Forming, pressing and laminating with vacuum
Forming, pressing and laminating with vacuum. Popular processes used in many sectors of industry and in manufacturing technology. To join a wide variety of materials together. Or to bring them into a specific shape.
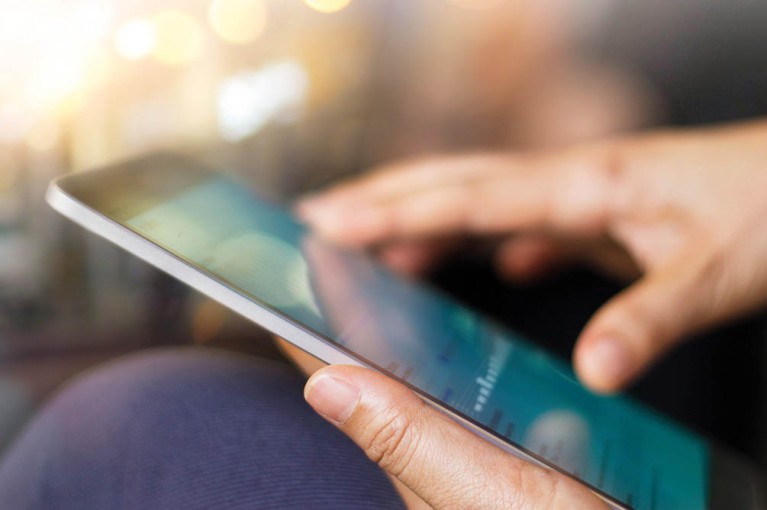
Busch vacuum technology in forming, pressing and laminating with Vacuum
No matter which materials are formed, pressed or laminated. Busch offers the optimum vacuum solution to create safe, visually appealing, and long-lasting end products.We at Dreistegen are happy Busch customers and are impressed by the quality of the machines.
Learn more about forming, pressing and laminating with vacuum
What is vacuum forming, pressing, and laminating?
Vacuum forming, pressing, and laminating uses the force of atmospheric air pressure to push, squeeze and bend things to their desired form. Everywhere around us, air is pressing in against us with a force equivalent to ten metric tons per every square meter. We do not feel it because we have the same force inside our bodies resisting it. But remove that pressure and you have a very effective press.
How does vacuum thermoforming work?
Vacuum thermoforming is the process of forming the plastic trays used in packaging food, electronic goods, toys, etc. The plastic is fed in as a sheet or foil and is heated to soften. Then vacuum is applied to push it tightly into a mold, where it sets to form the tray.
How does vacuum pressing work?
Vacuum pressing is used to form high density, three dimensional shapes. It can be used for many different materials. Vacuum is first applied to draw the raw material into the mold, and then the pressure of atmospheric air is used to compress it. An interesting example is cheese, where the whey is pressed out of the curds under vacuum.
How does vacuum laminating work?
Composite materials are made by forming strong fibers together in a resin to create a tightly bound mat. As with all gluing processes, this is strongest when tightly clamped to force out air bubbles. In vacuum laminating, the part is put in a bag which is then evacuated. This draws out the gases from within the composite. And applies the force of atmospheric air to clamp it tightly while it sets.
Does carbon fiber need to be vacuum pressed?
Sometimes, as a prepreg or in a bagging application, carbon fiber needs to be vacuum pressed. Vacuum pressing optimizes the fiber-resin ratio in the composite piece. And prevents air from getting trapped in layers. It also stops shifting during the orientation of the fiber.
What are the advantages of vacuum forming over injection molding?
There is more adaptability in terms of design in vacuum forming as opposed to injection molding. Speed of process is also quicker and tooling costs are lower. A wide range of prototypes can be produced at a faster pace and with more accuracy. Another advantage is the homogeneousness of the product surface. Furthermore, vacuum protects the products in the diesel process, thus preventing self-ignition of plastics or rubbers under high pressure and oxygen.
What are the advantages of vacuum pressing over mechanical pressing?
In vacuum pressing, the part that shall be pressed is enclosed in a bag which is compressed by the atmospheric pressure. This process is, for example, used for pressing several layers of different materials to achieve strongly fixed but yet lightweight parts. Another important advantage of vacuum pressing is the flexibility due the adaptability of the vacuum bag to the shape of the workpiece.
What are the advantages of vacuum laminating over mechanical laminating?
Vacuum laminating can be done in more complicated molds with undercuts. It can also be employed for large parts in a non-serial production. The vacuum laminating process, also called vacuum bagging, is more adaptable, sustainable, cost-effective as well as faster than mechanical laminating processes.
What are the best vacuum pumps for forming, pressing, and laminating?
The most suitable vacuum pumps depend on the specific application. In general, rotary vane vacuum pumps, claw vacuum pumps and screw vacuum pumps are the most common ones used for vacuum forming, pressing, and laminating.
What are the best vacuum pumps from Busch for the forming, pressing and laminating process?
R5 rotary vane vacuum pumps have been proven in forming applications for many years and are considered state-of-the-art. The energy-efficient MINK claw vacuum pump is used for pressing, for example, for producing furniture. If higher vacuum is required, R5 rotary vane vacuum pumps are the first choice. COBRA screw vacuum pumps are the preferred vacuum generators for laminating processes in the production of solar modules, flat panels and smartphone displays. They can discharge leaking gases and vapors without interference.
What are some examples for the use of Busch vacuum technology in forming, pressing, and laminating applications?
Busch vacuum technology is used in forming applications, including mold evacuation in the production of wind generator blades. Our solutions also play a role in thermoforming for producing packaging. In pressing applications,
Busch technology is used for attaching synthetic veneers to furniture surfaces and plays a role in Vacuum Assisted Resin Transfer Molding (VRTM). When it comes to laminating, Busch vacuum pumps are used in the production of flat panel displays, solar panels and mobile phone screens.
What are the key points to consider when buying a vacuum forming, vacuum pressing or vacuum laminating system?
The production batch time and the volume of the mold or form are major considerations when buying a vacuum forming, vacuum pressing or vacuum laminating system. Also, very important are the amount and characteristics of materials, i.e., hazardous solvents or air, and the required system pressure. However, there is no one-size-fits-all solution when buying a vacuum forming, vacuum pressing or vacuum laminating system. For purposes of designing the best solution for your needs, more general factors can also be taken into consideration:
Peace of mind
The best vacuum system is the one you never have to worry about. It should deliver the required performance. And run seamlessly and reliably. This is achieved by a combination of the right technology in a suitable skid integration. And the required protection and safety sensors. The correct operating procedures, including warm-up and shut-down cycles, are also key factors for trouble-free operation.
Safety
A vacuum forming, vacuum pressing, or vacuum laminating machine should never pose a danger to workers. This is especially important whenever explosive, flammable, and toxic compounds are being handled. In this case, the vacuum unit needs to comply with local explosion regulations such as ATEX, IECEX, Ex-Proof or KOSHA. The right level of leak-tightness is also crucial to prevent any seepage of toxic compounds. In this case, specific options such as double mechanical seals and barrier gases are recommended.
Cost of ownership
Focusing only on the initial investment costs is usually not the best way to optimize the total cost of ownership of a vacuum forming, vacuum pressing or vacuum laminating machine. Several other parameters must be considered: Mainly to choose the right technology and to adapt the system design. Relevant points to think about are the consumption of cooling water, operating fluid, flushing liquid or other. The frequency and cost of maintenance should also be considered. Finally, it is important to take a holistic look at the vacuum system. Pipes that are too small, for instance, can greatly impair the performance of the system.
Energy efficiency
The energy consumption of a vacuum forming, vacuum pressing, or vacuum laminating machine is a key selection factor. Depending on the operating pressure, different technologies can be considered. For low pressures and high-volume flows, a multi-stage design that includes vacuum boosters can be a cost- and energy-efficient solution. Additionally, the regulation of vacuum demand is key. Nowadays, most systems can be operated with a variable speed drive to reduce power consumption when vacuum demand is low.
Extended lifetime
To extend the lifetime of a vacuum system, several parameters should be considered. For example, the use of the right technology and the right pump configuration. Another consideration is the proper use of the system. In most cases, warm-up, and shutdown cycles are required to maintain performance at factory standards.
Money savings by system upgrade
Your process, including vacuum demand, may have changed. This leads to the questions: Is it still adapted to your needs? Is it still operating as energy-efficiently as possible? When it is time to upgrade or replace a vacuum system, it is worth looking at the entire installation. Try to identify any potential for optimization. Modern technologies can save money by reducing operating fluids and energy consumption.
Process gas
Depending on the composition of the process gas, it may be valuable to recover or neutralize it. A dry solution, for instance, allows the recovery of non-contaminated process gas at the exhaust of the vacuum pump.
Thermoforming Packaging
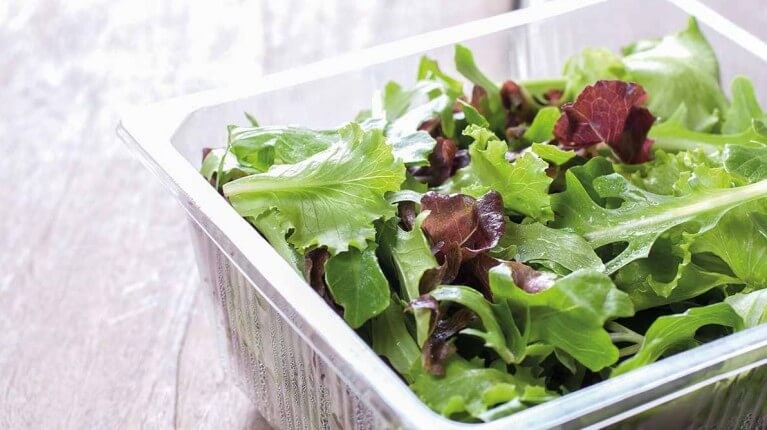
In thermoforming, plastic foils are heated to soften them. Vacuum is applied through the mold, and pulls the foil, which has been softened, into the mold. Once the foil has cooled down, it keeps its new shape. The products to be packaged can now be filled in.
Thermoforming of plastics
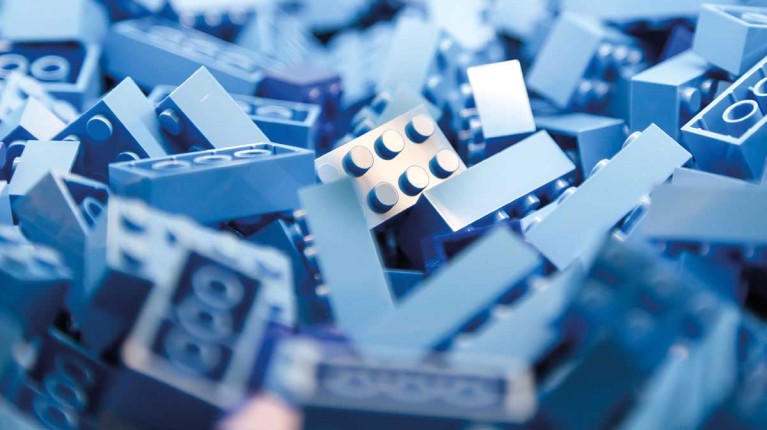
The plastic sheet is heated up in an oven until it is pliable. It can then be stretched into a mold using vacuum. Once brought into the desired shape, it keeps the specific shape of the mold. The thermoformed plastic part is trimmed and becomes a usable product. For example, a plastic toy, a surface part for the interior of a car or any kind of prototype part.
Lamination and veneer pressing of wood
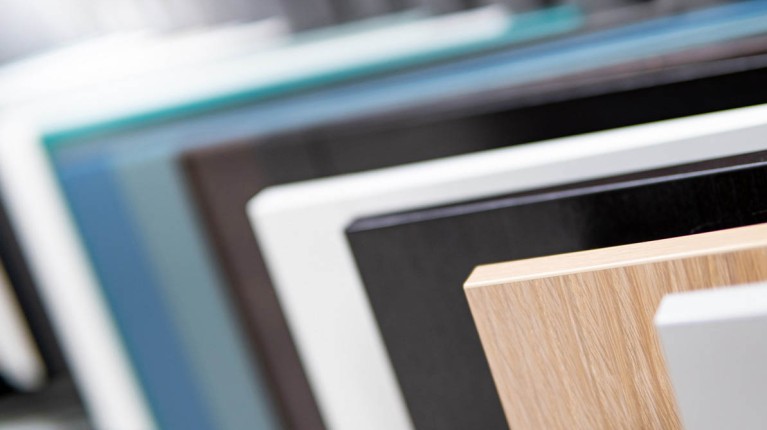
The aim of these applications is that the plastic coating or veneer fits perfectly and keeps this shape. Therefore, the right vacuum level and the choice of the perfect vacuum generator are extremely important to ensure that the coating is not damaged during the process.
Solar panel lamination
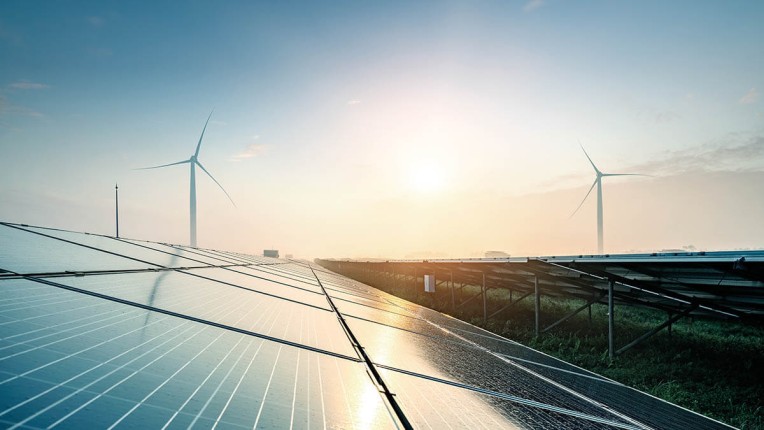
To protect solar modules from stress and weather, the cells are enclosed between glass panes or foils. The laminating process, also called encapsulation, takes place under vacuum. The use of vacuum ensures that the air between the layers that are glued together is entirely removed. And thus ensures a long lifetime of the modules by preventing air bubble formation, delamination and cell breakage.