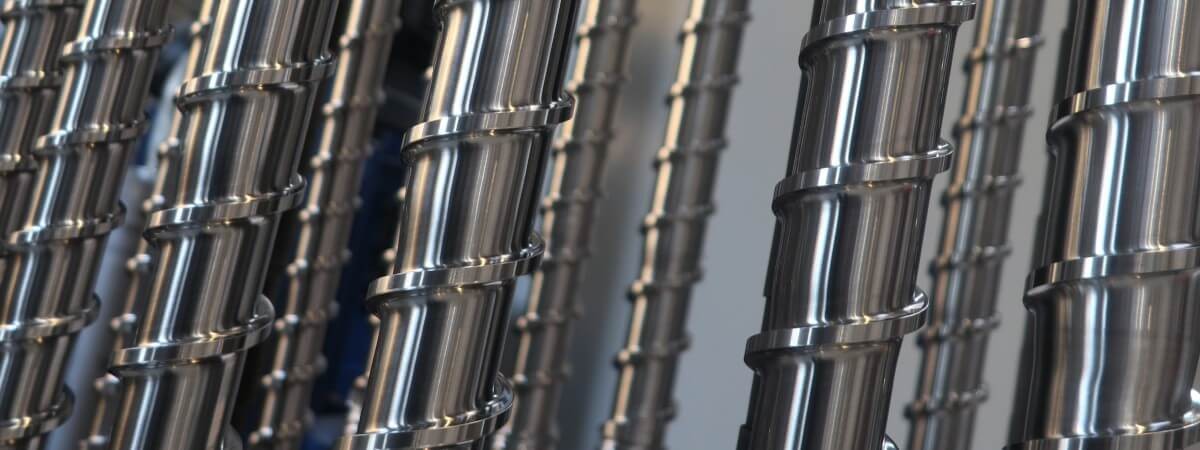
Fig. 1: Plasmanitrierte Extruderschnecken für die Arc-PVD-Beschichtung vorbereitet. Source: Busch Vacuum Solutions.
Schrauben-Vakuumpumpe zur Arc-PVD-Beschichtung
Die Oberflächenveredelung von großen metallischen Werkzeugen und Komponenten ist das Kerngeschäft der Firma Dreistegen GmbH. Dabei werden verschiedene Randschichtdiffusionsverfahren, wie Nitrieren, Nitrocarburieren oder Oxidieren, und Beschichtungsverfahren, wie physikalische Gasphasenabscheidung (PVD) und chemische Gasphasenabscheidung (CVD) unter Ausnutzung von kalten Plasmen angewandt. Beim Aufbringen von harten Dünnschichten durch Lichtbogenverdampfung (Arc-PVD) unter Vakuum verlässt sich Dreistegen auf eine COBRA NC Schrauben-Vakuumpumpe von Busch Vacuum Solutions. Diese generiert als Vorpumpe zusammen mit zwei parallel geschalteten Turbomolekular-Vakuumpumpen das Vakuum in der Beschichtungskammer.
Im Jahr 2008 machte sich Dr. Oliver Kayser in den Gebäuden einer alten Textilfabrik in Monschau in der Eifel selbstständig. Er erweckte die bis zu 200 Jahre alten Industriegebäude zu neuem Leben und befasste sich zu Beginn hauptsächlich mit der Plasmanitrierung und der PVD-Beschichtung von Werkzeugen und Komponenten. Was in teilweise ruinösen Gebäuden klein entstand, hat sich inzwischen zu einem modernen mittelständischen Betrieb mit 40 Mitarbeitern entwickelt, der Werkstücke mit speziellen Dünnschichten versieht, um diese vor Verschleiß und Korrosion zu schützen. Außerdem können diese Beschichtungen dazu beitragen, dass sich auf den Oberflächen keine Beläge bilden. Parasitäre Reaktionen mit anderen Materialien werden so vermieden. Viele der Kunden von Dreistegen kommen aus dem Bereich Kunststoffverarbeitung und lassen Spritzgieß-, Extruder- oder Blasformwerkzeuge beschichten. Hierfür hat Dr. Oliver Kayser eine spezielle Beschichtung entwickelt, die eine katalytische Stimulation der Werkzeugoberfläche auf die Zersetzung von plastifiziertem Kunststoff verhindert. Dadurch haftet der Kunststoff nicht an der Form. Dies bedeutet für den Betreiber: Schnelle Material- und Farbwechsel beim Extrudieren oder Spritzgießen sind möglich. Zudem kann Trennmittel eingespart oder ganz darauf verzichtet werden.
Außerdem beschichtet Dreistegen Umform- und Druckgusswerkzeuge vor allem für die Automobilindustrie und deren Zulieferer. Insgesamt bietet Dreistegen verschiedene Nitrierverfahren, PVD- und CVD-Beschichtungen sowie Polituren an. Dr. Oliver Kayser beschäftigt sich intensiv mit modernen Beschichtungstechnologien und experimentiert stets an der Optimierung von dünnen Schichten, um ihnen spezifische Eigenschaften zu verleihen, die für bestimmte Anwendungen Vorteile für den Kunden generieren. Hierzu gehört auch, die Anlagentechnik zu optimieren.
An einer am Markt bezogenen Arc-PVD-Beschichtungsanlage mit einem nutzbaren Drehdurchmesser von 1.200 und einer Nutzhöhe von 1.500 Millimetern war ursprünglich ein Vakuumsystem mit einer ölgeschmierten Drehschieber-Vakuumpumpe als Vorpumpe und zwei Vakuum-Boostern installiert. Dieses System erzeugte den notwendigen Unterdruck für die zwei parallel arbeitenden Turbomolekular-Vakuumpumpen. Diesen kompletten Vorvakuum-Pumpstand hat Kayser mit einer COBRA NC 400 B von Busch ersetzt. Die Schrauben-Vakuumpumpe erreicht einstufig einen Enddruck von 0,05 mbar (hPa). Damit kann sie den zuvor eingesetzten dreistufigen Pumpstand eines anderen Herstellers in punkto Enddruck und Saugvermögen ersetzen und ist dabei wesentlich energieeffizienter.
Kayser schätzt an der COBRA NC die stabile und zuverlässige Leistung sowie ihre Laufruhe. Außerdem ist der Platzbedarf im Vergleich zum zuvor eingesetzten Vakuumsystem wesentlich geringer.
-
Fig. 2: Anlage zur Arc-PVD-Beschichtung mit einer COBRA NC Schrauben-Vakuumpumpe als Vorpumpe für zwei Turbomolekular-Vakuumpumpen. Source: Busch Vacuum Solutions.
Kayser hat sich auch mit Schrauben-Vakuumpumpen eines anderen Fabrikats auseinandergesetzt. Diese hatten eine einseitige Lagerung und wurden durch einen speziellen Motor angetrieben, der nicht einfach zu wechseln war.
An der COBRA schätzt Kayser den modularen, funktionalen Aufbau mit beidseitiger Lagerung der beiden Schraubenrotoren und den Antrieb durch einen angeflanschten Standardmotor, der jederzeit austauschbar ist.
Der eigentliche Arc-PVD-Prozess dauert vom Beladen der Beschichtungskammer bis zum Entnehmen der Werkstücke zwischen 14 und 18 Stunden. In den kurzen Pausen zwischen zwei Prozessen zur Bestückung und Entnahme der Werkstücke bleibt die COBRA NC Vakuumpumpe in Betrieb. Das bedeutet, dass die COBRA NC das ganze Jahr über durchläuft.
Für Kayser ist die jetzige Lösung zum Erzeugen des Prozessvakuums in seiner Beschichtungsanlage mit der Kombination aus einer COBRA NC Schrauben-Vakuumpumpe und zwei parallel nachgeschalteten Turbomolekular-Vakuumpumpen die ideale Lösung.
Das Grundmaterial der Werkstücke muss bereits eine gewisse Oberflächenhärte aufweisen, bevor es Arc-PVD-beschichtet wird. Deshalb werden bei Dreistegen in aller Regel die zu beschichtenden Werkstücke zuvor plasmanitriert.
Die plasmanitrierten Werkstücke werden dann mit Glasperlen gestrahlt oder bei Bedarf leicht poliert. Nach der Reinigung der Werkstücke werden diese auf Halterungen fixiert und die Beschichtungskammer damit beladen. Die geschlossene Kammer wird dann auf ein Vakuumniveau von 10-5 mbar (hPa) evakuiert. Danach werden die Werkstücke in der Kammer auf bis zu 450° C erwärmt.
Nach dem Erreichen der Prozesstemperatur erfolgt der Abtrag der natürlichen Oxide in einem Argon-Glimmentladungsplasma. Im Anschluss werden die Lichtbogenverdampfer gezündet. Dabei können sich die Lichtbögen bewegen. Sie bleiben jedoch durch rückseitig angebrachte Permanentmagnete an die Spendermaterialien aus Titan, Chrom oder deren Legierungen gebunden. Auch Legierungen aus Aluminium oder anderen Metallen werden verwendet. Im Lichtbogen wird das Spendermaterial explosionsartig verdampft, und die einzelnen Dampfteilchen werden nahezu hundertprozentig ionisiert. Durch die elektrische Vorspannung (BIAS) erfolgt ein Bombardement der Ionen auf die Werkstücke. Zusätzlich werden Reaktionsgase wie Stickstoff, Acetylen, Methan, Sauerstoff, Wasserstoff und andere zugeführt. Das Zuführen der Gase sorgt für einen Anstieg des Drucks in der Beschichtungskammer auf 10-2 mbar (hPa). Die im Plasma zerlegten Reaktionsgase verbinden sich auf der Oberfläche der Werkstücke mit den Metallionen zu schichtbildenden Hartstoffen. Typische Verbindungen dabei sind Titannitrid (TiN), Titancarbonitrid (TiCN), Chromnitrid (CrN), Aluminium-Titan-Nitrid (AlTiN) oder Chromoxid (Cr2O3). Aufgrund der hohen Teilchenenergien und der Streufähigkeit entsteht eine äußerst haftfeste und gleichmäßige Beschichtung auch bei Werkstücken mit komplexer Geometrie. Die mittels Lichtbogenverdampfen bei Dreistegen erzeugten dünnen Schichten weisen durchweg Härten von mehr als 2.000 HV (Vickershärte) auf.
Die Wartungsarbeiten am Vakuumsystem sind durch den Einsatz der COBRA NC Schrauben-Vakuumpumpe gegenüber dem ursprünglich eingesetzten Pumpstand erheblich reduziert worden.
Nur ein jährlicher Getriebeölwechsel ist an der Schrauben-Vakuumpumpe durchzuführen.
Dr. Oliver Kayser betont, dass die absolute Betriebssicherheit der Schrauben-Vakuumpumpe für ihn sehr wichtig ist.
Ein Ausfall der Vakuumpumpe während des Prozesses würde einen enormen Schaden anrichten, da die hochwertigen Werkstücke hierdurch unbrauchbar würden.
Nach zweijähriger ununterbrochener Betriebszeit der COBRA NC sagt Dr. Oliver Kayser:
Wir bei Dreistegen sind begeisterte Busch Kunden und von der Qualität der Maschinen überzeugt.