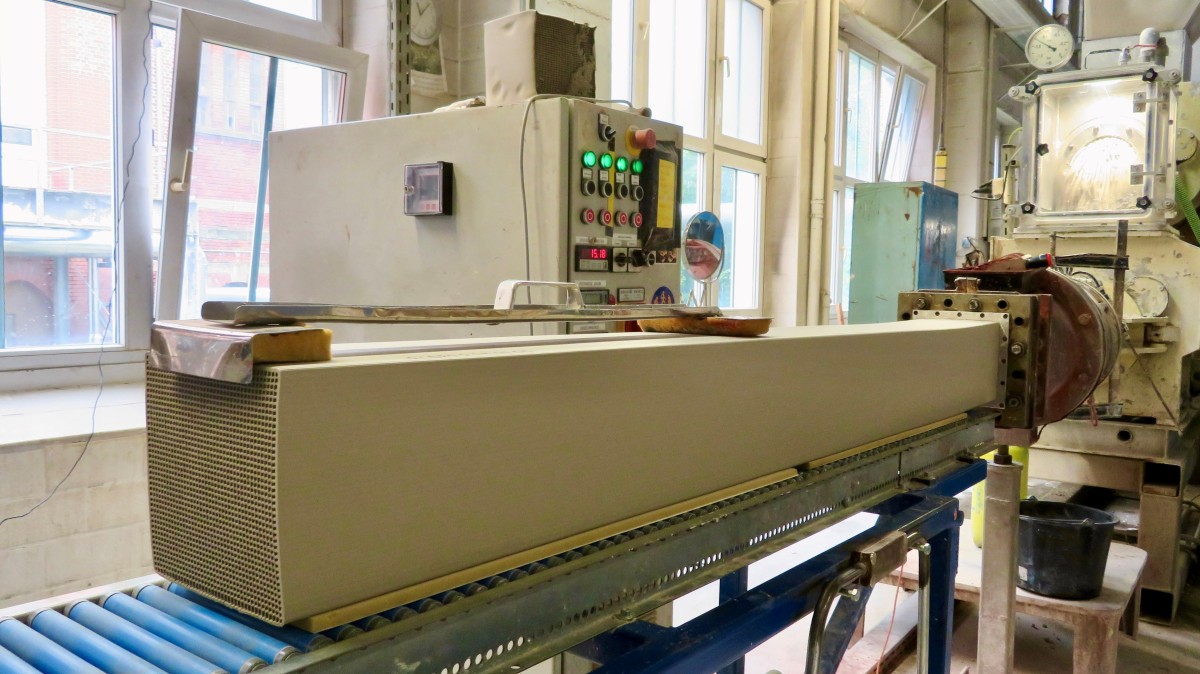
Los cuerpos alveolares reciben sus finos orificios y paredes delgadas mediante una plantilla detrás de la prensa de tornillo. Foto: Busch Vacuum Solutions.
Menos esfuerzo de mantenimiento gracias a la generación de vacío avanzada
Porzellanfabrik Hermsdorf GmbH, Alemania
En la fábrica de porcelana de Hermsdorf en Turingia, dos sistemas de vacío estándar de Busch Vacuum Solutions demuestran que todo es posible gracias a una mayor calidad, menos mantenimiento y menores costes. Allí se utilizan para la desgasificación de extrusora.
La cerámica industrial se produce en Hermsdorf, cerca de Jena, desde 1890. En el pasado, aisladores de alta tensión; ahora, cuerpos alveolares de cerámica para intercambiadores de calor, sistemas de ventilación y de control de emisiones. Para ello, siempre se han mantenido al día, desarrollando materiales, productos y procesos de fabricación innovadores y de última generación. De la misma forma que los dos nuevos sistemas de vacío SIMPLEX de Busch que se utilizan para desgasificar la masa cerámica. En 2021, estas sustituyeron a cuatro bombas de vacío de paletas rotativas lubricadas con aceite y, desde entonces, han suministrado el vacío necesario a cuatro líneas de extrusión. Actualmente, más de 100 empleados trabajan en las históricas naves de la fábrica de porcelana.
1600 orificios, sin burbujas de aire
El hilo de cerámica de forma cuadrada, aún húmedo, se desliza suavemente hacia fuera de la prensa de tornillo. Pero después de 1,50 metros, la carrera ha terminado. A continuación, las manos inteligentes cortan la parte delantera y la colocan en un rack grande para que se seque. Lo hacen continuamente en tres turnos. Después de unos nueve días, cuando la masa solo contiene uno por ciento de humedad residual, los alvéolos se queman en un horno a 1200 grados. A lo largo de ellos pasan 1600 pequeños orificios como células alveolares, separados solo por paredes finas, todas precisas y simétricas. Para garantiza que esto siga así después del proceso de combustión, la masa no debe contener bolsas de aire. Estas se expandirían con el calor del horno y provocarían la explosión de todo el cuerpo alveolar. Por este motivo, la masa debe someterse a una desgasificación previa con sistemas de vacío SIMPLEX de Busch. El corazón de cada cuadro de control y depósito de vacío es una bomba de vacío de rotores de uña en seco MINK MV Synchro. Lo que otras bombas de vacío consideran como un reto, es decir, la manipulación de masas muy húmedas y pastosas, estas pueden dominarlo con facilidad. Justamente por eso se han desarrollado para la desgasificación de extrusoras.
El hilo de cerámica de forma cuadrada, aún húmedo, se desliza suavemente hacia fuera de la prensa de tornillo. Pero después de 1,50 metros, la carrera ha terminado. A continuación, las manos inteligentes cortan la parte delantera y la colocan en un rack grande para que se seque. Lo hacen continuamente en tres turnos. Después de unos nueve días, cuando la masa solo contiene uno por ciento de humedad residual, los alvéolos se queman en un horno a 1200 grados. A lo largo de ellos pasan 1600 pequeños orificios como células alveolares, separados solo por paredes finas, todas precisas y simétricas. Para garantiza que esto siga así después del proceso de combustión, la masa no debe contener bolsas de aire. Estas se expandirían con el calor del horno y provocarían la explosión de todo el cuerpo alveolar. Por este motivo, la masa debe someterse a una desgasificación previa con sistemas de vacío SIMPLEX de Busch. El corazón de cada cuadro de control y depósito de vacío es una bomba de vacío de rotores de uña en seco MINK MV Synchro. Lo que otras bombas de vacío consideran como un reto, es decir, la manipulación de masas muy húmedas y pastosas, estas pueden dominarlo con facilidad. Justamente por eso se han desarrollado para la desgasificación de extrusoras.
-
El sistema de vacío inteligente SIMPLEX VO de Busch realiza la desgasificación de la masa en la extrusora. Foto: Busch Vacuum Solutions.
Sin lodo
Las bombas de vacío de paletas rotativas lubricadas con aceite utilizadas anteriormente no soportaban bien las condiciones del proceso. "El aceite se convertía rápidamente en una emulsión con el vapor de agua condensado. Eran ruidosas, olían mal y los filtros estaban permanentemente obstruidos. Esto provocaba un desgaste excesivo y un fallo de la bomba. Una vez al mes teníamos que cambiar los filtros y el aceite, lo que era un trabajo encantadoramente lodoso», afirma Christian Ferber, director general de Porzellanfabrik Hermsdorf GmbH. Los nuevos sistemas de vacío SIMPLEX VO de Busch son completamente diferentes. No requieren aceite en la cámara de compresión y son prácticamente libres de mantenimiento, son silenciosos y tienen control de velocidad. Mientras que las bombas anteriores funcionaban constantemente y tenían que controlarse manualmente mediante válvulas de aire falso, los nuevos sistemas de vacío de Busch se adaptan automáticamente al nivel de vacío requerido y se desconectan cuando no se necesita vacío. «Al principio utilizamos un sistema de Busch para realizar pruebas y quedamos impresionados inmediatamente. Todavía estamos totalmente satisfechos con nuestros propios sistemas SIMPLEX. En cuestiones de mantenimiento, los nuevos sistemas facilitan mucho las cosas», afirma Christian Ferber.
Las bombas de vacío de paletas rotativas lubricadas con aceite utilizadas anteriormente no soportaban bien las condiciones del proceso. "El aceite se convertía rápidamente en una emulsión con el vapor de agua condensado. Eran ruidosas, olían mal y los filtros estaban permanentemente obstruidos. Esto provocaba un desgaste excesivo y un fallo de la bomba. Una vez al mes teníamos que cambiar los filtros y el aceite, lo que era un trabajo encantadoramente lodoso», afirma Christian Ferber, director general de Porzellanfabrik Hermsdorf GmbH. Los nuevos sistemas de vacío SIMPLEX VO de Busch son completamente diferentes. No requieren aceite en la cámara de compresión y son prácticamente libres de mantenimiento, son silenciosos y tienen control de velocidad. Mientras que las bombas anteriores funcionaban constantemente y tenían que controlarse manualmente mediante válvulas de aire falso, los nuevos sistemas de vacío de Busch se adaptan automáticamente al nivel de vacío requerido y se desconectan cuando no se necesita vacío. «Al principio utilizamos un sistema de Busch para realizar pruebas y quedamos impresionados inmediatamente. Todavía estamos totalmente satisfechos con nuestros propios sistemas SIMPLEX. En cuestiones de mantenimiento, los nuevos sistemas facilitan mucho las cosas», afirma Christian Ferber.
-
Los cuerpos alveolares secos esperan para ser despedidos. No contienen bolsas de aire que puedan explotar en el horno. Foto: Busch Vacuum Solutions.
De Hermsdorf al mundo
Dos sistemas estándar en seco con ahorro energético requieren muy poco mantenimiento y sustituyen a cuatro bombas antiguas lubricadas con aceite que requerían mucha energía y mantenimiento: «Gracias al buen asesoramiento que recibimos de Busch, hemos ahorrado 10.000 kWh al año. Desde la instalación, los dos sistemas de vacío han funcionado sin ningún problema. Sin comparación con las bombas anteriores», afirma Christian Ferber. Y gracias a la nueva solución de vacío de Busch, cada mes salen de la planta tradicional de Hermsdorf entre 80.000 y 90.000 cuerpos alveolares de alta calidad en diferentes formas y tamaños. Garantizan una recuperación de calor eficiente y aire limpio en sistemas de ventilación de casas pasivas o plantas de poscombustión en grandes buques de contenedores y cruceros en todo el mundo.
Dos sistemas estándar en seco con ahorro energético requieren muy poco mantenimiento y sustituyen a cuatro bombas antiguas lubricadas con aceite que requerían mucha energía y mantenimiento: «Gracias al buen asesoramiento que recibimos de Busch, hemos ahorrado 10.000 kWh al año. Desde la instalación, los dos sistemas de vacío han funcionado sin ningún problema. Sin comparación con las bombas anteriores», afirma Christian Ferber. Y gracias a la nueva solución de vacío de Busch, cada mes salen de la planta tradicional de Hermsdorf entre 80.000 y 90.000 cuerpos alveolares de alta calidad en diferentes formas y tamaños. Garantizan una recuperación de calor eficiente y aire limpio en sistemas de ventilación de casas pasivas o plantas de poscombustión en grandes buques de contenedores y cruceros en todo el mundo.