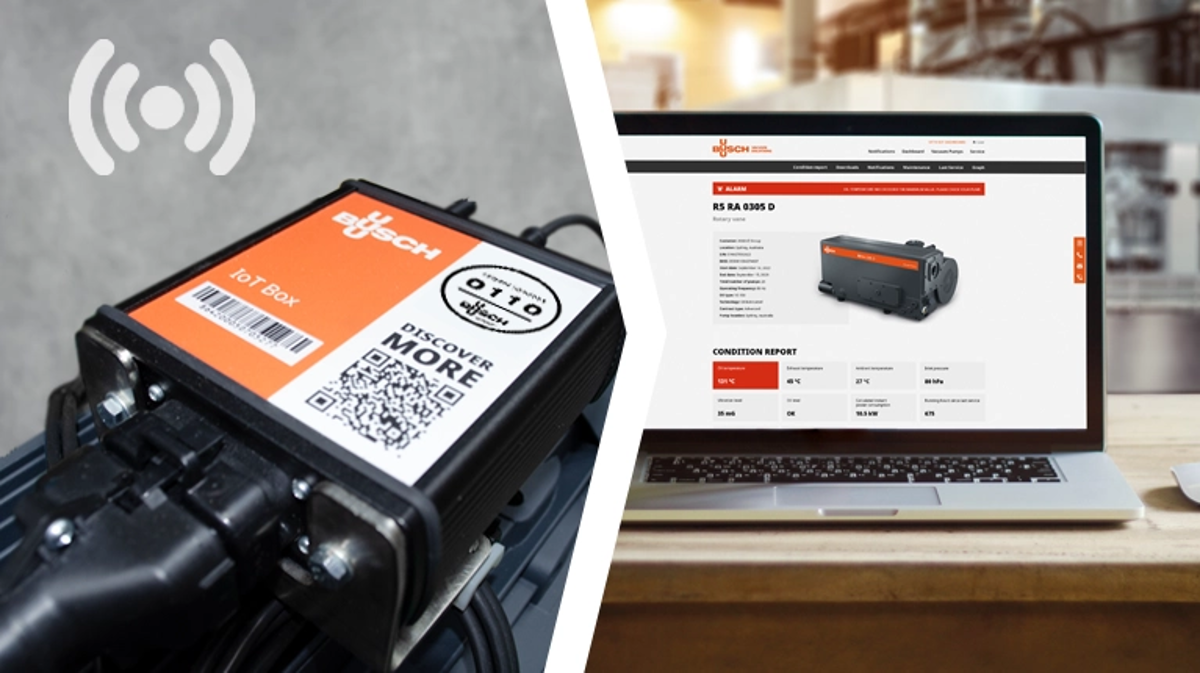
Fonte: Busch Vacuum Solutions.
7 modi per ridurre i tempi di fermata della produzione
I tempi di fermata della produzione rappresentano uno dei maggiori rischi nell'industria manifatturiera. Dai mancati funzionamenti delle apparecchiature alla carenza di materie prime, qualsiasi tempo di fermata della produzione può comportare notevoli perdite di ricavi e di quote di mercato.
Il tempo di fermata pianificato è un arresto programmato delle apparecchiature o dei processi di produzione per eseguire manutenzione, ispezioni, riparazioni, aggiornamenti o configurazioni di produzione. È fondamentale pianificare i tempi di fermata per la manutenzione al fine di mantenere le apparecchiature in condizioni ottimali ed evitare tempi di fermata non pianificati. Anche se i tempi di fermata pianificati interrompono il processo di produzione, si mantiene ancora il controllo dei processi produttivi.
I tempi di fermata non pianificati sono quelli che si verificano in caso di arresto imprevisto o mancato funzionamento delle apparecchiature o dei processi di produzione. Se non vengono confezionati, i prodotti alimentari e le bevande si deteriorano, così come si generano costosi ritardi nei programmi di produzione e consegna. Inoltre, l’instabilità delle operazioni rende più difficoltoso rispettare le normative ambientali e le misure di sostenibilità. Ciò potrebbe causare un aumento degli incidenti ambientali.
Pertanto, prevenire i tempi di fermata in produzione è fondamentale per garantire la produttività.
Seguite i nostri sette suggerimenti per ridurre i tempi di fermata delle macchine della vostra linea di produzione.
1. Sviluppare un sistema per individuare e risolvere rapidamente i problemi di produzione
-
Fonte: Busch Vacuum Solutions.
2. Utilizzare l'analisi predittiva per individuare potenziali problemi prima che si verifichino
-
Fonte: Busch Vacuum Solutions.
3. Implementare un programma di manutenzione preventiva
È possibile raccogliere regolarmente informazioni importanti sulle apparecchiature, in modo da poter realizzare un approccio sistematico alla manutenzione sistematica. Con la giusta manutenzione mirata, è possibile reagire a previsti mancati funzionamenti o incidenti delle apparecchiature prima che si verifichino. Riducendo la possibilità di tempi di fermata imprevisti, il personale può concentrarsi su attività più redditizie.
-
Fonte: Piman Khrutmuang - stock.adobe.com.
4. Creare un sistema per affrontare gli inconvenienti e i problemi man mano che si presentano
-
Fonte: Busch Vacuum Solutions.
5. Automatizzare quanti più processi possibile per ridurre l'errore umano
In questo modo il personale avrà più tempo per concentrarsi su attività redditizie e sviluppare le proprie competenze, il che si tradurrà in maggiori profitti per l’azienda e dimostrerà ai dipendenti che sono la risorsa più preziosa dell’azienda.
-
Fonte: Gorodenkoff - stock.adobe.com.
6. Formare gli operatori su come utilizzare correttamente le apparecchiature
-
Fonte: Busch Vacuum Solutions.
7. Utilizzare soluzioni IoT intelligenti
Le soluzioni IoT intelligenti contribuiscono a ridurre i tempi di fermata grazie a un sistema in grado di individuare e risolvere rapidamente i problemi di produzione (Suggerimento 1). Traccia e monitora le apparecchiature e i processi con l'analisi predittiva, consentendo di creare un piano di manutenzione e ordinare in anticipo le parti di ricambio necessarie (Suggerimento 2). I sensori e l'analisi dei dati consentono all'IoT di tracciare e monitorare continuamente i dati sulle prestazioni e sull'ottimizzazione dei processi forniti dalle apparecchiature. Ciò consente di effettuare la manutenzione preventiva (Suggerimento 3) e di prevedere i potenziali problemi man mano che si presentano (Suggerimento 4), riducendo efficacemente la frequenza dei tempi di fermata pianificati o non pianificati. L'IoT consente anche l'automazione delle attività, abbreviando il tempo necessario per completarle e, in ultima analisi, aumentando la produttività e riducendo gli errori umani (Suggerimento 5). Grazie ai suoi strumenti intuitivi, è facile imparare a utilizzare l'IoT. Il personale sarà in grado di utilizzarlo correttamente in pochissimo tempo (Suggerimento 6). Desiderate ottimizzare i vostri processi installando un sistema IoT? Scoprite come il Busch IoT Dashboard e la Busch Vacuum App possono aiutarvi nel monitoraggio del vostro processo del vuoto! Busch offre anche la manutenzione preventiva, inviando automaticamente uno specialista dell'assistenza in base all'analisi dei dati raccolti quando necessario.
FAQ
Che cos'è un tempo di fermata di produzione?
- Il tempo di fermata è il tempo durante il quale un processo di produzione viene interrotto. Esistono due tipi di tempi di fermata: pianificati e non pianificati.
- I tempi di fermata pianificati sono arresti programmati delle apparecchiature di produzione per eseguire manutenzione, ispezioni, riparazioni e aggiornamenti.
- I tempi di fermata non pianificati sono un arresto imprevisto o un mancato funzionamento delle apparecchiature o dei processi di produzione.
Come si calcolano i tempi di fermata della produzione?
I costi relativi ai tempi di fermata della produzione si calcolano in base al seguente parametro:
% dei tempi di fermata = (quantità di tempo di fermata/tempo di esercizio pianificato) * 100
Qual è il tempo medio di fermata della produzione?
Le aziende manifatturiere perdono in media 800 ore all'anno, o più di 15 ore settimanali, di tempo di produzione a causa dei tempi di fermata delle apparecchiature.
Consideriamo uno scenario comune per una fabbrica di formaggio parmigiano:
una forma di parmigiano pesa in media 42 kg. Il prezzo stimato è di 9 euro per chilogrammo, pari a una forma di parmigiano del valore totale di 378 euro. È possibile produrre tre forme di formaggio al minuto, per un totale di 68.040 euro all'ora.
Se il caseificio del parmigiano dovesse subire in una settimana 15 ore di tempo di fermata non pianificato a causa di un mancato funzionamento delle apparecchiature, perderebbe 1.020.600 euro.