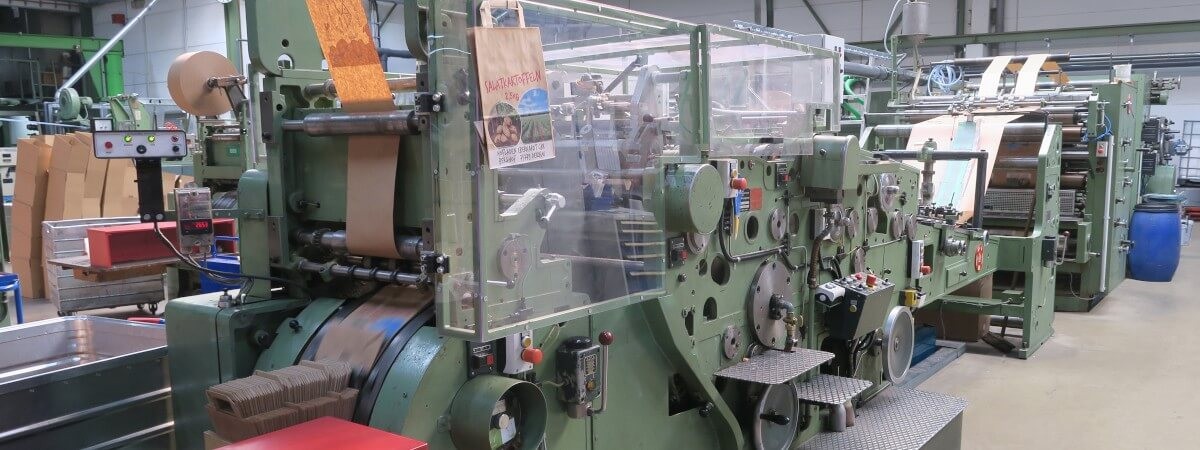
Fig. 1: One of the inline systems for paper bag production. Source: Busch Vacuum Solutions.
Advanced and Efficient Vacuum Supply in Paper Bag Production
GSD-Verpackungen
GSD-Verpackungen - Gerhard Schürholz GmbH is specialized in the production of paper bags and paper shopping bags. The majority of the processing machines requires vacuum to hold, transport and finish the individual bags.
GSD-Verpackungen has made energy savings of over 50% and reaped many other benefits for its advanced production systems by changing over from vacuum supply generated by individual vacuum pumps to the respective machines, to a centralized vacuum system from Busch.
About GSD-Verpackungen
GSD-Verpackungen was founded in Drolshagen in 1877 and has been owned by the Schürholz family since 1962. The family-owned business has specialized in the production of paper bags and paper shopping bags in small batches of 2,000 and above, and today supplies customers throughout Germany. 60% of goods produced go to discounters, supermarket chains and wholesalers, which in turn supply bakeries or butcher’s shops, for example.Complex special processing is also available in addition to standard sizes and designs. Elaborate print designs with up to eight colours can be created using a flexographic printing process. The company currently employs a total of 160 staff. Production runs five days a week, and – depending on the department – in either two or three-shift operation. GSD-Verpackungen carries out inline production with over 50 machines. This means that paper is delivered on rollers, and passes fully-automatically through all production steps from printing, to finishing, being formed (Fig. 1). The bags are stacked up ready to go at the end of the inline systems, and can be packaged immediately.
Process of paper handling and transport
Many of the machines for the paper bag production need vacuum for various processing or handling tasks. Vacuum is used to either hold or move paper, depending on the machine. In the past, a total of 22 rotary vane vacuum pumps of different sizes were in operation to generate vacuum. This was a thorn in the side of Production Manager Jörg Möller, because their heat emissions made the production hall hot and this worsened working conditions, particularly in summer months. It also meant high noise levels. The rotary vane vacuum pumps used were predominantly dry-running. This means they don’t use any oil for cooling and lubrication but were equipped with self-lubricating carbon vanes. Their abrasion released a fine carbon dust into the air, which was deposited around the vacuum pump. Moreover, they need to be replaced regularly, which was associated with high costs. Spare vacuum pumps always had to be ready for use in order to prevent lengthy production downtimes, as nearly all vacuum pumps were in operation throughout the production time, and each of them was in operation for an average of 4,000 hours per year. Jörg Möller was particularly aware of the issues with the aspect of energy consumption of the vacuum pumps.Vacuum system solution and its benefits for the customer
Dr.-Ing. K. Busch GmbH then created a completely new concept for generating the vacuum for all production machines on all five inline systems. Production Manager Jörg Möller was so impressed by the concept that a centralised vacuum supply from Busch with five MINK claw vacuum pumps (Fig. 2) has been in operation since October 2016.
Five vacuum pumps replaced the previous 22 rotary vane vacuum pumps, and still have enough power reserves to even enable a sixth inline system to be connected.
The benefits were clear even in the first few months after the centralized vacuum system was installed: no noise emissions or indoor air pollution from carbon dust around the workstations in the production areas.
-
Fig. 2: Centralized vacuum system from Busch with MINK claw vacuum pumps. Source: Busch Vacuum Solutions.
There were also vast energy savings compared to the former decentralized vacuum supply. The MINK claw vacuum pumps are each driven by energy-efficient IE3 motors with 6 kilowatts of rated power, corresponding to energy consumption of 30 kilowatts for the five motors in total.
In practice, the first few months of operation showed that demand-driven control of the new centralized vacuum system from Busch meant that only two or three MINK claw vacuum pumps at most need to be operational simultaneously. The actual power consumption is then 60,000 kilowatt hours a year, with a theoretical setup of 2.5 vacuum pumps and an operating time of 4,000 hours. The motor ratings of the rotary vane vacuum pumps used previously were 32.5 kilowatts in total, corresponding to an annual power consumption of 130,000 kilowatt hours. The result of changing from decentralized to centralized vacuum supply is a saving of 70,000 kilowatt hours, or 54% of the energy costs.
The result of changing from decentralized to centralized vacuum supply is a saving of 70,000 kilowatt hours, or 54% of the energy costs.
-
Fig. 3: Cutaway of a MINK claw vacuum pump. Source: Busch Vacuum Solutions.
MINK claw vacuum pumps operate entirely contact-free (Fig. 3), meaning that none of the internal moving parts in the vacuum pump come in contact with each other. As a result, there is no wear, making this type of vacuum pump nearly maintenance-free. Busch recommends a preventive annual change of the gear oil when using the systems in 24-hour operation. This can be performed while the system is in operation, by switching off the relevant vacuum pump in the centralized vacuum system. Vacuum generation for production is still ensured by the four other vacuum pumps thanks to the cascade connection and the operation of one of the five MINK claw vacuum pumps with a frequency-controlled motor. For Jörg Möller, this means a significant reduction in the cost and time needed for maintenance work. The contact-free operating principle of the MINK claw vacuum technology is highly reliable, as it does not require wear parts. This means, for example, that carbon vanes breaking and causing a sudden and total vacuum pump failure are a thing of the past.
Production Manager Jörg Möller has succeeded in implementing a highly economical and reliable vacuum supply solution for his plant.
Production Manager Jörg Möller has succeeded in implementing a highly economical and reliable vacuum supply solution for his plant.