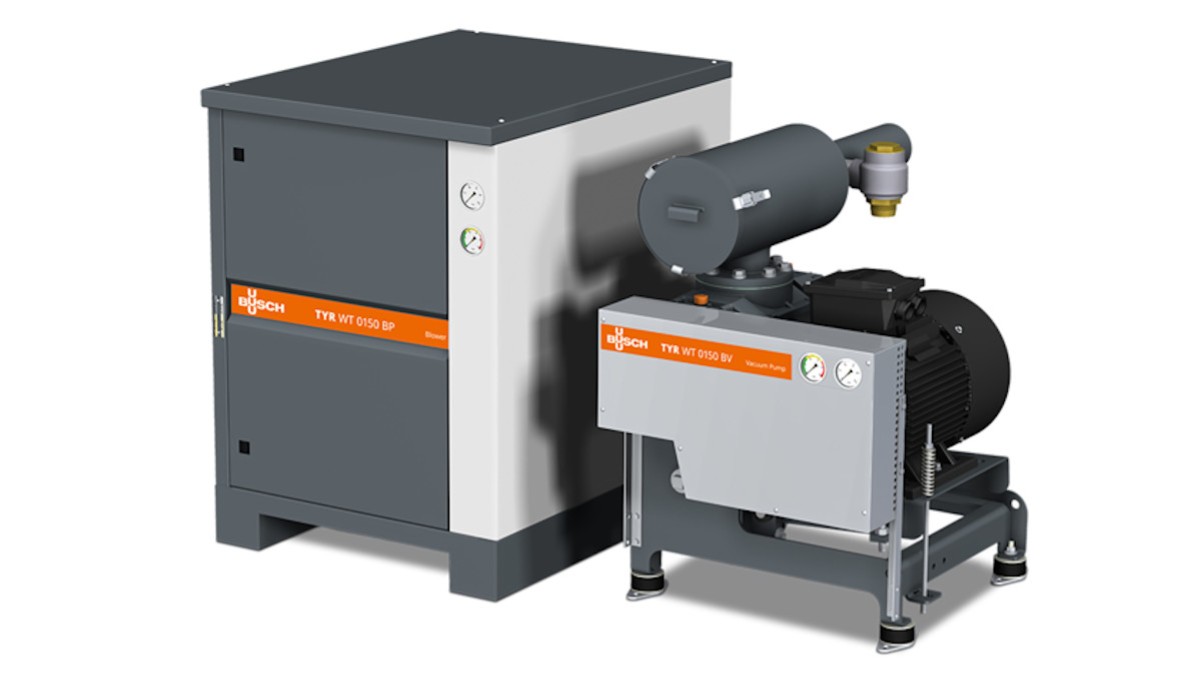
Fig. 1: Rotary lobe blowers with and without acoustic enclosure. Source: Busch Vacuum Solutions.
Vacuum Pumps for Pneumatic Suction Conveying
Economical conveying of bulk goods
Nowadays, pneumatic suction conveying is an important technology for feeding bulk goods gently through piping systems to the various process steps. In the area of food processing, the pharmaceutical and chemical industry and for material feed in plastics processing, suction conveying is indispensable when powder or granular materials have to be transported. The proper choice of the vacuum generator essentially determines the operating costs of a pneumatic conveying system.
Modern vacuum technology today enables the economical and environmentally friendly operation of vacuum conveying systems. In order to be able to select the most effective method of vacuum generation, it is vital to be very familiar with the operating conditions of the vacuum conveying system and to apply this knowledge when selecting the vacuum pump. These parameters are of crucial importance in order to select the most suitable one from various principles for vacuum generation. On the one hand, the conveyed material and its properties must be known. Additional influential parameters are pipe routing, length and diameter as well as the type of conveying (fig. 2). These parameters can be used to determine the required differential pressure (∆p). The differential pressure and the volume flow are the main influential parameters for the technical selection of the vacuum pump or vacuum system. For the economic efficiency calculation, operating costs must be considered in addition to acquisition costs. This includes the energy consumption, possibly further acquisition costs for throttle regulation, valves or control depending on the vacuum generation, the operating time (e.g. continuous operation, batch operation) as well as the maintenance effort and costs.
Modern vacuum technology today enables the economical and environmentally friendly operation of vacuum conveying systems. In order to be able to select the most effective method of vacuum generation, it is vital to be very familiar with the operating conditions of the vacuum conveying system and to apply this knowledge when selecting the vacuum pump. These parameters are of crucial importance in order to select the most suitable one from various principles for vacuum generation. On the one hand, the conveyed material and its properties must be known. Additional influential parameters are pipe routing, length and diameter as well as the type of conveying (fig. 2). These parameters can be used to determine the required differential pressure (∆p). The differential pressure and the volume flow are the main influential parameters for the technical selection of the vacuum pump or vacuum system. For the economic efficiency calculation, operating costs must be considered in addition to acquisition costs. This includes the energy consumption, possibly further acquisition costs for throttle regulation, valves or control depending on the vacuum generation, the operating time (e.g. continuous operation, batch operation) as well as the maintenance effort and costs.
-
Fig. 2: Different conveying methods require different differential pressures or vacuum levels. Source: Busch Vacuum Soluions.
Different principles of vacuum generation
The following mechanical vacuum pumps, which achieve different differential pressures or vacuum levels, are mainly used for suction conveying (fig. 3): - Side channel blowers
- Rotary lobe blowers
- Rotary vane vacuum pumps
- MINK claw vacuum pumps
-
Fig. 3: Vacuum levels (ultimate pressures) of the various blowers and vacuum pumps. Source: Busch Vacuum Solutions.
Side channel blowers
Small side channel blowers achieve high volume flows, making them suitable for use in short conveyor tracks and in flight conveying when low differential pressures and high volume flows are required. Side channel blowers compress oil-free and are relatively inexpensive to acquire. However, side channel blowers do not have a stable characteristic curve and are therefore not stable in volume. If they are operated at their performance limits, they have an above-average energy requirement.
Rotary lobe blowers
Rotary lobe blowers (fig. 1) operate contact-free and thus without oil in the compression chamber. They can be used for differential pressures up to 500 hPa (mbar). Due to these relatively low differential pressures, the use of rotary lobe blowers in suction conveying is limited to applications requiring high volume flows at low differential pressures. In this area of application, rotary lobe blowers are characterized by their low power requirement.
Rotary vane vacuum pumps
Rotary vane vacuum pumps (Fig. 4) are the ideal vacuum generators for suction conveying when high differential pressures are required and long conveyor tracks must be overcome. In addition, rotary vane vacuum pumps are always suitable when products must be conveyed slowly (plug conveying, fig. 2). Ultimate pressures of up to 0.1 hPa (mbar) can be achieved with rotary vane vacuum pumps, which corresponds to a vacuum of 99.99 percent. No other vacuum generator in suction conveying achieves such a high vacuum (fig. 3) and can also operate at lower differential pressures. This guarantees a stable characteristic curve over the entire pressure range from atmospheric pressure to operating pressure. Rotary vane vacuum pumps are lubricated with circulating oil. This means that they have an internal oil circuit, which requires regular maintenance.
-
Fig. 4: Rotary vane vacuum pump. Source: Busch Vacuum Solutions.
MINK claw vacuum pumps
MINK claw vacuum pumps (fig. 5) from Busch Vacuum Solutions have been the standard vacuum generators in pneumatic suction conveying for several years. This is a development that has been justified by their energy efficiency, the fact that they are nearly maintenance-free and can be controlled on a demand-driven basis. MINK claw vacuum pumps are available in various versions and sizes from 60 to 1200 m3/h each with standard motors or with variable speed drives. Busch also offers individual central vacuum supply systems for several conveying systems or entire plants. MINK claw vacuum pumps compress oil- and contact-free. This makes them nearly maintenance-free and extremely energy-efficient.-
Fig. 5: MINK claw vacuum pump. Source: Busch Vacuum Solutions.