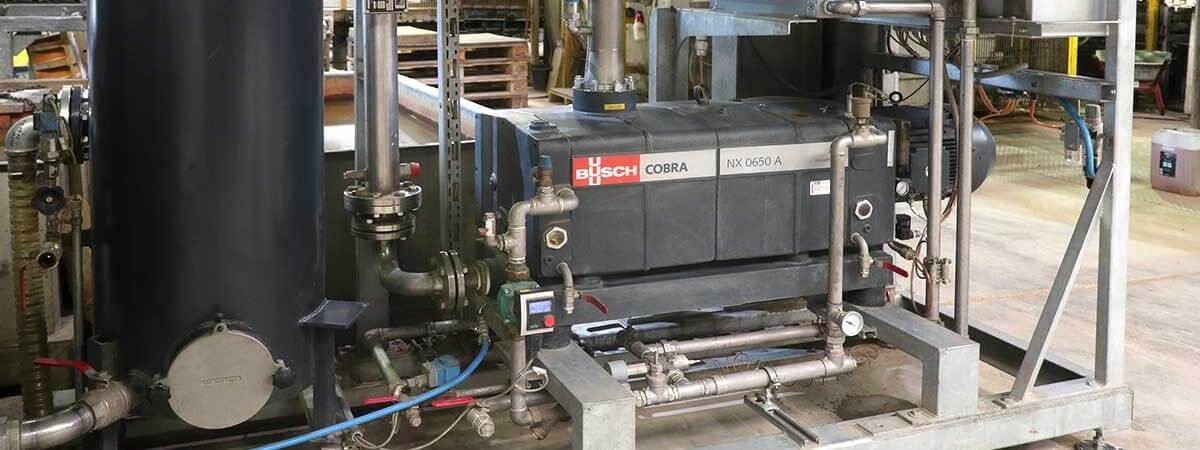
Source: Busch Vacuum Solutions.
Reliable Degassing at the Extrusion Press with Dry Vacuum Technology
Dachziegelwerke Nelskamp GmbH
The company Dachziegelwerke Nelskamp GmbH produces around 40 million roof tiles and accessories at the Groß Ammensleben location near Magdeburg, Germany. The clay roof tiles in NIBRA® quality are sold in a wide variety of shapes, designs and sizes through the building materials trade – primarily in Germany, the Benelux countries and Scandinavia. Nelskamp operates one extrusion press in each of the two modern production lines at the Groß Ammensleben location.
One of the extrusion presses has been equipped with a COBRA clay degassing system from Busch since April 2018.
One of the extrusion presses has been equipped with a COBRA clay degassing system from Busch since April 2018.
Due to extremely good experiences in terms of reliability, operational safety and economic efficiency, the second extrusion press has now also been equipped with an identical degassing system from Busch.
Dachziegelwerke Nelskamp GmbH
Nelskamp started the production of roof tiles back in 1953 with the "Finkenberger pantiles" as a high-quality alternative to clay roof tiles. Nowadays, Nelskamp has a total of six production locations throughout Germany and manufactures roof tiles, accessories and energy roofs. The first factory in Groß Ammensleben was built in 1995 and now produces roof tiles as well as accessories. Since 2002, the newly built second factory has been producing large flat tiles, of which only five to six are needed to cover one square meter of roof area.For Nelskamp, quality is the top priority. One hundred percent of the clay used is Westerwald clay, which is characterized by its low water absorption. The tiles made from Westerwald clay are fired at high temperatures. They are very hard, have a high level of flexural strength and are extremely frost-resistant. A total of 230 employees work in shifts with a seven-day week at Nelskamp's two roof tile factories in Groß Ammensleben.
Extrusion process
In the past, liquid ring vacuum pumps were used to extract the air from the clay mass directly from the vacuum chamber at the extrusion presses. Initially, a mixture of oil and water was used as the operating fluid; later, only water was used. This was not a satisfactory solution for the Mechanical Maintenance Manager because the vacuum level was subject to fluctuations.The liquid ring vacuum pumps reached the lowest ultimate pressure of 33 millibar at a water temperature of 15°C. If the temperature of the water as operating fluid increased due to the ambient temperature, for example, the vacuum level declined. In addition, maintenance work on the vacuum pumps was very time-consuming and drove up operating costs. There were also vacuum pump failures. The liquid ring vacuum pumps were not regulated, meaning they were permanently running at full speed.
As a modern family-owned company focused on sustainable management, Nelskamp pays attention to resource-saving and environmentally-friendly production methods. In 2006, Nelskamp was awarded the environmental prize of the German state of Saxony-Anhalt for its environmental concept. Nelskamp is also a member of the Saxony-Anhalt environment alliance – an alliance for sustainable regional economic policy through cooperative environmental protection. Energy consumption in the factories is therefore viewed extremely critically and potential savings are constantly being sought. This was also one of the reasons to look for alternatives for liquid ring vacuum technology.
Busch solution
Finally, Busch Vacuum Solutions found a suitable clay degassing system with a COBRA NX screw vacuum pump at its core. These screw vacuum pumps do not require any operating fluid for compression; meaning they work completely dry, without water, oil or any other liquid. The upstream standing filter has been optimized for separating dust and particles from clay masses. The frequency-controlled motor of the COBRA vacuum pump and the integrated demand-driven control unit enable the defined target value of the vacuum level in the vacuum chamber to be precisely maintained or adjusted in the event of temperature fluctuations in the material or the environment. This is an important aspect for the plant management because it ensures that the vacuum level is always correct and that a consistently high quality can be produced.-
Fig. 1: COBRA clay degassing system from Busch, installed on an extrusion press in roof tile production at Dachziegelwerke Nelskamp GmbH. Source: Busch Vacuum Solutions.
The COBRA clay degassing system (Fig. 1) was delivered completely mounted on a base frame and only needed to be connected. In addition to the vacuum pump and the control cabinet, the compact unit consists of:
In principle, a COBRA screw vacuum pump (Fig. 2) can be operated at pressures between 0.01 millibar and atmospheric pressure. As the common vacuum levels for degassing clay are between 50 and 100 millibars, the vacuum pump has sufficient reserves – both upwards and downwards.
- an upstream standing filter for dust and particle separation,
- an additional inlet filter with a polyester insert
- and a complete cooling water circulation unit.
In principle, a COBRA screw vacuum pump (Fig. 2) can be operated at pressures between 0.01 millibar and atmospheric pressure. As the common vacuum levels for degassing clay are between 50 and 100 millibars, the vacuum pump has sufficient reserves – both upwards and downwards.
-
Fig. 2: Operating principle of a COBRA screw vacuum pump that degasses the clay in the extrusion press without the use of any operating fluid. Source: Busch Vacuum Solutions.
The COBRA vacuum pump almost never operates at full power with 50 Hertz, thanks to the demand-driven control unit. This means that power consumption is reduced because only the amount of power required for the actual demand is consumed.
Compared to the previous solution with liquid ring vacuum pumps, this results in considerable energy savings, especially since screw vacuum technology already reduces the power consumption compared to liquid ring vacuum technology. Around 8,000 operating hours are recorded each year because the vacuum pump is in operation practically all year round and around the clock, with the exception of brief interruptions.
Since the COBRA clay degassing system was commissioned in April 2018, it has been operating without any malfunctions, let alone failures. Maintenance work is limited to an absolute minimum. A maintenance contract with Busch stipulates that a Busch vacuum engineer will service and inspect the system once a year. Otherwise, the inspection is limited to regular visual inspections.
Company management and the individual responsible for maintenance agree that they have opted for the technically and economically optimum solution in the form of the COBRA clay degassing system. That is why the previous liquid ring vacuum pump on the second extrusion press has now been replaced by a COBRA clay degassing system.
Compared to the previous solution with liquid ring vacuum pumps, this results in considerable energy savings, especially since screw vacuum technology already reduces the power consumption compared to liquid ring vacuum technology. Around 8,000 operating hours are recorded each year because the vacuum pump is in operation practically all year round and around the clock, with the exception of brief interruptions.
Since the COBRA clay degassing system was commissioned in April 2018, it has been operating without any malfunctions, let alone failures. Maintenance work is limited to an absolute minimum. A maintenance contract with Busch stipulates that a Busch vacuum engineer will service and inspect the system once a year. Otherwise, the inspection is limited to regular visual inspections.
Company management and the individual responsible for maintenance agree that they have opted for the technically and economically optimum solution in the form of the COBRA clay degassing system. That is why the previous liquid ring vacuum pump on the second extrusion press has now been replaced by a COBRA clay degassing system.