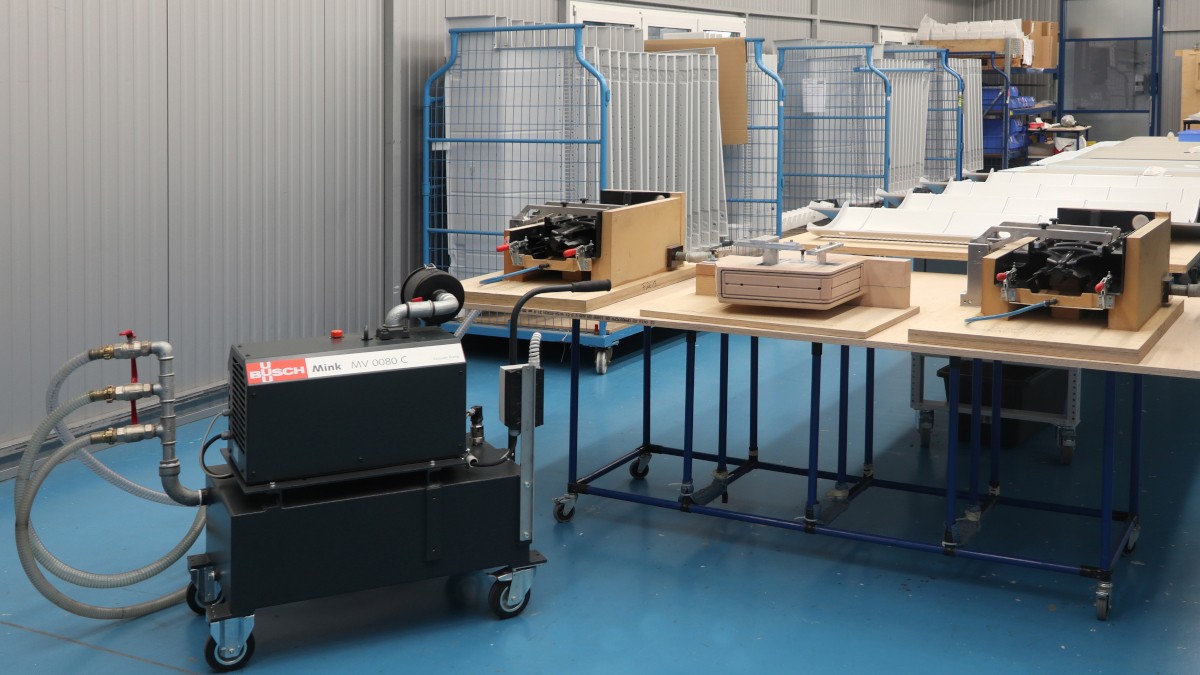
Fig. 1: The MINK MV claw vacuum pump as a mobile unit with a vacuum vessel in use on three holding devices for bonding plastic parts. Source: Busch Vacuum Solutions.
Perfect Holding with Modern Vacuum Technology
Ernst Hombach GmbH & Co. KG
Ernst Hombach GmbH & Co. KG has now found the perfect solution for holding plastic parts during bonding. For more than two years, the company has been using a mobile MINK MV claw vacuum pump from Busch Vacuum Solutions to precisely fix various plastic parts in clamping and holding devices so that they can be joined together by bonding. The highlight of this solution is that the vacuum pump is mounted on a vacuum vessel and is frequency-controlled. It therefore delivers the required output depending on demand, regardless of whether one or three parts need to be fixed on the holding devices. This makes bonding parts extremely flexible, effective and efficient.
About Ernst Hombach GmbH & Co. KG
With 130 employees, Ernst Hombach manufactures plastic products in Uehlfeld, Franconia, ranging from high-quality individual parts to prefabricated mass-produced components for medical technology, railway vehicles and many other industries. The company was founded in 1947 by Ernst Hombach. During the early years, they only manufactured lampshades, but in the 1960s Ernst Hombach became involved with vacuum thermoforming and revolutionized this process with the development of closed-chamber twin-sheet forming. This process makes it possible to thermoform two thermoplastic plates simultaneously into an upper and lower mold, allowing hollow bodies to be produced in a single operation. Today, twin-sheet technology is used, among other things, to produce cladding for machines or equipment in medical technology, such as housings for magnetic resonance imaging equipment (Fig. 2). Hombach can offer virtually all steps of production to its customers, from the concept to series production – from design, construction and prototyping to thermoforming, further processing, pre-assembly and finishing. Timo Tobolla, Managing Director, thus rightly sees himself as a system supplier for his customers.
-
Fig. 2: Parts for the housing on magnetic resonance imaging (MRI) devices are thermoformed at Hombach using the twin-sheet process and then completed into finished components. Source: Ernst Hombach GmbH & Co. KG.
Fixing plastic parts with the help of vacuum
Individual thermoformed parts are bonded in a separate production hall. In this process, the individual plastic parts are fixed in a holding device under vacuum and joined to other components by bonding. Due to the required high level of precision of these bondings, it is indispensable that the parts are securely and precisely fixed. In the past, an oil-lubricated vacuum pump was used for this purpose, which was placed on a pallet at the respective workstations and to which a maximum of two holding devices could be connected at any one time. The disadvantage of this solution was that this system was not very flexible. What's more, the vacuum pump always ran at full speed and thus always had an unnecessarily high-power consumption. In addition, the vacuum pump was relatively loud, which was annoying when operating directly at the workstations.Flexible Busch solution for holding plastic parts
After consulting with a vacuum expert from Busch Vacuum Solutions, the expert offered a solution that was precisely tailored to these needs, namely a MINK MV claw vacuum pump. This vacuum pump does not require oil as an operating fluid. It therefore works completely dry and contact-free. This makes it nearly maintenance-free: no oil change, no filter change, no wearing parts. The MINK MV is standard equipped with frequency control. This means that the vacuum pump can be programmed to set a specific vacuum level necessary to hold the parts. The vacuum pump adapts its performance to the respective requirements. For example, if the necessary vacuum is applied to a holding device, the pump reduces the rotational speed until it comes to a standstill. If a second holding device is connected, vacuum is also immediately applied there by the buffer in the vacuum vessel. If the pressure in the vacuum vessel rises above the programmed level, the vacuum pump automatically starts to lower and maintain it again via the rotational speed.
The MINK MV claw vacuum pump is installed together with the vacuum vessel to form a compact and mobile unit (Fig. 1), which can be easily moved to the respective work- stations. Timo Tobolla sees the main advantage of this solution in the fact that he uses considerably less energy with the MINK MV and that, instead of two holding devices in the past, three can now be simultaneously operated under vacuum. Furthermore, the regular maintenance work previously required, and the associated costs are no longer necessary.
In addition, handling the new vacuum supply is much easier and, what's more, the new vacuum pump is quieter than the vacuum pump used previously.