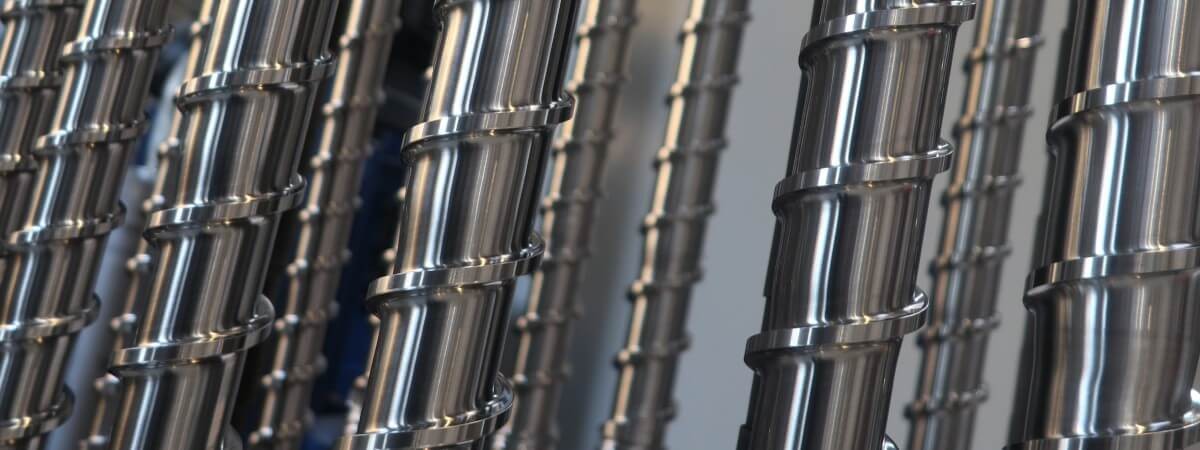
Рис. 1. Винт экструдера после плазменного азотирования, подготовленный к технологическому процессу нанесения покрытия методом дуговой конденсации из паровой фазы. Источник: Busch Vacuum Solutions.
Винтовой вакуумный насос для нанесения покрытия методом дуговой конденсации из паровой фазы
Основа бизнеса компании Dreistegen GmbH — чистовая обработка поверхностей крупных металлических инструментов и компонентов. Для обработки используются различные диффузионные способы нанесения покрытий, например азотирование, нитроцементация и окисление, а также конденсация из паровой фазы (PVD) и химическое осаждение из паровой фазы (CVD) с использованием холодной плазмы.
Для нанесения тонких закаленных слоев методом дугового испарения (дуговая конденсация из паровой фазы) в условиях вакуума в Dreistegen используется винтовой вакуумный насос COBRA NC производства Busch Vacuum Solutions. Будучи форвакуумным насосом, он работает с двумя параллельными турбомолекулярными вакуумными насосами, с помощью которых генерируется вакуум в камере для нанесения покрытия.
В 2008 году д-р Оливер Кайзер (Oliver Kayser) основал собственный бизнес в зданиях старой текстильной фабрики в городе Моншау (регион Эйфель, Германия). Старое промышленное здание, построенное 200 лет назад, было возвращено к жизни Кайзером, который начал свой бизнес с плазменного азотирования и нанесения покрытий на инструменты и компоненты методом PVD. Сегодня некогда скромное предприятие, основанное в обветшавших зданиях, выросло в современную компанию среднего размера с 40 сотрудниками, которые занимаются нанесением специальных тонких покрытий, обеспечивающих защиту от износа и коррозии, на обрабатываемые изделия. Более того, эти покрытия защищают поверхности от образования наростов. В результате исключается риск возникновения паразитных реакций с другими материалами. Многие заказчики компании Dreistegen занимаются обработкой пластмасс и заказывают у Dreistegen покрытия для инструмента, получаемые методом литья под давлением, экструдирования или литья с раздувом. Д-р Оливер Кайзер разработал специальную форму покрытия, защищающего каталитическую поверхность инструмента от разрушения при контакте с расплавленной пластмассой. В результате пластмасса не прилипает к литому покрытию. С точки зрения оператора это является возможностью быстро менять материал и цветовой оттенок при использовании метода экструзии или литья под давлением. При этом сокращается объем используемой литейной технологической смазки, а в отдельных случаях смазка полностью исключается из процесса.
Компания Dreistegen также наносит покрытия на инструменты для формования и формы для литья, главным образом для автомобильной промышленности и поставщиков автомобильных компонентов. Dreistegen предлагает целый ассортимент решений для азотирования, нанесения покрытий методами PVD и CVD и чистовой обработки.
Д-р Оливер Кайзер постоянно изучает современные технологии нанесения покрытий и тестирует различные методы оптимизации тонкослойных покрытий для придания им особых свойств, обеспечивающих преимущества для заказчиков в конкретных областях применения. При этом совершенствуется технология, которая используется на его производстве.
Приобретенная компанией система нанесения покрытия методом дуговой конденсации из паровой фазы с рабочим диаметром поворота 1200 mm и рабочей высотой 1500 mm изначально была оснащена вакуумной системой с масляным пластинчато-роторным вакуумным насосом, который использовался в качестве форвакуумного насоса, и двумя двухроторными бустерными вакуумными насосами Рутса. Эта система генерировала вакуум, необходимый для параллельной работы двух турбомолекулярных вакуумных насосов. Кайзер заменил всю форвакуумную установку агрегатом COBRA NC 400 B компании Busch. Винтовой вакуумный насос обеспечивает предельное остаточное давление 0,05 mbar (hPa) посредством одной ступени. Он способен заменить старый трехступенчатый вакуумный агрегат другого производителя и обеспечить те же показатели предельного остаточного давления и скорости откачки при меньших затратах энергии.
Кайзер высоко оценил стабильность характеристик, эксплуатационную надежность и практически бесшумную работу насоса COBRA NC. Более того, в сравнении с предыдущей вакуумной системой этот насос занимает гораздо меньше пространства.
-
Рис. 2. Система для нанесения покрытия методом дуговой конденсации из паровой фазы с винтовым вакуумным насосом COBRA NC в качестве форвакуумного насоса для двух турбомолекулярных вакуумных насосов. Источник: Busch Vacuum Solutions.
Кайзер также тщательно изучил характеристики винтовых вакуумных насосов других производителей. В них использовалась односторонняя система подшипников, и они приводились в движение специальным двигателем, который было трудно заменить.
Д-ру Кайзеру очень понравилась модульная, функциональная конструкция насоса COBRA с двусторонней системой подшипников на двух винтовых роторах и со стандартным легко заменяемым двигателем с монтажным фланцем.
С момента загрузки камеры для нанесения покрытия до извлечения обрабатываемых изделий процесс дуговой конденсации из паровой фазы занимает приблизительно 14–18 часов. Вакуумный насос COBRA NC продолжает работать в периоды коротких перерывов между двумя процессами, когда осуществляется сборка и удаление обрабатываемых изделий. Это означает, что насос COBRA NC работает круглый год. Нынешняя система генерации технологического вакуума в установке нанесения покрытия, состоящая из комбинации винтового вакуумного насоса COBRA NC и двух параллельных турбомолекулярных вакуумных насосов, расположенных ниже по технологическому потоку, представляется д-ру Кайзеру оптимальным решением.
Перед тем как подвергнуть изделие обработке методом дуговой конденсации из паровой фазы поверхности основного материала этого изделия необходимо придать определенную твердость. Для этого перед нанесением покрытия специалисты Dreistegen осуществляют подготовку обрабатываемых изделий с помощью плазменного азотирования.
Затем азотированные таким образом обрабатываемые изделия подвергаются дробеструйной обработке с помощью стеклянной дроби либо слегка полируются. После очистки обрабатываемые изделия крепятся в держателях и загружаются в камеру для нанесения покрытия. После этого закрытая камера вакуумируется до уровня 10–5 mbar (hPa). Далее обрабатываемые изделия, находящиеся в камере, нагреваются до максимальной температуры 450 °C.
После достижения температуры процесса натуральные оксиды вытравливаются в аргоновой плазме тлеющего разряда. Далее дуговые испарители разжигаются и могут перемещаться. Однако под действием постоянных магнитов, закрепленных в задней части, они остаются в контакте с донорским материалом (титаном, хромом или их сплавами). В процессе также можно использовать алюминиевые сплавы и другие металлы.
В условиях дуги в результате взрывного процесса донорский материал преобразуется в пар, и отдельные частицы этого пара практически полностью ионизируются. Для распределения ионов на обрабатываемом изделии применяется метод электрического зажигания (BIAS). В процессе также добавляются реактивные газы, такие как азот, ацетилен, метан, кислород и водород. Добавление этих газов приводит к повышению давления в камере для нанесения покрытия до 10-2 mbar (hPa). Реактивные газы, выделяемые из плазмы, смешиваются с ионами металла на поверхности обрабатываемого изделия; в результате образуются слои твердого покрытия. К стандартным компаундам относятся нитрид титана (TiN), карбонитрид титана (TiCN), нитрид хрома (CrN), нитрид сплава титана и алюминия (AlTiN) и оксид хрома (Cr2O3). Благодаря высокой энергии и мощности вбрасывания частиц обеспечивается исключительная однородность и превосходные адгезивные свойства покрытия даже на обрабатываемых изделиях сложной формы. Тонкие слои, которые создаются на установке Dreistegen с помощью дугового испарения, обладают твердостью более 2000 VHN (твердость по Виккерсу).
В сравнении с оригинальными вакуумными блоками объем работ по техническому обслуживанию вакуумной системы значительно меньше; сокращение работ достигается за счет использования винтовых вакуумных насосов COBRA NC.
Единственное мероприятие, которое ежегодно требуется выполнять на винтовом вакуумном насосе, — это замена трансмиссионного масла.
Д-р Оливер Кайзер подчеркивает особенно важное для него преимущество — высочайший уровень эксплуатационной надежности винтовых вакуумных насосов. Выход вакуумного насоса из строя во время технологического процесса привел бы к существенному ущербу — необратимому повреждению дорогостоящих обрабатываемых изделий.
Спустя два года бесперебойной эксплуатации насосов COBRA NC д-р Оливер Кайзер делится своими впечатлениями:
«Мы — компания Dreistegen — весьма довольны сотрудничеством с Busch и качеством установленных машин».