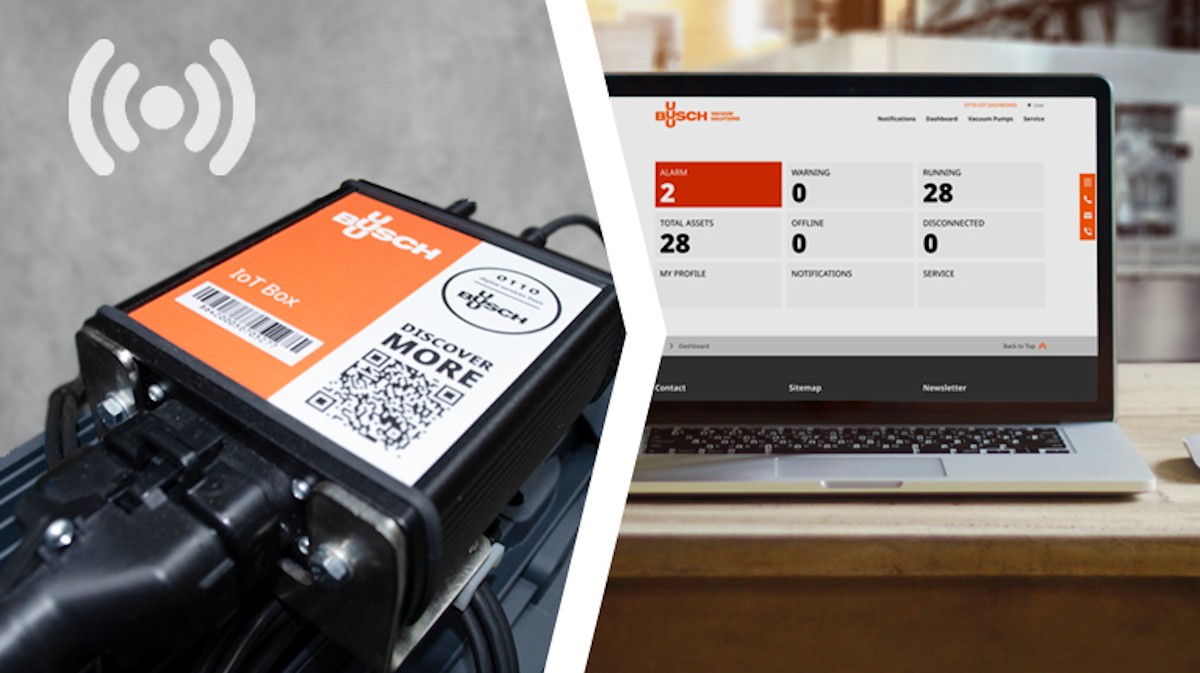
Источник: Busch Vacuum Solutions.
Семь способов сократить простой производства
Простои производства — один из самых больших рисков в обрабатывающей промышленности. При отказе оборудования или нехватке сырьевых материалов любые простои могут привести к значительным потерям дохода и доли рынка.
Плановый простой — это плановый останов производственного оборудования или процесса для выполнения технического обслуживания, проверок, ремонта, модернизации или производственных настроек. Чтобы поддерживать оборудование в оптимальном состоянии и исключить неплановые простои, необходимо планировать остановы для технического обслуживания. Плановые простои прерывают производственный процесс, однако контроль над процессом сохраняется.
Неплановые простои возникают при неожиданном останове или отказе производственного оборудования или технологического процесса. Такой останов приводит к порче пищевых продуктов, если они не упакованы, к дорогостоящим задержкам в производстве и увеличению сроков доставки. Кроме того, при нестабильной работе сложнее соблюдать природоохранное законодательство и выполнять программы по устойчивому развитию. В результате возникает риск увеличения количества экологических инцидентов.
Таким образом, предотвращение простоев производственных линий является ключевым фактором обеспечения производительности.
Мы предлагаем семь рекомендаций, которые позволят сократить время простоя оборудования производственной линии.
1. Разработайте систему быстрого выявления и решения производственных проблем
-
Источник: Busch Vacuum Solutions.
2. Используйте упреждающую аналитику для выявления потенциальных проблем до их возникновения
-
Источник: Busch Vacuum Solutions.
3. Внедрите программы профилактического технического обслуживания
Вы можете регулярно собирать ценную информацию о своем оборудовании для целей систематического технического обслуживания. При правильном целенаправленном техническом обслуживании появляется возможность своевременно реагировать на прогнозируемые отказы оборудования или аварийные ситуации до их возникновения. Уменьшив вероятность непредвиденных простоев, сотрудники могут сосредоточиться на конкретных производственных задачах.
-
Источник: Pieman Khrutmuang — stock.adobe.com.
4. Создайте систему обработки сбоев и отказов по мере их возникновения
-
Источник: Busch Vacuum Solutions.
5. Автоматизируйте как можно больше процессов, чтобы сократить количество ошибок оператора
Это позволит вашим сотрудникам сосредоточиться на профильных задачах, приносящих прибыль, и развивать профессиональные навыки, благодаря которым будет повышаться рентабельность производства, а ваши сотрудники станут самым ценным ресурсом вашей компании.
-
Источник: Gorodenkoff — stock.adobe.com.
6. Обучите операторов правилам эксплуатации оборудования
-
Источник: Busch Vacuum Solutions.
7. Используйте интеллектуальные решения в области IoT (интернет вещей)
Интеллектуальные IoT-решения помогают сократить время простоя за счет увеличения скорости выявления и устранения производственных проблем (рекомендация 1). Благодаря средствам предупредительной аналитики такие решения позволяют отслеживать состояние оборудования, контролировать параметры технологического процесса и заранее разрабатывать график технического обслуживания и заказывать необходимые запасные части (рекомендация 2). Датчики и средства аналитики данных позволяют системам IoT непрерывно следить за технологическим процессом и контролировать параметры производительности и оптимизации процесса и оборудования. Это дает возможность проводить профилактическое техническое обслуживание (рекомендация 3) и прогнозировать потенциальные проблемы по мере их возникновения (рекомендация 4), а значит значительно уменьшать частоту плановых и неплановых простоев. Решения IoT также позволяют автоматизировать задачи и сокращать время, необходимое для их выполнения, что в конечном итоге приводит к росту производительности и уменьшению количества ошибок оператора (рекомендация 5). Благодаря удобству использования инструментов операторы легко обучаются методам эксплуатации систем IoT. Ваши сотрудники в кратчайшие сроки смогут начать работать с системой (рекомендация 6). Хотите оптимизировать процесс с помощью системы IoT? Узнайте, как информационная панель Busch IoT и приложение Busch Vacuum App могут помочь вам в контроле процесса вакуумирования! Кроме того, Busch обеспечивает профилактическое обслуживание, при необходимости автоматически направляя специалиста по обслуживанию на основании анализа собранных данных.
Часто задаваемые вопросы
Что такое простой производства?
- Простой — это период остановки производственного процесса. Существует два типа простоев: плановые и неплановые.
- Плановый простой — это плановое отключение производственного оборудования для проведения технического обслуживания, проверки, ремонта и модернизации.
- Неплановый простой — это неожиданные остановы или сбои в работе производственного оборудования или технологического процесса.
Как вычисляется простой производства?
Для расчета затрат, связанных с простоем производства, используйте следующее уравнение:
время простоя % = (время простоя в числовом выражении/запланированное время эксплуатации) * 100
Каковы средние простои производства?
Средние потери времени в результате простоя оборудования составляют 800 часов в год или более 15 часов в неделю.
Рассмотрим общий сценарий для сыроварни:
Средняя масса блока сыра пармезан составляет 42 кг. Ориентировочная цена за килограмм составляет 9 евро, следовательно один блок сыра стоит 378 евро. Линия производит три сырных блока в минуту, то есть за один час производится сыра на сумму 68 040 евро.
Если из-за отказа оборудования сыроварня внепланово простоит 15 часов в течение одной недели, потеря прибыли составит 1 020 600 евро.