maintenance-free
- Dry and contact-free compression
Benefits of the MINK MI/MM compressor series
MINK MI/MM claw compressors have been specially designed for dependable industrial overpressure generation, for example for pneumatic conveying, water degassing, water treatment, fish farming applications and many more.
These compressors operate at very high efficiency levels. They deliver constantly high volume flows during their entire life cycle with substantial lower energy consumption than conventional compressors of the same output.
The contact-free operating principle provides the benefit of nearly maintenance-free operation. None of the internal moving parts come in contact with each other. Components are not subject to wear and servicing tasks are reduced to a minimum.
The proven, dry claw technology allows MINK MI/MM to run without operating fluids in the compression chamber. In practice, this means no contamination of the pumped medium and no environmental emissions.
All MINK MI/MM compressors
MINK MV
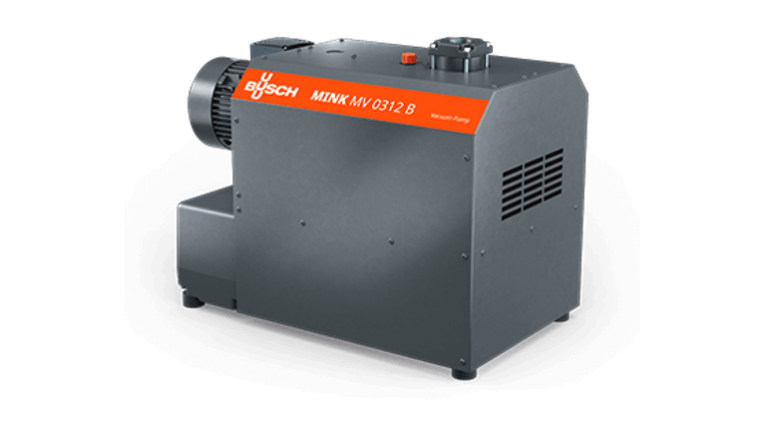
- Latest claw vacuum technology
- State-of-the-art acoustic design
- Up to 50% lower overall operating costs
- Small footprint
- Nearly maintenance-free
- Dry and contact-free compression
Video: How MINK MV vacuum pumps work
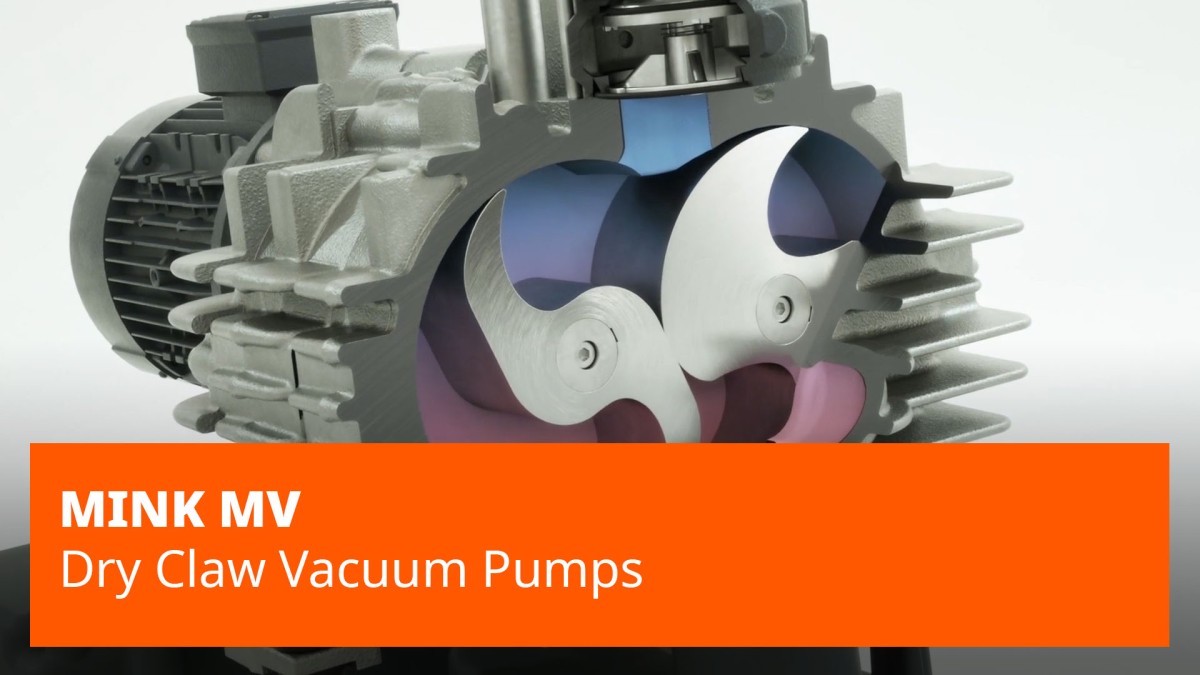
Benefits of the MINK MV series
MINK MV are the new standard for claw vacuum pumps.
They are three times better than comparable conventional vacuum generators: more quiet, more efficient, more compact.
These vacuum pumps have been specially designed for a wide range of applications, for example woodworking, pneumatic conveying or plastics processing.
The optimized sound insulation is manufactured according to the latest developments in acoustic design. Thus, the low noise levels allow quiet operation in the immediate vicinity of workstations.
Thanks to their sophisticated design MINK MV vacuum pumps achieve exceptionally high efficiency levels. They can reduce overall operating costs by up to 50% in comparison to conventional vacuum generators.
With their compact dimensions, MINK MV vacuum pumps can be installed in the smallest of floor areas.
The contact-free operating principle provides the benefit of a nearly maintenance-free operation. None of the internal moving parts come in contact with each other. Components are not subject to wear and servicing tasks are reduced to a minimum.
The proven, dry claw vacuum technology allows MINK MV to run without operating fluids in the compression chamber. In practice, this means no contamination of the pumped medium and no environmental emissions.
All MINK MV products
Video: How to change filters and gear oil of the MINK MV
MINK MW
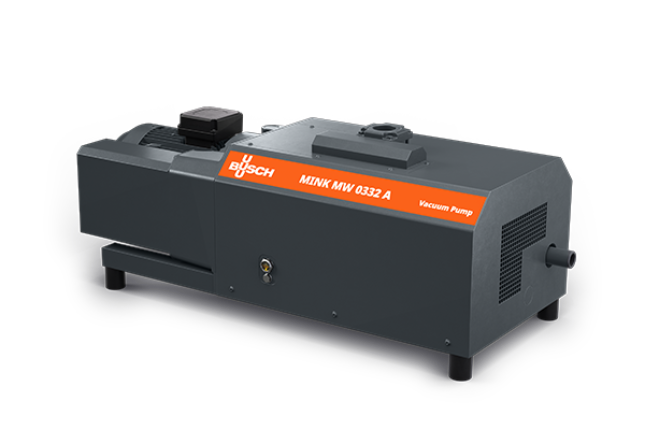
- Latest claw vacuum technology
- Low energy consumption
- Nearly maintenance-free
- Dry and contact-free compression
Benefits of the MINK MW series
MINK MW is the first claw vacuum pump series ever that can be continuously operated at an ultimate pressure of 0.8 hPa (mbar). Preferred applications for the MW include thermoforming, pick and place, vacuum die casting, central vacuum systems for packaging, and vacuum cooling.
These vacuum pumps operate at very high-efficiency levels. They deliver consistently high pumping speeds throughout their entire life cycle, with a significantly lower energy consumption compared to conventional vacuum generators of the same output.
The contact-free operating principle provides the benefit of nearly maintenance-freeoperation. None of the internal moving parts come into contact with each other, so components are not subject to wear, and servicing tasks are minimized.
The proven, dry claw vacuum technology allows MINK MW to run without operating fluids in the compression chamber. In practice, this means no contamination of the pumped medium and no environmental emissions.