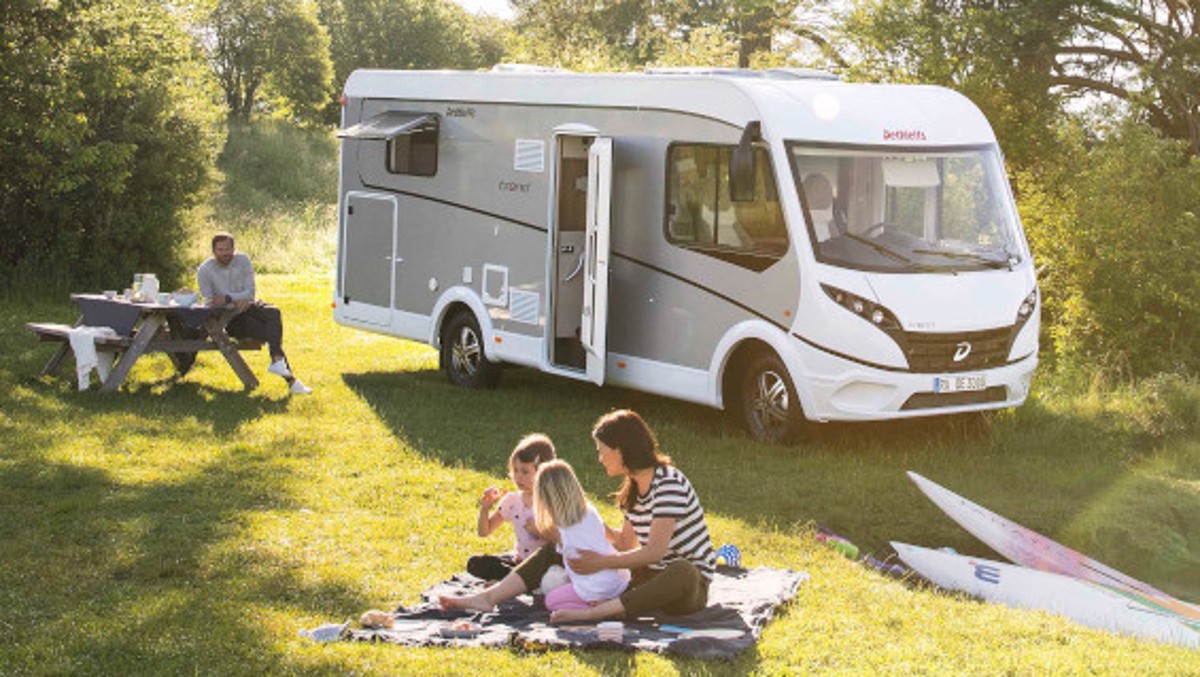
Fig. 1: The latest generation of the Dethleffs motor home. Source: Dethleffs GmbH & Co. KG.
Efficient Vacuum Supply for Motor Home Production
Dethleffs GmbH & Co. KG
The company Dethleffs GmbH & Co. KG produces a wide range of caravans and motor homes in a variety of sizes and designs for customers all over the world. Based in Isny in the Allgäu in Germany, Dethleffs recently found that its headquarters had reached their limit in terms of capacity.
So, the company decided to build a new production hall, where camper vans and urban vehicles have been manufactured since May 2018. It is equipped with five new CNC machining centers, where parts made from panel material are cut for the interior fittings in a more or less automated process.
All five machining centers are connected to a central vacuum supply from Busch. It supplies the vacuum needed to clamp the panels and individual parts using the nesting method.
So, the company decided to build a new production hall, where camper vans and urban vehicles have been manufactured since May 2018. It is equipped with five new CNC machining centers, where parts made from panel material are cut for the interior fittings in a more or less automated process.
All five machining centers are connected to a central vacuum supply from Busch. It supplies the vacuum needed to clamp the panels and individual parts using the nesting method.
Centralizing the vacuum supply has enabled Dethleffs to make sure parts are clamped reliably, while also saving the maximum possible amount of energy at the same time.
Production of camper vans and urban vehicles
The new production hall is home to the production facilities for timber attachment parts, a logistics center and warehouse, and the final assembly line (Fig. 2) for camper vans and urban vehicles. This means that all the production stages for these vehicles are completed in this hall, without any interaction with the other production halls.The timber parts production area manufactures various vehicle parts using veneer plywood for assemblies including kitchen units, seating areas, below-bed cupboards and raised cabinets.
- The individual parts in these assemblies are produced on five CNC routers that work in parallel and are joined in a logistical chain. This means that the only manual process required is the loading of the panel material into the five machines' feeding stations.
- The individual panels are automatically fed into the router on a belt.
- Prior to that, the shapes to be cut are created in a piece of software.
- Then each panel part is marked with a label so that it can be assigned to the right component or assembly location.
-
Fig. 2: The motor home assembly line. Source: Dethleffs GmbH & Co. KG.
The veneer plywood panels to be machined (Fig. 3) are the same size as the machining table, which has a cover board and then a protection board (both made from MDF) on top. This ensures that barely any "leak air" is drawn into the system.
-
Fig. 3: The panels to be machined are clamped on nesting tables. Source: Busch Vacuum Solutions.
Once the individual parts have been machined, a belt automatically transports them to a central unloading point along with any leftover pieces of panel (Fig. 4). At this point, the various individual parts are then removed manually and sorted for the next stages in the production process.
-
Fig. 4: The feeding station for the parts to be machined for the interior fittings. Source: Busch Vacuum Solutions.
Vacuum system solution from Busch
The decision to centralize the vacuum supply in this production hall was easy. Thomas Ballweg, a project engineer who helped to design the central vacuum system, was able to draw on the positive experience of the solution's reliability and economic efficiency at two sister companies. These two companies got rid of individual supply solutions with vacuum pumps installed directly in the machining centers a long time ago, switching instead to central vacuum systems from Busch. For Thomas Ballweg, his colleagues' experience at other production facilities merely confirmed his own research.Busch's centralized vacuum supply (Fig. 5) is very different to conventional vacuum supply solutions with dry-running rotary vane vacuum pumps installed directly on the machine. Firstly, are equipped with , which intrinsically consume less power than conventional dry-running rotary vane vacuum pumps with carbon blades and are nearly maintenance-free. This is down to the dry and contact-free operating principle.
Secondly, MINK claw vacuum pumps can be operated with frequency-controlled drives, which allow for demand-driven operation. Furthermore, centralizing the vacuum supply offers other benefits. In principle, the operator needs fewer vacuum pumps because not all of the five connected CNC routers will necessarily need full pumping speed at all times. The integrated control unit makes sure the individual MINK claw vacuum pumps adjust their speed to current demand.
-
Fig. 5: Busch's central vacuum system with MINK claw vacuum pumps. Source: Busch Vacuum Solutions.
The central vacuum system is installed one storey up, directly above the timber parts production line, and connected to the five CNC routers by a ring line. The operator selects a setpoint for the vacuum, which the control unit then maintains regardless of the pumping speed required. If no vacuum is needed for clamping on any of the routers (during a production break, for instance), all of the vacuum pumps switch off automatically and remain in standby mode.
However, the vacuum is maintained in the ring line so that it can be applied to the machining table again as soon as it is needed for clamping. The system is fully automatic and is based on a redundant design. This means that the individual vacuum pumps can be disconnected separately without interrupting active production with downtimes or having a negative influence on the pumping speed.
However, the vacuum is maintained in the ring line so that it can be applied to the machining table again as soon as it is needed for clamping. The system is fully automatic and is based on a redundant design. This means that the individual vacuum pumps can be disconnected separately without interrupting active production with downtimes or having a negative influence on the pumping speed.
If one of the vacuum pumps were to break down, you wouldn't notice a thing on the production line because the other vacuum pumps would compensate for the reduced pumping speed by increasing their own rotational speeds.
Installing the central vacuum system in a separate room saves space in the production hall while also avoiding noise and heat emissions at the work stations.
According to Thomas Ballweg's calculations, the added costs for the vacuum system when compared to a decentralized solution will be balanced out in three years based on the savings in energy costs alone.
On top of that, there are extra savings from the lack of wear parts that would have to be replaced regularly in dry-running rotary vane vacuum pumps, plus any costs for maintenance work and potential downtimes.
The pioneering spirit of company founder Arist Dethleffs lives on in the company to this day. It is reflected in the ongoing advancement of the model series, the countless innovations, and, of course, in the heart of the camping tradition: family. The company has been closely linked to the town of Isny in the Allgäu right from the outset and keeps its brand core closely in its sights with its position as a "friend of the family". Dethleffs is now a member of the Erwin Hymer Group.
According to Thomas Ballweg's calculations, the added costs for the vacuum system when compared to a decentralized solution will be balanced out in three years based on the savings in energy costs alone.
On top of that, there are extra savings from the lack of wear parts that would have to be replaced regularly in dry-running rotary vane vacuum pumps, plus any costs for maintenance work and potential downtimes.
About Dethleffs
"Not without my family!" was the decision made by Arist Dethleffs in 1931 when he designed Germany's first ever caravan, which he called the "Wohnauto" ("living car" in English). The ski pole and whip manufacturer created the design because he wanted his family to join him on his long business trips. Not many people in those days were familiar with the concept of free time. Family vacations were a privilege and the tourism trade was still in its infancy. The creation of the Dethleffs caravan marked the start of a new era, particularly for the company that eventually committed itself completely to caravan production followed by motor home production later on (Fig. 1).The pioneering spirit of company founder Arist Dethleffs lives on in the company to this day. It is reflected in the ongoing advancement of the model series, the countless innovations, and, of course, in the heart of the camping tradition: family. The company has been closely linked to the town of Isny in the Allgäu right from the outset and keeps its brand core closely in its sights with its position as a "friend of the family". Dethleffs is now a member of the Erwin Hymer Group.